
リーマとは、わかりやすく言うと精度の出ていない穴を高精度のきれいな穴に整えるための工具です!
下穴をくり広げることで精度を高め、真円度や表面粗さを向上させます。
この工具、一口に「リーマ」といっても様々な種類があります。
本記事では金属加工における様々な種類のリーマをご紹介し、それぞれの特徴とともに解説しました!
リーマの使い方については、以下の記事「リーマの使い方と加工の手順、コツは?現役加工技術者が解説!!」をご参照ください!
以下の記事では普段使用しているリーマと、実際に加工技術者が行っているリーマを使った加工技術を惜しみなく公開しています。
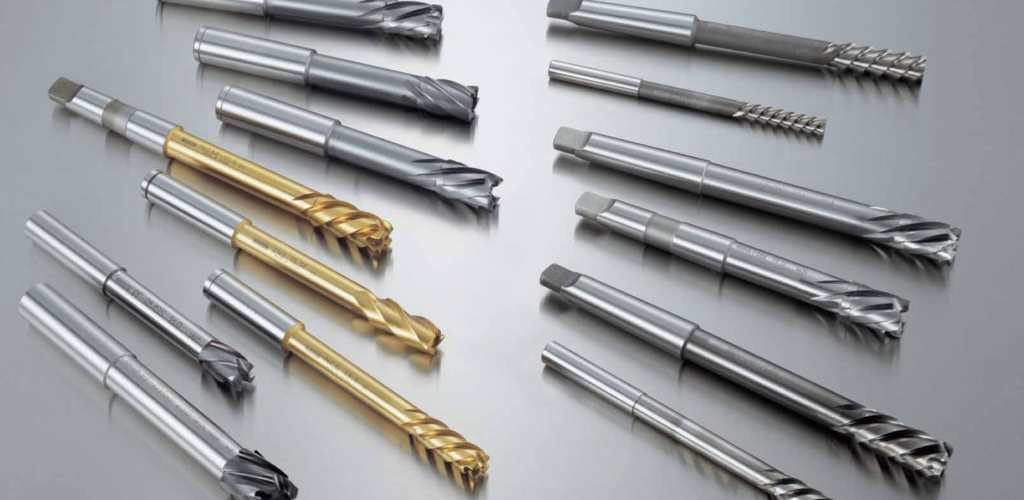
ブローチリーマ

ブローチリーマは、マシニングセンタやフライス盤でリーマ加工を行うにあたって、最もよく使うリーマの一つです。
私の勤務先では、基本的にこのブローチリーマとスキルリーマの2種類しか使いません。
ブローチリーマの特徴・メリット
ブローチの重切削性
ブローチリーマは、ブローチの重切削性とリーマの仕上げ面の美しさのいいとこ取りをした工具といえます。
わずかなテーパーになっている食い付き部が比較的長いため、取り代が0.4mmほどあるような条件でも加工を行うことができます。
ドリルと同じくらいの切削速度で加工することも可能
ブローチリーマは刃先が丈夫で切削性が高いため、比較的高い切削速度にも耐えられます。
摩耗は早まりますが、ドリルと同じくらいの切削速度でも加工することが可能です。
比較的長く使える
刃先が丈夫なので、刃先のチッピングといった心配が少なく、比較的長く使えます。
60°以上のねじれ角でびびりにくい
切削抵抗を減らすため60°以上のねじれ角が施されています。
そのためびびりにくく、良好な仕上げ面を得られやすいです。
面取りがなくてもなじみやすい
食い付き部が長くテーパーになっており、先端が丈夫なので、面取りをしていなくても問題なく下穴になじんでいき加工を行うことができます。
ブローチリーマのデメリット
通し穴しか加工できない
ブローチリーマの不完全部は比較的長いため、止まり穴は加工することができません。
通し穴のみに活用しましょう。
食い付き部が長いデメリットは他にも
食い付き部が長いことは、メリットにもつながるブローチリーマの特徴ではありますが、加工可能なクランプ条件が限られる上、加工時間もかかるデメリットもあります。
私もブローチリーマを使う際はだいたい15mmくらい余分に通すようにしているため、穴奥のスペースが15mmに満たない場合はスキルリーマを使うか、通せるギリギリのところまで気をつかって加工する必要があります。
また、余分な15mmを加工する分サイクルタイムも伸びてしまいます。
ステンレスは摩耗が早い
ブローチリーマはSUS304などのステンレスにはカタログ上対応していない工具です。
実際に加工することは可能ですが、取り代は0.1以下に少なくする必要がありますし、摩耗も大きくなります。
摩耗したのが比較的わかりにくい
ブローチリーマは刃先の形状から見た目には摩耗がわかりにくいです。手で刃先を触ってみて切れ味が良いかどうかで多少判断することができますが、正確に判断するのは難しいと言えます。
どのくらい摩耗が進んでいるかによって別のリーマと分けて管理するなど、工具管理のルールを決めることである程度解決できます。
スキルリーマ

ブローチリーマとともに、最もよく使うリーマの一つです。ブローチリーマを貫通穴に使うのに対して、”底づき穴用”もしくは”止まり穴用”であれば、止まり穴も加工可能です。
スキルリーマの特徴とメリット
止まり穴、底づき穴用の工具がラインナップされている
スキルリーマの最大の特徴は、止まり穴にも対応している点です。
穴底形状に対応した3種類のスキルリーマがあり、それぞれに特徴があります。
・通し穴用(下図の左)は刃先が強い
・底づき穴用(下図の中央)は穴奥0.6mm手前まで仕上げられるエンド刃がついている
・止まり穴用(下図の右)は穴奥0.6mm手前まで仕上げられるエンド刃がついており、右ねじれで切粉を後方排出するが、穴が大きくなりやすい
これらを使い分けて加工を行うのがベストです。
私のおすすめは底づき穴用。止まり穴用と比べてリーミング性能が高く、エンドミルを使って取り代を0.05mm以下にしておけば止まり穴の加工も一応は可能です。切粉は前方に排出されてしまうため、止まり穴を加工する場合は下穴を2mm程度深めに入れておきましょう(下図)。下穴を深くできない場合は穴底面のキリ先端部が穴径の3分の2以上になるようにし、切粉の逃げ場を確保した上で、起動・停止ボタンを交互に連打し切粉を切る必要があります。
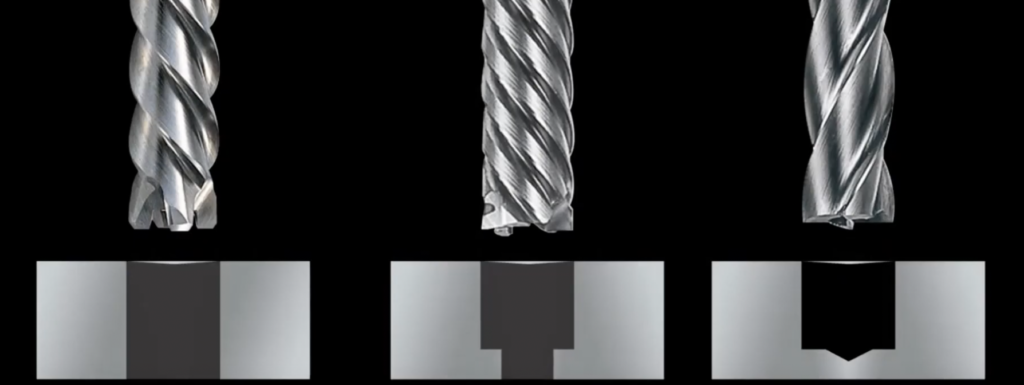
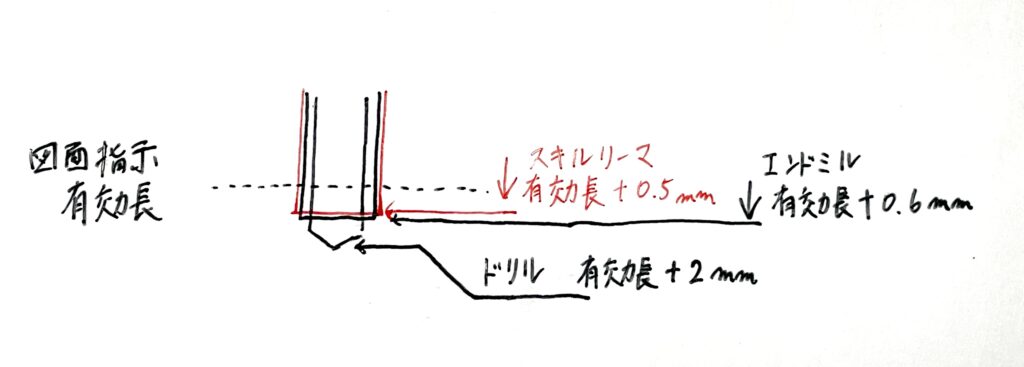
止まり穴のリーマ加工について詳しくはこちらの記事で解説しています!
食い付き長(不完全部)が短い(底づき穴用・止まり穴用)
例えば先程ご紹介したブローチリーマは食い付き長がかなり長いため、リーマをしっかり余分に通せるだけのスペースを確保しておかなければなりません。
一方でスキルリーマの底づき穴用・止まり穴用は食い付き長(不完全部)が短い特徴があるため、通しのリーミングでも板厚より深めに通す必要がありません。食い付き長はその多くが0.6mmになっています。
ステンレスでも問題なく加工できる
スキルリーマは、カタログ上でもステンレスに対応しています。
先程ご紹介したブローチリーマは対象ではありませんでした。
SUS304といったステンレスを扱う場合は、推奨となっているスキルリーマを使ったほうがブローチリーマを使うより安心感がありますね。
ちなみにですが、経験上取り代を0.05以下で少なめにとっておけばブローチリーマでもステンレスの加工は可能です。
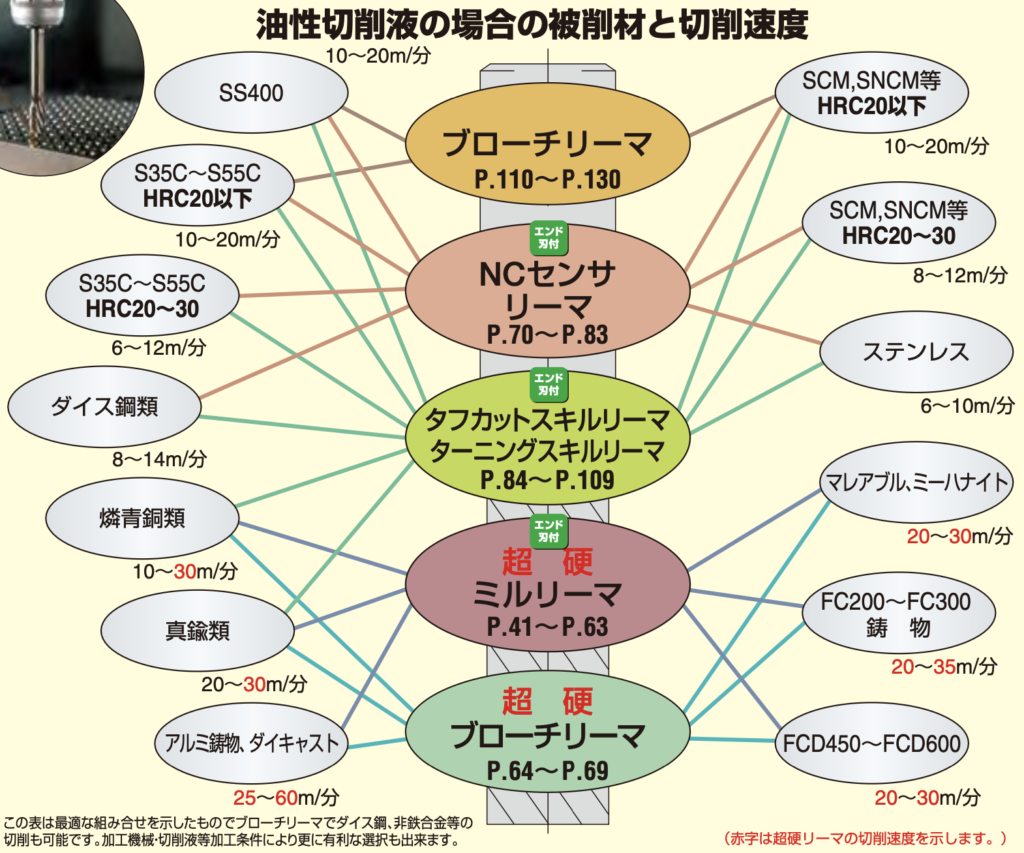
エンドミルでの穴曲がり修正なしでも使える
スキルリーマを使えばエンドミルを通さずに、下穴曲がりを修正しながらリーミングを行うことが可能です。
取り付ける工具や全体の加工時間を減らせるメリットは大きいですね。
とはいえ私はリーマの寿命を伸ばすために同径のエンドミルを通すためあまりやりません。同径のエンドミルを通せばリーマはドリルチャックで掴めますしね。
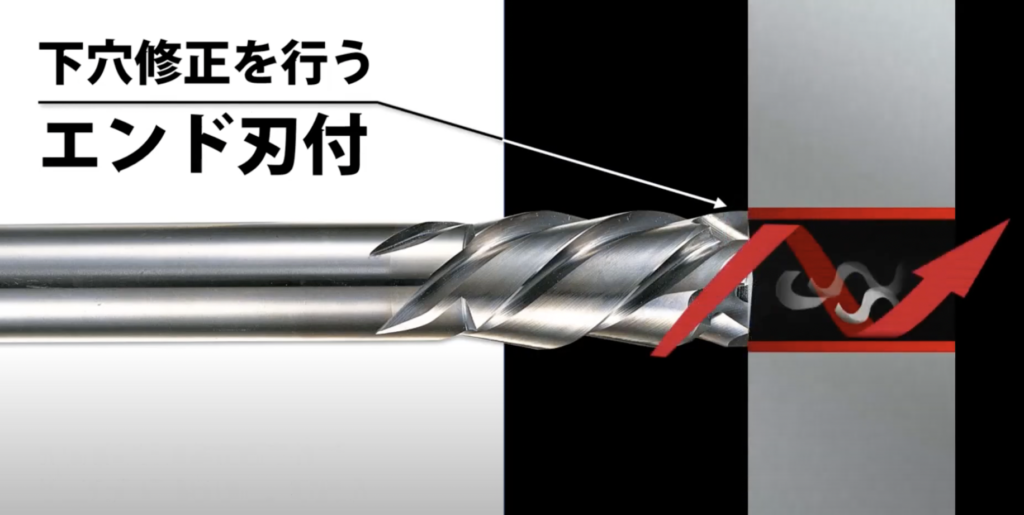
再研磨することでブローチリーマのようにも使える
私は普段底づき穴用のスキルリーマを使っているのですが、少なくともこのリーマの場合、刃先が傷んでも再研磨すればブローチリーマと同じように通し穴用のリーマ使うことができます。
再研磨したスキルリーマを使う場合、エンドミルで取り代を0.1mm以下にしてからリーマを通すようにしましょう。
スキルリーマのデメリット
今回はスキルリーマならではの加工ができる底づき穴用、止まり穴用のスキルリーマに限定してデメリットを解説します。
刃先が傷みやすい
特に底づき穴用と止まり穴用のスキルリーマは、ブローチリーマのような通し穴用のリーマと比べて刃先の耐久性が大きく劣ります。
摩耗によって穴径が小さくなってしまったり、チッピングして切れ味が悪くなることによって切粉が悪さをし、穴径が大きくなってしまうこともあります。
使う前に刃先をしっかり確認してから使う必要があります!
面取りが必要
底づき穴用と止まり穴用のスキルリーマは食付き部が約0.6mmと短いです。
そのため面取りをしておかないと食い付き時に刃先が暴れる可能性がありますので、面取りを行ってからリーマを通すようにしましょう。
ちなみに、同径のエンドミルを通し、取り代を0.05mm以下程度にしておけばリーマが暴れることがないため、面取りは必要はありません。
止まり穴は切粉のトラブルが起こりがち
リーマで止まり穴を加工する際は、切粉のトラブルがよく起こります。
加工前に仕上がり径と同径のエンドミルを下穴に通し、取り代を少なくしておくことで切粉のトラブルを減らすことができます。
下穴底面がフラットの穴は加工できない
スキルリーマの底づき穴用は下向きに切粉が排出されます。そのため、下穴底面がフラットの穴は切粉の逃げ場がなくなるため加工することができません。
また、止まり穴用も、切粉が上部に排出されるとはいえフラットの底面を加工するのは難しいです。
穴径の3分の2程度は下穴の先端部を残した状態でリーマを通すようにしましょう。
ハンドリーマ・マシンリーマ・チャッキングリーマ
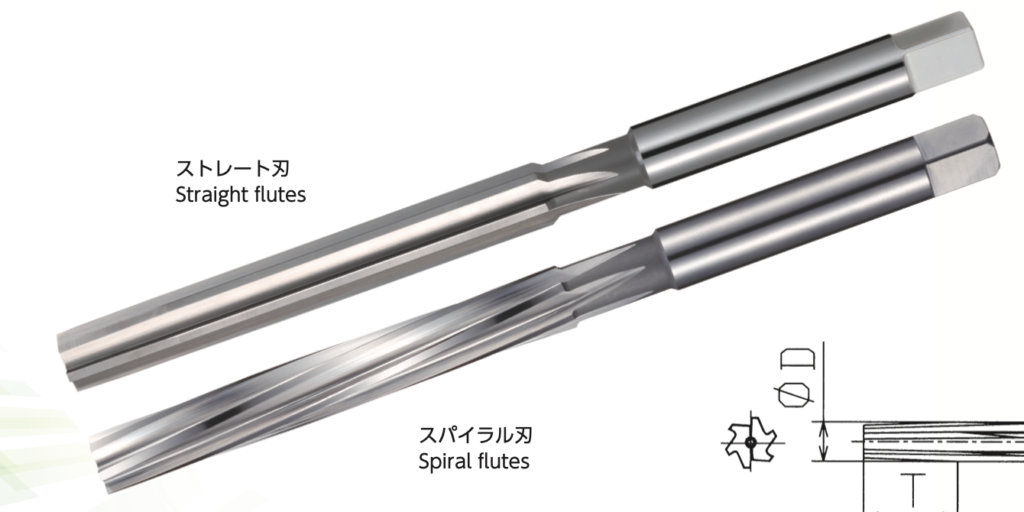
ハンドリーマは、タップハンドルを使って手作業でリーミングを行えるリーマです。
私の勤務先では基本的にあまり使いませんが、小径のものは0.1ごとに多くの径のものがそろえてあるため、中途半端な径の仕上げには重宝します。
ハンドリーマ・マシンリーマ・チャッキングリーマの違いは?
食い付き角 | シャンク形状 | 刃長 | |
---|---|---|---|
ハンドリーマ | 1° | 4面取り | 通常 |
マシンリーマ | 45° | ストレート モールステーパー | 通常 |
チャッキングリーマ | 45° | ストレート モールステーパー | 短い |
食い付き角の違い
ハンドリーマは、手で立てても食いつくように、食い付き部が1°のテーパーで長めにとってあります
一方、マシンリーマ、チャッキングリーマはフライス盤やマシニングセンタで使用することが想定されているため、食い付き角は45°で食い付き部の長さは短く、ハンドリーマほど深くまで通さなくても良い作りになっています。
シャンクの違い
ハンドリーマは下画像のようなタップハンドルでつかめるように4面取りが加工されています。
マシンリーマ、チャッキングリーマはストレートもしくはモールステーパーで、フライス盤やマシニングセンタで掴むのに適したシャンク形状です。
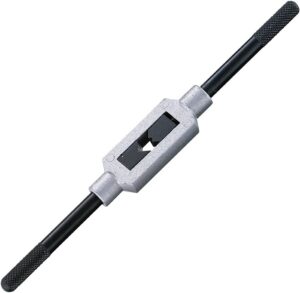
刃長の違い
ハンドリーマ、マシンリーマの通常刃長に比べ、チャッキングリーマの刃長は短くなっていることが特徴です。
ハンドリーマ・マシンリーマ・チャッキングリーマの特徴、メリット
ハンドリーマは手でも機械でも使える
ハンドリーマは、シャンク径φ13以下でしたら一般的なドリルチャックで掴むことができます。
そのため、手で通すだけでなく機械を使ってもリーミングを行うことができます。
φ13を超える大径になると、ドリルチャックで掴めないためハンドリーマは手で立てるのみになります。(コレットチャックに合うシャンク径のものを選んだり、治具を製作すれば掴むことは可能です。)
比較的安価
ブローチリーマやスキルリーマと比較して、ハンドリーマやマシンリーマは安価です。
使用頻度の低い径でコスト重視の場合、こちらを選択するのが良い場合もあります。
直刃は再研磨しやすい
直刃は再研磨を行いやすい形状です。
切れ味が悪くなったら再研磨を行って再利用しましょう。
再研磨時の注意点として、リーマにはほんのわずかにバックテーパーがついています。先端が太くなっており、根元側がほんのわずかに細いです。
そのため再研磨を行うとわずかに仕上がり径が小さくなることを知っておきましょう。
直刃とねじれ刃がある
ハンドリーマやマシンリーマには直刃とねじれ刃の両方がラインナップされています。
例えばキー溝の加工された穴にリーマを通す場合などは直刃だと空振りする部分があり真円に加工できないため、ねじれ刃を選択する必要があります。
こういった場合、ねじれ角はブローチリーマの方が大きいため、そちらの方が適しています。
ハンドリーマ・マシンリーマ・チャッキングリーマのデメリット
表面が荒くなりやすい
ハンドリーマやマシンリーマは、刃先の構造上ブローチリーマやスキルリーマに切れ味が劣ります。
表面が荒くなりやすいため、傷んできたら早めに再研磨や交換の対処をするようにしましょう。
止まり穴は加工できない
ハンドリーマやマシンリーマを通した際、切粉は下向きに排出されます。
切粉のつまりが起きてしまう上、食付き部がある程度長いため、止まり穴を加工することはできないと考えておいた方が良いでしょう。
切削条件を上げられない
これらのリーマは良くも悪くも最も基本的なリーマなので、切削条件はφ10程度の小径のものでも回転数200rpm程度、送りも40mm/min程度に抑えておく必要があります。
取り代を大きくできない
同様に、取り代についてもあまり大きいものには対応できません。取り代は大きめでも0.1mm程度にしておくのが無難です。
切削抵抗が大きい
特にハンドリーマは食付き部の角度が1°のため、切削抵抗が大きくなりやすいです。
びびりが発生したり、カジリによってリーマが動かなくなってしまう場合もあるため、取り代は少なめにし、しっかり油で潤滑性を高めた上で加工を行いましょう。
テーパーピンリーマ
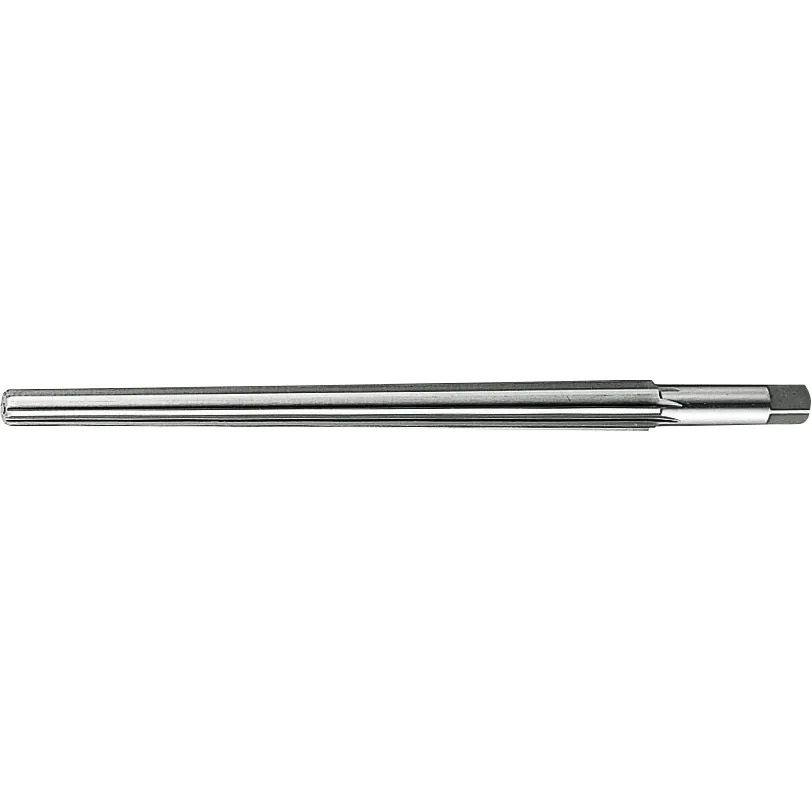
テーパーピンリーマはハンドリーマがテーパーになったものです。
テーパーピン穴の加工に使用します。
使用方法や注意点はハンドリーマに準じますが、テーパーになっており下穴を繰り広げる必要がある分切削抵抗が大きくなり、切粉も増えますので、油をしっかり供給しつつ、切粉の排出に気を遣いながら加工を行いましょう。
ブリッジリーマ
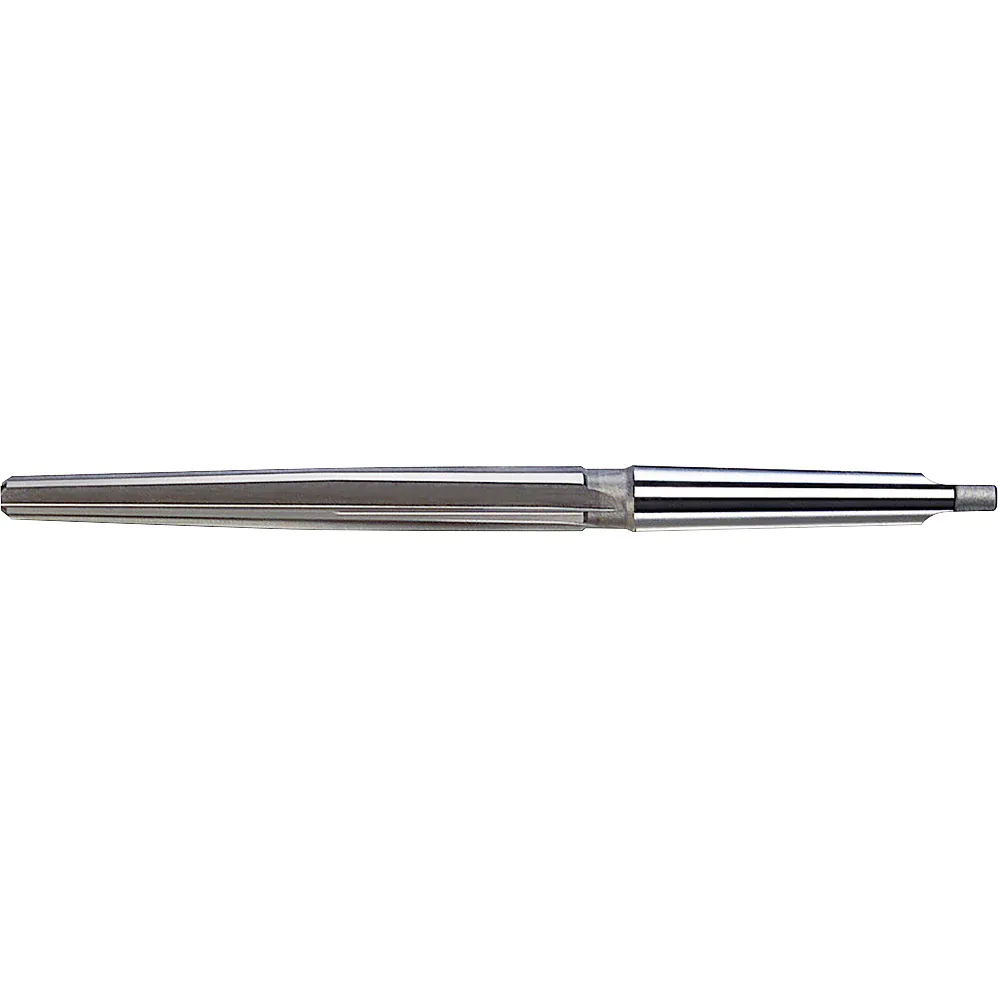
ブリッジリーマの特徴・メリット
ブリッジリーマは一見マシンリーマと似た形状ですが、先端食付き部が大きいく長いテーパーになっているのがわかりますね。
ブリッジリーマは大きい取り代からリーミングを行うことに特化した比較的マイナーなリーマです。
例えばφ10のブリッジリーマであれば、テーパー部の始まりの径がφ7.5、3.8°のテーパーで、55のテーパー長さです、ハンドリーマと比較してテーパー部自体もかなり長いですし、角度も大きくなっていることがわかります。
先端の径は仕上がり径の75%ほどの径になっているため、仕上がり径の2割もの取り代が残っていたとしても加工できるといえます。
とはいえ、切削抵抗が大きく、板厚が厚いと難易度が大きく上がる、難しいリーマです。
ブリッジリーマのデメリット
ブリッジリーマのデメリットは、ハンドリーマ・マシンリーマで挙げたものに加えて2点あります。
・大きい取り代のため、切削抵抗が大変大きくなる
・多くの切粉が出るため、切粉のトラブルが起こりやすい
どちらの問題も、板厚が厚く、穴深さが深くなるほど大きくなります。
初めて加工する場合は、一度試し加工を行ってからの本加工をおすすめします。
シェルリーマ
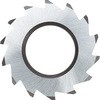
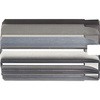
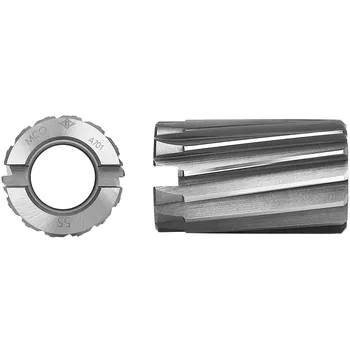
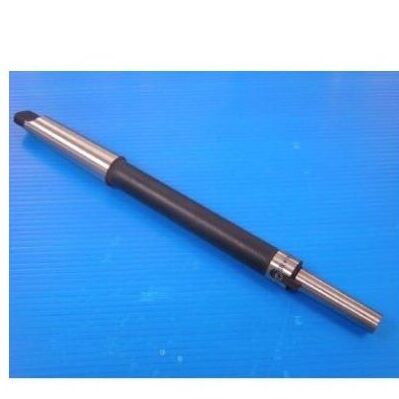
シェルリーマは、大径加工用のリーマです。
大きな特徴として、刃部とシャンク部が別々になっています。
画像のようなシェルリーマアーバーにリーマを装着し、使用します。
刃の形状はマシンリーマと同様のため、同じような点に注意すれば加工が可能です。大径のため、通常より傷が目立ちやすい点に注意して加工を行いましょう。
デメリットとしてはその値段です。岡崎精工製のシェルリーマでφ70ともなると、安価なモノタロウでも10万くらいの価格でした。使用されるハイスの量も多く、比較的出荷量も少ない工具のためかと思いますが、なかなか値が張りますね。
超硬リーマ
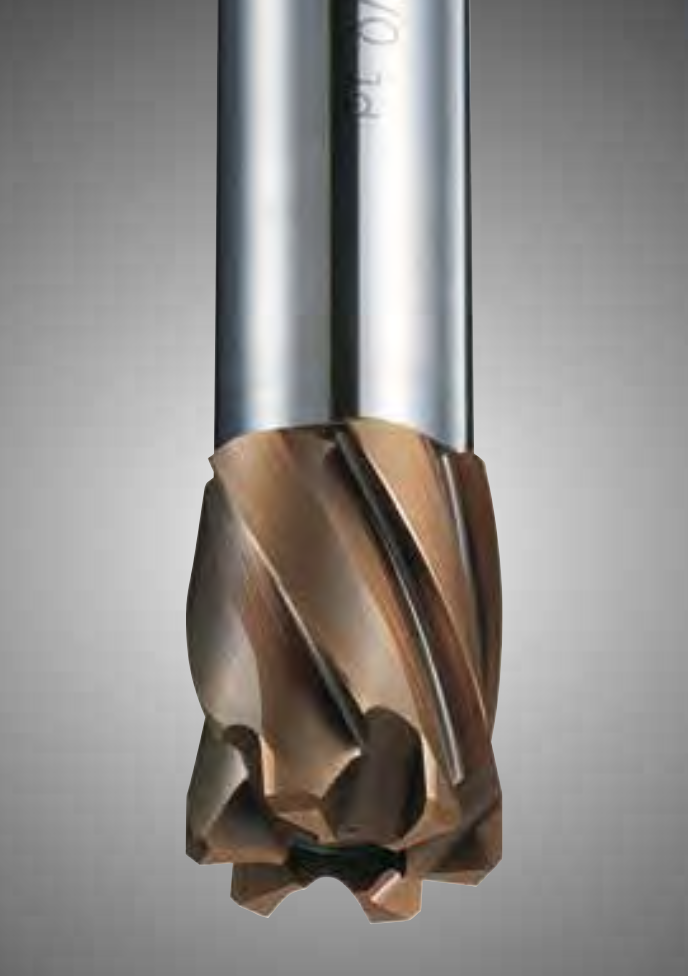
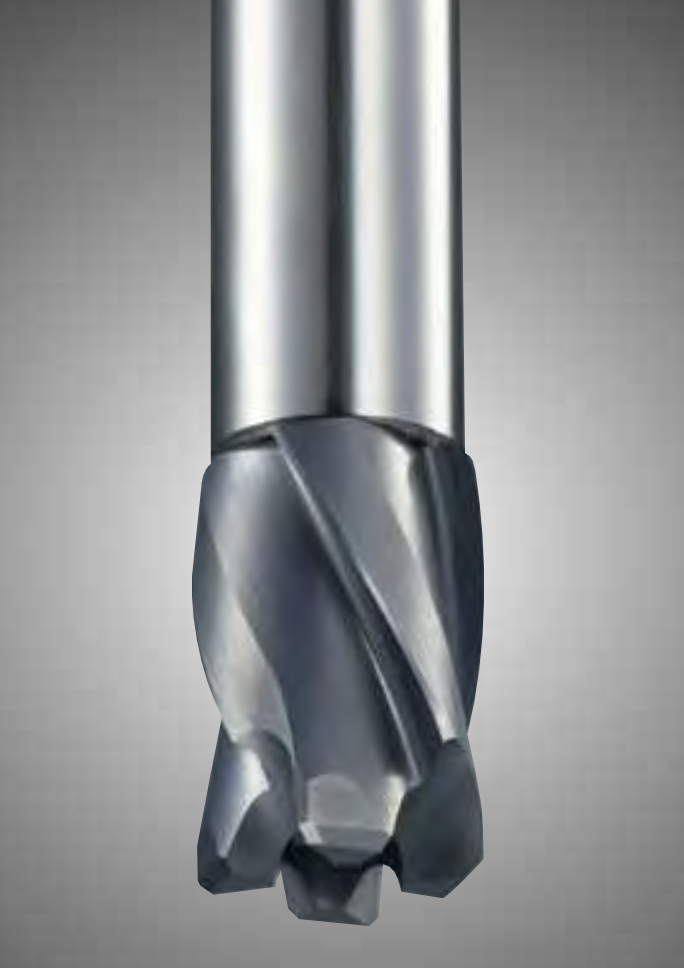
超硬リーマの特徴・メリット
超硬リーマは、硬度の高い超硬を使ったリーマです。
ハイスのリーマよりも切削速度を上げることができ、摩耗も少なく長寿命です。
大体ですが、対応する切削速度はハイスリーマの2倍です。つまりスピード的にも倍くらいで加工できます!
日研からは、インコネルやチタン合金などの難削材に対応したリーマも販売されています。そういったリーマには、溶着や加工硬化を防ぐため、切れ味を向上させ、耐溶着性のコーティングが施してあります。
また、ハイスのものと同じように底づき穴用と止まり穴用のものもあります。
超硬リーマのデメリット
超硬リーマはハイスリーマより靭性が低いため、低切削速度域や断続切削で刃先が欠けやすいです。
チッピングを防ぐため、工具のカタログを確認した上で、推奨切削速度の範囲内の設定に収めるようにしましょう。
もう一点のデメリットとして金額が挙げられます。超硬工具はハイスよりも高価ですので、少量多品種加工の場合はハイスのほうがコストパフォーマンスに優れていると言えます。
アジャスタブルリーマ
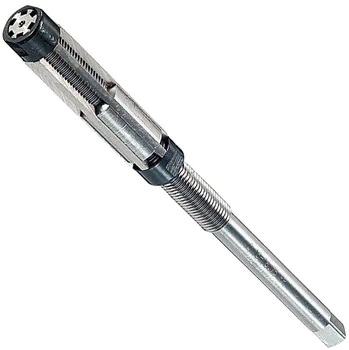
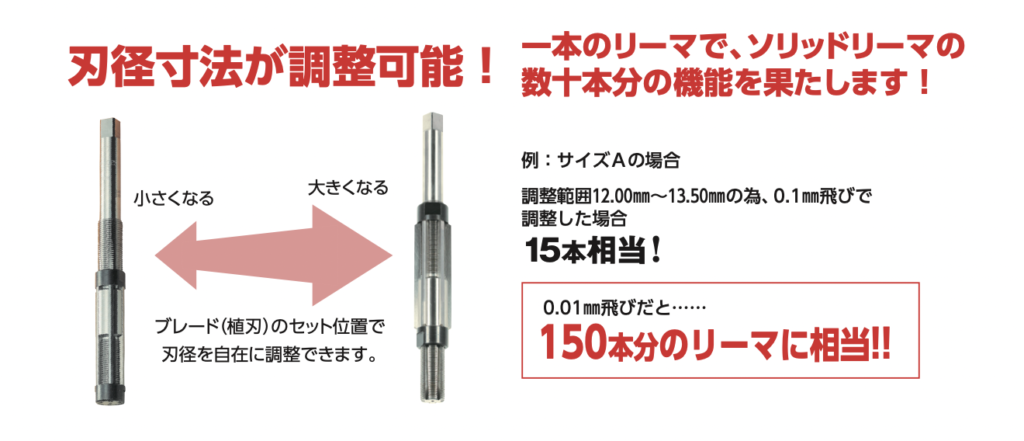
アジャスタブルリーマは、なんと刃径を調節できる大変特徴的なリーマです!!
FPツールから発売されており、この名称もおそらく商品名です。
アジャスタブルリーマの特徴・メリット
様々な径の公差穴を仕上げられる
アジャスタブルリーマは、調節機構が無段階です!つまりどんな径の公差穴でもねらって仕上げることが可能です。
上の図にも記載されているとおり、1本で複数本の役割を担えるリーマです。
摩耗にも調整で対応可能
無段階で調節できるため、切れ刃が摩耗して小さめの穴に仕上がるようになったとしても、調節することでもとの寸法で加工することができます。
複数本をまとめられれば経済的
端数のリーマを多く持っている場合などは、アジャスタブルリーマに絞ることで工具本数を減らすことができます。
複数のソリッドリーマが必要になる場合、アジャスタブルリーマを使えば経済的です。
現物合わせの加工が可能
はめあいの寸法が正確に分からない「現物合わせ」加工でも、無段階調節が活きます。
アジャスタブルリーマであれば現物に合わせたリーマを購入する必要がなくなります。
アジャスタブルリーマのデメリット
調整作業が手間
前項に掲載した動画のように、寸法調整はなかなか大変な作業です。
マイクロメーターで測りながらの作業になるため、時間がかかる作業になってしまいます。
失敗できない公差穴は試し削りが必要
寸法調整になれないうちは、穴径がマイクロメーターで測った測定値と同じになるかどうかは分からない部分があります。
測定誤差や、切削にあたって穴径拡大する場合もありますので、ミスできない場合まずは試し削りが必要です。
普段使い慣れているリーマであればその必要はないため、その分時間がかかってしまいます。
どのリーマを使えばいい??
本記事では様々なリーマをご紹介しました。
その中で、私の勤務先で使用しているのは、ブローチリーマ、スキルリーマ、ハンドリーマ、マシンリーマのみです。
その中でも基本的にブローチリーマとスキルリーマを使っています。
止まり穴はスキルリーマ、通しはブローチリーマと使い分けています。
スキルリーマは底づき穴用がほとんどで、止まり穴の場合でも、下穴を2mm程度深めに開け、同径のエンドミルを通した上で、底づき穴用でリーミングを行ってしまいます。
下穴を浅めにする必要がある場合は、止まり穴用のスキルリーマを選ぶのも良いかと思います。
ハンドリーマとマシンリーマはブローチリーマやスキルリーマがない端数の径のものや、φ12を超えるような比較的大きいリーマでしか使いません。
どのリーマも使えるようになった上で、加工内容に応じた工具を選択できればベストかと思います!!
コメント