
中小企業や町工場では「エクセルで十分」「導入コストが高い」といった理由で、生産管理システムの導入をためらうケースも少なくありません。しかし、適切なシステムを活用することで、工程管理や納期管理、在庫管理が効率化され、業務の負担を大幅に軽減できます。
本記事では、「生産管理システムはいらないのか?」という疑問に対し、導入のメリットや課題、失敗事例を交えて詳しく解説します!
生産管理システムはいらない?導入の必要性とは
生産管理システムがいるかいらないか、結論から先にいうと、「企業による」という答えになります。
その理由としては、企業ごとに規模や業務内容、強み・弱みは多種多様で、システムで補うべきかどうかは一概に言えないからです。
システムについて考えるにあたって、まず「何のためにシステムがあるのか」を解説します!
生産管理システムの基本的な役割
生産管理システムは、製造業の業務をデジタル化し、以下の管理を効率化するためのツールです。
システムによっては、これらの他にも部署間でやりとりできるチャット機能や、会計システムとの連携機能があります。
当然ながらシステムごとに設計思想はまちまちですので、それぞれに強い分野、弱い分野があります。
生産管理システムが解決できる問題とは?
システムを導入しない場合、どのような問題が発生するのでしょうか?
以下は、生産管理システムを導入しないことで起こりがちな課題です。
特に、多工程にわたる製造プロセスでは、手作業での管理では限界があり、ミスや納期遅れの原因となります。
① 納期遅れが発生する
「旋盤加工→マシニング加工→焼入れ→研磨」といった工程がある場合、各工程の進捗を管理しないと、納期遅れが発生します。
システムがないと、進捗確認のために都度現場を回る必要があり、情報共有の手間が増えます。
② 在庫管理が煩雑になる
エクセル管理では、リアルタイムの在庫情報を把握するのが難しく、「必要な時に材料がない」「過剰在庫でコストが増大」といった問題が発生します。
生産管理システムがあれば、在庫状況をリアルタイムで把握でき、適正在庫の維持が可能になります。
③ 部門間の連携がうまくいかない
生産管理システムを導入しないと、営業部門・製造部門・購買部門の間で情報共有がスムーズに行われず、二重発注や納期ミスが発生しやすくなります。
システムを活用することで、社内全体でリアルタイムの情報共有が可能になります。
生産管理システムの導入失敗事例について
生産管理システムを導入すれば、仕事の効率化に対する期待ばかりが先行してしまいがちですが、導入が失敗するケースも多く存在します。ここでは、生産管理システムの導入が失敗に終わる代表的な事例について見ていきましょう。
また、失敗事例から見えてくる教訓をもとに、どのようにして自社に最適な生産管理システムを選べばよいのかについても解説しています。
目的や目標が不明確なまま導入を進めたケース
まず、何のためにシステムを導入するのかはっきりさせてから導入するということは非常に重要です。
私は中小企業向け生産管理システムのベンダーが5社集まるオンライン座談会に参加したことがあるのですが、その際も「最も重要な点」として話題になっていたポイントです。
システムを導入する目的が曖昧であると、どのような効果を目指すべきかが不明確になり、結果的にシステムの導入にかかるコストや労力に対して十分な成果を得られないことがあります。システム導入自体がゴールになってしまうと、本来の課題解決にはつながりにくいということですね。
例えば、在庫管理の効率化や生産スケジュールの最適化を目指していたはずが、システム導入後も従業員が以前と同じ作業を手作業で続けることで、結局システムが活用されず、導入効果を実感できないといったパターンです。
システム導入前に明確なゴール設定とその達成方法を全社で共有することが不可欠です。
過剰なカスタマイズの弊害
さらに、「過剰にカスタマイズを行った結果、システムが複雑化しすぎて運用が困難になった」という事例もあります。
システムによっては、自社のニーズに合ったカスタマイズが可能ですが、あまりにも多くのカスタマイズを行うと、システムの保守が難しくなり、アップデートや新しい機能の導入がしにくくなるリスクがあります。
これにより、システムの維持費用が予想以上に高くなり、結果的に導入のコストパフォーマンスが悪化してしまうことがあります。
このような問題を回避するためには、必要最低限のカスタマイズにとどめ、できるだけ標準機能を活用することで、システムのシンプルさを保つことが重要です。
また、そもそもカスタマイズの必要がないコンパクトなシステムを選ぶことがこのような失敗を避ける一つの方法になります。日本ツクリダス社のエムネットくらうどのようなシステムですね。
標準機能が自社のニーズをどれだけ満たしているかを事前に確認し、無駄なカスタマイズを避けることで、運用の安定性を確保できます。
現場の従業員がシステムを使いこなせなかったケース
システム導入時には現場の従業員への教育や研修が必要不可欠ですが、これが十分に行われない場合、システムの操作が複雑で利用が進まず、導入されたシステムが放置される結果に終わることがあります。
特に、従来の手作業に慣れている作業者にとって、新しいシステムは難しく感じられ、操作ミスが頻発することでかえって生産性が低下してしまう・・・ということも少なくありません。
これを避けるためには、システム導入時に現場作業者を巻き込み、トレーニングをしっかりと行い、システムを利用する意識を作っていくことが求められます。
経営トップの関与不足による失敗
生産管理システムの導入には、全社的なサポートが必要であり、経営トップがその導入の重要性を理解し、支援することが成功のカギとなります。
しかし、経営陣がシステム導入を軽視し、導入プロジェクトを担当者任せにしてしまうと、プロジェクトは組織としての一体感を欠き、結果的に中途半端な導入に終わってしまうことがあります。
経営層がしっかりと支援し、全社を挙げてシステムを使う文化を根付かせるためには、まず「小さく始める」など導入への抵抗感を減らす施策が重要といえます。
導入の難しさ。問題点やデメリットは?
生産管理システムが「いらない」と感じてしまう理由の一つとして、その導入のハードルの高さがあげられます。ここでは、生産管理システム導入時に起こり得る代表的なデメリットや問題点について見ていきましょう。
導入コストの高さ
生産管理システムは高機能であるがゆえに、初期導入費用がかなり高額になることが多いです。
システムのライセンス費用に加え、導入のためのコンサルティング費用、社内でのカスタマイズのための費用、そしてハードウェアの準備費用など、多方面にわたるコストがかかります。これに加えて、システムを維持・運用するためのランニングコストも考慮しなければならず、中小企業にとっては導入するハードルが高いと感じられる場合も多いでしょう。
比較的大きい規模に対応したシステムであれば、1000万円を超えることもザラにあります。
当サイトでは、以前、初年度費用が100万円を切るシステムについてまとめています。クラウドであればこの金額でも十分対応可能です。これらのシステムであれば、基本的にライセンス費用とオプション費用のみで利用することができます。ぜひ合わせてご覧ください。
デジタル化が進んでいない町工場のような企業にとっては、安価な生産管理システムを導入することはコストパフォーマンスの優れた選択肢といえます。
現場作業者への負担
先に書いた失敗事例「現場の従業員がシステムを使いこなせなかったケース」にもある通り、システム導入には、現場作業者への教育や研修が不可欠です。
特に、従来の手作業での運用に慣れている作業者にとって、新しいシステムへの移行は大きな負担となります。
システムと現場ニーズの不一致
生産管理システムは多くの種類から選ぶことができ、幅広い機能のものが提供されていますが、それが必ずしもすべての現場に適しているわけではありません。
特に多いのが、現場のニーズに対してシステムが多機能すぎて、その機能のほとんどが使われないパターンです。
このような問題を防ぐためには、導入前に現場の業務内容をしっかりと分析し、システムとの相性について確認しておくことが重要です。
トラブルに対しての柔軟な対応がしにくくなる可能性
生産管理システムは、業務の標準化や効率化を目的とした便利なツールです。ですが、ルールがきっちり決まっている分、ちょっとした変更に柔軟に対応しづらいこともあります。
特に、「急に仕様が変わった」「納期が変わった」「客先の発注もれ」など、状況に応じて柔軟に対応しないといけない場合、システムが逆に足を引っ張ってしまうことも・・・。
現場の判断でサッと対応できたものが、システムのルールに縛られて動きづらくなってしまうことがあるんです。
そうならないためにも、システムを導入するときは「変更やトラブルが起きたとき、ちゃんと対応できるか?」という視点を持っておきましょう。トラブル発生時の対応フローを決めておく、エラーを吐きにくい柔軟なシステムを選ぶなど、事前の準備をしっかりしておくことで、思わぬデメリットを防ぐことができます。
部門間の連携不足と情報共有の課題
「生産管理システムを導入すると、納期や工程などの情報を一元管理できるようになり、業務がスムーズに回るはず・・・」と思いきや、実際には部門間の連携が取れていないと、システムを活かしきれないこともあります。
たとえば、現場の加工担当と事務スタッフの間でシステムを使った情報共有がうまくいっていないと、結局「今、どの工程まで進んでる?」と直接確認しに行くことになり、導入前とほとんど変わらない…ということになりかねません。
こうした問題を防ぐには、システムを導入する前から、各部門が情報共有の重要性を理解し、一緒にプロジェクトを進めることが大切です。
「生産管理システムはいらない」を防ぐための選び方
システム導入で失敗しないためには、自社の課題を明確にし、適切なシステムを選ぶことが重要です。
① 自社の課題を整理する
まず、「生産管理システムで解決したい課題」を明確にしましょう。
✔ 納期管理が難しい
✔ 在庫管理に手間がかかる
✔ 工程管理を効率化したい
このような具体的な課題を整理することで、必要な機能が見えてきます。
② 生産方式に合ったシステムを選ぶ
自社の生産方式(受注生産・多品種少量生産・大量生産)に適したシステムを選ぶことが重要です。
例えば、受注生産型の企業であれば、オーダーメイドに対応できるシステムを選ぶと良いでしょう。
③ 無料トライアルを活用する
多くのベンダーがデモや無料トライアルを提供しているので、導入前に試してみるのがおすすめです。
実際に現場で使い勝手を確認し、業務に合うかを見極めましょう。
④ サポート体制を確認する
システム導入後にトラブルが発生した際、ベンダーのサポートが遅いと業務に支障が出ることがあります。
導入前に、サポートの対応範囲やスピードを確認しておきましょう。
町工場におすすめの生産管理システムは?
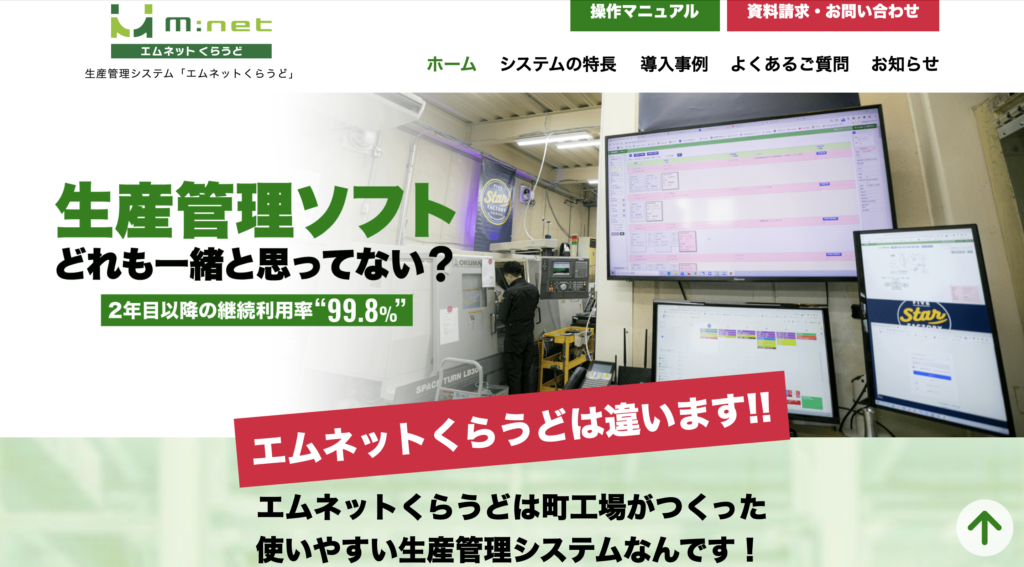
筆者自身が町工場の現場で働いているため、私目線で町工場に最もおすすめできる生産管理システムをお伝えします。
そのシステムは「エムネットくらうど」です。
大阪の町工場「日本ツクリダス」社が作った生産管理ソフトで、自社で快適に運用するために作ったシステムを販売しているものです。
その特徴は、安さと扱いやすさ。バーコードを使った簡単な操作で、現場にとっても導入のハードルが低いです。
導入しやすい低価格でありながら、下に掲載の通り、町工場に必要な機能を全て備えています。
「生産管理を徹底したら、休みを増やしたのに売上が上がった。」という声もあり、実績は折り紙付きです。
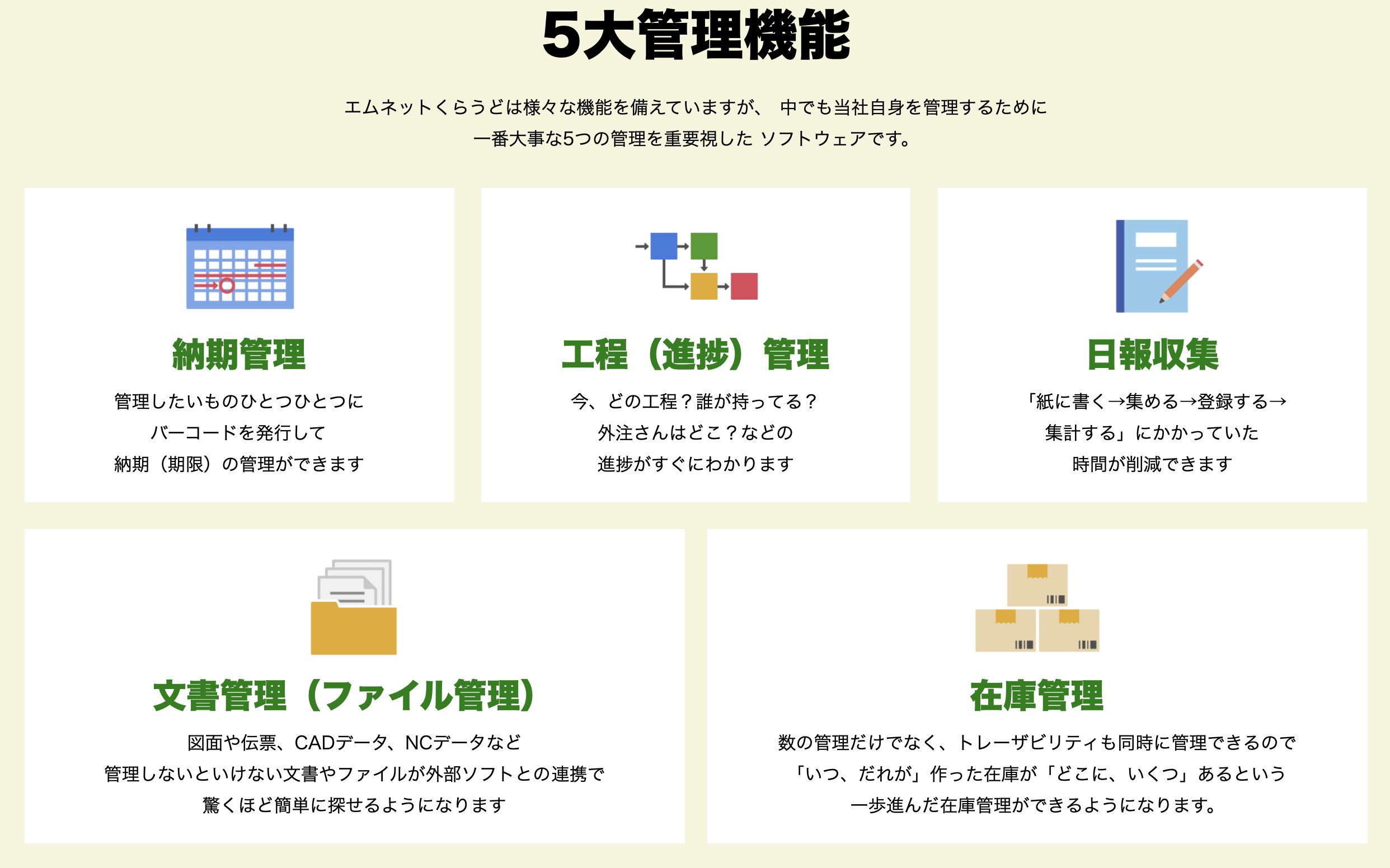
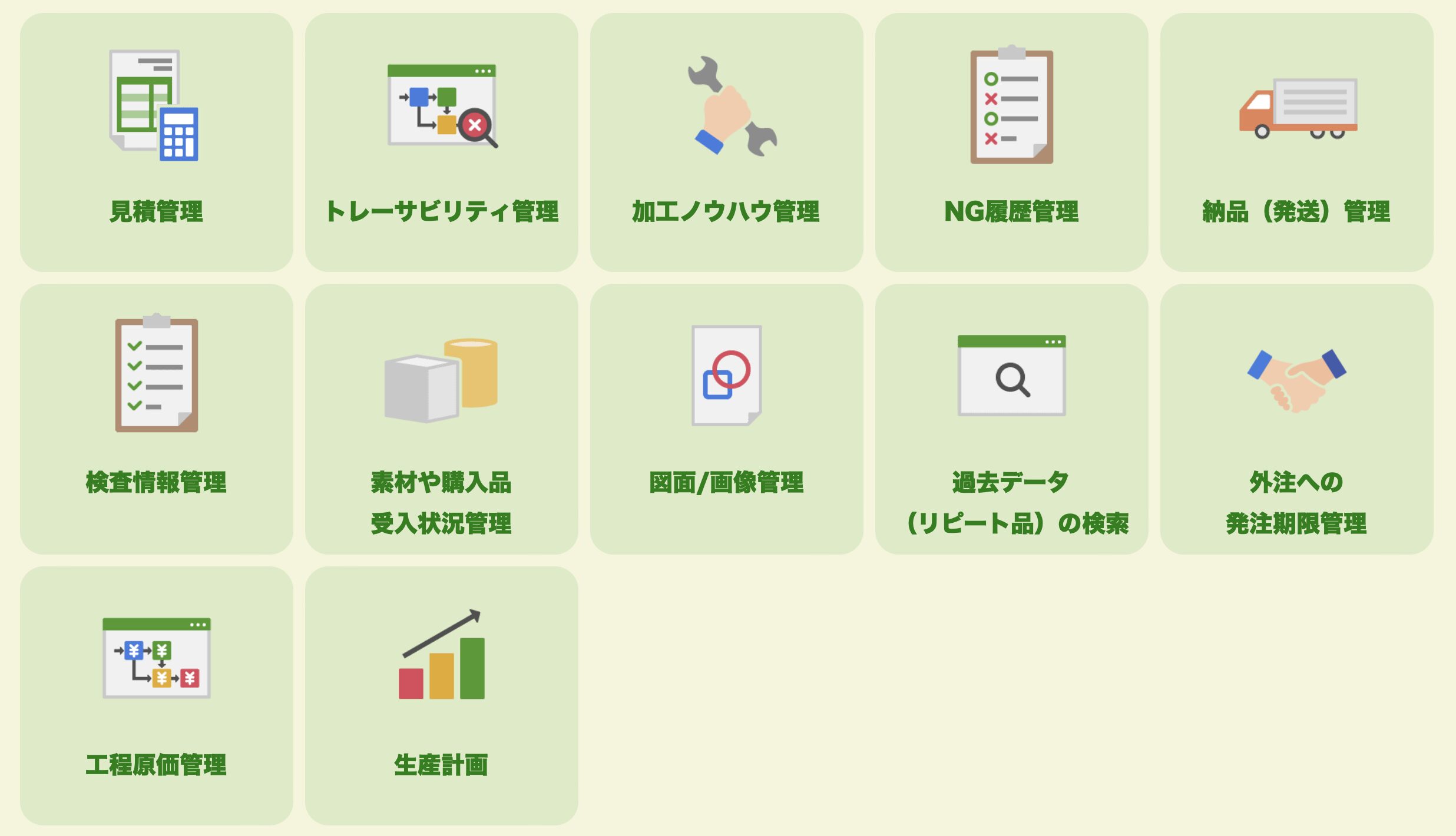
なぜこのソフトが一番と考えたのかという点については、以下の関連記事をご覧ください!
まとめ|生産管理システムの導入はコストと効果のバランスが鍵!
「生産管理システムはいらない」と感じる企業もありますが、うまく導入できれば業務効率の向上や生産性アップに大きく貢献するツールです。ただし、導入するかどうかは、自社の業務規模や課題に応じて慎重に判断することが重要です。
✔ 納期遅れ・工程管理のミスが頻発しているなら導入の価値あり!
✔ 生産計画が複雑で、現場との情報共有がうまくいっていないならシステム活用を検討!
✔ 逆に、現在の業務フローで効率的に運用できているなら、無理に導入する必要はない!
生産管理システムは、使いこなせば大きなメリットがありますが、導入の仕方を間違えると「コストばかりかかって使いこなせない…」という結果になりがちです。トライアルを活用し、自社に合ったシステムかどうかを見極めてから導入するのが成功の鍵となります。
また、「導入すればすぐに解決する!」と考えるのではなく、「どんな業務を効率化したいのか?」を明確にすることが大切です。
導入後の運用まで見据えて、適切なサポートが受けられるシステムを選ぶことで、より効果的に活用できるでしょう。
最終的に、生産管理システムが必要かどうかは「コストと効果のバランス」で決めるのがベストです。自社の業務状況を見極め、最適な選択をしていきましょう!
コメント