
→「工場の稼働率の目安」の項目へジャンプ
→「工場の稼働率の計算方法」の項目へジャンプ
「自分の工場の稼働率は、他と比べて高いのか?低いのか?」「何%くらいが理想の稼働率なんだろう…」
そんな疑問を抱いたことはありませんか?
私は町工場でNC旋盤・汎用旋盤・マシニングセンタを扱う技術者として、毎日さまざまな部品加工に向き合っています。現場で設備を動かす立場だからこそ、“工場の稼働率”の目安や計算方法を正しく理解することの重要性を肌で感じています。
この記事では、工場における稼働率の基本から、実際の計算式の使い分け方、目安の数値と業界平均と比べた理想の水準、さらには私の経験に基づいた改善策の実例まで詳しく解説していきます。
特にこれから「工場の稼働率を上げたい」と考えている町工場の経営者・技術者の方に向けて、現場目線で語るリアルな課題と解決のヒントを盛り込んでいます。
また、クラウド型の生産管理システムによる稼働率の“見える化”についても、展示会での体験を通してお伝えしていきます。
工場稼働率の目安や計算方法に興味を持ったあなたにとって、きっと役立つ内容になっているはずです。
ぜひ最後まで読み進めて、あなたの現場のヒントにしてみてください。
工場の稼働率の目安とは?|計算方法と平均的な水準を理解しよう
工場で働く私たち町工場の技術者にとって、「稼働率」は非常に重要な指標です。
特に私のようにNC旋盤や汎用旋盤、マシニングセンタのような機械を扱っていると、1日のうちどれだけ効率的に設備を稼働させたかが、納期の達成や生産性に直結します。
工場の稼働率とは何か?
一般的な工場の稼働率とは、生産設備や作業者が“本来稼働すべき時間”に対して、“実際に稼働した時間”の割合を示すことが多いです。
後述しますが、稼働率にも種類がありますので、ここでは最も一般的なものを取り上げます!
たとえば、一人の作業者が8時間勤務中に実働が6時間であれば、稼働率は以下の式で計算されます:
稼働率(%)= 実際の稼働時間 ÷ 本来稼働すべき時間 × 100
= 6時間 ÷ 8時間 × 100 = 75%
75%というと、結構少ないように感じるかと思いますが、一日加工に費やしている時間を測ってみると、打ち合わせや資料作成、会議、トラブル対応などで結構時間を取られているもので、決して非常識な数字ではないというところが私の実感です。
工場の稼働率の目安はどれくらい?業界平均との比較
では、工場の稼働率の目安はどれくらいが理想的なのでしょうか。
稼働率は主に「生産設備」を主体としたものと、「作業者」を主体とした稼働率がありますが、一例として「作業者」を主体としてお話します。
私のような町工場勤務の現場でも話題に上るテーマですが、一般的には「80〜90%が理想」とされています。
ただし、これは単純な数値だけで判断してはいけません。
たとえば、受注が増えて稼働率が90%を超えていると、見た目は良さそうに見えますが、設備や作業者に過剰な負担がかかっている可能性があります。
逆に、稼働率が70%程度でも、生産計画や納期に合っていて無駄な残業や在庫が出ていない状態なら、むしろ理想的とも言えます。
私の現場でも繁忙期であれば、稼働率が複数台の管理によって90%を超えることもありますが、それが続くとどうしてもチョコ停(小さな停止)をしながらの段取りによる不良率の増加や、情報共有不足によって手戻りが発生するといった副作用が出てきます。
また、現場によっては全自動の専用機を24時間体制で動かすことで稼働率100%、それでもむしろ時間に余裕がある・・・という現場もあるかもしれません。稼働率の適正数値は、現場ごとに大きく異なるものです。
理想の稼働率とは、あくまで受注と生産能力のバランスが取れている状態で、かつ機械も人も無理をしていないラインというのが私の考えです。
稼働率を判断するために必要なデータとは?
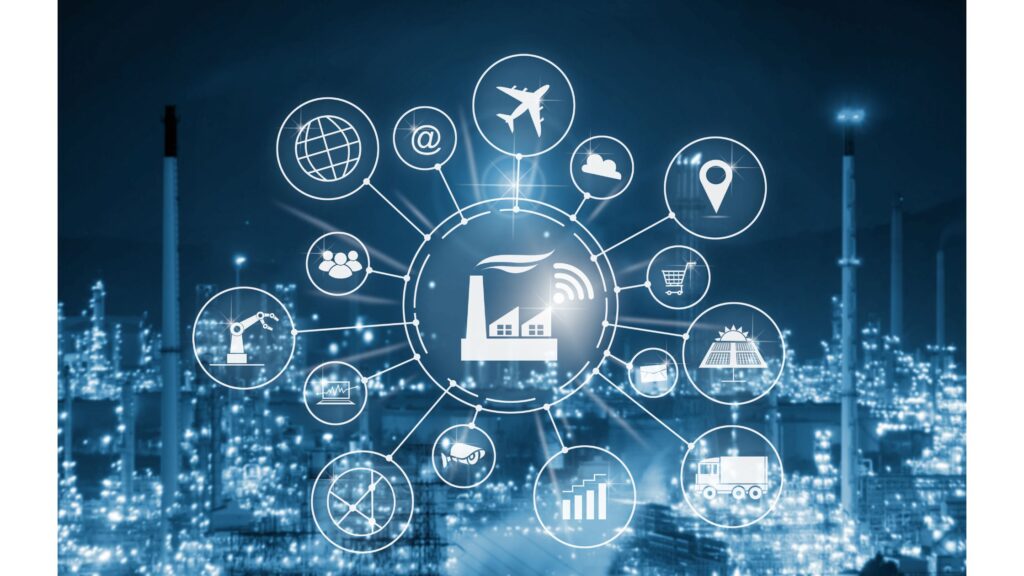
稼働率を正しく評価するには、「感覚」ではなく、具体的なデータの把握と可視化が欠かせません。
私たち町工場の現場では、紙の日報やホワイトボードでの手書き管理もまだ多い印象ですが、きっちり管理しようと思うと、正確な「稼働実績データ」と「基準時間データ」が必要になります。
以下は、稼働率を算出する際に工場で一般的に使われているデータの例です:
- 稼動実績データ:作業開始時刻、終了時刻、休憩・停止時間など
- 基準時間データ:その設備や人が「本来稼働すべき時間」
- 異常停止データ:故障・エラーなどの理由付き記録
こうした細かな記録があることで、どこに改善余地があるのか、稼働率を上げるための具体的な施策が見えてくるというのは、間違いないでしょう。
とはいえ、私の勤務先ではこれほどのデータはとっていません。少数精鋭の町工場なので、データをとるほど管理コストも重くなっていくためです。
町工場にこそ必要なのは「生産稼働率」
私の考えでは、町工場に一番必要な稼働率は、作業者単位の「生産稼働率」です。そして、その算出のために必要なデータは以下の2つだけです。
・「製品ごとの加工時間」これは段取りとサイクルタイムを足し合わせた時間です。その製品のための打ち合わせ時間も含まれます。
・「残業・休暇取得のデータ」有給の管理や残業代の支払いなどに必要なので、このデータは必ずあるはずです。このデータから、従業員ごとの「実稼働時間」が算出できます。
この2つのデータがあれば、「加工時間」÷「実稼働時間」で最も重要な「生産稼働率」を算出できます。
分子が加工時間ですので、その作業者が機械を2台や3台担当している場合、生産稼働率は100%を超えます。
生産稼働率が低いということは、加工以外の打ち合わせや切粉処理、加工外のトラブル対応など、加工に関係する作業以外の作業に多くの時間が費やされていることを意味します。この数値を適切な水準まで引き上げることは、ムダのない効率的な現場づくりにおいて非常に重要な取り組みです。
製品ごとの加工時間は、安価な町工場専用管理システムで簡単に管理できます。
最近はクラウド型の生産管理システムを導入する工場も増えていますが、稼働率を見える化する環境づくりが、町工場の生産性アップには不可欠です。
稼働率と可動率
ここで注意点として、似た言葉がありますのでお伝えしておきたいのが「稼働率」と「可動率」との違いです。
可動率とは、設備が“正常に動作可能”だった時間のうち、実際に動いていた時間の割合を示す指標で、稼働率とは評価の視点が異なります。
- 稼働率:需要やオーダーも含めた「作業実績」の指標
- 可動率:設備のトラブルや故障を含めた「機械の信頼性」の指標
たとえば不測のエラー発生によってマシニングセンタが1時間停止したとすれば、その時間は可動率を下げる原因になりますが、稼働率には「稼働しなかった時間」としてカウントされます。
つまり、8時間のうち、実働が6時間で、1時間がトラブル停止なら、稼働率75%、可動率は7÷8=約88%といった評価ができます。
稼働率は工場の生産効率を表し、可動率は設備の安定性を示します。
この2つを正しく理解しておくと、稼働率の改善ポイントが明確になります。
稼働率の計算方法を詳しく解説|正しい評価と注意点
稼働率の2つの計算式(生産量・稼働時間ベース)
工場の現場でNC旋盤やマシニングを扱う私にとって、「今月の稼働率はどうだったか?」というのは、切っても切れない重要なテーマです。
けれど、稼働率の計算方法を正しく理解していないと、改善すべき点を見落としてしまうこともあります。
工場の稼働率には、大きく分けて2つの計算方法があります。
① 稼働時間ベースでの稼働率計算
稼働率(%)= 実際の稼働時間 ÷ 本来稼働すべき時間 × 100
こちらは、「勤務時間」や「シフト上の予定稼働時間」に対して、実際に設備が動いていた時間で評価する方法です。たとえば、8時間の定時のうち、設備が実際に動いていたのが6時間なら、稼働率は75%になります。
冒頭でご紹介した稼働率もこちらのパターンです。こちらの稼働率はさらに「作業者」を主体とするか「生産設備」を主体とするかで2つに別れます。
② 生産量ベースでの稼働率計算
稼働率(%)= 実際の生産量 ÷ 生産能力 × 100
これは、設備や工程が1日に何個の製品をつくれるかという「生産能力」に対して、実際にどれだけ生産できたかを割合で示す方法です。たとえば、私の担当するNC旋盤の1日の生産能力が100個で、80個しか加工できなかった場合、稼働率は80%となります。
私の勤務先のような少量多品種加工の町工場では「稼働時間ベース」の稼働率管理が適しており、生産能力が明確な量産加工では「生産量ベース」の稼働率、といったように目的によって計算方法を使い分けるのが重要です。
稼働率の評価でよくある誤解と落とし穴
ここで大切なのは、稼働率の数字だけを鵜呑みにしないことです。
よくある誤解のひとつが、「稼働率が高ければ生産性が高い」というもの。しかし、実際にはそう単純ではありません。
ここでも作業者を主体とした「稼働時間ベース」の稼働率という前提にてお話します。
たとえば、稼働率が97%と聞くと一見素晴らしく思えますが、それがサービス残業や無理な複数台加工で無理やり出した数字なら、従業員の疲弊や設備トラブルの増加というリスクと背中合わせです。私自身も、かつて短納期対応で連日の残業が続き、複数のトラブルが出たことがありました。
このときは稼働率だけ見れば95%超え。でも現場はヘトヘト、不良率があがるだけでなく、急な依頼は良い仕事でもすべて断らなければならないため、客先からの信頼を失いかねません。そして、溜まった雑務は先送りにされているだけで、いつかはやらなければならないため後々の稼働率を必ず下げます。
逆に、稼働率が70%でも、無駄な加工待ちや工程間の滞留がなく、設備も安定稼働している状態ならば、非常に健全な状態ということもありえます。
また、注意が必要なのが「段取り時間や異常停止の扱い」です。段取り替えが多い現場では、段取りを稼働時間に入れていないと機械の実働時間が減って稼働率が下がりがちです。そのため、私のように1日に複数の小ロット品を加工する現場では、この段取り時間も機械稼働時間に加えてしまうのがおすすめです。もちろん、稼働率向上の施策とは別に段取り作業の最適化を行うことが利益向上のカギになります。
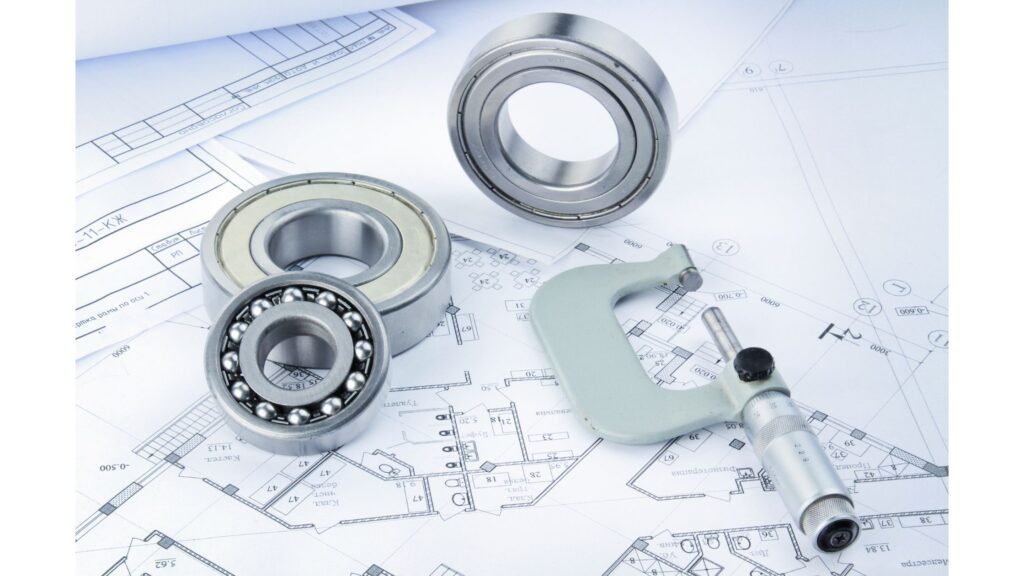
設備総合効率(OEE)との関係性も理解しよう
稼働率をさらに深く分析したいときに登場するのが、「設備総合効率(OEE)」という指標です。
OEEは次の3つの要素をかけ合わせて算出されます:
OEE = 稼働率 × 性能稼働率 × 良品率
このOEEは、設備の本当の稼働パフォーマンスを見える化するための指標です。
性能稼働率とは、設備が動いている時間内で「どれだけ効率良く製品を作れたか」を示す指標です。「サイクルタイム × 生産数量 ÷ 稼働時間」で算出されます。
たとえば、1分で1個加工するのが理想で、300個作るのに360分かかったとすれば、性能稼働率は約83%になります。
NC旋盤の稼働率が90%でも、加工速度が遅かったり不良品が多ければ、OEEは大きく下がります。
OEEを使うと、「どこにロスがあるか」が明確になります。
とくに量産加工を行う工場では、生産管理ソフトと連携してOEEを記録しているところが多く、「稼働しているのに成果が出ていない」ような“隠れロス”を見つけるのに役立っています。
また、OEEは「製品1個あたりの利益」を考える上でも重要です。高稼働でも不良率が高ければ利益が出ませんから、稼働率だけを追い求めるのではなく、質の高い稼働こそが最終的に利益につながるといえます。
工場の稼働率を上げるには?|改善の具体策と現場の工夫
工場の稼働率を高めるにはどうしたらよいか。これは、私のような町工場の現場技術者にとって永遠の課題です。
「稼働率を上げる=もっと機械を動かす」ではなく、「ムダを減らし、効率を上げる」ことが本質です。ここでは、私が実際の現場での経験をもとに「工場の稼働率を上げる方法」について、具体的にお話しします。
受注数と生産能力のバランスを取るための営業戦略
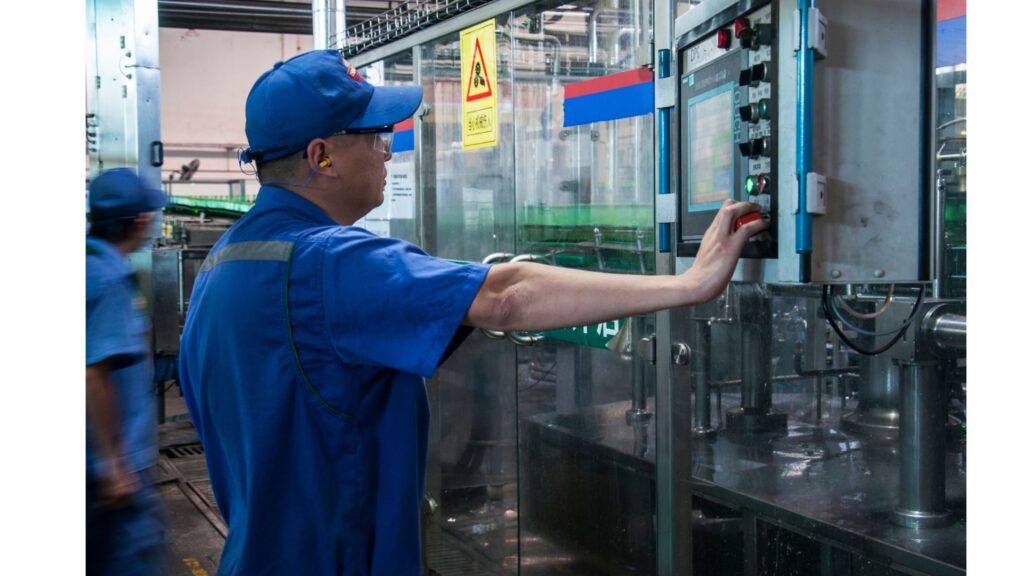
工場の稼働率を上げようとする時、真っ先に思いつくのが「もっと仕事を増やすこと」かもしれません。
たしかに、生産能力に対して仕事が少なければ、機械は動かず稼働率は低下します。私たちのような町工場では、営業が受けてくる案件の数と種類が、直接稼働率に影響します。
私の勤務する町工場でも、過去に受注が少なかった月は、稼働率が60%を下回ったことがありました。コロナの前くらいです。このときは勤務先の社長が受発注企業の集まる商談会に参加して新規顧客を獲得し、結果的に稼働率は80%以上に戻りました。その後のコロナ期間も、この営業の結果があったから乗り越えられたと感じています。
ただしここで注意が必要なのは、闇雲に受注を増やすと稼働率は上がっても「無理が出る」ということです。加工の順番調整や設備負荷のバランスを考えながら、余力を見極めて受注するのが大切です。
実際、もしコロナがなかったら、仕事が集中しすぎて逆に回らなくなっていた可能性が高いです。
こうした事態に備えるためにも、外注先となる信頼できる協力会社を複数持つことが非常に効果的です。外注体制を整えておくことで、自社で抱えきれない案件にも柔軟に対応でき、安定した稼働を維持することが可能になります。
例えば大阪府堺市に拠点を置く日本ツクリダス社は「デジタルとアナログを融合し、仕事の効率化を目指す本」の著者でもある角野嘉一氏が代表を務めており、まさにお手本のような会社です。
現在は加工・製造事業は別会社として独立したようですが、創立当初から最近まで金属加工の町工場だった会社です。
以前お話を伺った際は、デジタル化の遅れているこの業界で積極的にIT技術を取り入れており、インターネットを活用した集客によって全国500社以上との取引を実現していました。さらに、商社的な機能も兼ね備えており、業務が過多になった際は外部に適切に振り分け、自社の負荷をうまくコントロールしながら安定稼働を行える仕組みを作っていました。
このような柔軟かつ効率的な運営スタイルが、仕事に波がある町工場が持続的に稼働率を維持していくための、最適解のひとつと感じています。
生産計画の最適化と阻害ロスの低減がカギ
稼働率向上において、最も地味でありながら確実に効くのが「段取りの見直し」と「ロスの削減」です。
私のようにNC旋盤での多品種小ロット加工を行っていると、段取り替えが1日の作業時間の殆どを占めます。
たとえば、ある製品の加工が終わって次の製品に移る際、治具交換や芯出し調整で30分以上止まることもしばしば。こうした段取り時間が長いほど、生産稼働率に関係なく生産効率が落ちてしまいます。
とはいえ、段取り時間の削減は職人技術的な部分。仕組みを変えただけで一朝一夕で身につくものではありません。
より短期で効果が出る、重要な対策は「ロスの削減」。手戻りを防いだり、探しものの時間を防いだりすることです。
私たちの現場では、以下のような工夫で改善を進めました:
- ツール表の整備等:マシニングセンタのツールをホワイトボードに書き留めておくことで、加工者が変わっても手戻りが起こらないよう対策しています。
- 治具・材料・ゲージ等の整理:探し物の時間は本当に無駄です。煩雑に置かれているものを整理し、表で管理する形に改善しています。
- 標準作業マニュアルの整備:段取りの手順を可視化し、初心者でもミスや手戻りが起こりにくい対策を行っています。
また、言うまでもないことかとは思いますが、加工順序を変えるだけで設備の停止時間を減らせる場面も多いです。急ぎの案件を優先しすぎて無駄な段取り替えを行うより、似た形状・材質の製品をまとめて加工することで効率は上がります。
さらに生産数の多い工場で「加工のムダ」を可視化するには、現場での異常停止やエラーのログをデータとして記録しておくことも一案です。とはいえ、小規模の町工場レベルであればそこまでは必要ないと思います。
簡単なところから、ムダをなくすことが稼働率を上げるための最重要ポイントです。
現場教育・スキルマップ・DXの活用
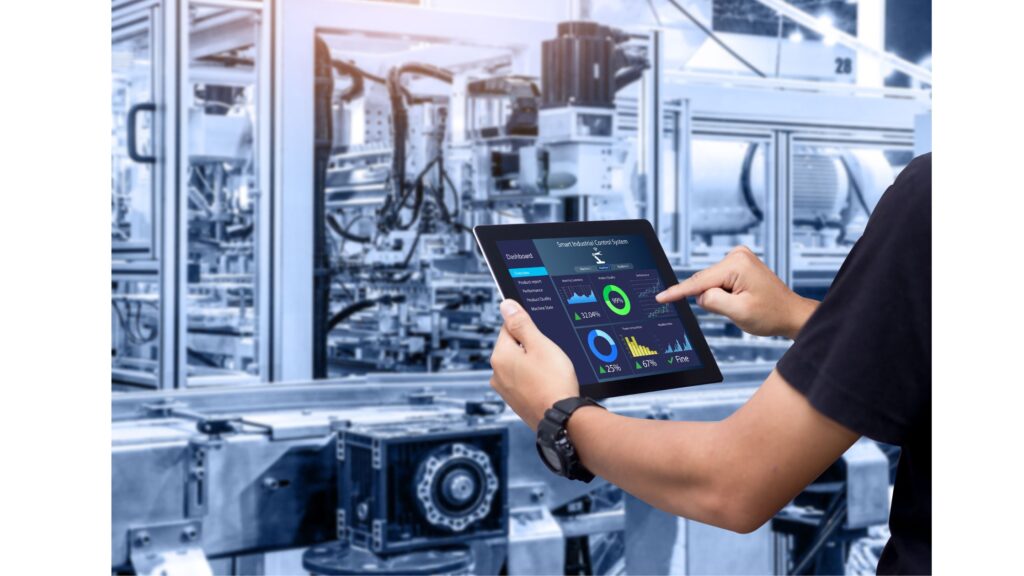
どれだけ計画や機械が整っていても、それを動かすのは「人」です。
つまり、人材のスキルや段取り力が、稼働率に直結します。
私の工場でも、熟練作業者と初心者で段取り時間に2倍以上の差がありました。
工場によっては「スキルマップ」を導入し、誰がどの作業をどのレベルでこなせるかを一覧化し、教育計画と人員配置を効率化しています。 人数が比較的多く、作業レベルにもばらつきがある場合は、担当作業の振り分けや教育に有効ですので、活用してみるのがおすすめです。
さらに、現場のデータを見える化する「クラウド型生産管理システム」の活用は、稼働率向上に欠かせません。
私がSNSを通じて話を伺った町工場の現場では、後述する「エムネットくらうど」という比較的導入しやすい価格帯の町工場向け管理システムを活用することで、作業の進捗状況や納期をリアルタイムで確認できるようにしています。その結果、「何をいつやるべきか」が明確になり、稼働率が改善しただけでなく、体感的にも現場の動きが格段に良くなったということです。
まだアナログの管理しかしていない会社では、比較的安価な管理システムの活用は、リスクより期待メリットの方が大きい場合がほとんどですので、ぜひ検討してみてください。
また、管理システムについては当サイトで深堀りして調査していますので、ぜひこちらの記事もご活用ください。
稼働率向上の本質は「現場にムリ・ムダ・ムラを残さない」こと
稼働率を無理に高めると、在庫の山、作業者の疲労、品質トラブル…と、悪循環に陥ります。
大切なのは、受注と生産能力のバランスを保ちながら、「稼働しやすい状態」を作ること。
私たち町工場では、人も設備も限られています。だからこそ、「段取り」「教育」「可視化」「バランス」が稼働率改善の鍵となります。
このあと紹介する「エムネットくらうど」のような仕組みがあれば、私たちのような小規模な町工場でも、データと連携しながら効率的に稼働率を上げていくことが可能になります。
エムネットくらうどで稼働率を見える化|町工場のDX実例
「稼働率を上げたい」と思っていても、そもそも現場が今どんな状態なのか分からなければ改善はできません。私自身、町工場でNC旋盤やマシニングセンタを動かす日々のなかで、「どの仕事を優先すべきか」「次に何をやるべきか」最善の選択ができていないことがよくあります。
特に、自分の作業範囲だけしか見えていないと、他の作業者の仕事や全体の流れを考慮できずに優先順位を決めてしまうため、「本当はこっちの加工を先に進めるべきだった」と後から気づくことが何度もありました。優先順位を誤ったことで、結果的に非効率になってしまったと感じる場面は少なくありません。
そんな状況を変えてくれるのが、私が当サイト立ち上げ当初からずっとおすすめしている、生産管理システム「エムネットくらうど」の導入です。
ここでは、2024年のJIMTOF(日本国際工作機械見本市)で、日本ツクリダスの角野嘉一社長から直接お話を伺い、実際にエムネットくらうどの操作デモを体験した経験から、稼働率向上にエムネットくらうどのような生産管理システムの導入が大変役立つことをお伝えします。
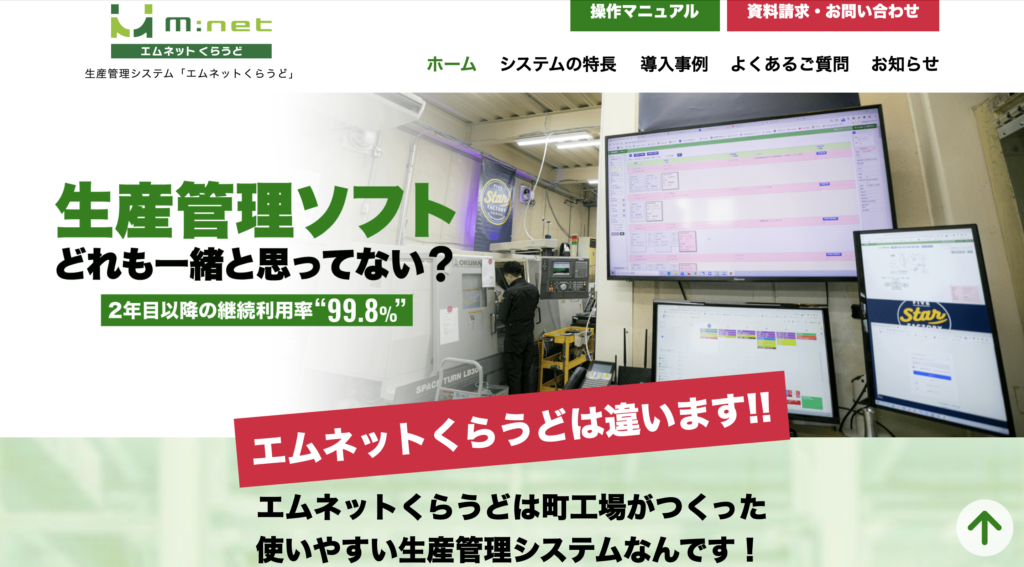
多品種・短納期に対応するための「案件見える化」
町工場の仕事で共通しているのが、日々多品種・短納期の仕事に追われているという点です。私の勤務先も例に漏れず、同時に複数の案件が進行し、図面の種類や材質もバラバラという状況です。
そうした中、「エムネットくらうど」のような町工場向けの管理システムでは、各案件をバーコードで管理することで、スマートフォンやタブレットから納期や進捗をリアルタイムで確認できるようになっています。
自動で作成される工程表を見れば、加工中の部品が今どの工程まで進んでいるのか、どの順で進めるべきかといった情報が一目でわかり、現場の優先順位づけが非常に明確になります。これにより、作業者の判断ミスや無駄な作業待ちが大幅に減り、結果的に稼働のムダを削減することができます。
現場と営業がリアルタイムで連携できる体制に
町工場では、事務方と製造の連携がうまくいかないとトラブルになりがちです。お客様から「この部品の進捗どうなってる?」という問い合わせが入った時、システムがなければ事務方がわざわざ現場まで確認に来るか、誰かが電話でやり取りするしかありませんでした。
その点エムネットくらうどを使えば、クラウド経由で外出先からでも進捗が確認できます。営業も、お客様の目の前でスマホから状況を伝えられるし、現場もわざわざ手を止めて対応しなくていい。
モニターで最新の進捗状況を表示できるため、朝礼で案件一覧を全員で確認することも簡単です。
特に印象的だったのは、開発元である町工場、日本ツクリダス社では営業と製造のメンバーがエムネットくらうどの案件一覧を確認して、優先すべき仕事を共有するのが習慣になっている点です。
「今日はこれを先に終わらせよう」「この仕事は明日でも間に合う」といった判断が全員で共有されており、現場の混乱を未然に防いでいると感じました。
図面・伝票・加工実績データを一元管理できる安心感
加工現場で最もストレスになるのが、「図面が見つからない」「納期が分からない」といった情報の混乱です。
特に急ぎの再発注案件で、「前の図面、どこだっけ?」と探し回ったこと、ありませんか?恥ずかしながら私も何度かありました。
展示会では、エムネットくらうど上に図面や伝票、加工実績データがすべて保存・管理されている実際の画面も見せていただきました。
案件名や日付、品番を入力すれば、必要な情報に即アクセスできる仕組みになっており、「これなら紙を探す時間がゼロになる」と強く感じました。
さらに、事務方も同じデータベースで納期を常にチェックできるため、納期遅れが発生しそうな案件については製造部門と即座に連携して対応することができます。
稼働率改善と利益向上の両立を支えるツール
稼働率の最適化にあたって「仕事のキャパを見ながら、無理なく、でも止めずに回す」ということが目指すところになります。
エムネットくらうどでは、現場の稼働状況が工程単位で見える化されており、無理な詰め込みや過剰な受注を避けながら、全体最適で稼働率を高められるような、仕事の忙しさがひと目でわかる仕組みが整えられています。
たとえば、
・加工順の入れ替えをスムーズに行える
・作業進捗の記録がリアルタイムで反映され、日報作成が不要に
・事務方も稼働状況を見ながら、納期回答や受注判断が即時にできる
といった具体的な効果が出ており、「稼働率を上げようと頑張るのではなく、整えたら自然に上がっていた」という理想の状態が実現されていると感じました。
町工場の限られたリソースの中で安定した利益を出すには、こういったツールによる“見える化”の力が不可欠だと、展示会での体験を通じて実感しました。
まとめ|理想の稼働率を目指すには?システム導入のすすめ
ここまで、工場の稼働率について、その基本から具体的な計算方法、改善のポイント、さらには実際の現場での工夫まで、私自身の経験を交えながら詳しくご紹介してきました。
結論として、理想の稼働率とは単なる「数値」ではなく、「バランス」と「見える化」によって無理なく維持できる運用体制にあると感じています。
稼働率を「上げる」のではなく「整える」時代へ
稼働率が高いからといって、それが必ずしも現場の理想的な状態とは限りません。過剰な残業、無理な受注、不良の増加…私自身、そうした“副作用”を経験してきました。
だからこそ、本当に目指すべきは「整った稼働」。設備や人に過度な負荷をかけず、納期や品質を安定させながら稼働できている状態です。
その実現のためには、「段取り」「計画」「教育」「情報共有」の4つの柱を強化し、現場のムリ・ムダ・ムラを減らす取り組みが欠かせません。
小さな町工場でも“見える化”から始められる
私のような現場技術者の視点から見ても、今や生産管理は紙や勘頼りの時代ではありません。
たとえば、JIMTOF2024で体験した「エムネットくらうど」のような町工場向けのクラウド型管理システムであれば、比較的安価に導入でき、現場の情報をリアルタイムで見える化できます。
・加工の順番を現場で判断できる
・納期や負荷が全員に共有される
・作業記録が自動化され、紙の手間が減る
・稼働率の推移も把握できるようになる
こうした変化が、確実に稼働率の向上と安定経営につながっていくと、展示会での体験や他工場の事例を通じて強く感じました。
稼働率の改善は、町工場が生き残るための戦略
納期短縮、単価が上がらない、人手不足など多くの課題がある製造業において、稼働率をいかにコントロールするかは、町工場が利益を出し生き残っていくために大変重要なテーマだと思っています。
高すぎてもダメ、低すぎても利益が出ない。だからこそ「最適化された稼働」を実現するために、現場の見直しと小さな仕組みづくりから始めることが大切です。
生産現場の最前線で働く一人として、この記事が少しでもあなたの工場の“稼働率を整えるヒント”になれば幸いです!
コメント