
以前の記事、「旋盤の使い方〜基礎編〜」では、ワークをクランプするところから削るところまでの大まかな流れを解説しました。
本記事では、「削り」にフォーカスを当て、基本的な削り方をより細かくレクチャーしていきます!
ワークをクランプ・工具を装着する
削りの作業に入る前にまずはワークをチャックでクランプ、工具を装着しましょう。
4つ爪の場合は簡単なトースカン芯出しも行います。
クランプと工具取付の方法については基礎編を参考にしてください!
クランプしたらいよいよ切削作業に入っていきます。
外径切削
初めに解説するのは旋盤加工の基本となる外径切削です。
今回は最も基本となる材質であるS45Cを使って、下画像のようにφ50黒皮材をφ30に加工してみましょう。端面も仕上げます。
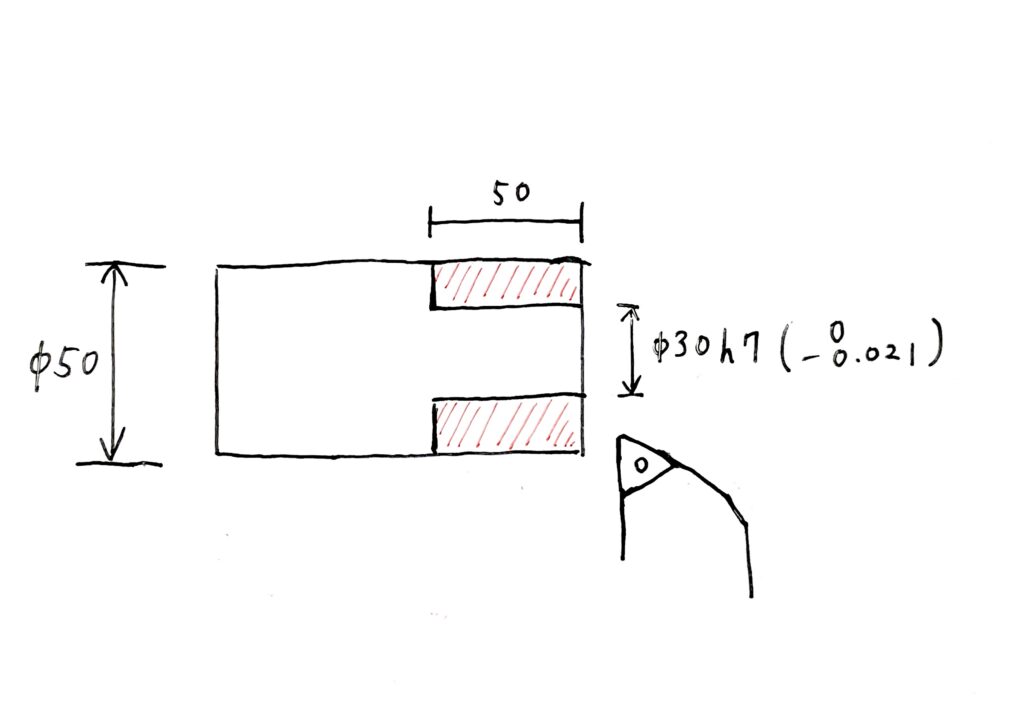
荒加工
まずは荒加工です。仕上げしろを端面方向(Z方向)に0.1mm、径方向(X方向)に直径値で0.5mmつけて、形状を削り出します。
この仕上げしろが大きすぎると仕上げのときに手間になりますし、小さすぎると擦れ摩耗の原因になったり公差が安定しなくなるため、径で0.5mmくらいが丁度良いと思います。
使用工具はノーズR0.8のサーメットの刃物とします。
刃物の形状は下画像のようなものです。このブレーカー形状であれば切粉が飛び散らず、汎用旋盤での加工に向いています。
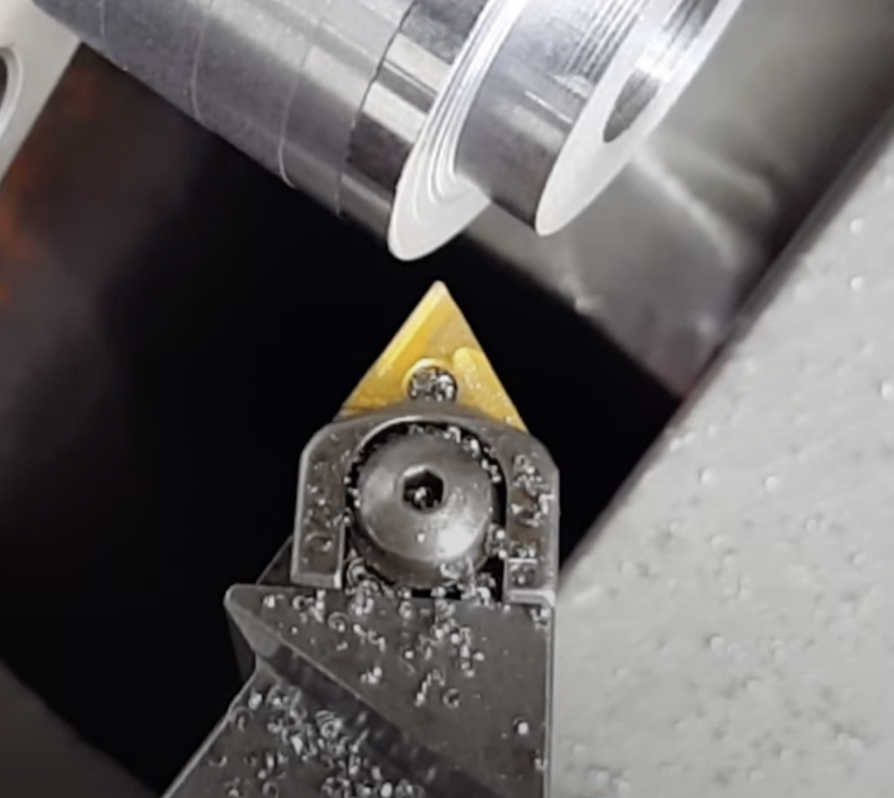
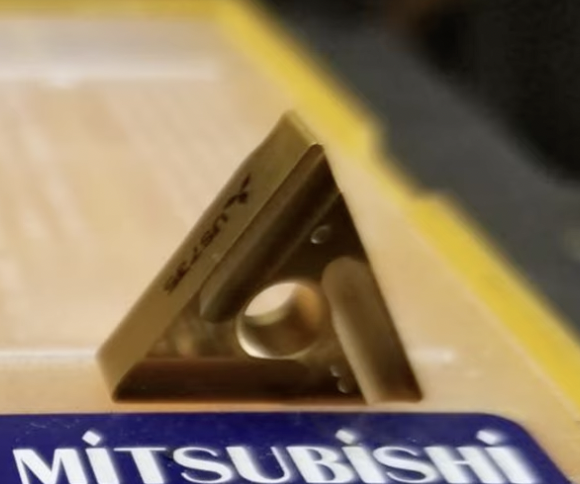
端面の捨て削りを行い、その点を0とする
まずは材料端面をまっすぐに整え、長手方向(Z方向)の刃先位置をゼロセットするため、端面を捨て削りします。
0.5も削ればOKです。
捨て削りの流れは以下の通り。
- ワークを600rpmほどで回転させる
- ワーク端面に面当てを行い、刃物を手前(Xプラス方向)に逃がしてからZをゼロセット
- 長手方向(Z方向)に0.5mm切り込む
- 手送りで、奥側(Xマイナス方向)に向かって切削する
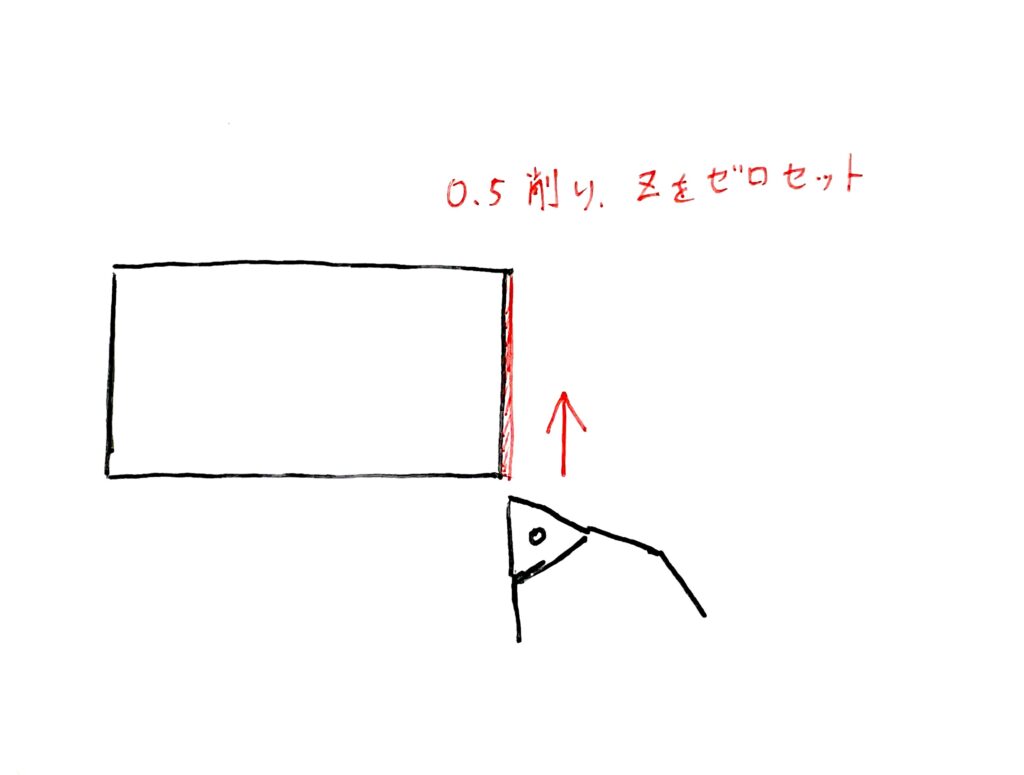
注意点として、上画像のような形状の刃物の場合、基本的に端面切削はノーズRより小さい幅しか削ることができません。つまりノーズR0.8であれば、0.5mmの幅を1回で削れますが、ノーズR0.4でしたら2回に分けて削る必要がでてきます。
まず、削るにあたって必要となる作業が「面当て」という作業です。
ゼロセット
ダイヤルやデジタルスケールの表示をゼロにする作業です。NC旋盤での原点設定に似ています。
闇雲にゼロにして良いわけではなく、後に解説する「面当て」を行った点や、捨て削りを行った点でゼロセットを行います。
この作業を行うことで寸法を把握しながら削ることができるため、旋盤加工をする上で何度も行うことになる超基本の作業です。
面当て(つらあて)
刃先をわずかにワーク表面にこすらせ、その点でゼロセットする作業です。
この作業を行うことで、大体0.01~0.03mmの精度で刃先位置を合わせることができます。
端面の面当ては刃物台ハンドルを使って行うのがポイントです。
ポイントとしては、面当てをしてゼロセット後、0.5切り込むことになると思いますが、そのように細かいハンドルの動きが必要なときは、細かくハンドルを戻しながら「コンコン」と小さく素早いノックをするようにハンドルを操作するとやりやすいです。このときにハンドルは持ち手ではなく外周を持って操作しましょう。
手送りの際は、一つのハンドルを両手で持ち、なるべく一定の送り速度になるように回します。
切削の抵抗があると思いますが、その抵抗を受けても一定速度で変化なく送れるとベストです。
これで端面の捨て加工、ゼロセットまで完了です。
外径荒加工を行う
いよいよ外径荒加工です!手順は以下のとおりです。
- ワークを回転させる
- 外径の面当てを行い、削りの終点に印をつける
- 1mmほど切り込んでゼロセットし、長手方向に10mmほど捨て削り、
- 回転を停止し、削った箇所をノギスで測定
- 再び回転させ、目的の位置(X30.5、Z-50)まで4mmずつ切り込んで削る
- 完成。ノギスで測定して寸法を確認

外径の面当て
それでは作業をはじめていきましょう。
まずは径方向の面当てを行います。
外径にゆーっくり刃先を近づけ、当たったところでゼロセット(X)します。
このときに削りの終点に刃物を当て、印をつけておきます。(今回はZ-49.9)
印があることで、自動送りの際にどこで止めればよいのか一目瞭然です。
外径の捨て削り
黒皮材はいびつな形状をしており、径の大きさがあてになりません。まずは測定面を作るため、1mmほど切り込み、そのX座標を再びゼロセット、長手方向に10mmほど捨て削りを行いましょう。
削る際は手送りでも良いですが、基本的に自動送りを使います。
基礎編で解説したように、送り表を見ながら希望の送り速度にレバーを合わせましょう。
基本的な送り速度(f)の目安
荒加工:0.25mm/rev
仕上げ加工:0.1mm/rev
送り速度の合わせ方
今回は荒加工ですので、下の旋盤でしたらA-C-G-4にレバーを合わせれば送り速度が適正の約0.25mm/revになります。
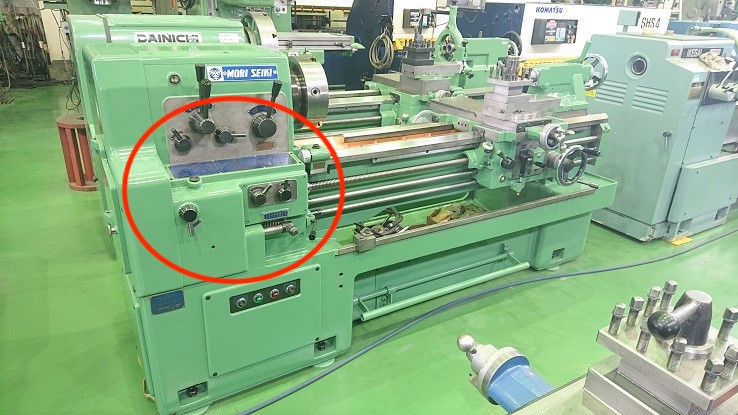
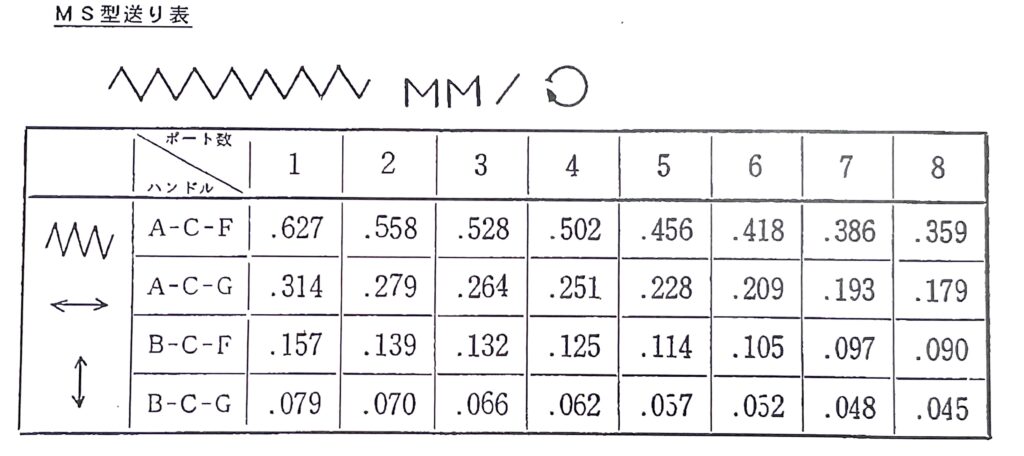
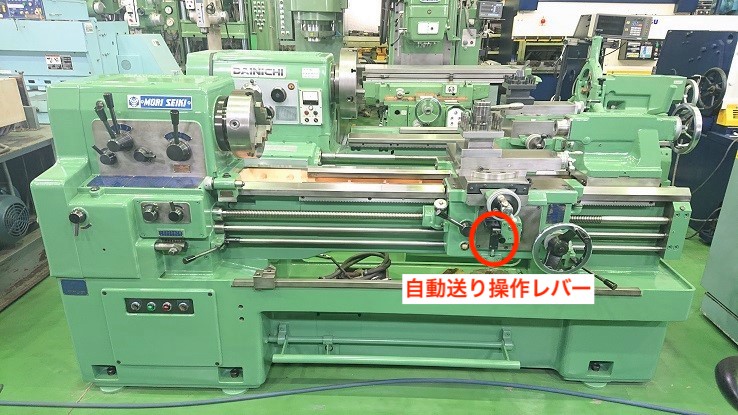
自動送りでは、送り速度が間違っていると最悪刃物とワークや機械が衝突してしまい、事故になりますので必ず素振りを行ってから切削を行うようにしましょう。
削り終わったら、削ったところをノギスで測定し、例えばφ48.80でしたらφ30まであと18.80削れば良いことになります。
削りしろを0.5mm残すため、あと18.30ですね。
私はミスを防ぐため、目標地点をゼロに合わせるようにしています。
荒加工の切り込み量はクランプ状況などにもよりますが、径で4mmくらいが基本になります。
18.30mm削る場合、5回に分けて削ることになります。
自動送りの終わりは少し手前で止め、手送りで最後まで送る
荒加工の際の注意点として、自動送りの削り終わりの際は、行きすぎないように終点の少し手前で止めるようにすると良いです。
今回の例では、あらかじめつけておいた印の手前で自動送りを止め、それから縦送りハンドルを使った手送りで「トントン」とノックするようにぴったりZ-50まで合わせてやります。
そうすればシビアに自動送りを止める必要がなく、正確に加工することができます。
削り終わったらノギスで確認して荒加工完成
荒加工が終わったら回転を止め、ノギスで再度確認しておきましょう。
今回の例では径がφ30.5、深さが50になっていればOKです。
仕上げ加工
荒加工が終わったら次は仕上げ加工です!
仕上げ加工では下の写真のようなサーメットの刃物を使っています。
写真のものはノーズR0.4ですが、私はびびりやすい局面が多いため基本的に仕上げはノーズR0.2しか使いません。
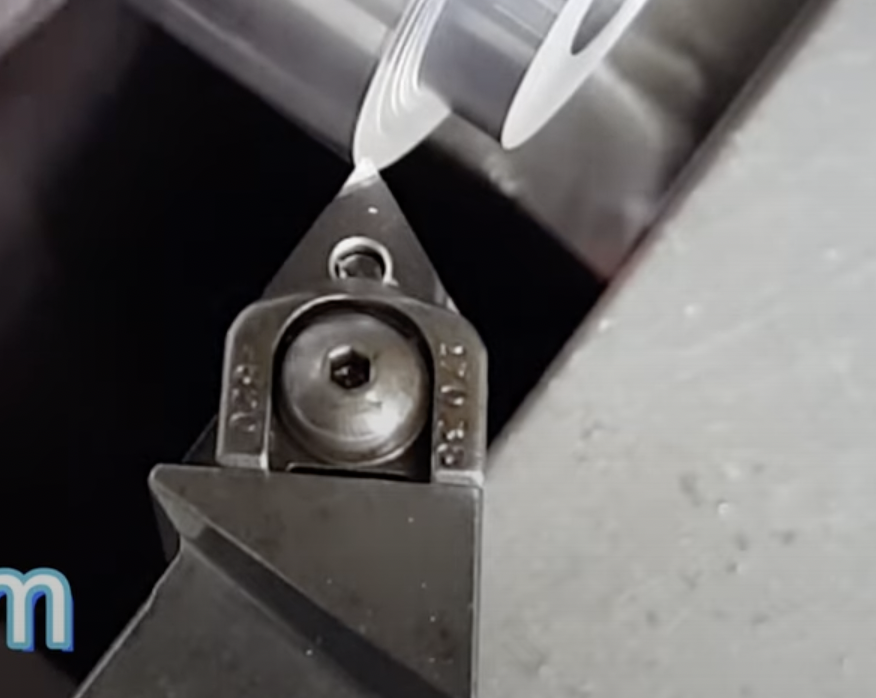
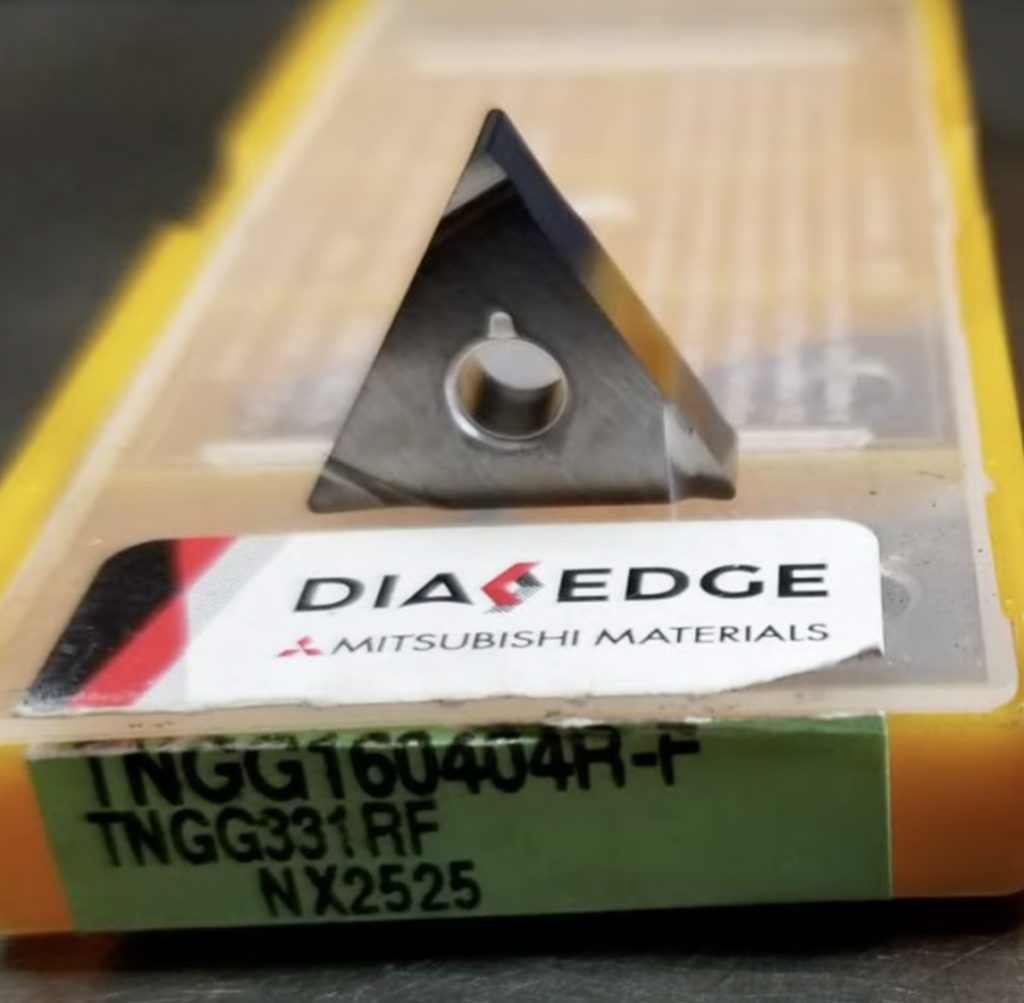
仕上げ加工の手順
仕上げ加工は以下のような手順で行います。
- ワークが冷却されていることを確認する
- ワークを回転させ、端面に面当て、Z方向のゼロセット
- Z方向に0.1mm切り込み、再びゼロセット、端面仕上げ加工を行う
- 外径に面当て、X方向もゼロセット
- X方向に0.2切り込み、再びゼロセット、1度目の仕上げ加工を行う
- 回転を止めて外径をマイクロメーターで測定
- 仕上げ寸法まで切り込み、2度目の仕上げ加工を行う
- 仕上げ完成。寸法を測定
- 同様に端面を仕上げる
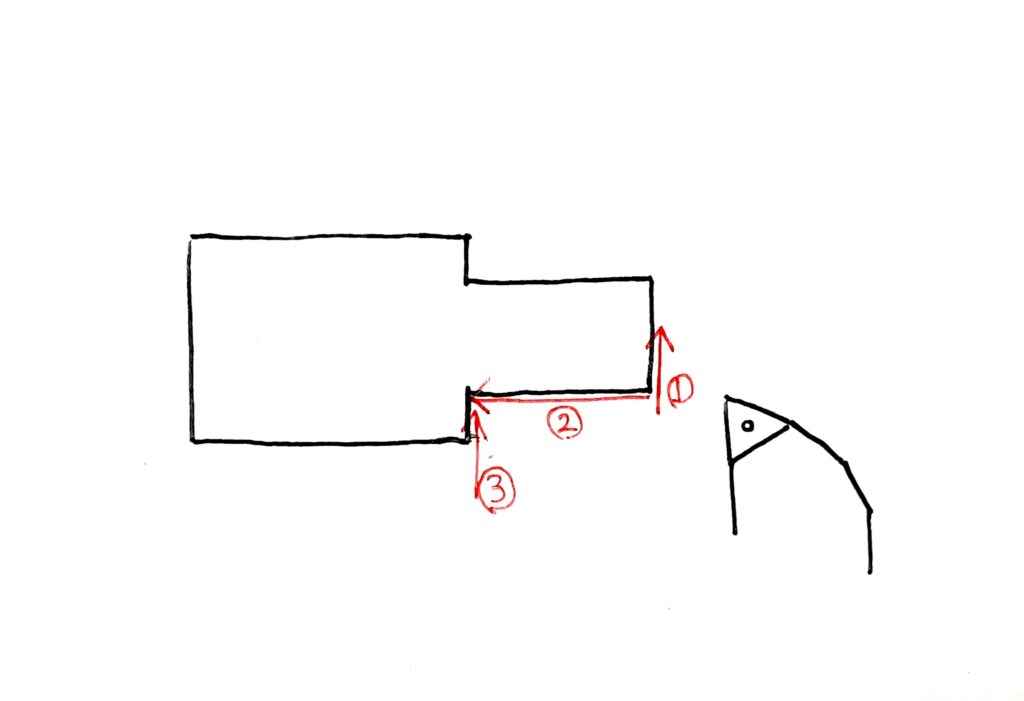
端面を仕上げる
仕上げの前は、必ずワークが冷えていることを確認しましょう。温度変化で寸法が狂ってしまいます。
温度変化に関する記事はこちら!
まずは端面から仕上げていきます。
回転数は1200rpmくらいが丁度良いです。MAXの約2000rpmで回しても構いませんが、特に初めのうちは少々怖いですので。
Z方向にゼロセットし、0.1mm切り込みます。端面の状態にもよりますが、0.05くらいでも十分な場合が多いです。
切り込んだら再びゼロセットをしておきます。
そして端面仕上げ。横送りハンドル(前後に動かすハンドル)を両手で持ち、一定のスピードになるように奥に向かって手送りで仕上げます。
自動送りを使いたい場合は、中心だけ手送りで送り、中心から手前に自動送りで送る方法もあります。私は自動送りを使うことが多いです。
中心付近は切削速度が低くなるため、刃先が傷みやすいです。中心付近で刃先が欠ける場合は芯高を確認しましょう。
外径を仕上げる
そしていよいよ公差部である外径仕上げ。
交差に入れるので、2回に分けて仕上げます。
測定のための一回目、本仕上げのための二回目といったイメージです。
仕上げの一回目と二回目で削り量をなるべく同じにすることが、正確に公差に入れるポイント!!
一回目の仕上げで中間値を狙うため、まずは荒の状態の径をノギスで測っておきましょう。
端面仕上げのときにZ方向はゼロセットできていますので、X方向の面当てを行います。
この面当ても正確めに行うことで、2回の仕上げの削り量を揃えることができ、高精度な加工につながります。
X方向に半分だけ切り込み、自動送りで削っていきます。送り速度はf0.1mm/revが目安です。
切り込み量は、例えば元の径がφ30.56であれば、φ30との中間、φ30.28になるように狙ってゼロセットすると良いです。
中仕上げを挟んで3回仕上げる場合や、公差がそれほど厳しくない場合は0.2くらい残るようにキリの良い数字を使ってもOKです。
合わせ終わったら自動送りでZ-49.9まで削りましょう。
Z-50まで送ってしまうと仕上げの弱い刃先でコーナーにぶつかってしまいますので、刃先が傷んでしまう可能性があります。
0.1残し、端面は最後に仕上げるのがポイントです。
一回目の切削が終わったらマイクロメーターで測定します。このとき例えばφ30.25であれば、狙いであるφ29.99まで残り0.26ですので、0.26切り込んで再びゼロセット、最終仕上げを行います。
うまく削れれば、ぴったり公差に入るはずです。
段の端面と面取りを加工して完成!
最後にZ-50まで刃先を持っていき、X方向に送って端面も仕上げましょう。
最後に面取りをして完成です!
内径切削
内径切削も、基本的には外径切削と同じ手順ですので、手順は省略します。
外径加工時にはないポイントのみ記載しておきます!
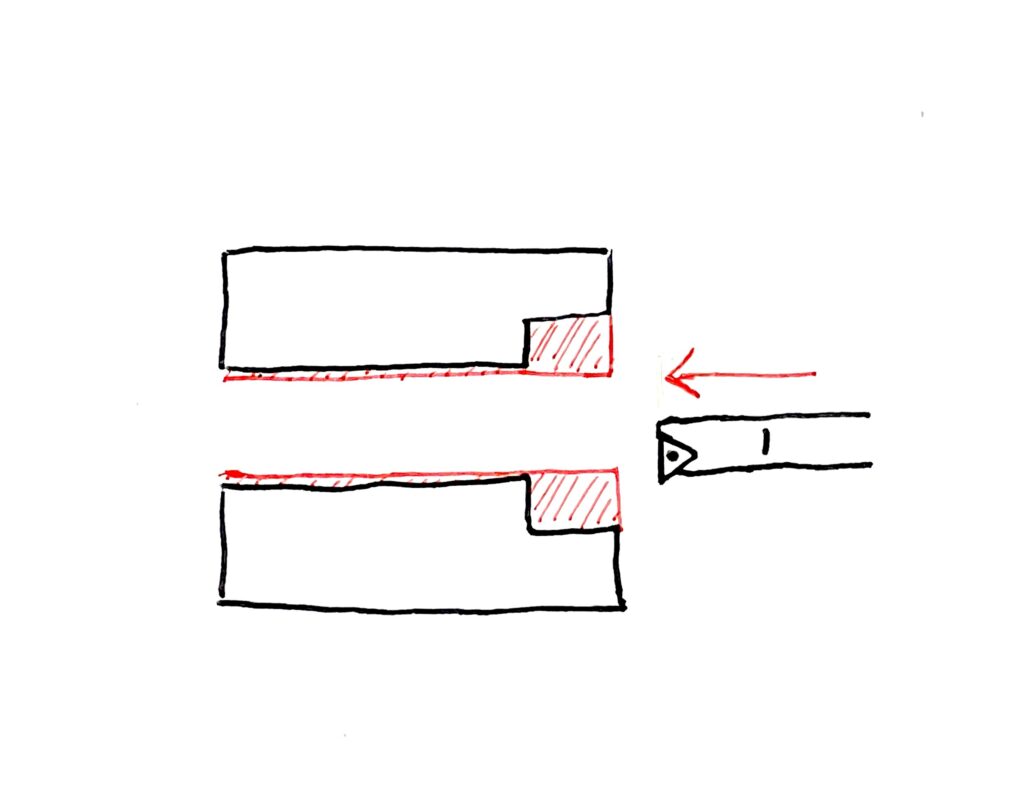
荒加工時のポイント
汎用旋盤の場合、基本的に荒加工はキリで終わらせます。例えばφ30の内径を仕上げたければ、φ29のドリルで穴を開け、直接仕上げに入ります。
キリが使いにくい大きめの径の場合や、段の加工がひつような場合だけ荒加工を行います。
荒加工の手順は、刃物の向きが変わるだけで基本的に外径と同じですが、びびりやすい加工のため刃物の突き出し長さは短めに設定するようにしておきましょう。
内径加工は荒用の刃物を装着するのが面倒なので、削り量が少ない場合はなるべく仕上げの刃物1本だけで終わらせてしまいます。
内径仕上げ加工のポイント
内径加工は、基本的ながらも経験が必要な奥が深い加工です。
荒加工でもそうですが、内径加工では、「刃物の突き出し長さ」という要素が加わります。
突き出し長さが長めで不安定な加工になってしまう場合、特に公差に入れる必要がある仕上げ加工で問題が出てきます。
具体的には「刃先の逃げ」が厄介です。 刃物の突き出しが長い分、刃物がたわんでしまうわけです。
そのため内径仕上げ加工も外径仕上げ加工と基本的に手順は同じですが、中仕上げの重要度が高くなります。
刃物の突き出し長さにもよりますが、外径と同様に2回の仕上げで削り量が違うと刃物の逃げ量が変わり、公差から外れてしまいます。
突き出し長さが長めで不安定な加工の場合、まずは中仕上げで一度測定面を作り、しっかり測定してから2回の仕上げで均等に削るという計3回の仕上げ加工を行うのがおすすめです。
イメージとしては残り0.5の状態から、0.4→0.2→0というように3回加工するということです。
NC旋盤の要素も入った記事ですが、こちらも参考にしてください!
びびりも問題になりやすいので、びびる場合はこちらの記事も役に立つと思います。
穴あけ加工
心押台を使って穴あけ加工を行う
穴あけ加工は、基本的に心押台を使って行います。心押台は下の動画のようにその本体が前後に動くようになっており、後部のハンドルを回すことで芯押し軸という軸部が前後します。
加工の際は心押台本体はクランプしておき、後部のハンドルを回して芯押し軸を押し出すことで穴あけ等を行っていきます!
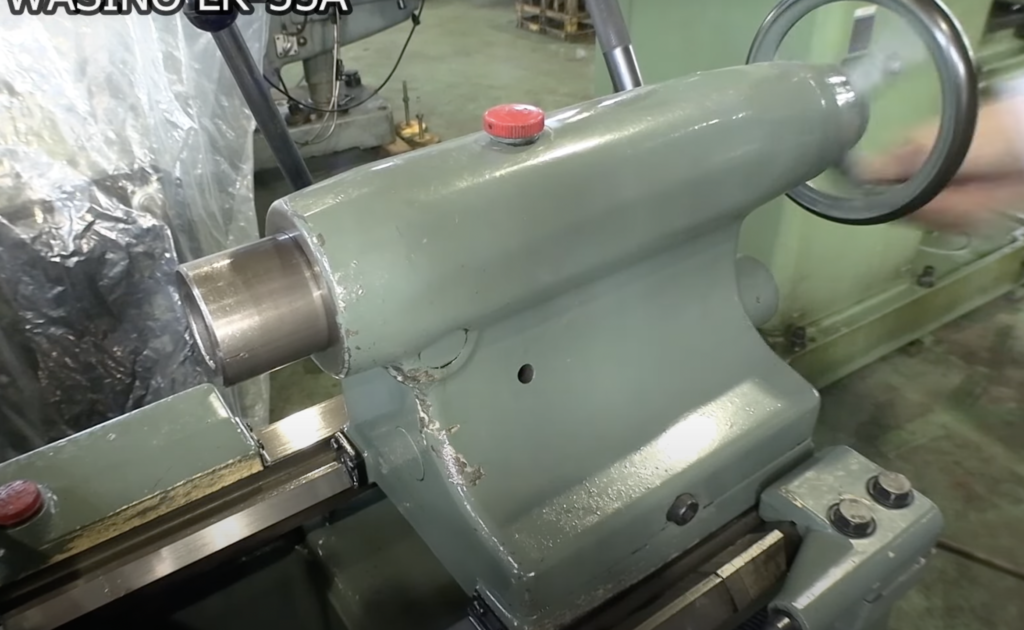
ドリルチャックを使った穴あけが基本
汎用旋盤での穴あけの基本はドリルチャックを使った穴あけです。
まずは芯押し軸に、下画像のようなドリルチャックを装着します。
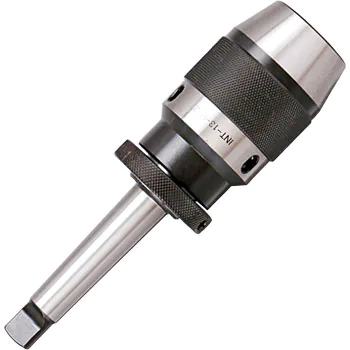
センタリングを行う
はじめに行うのがセンタリングです。
芯もみともいい、下画像のようなセンタドリルを使い、ドリルが暴れないようガイド穴をあけます。穴あけの際には基本的に必要になる作業です。
センタドリルをドリルチャックにつかみ、比較的ゆっくりめにハンドルを回して送りましょう。
回転数は高めが良いです。具体的には、S45Cなどの普通の鋼材であれば1000rpmくらいで加工しています。
折れやすいためかならず切削油を塗って加工するようにしましょう。
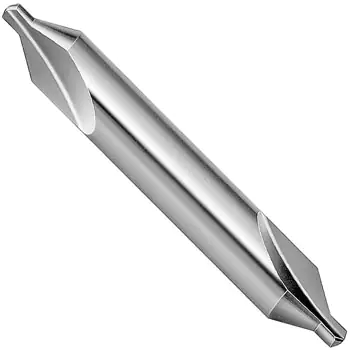
穴あけ加工を行う
次にハイスドリルをドリルチャックに装着し、加工します。
鋼材では加工条件は切削速度20m/minが目安ですが、大体500rpmくらいでやってしまっています。
ドリル径にもよりますが、ゆっくり送りすぎると刃先が摩耗しやすくなります。ある程度速めに送るようにしましょう。
深さ寸法の指示がある場合はハンドルのメモリを使って寸法を合わせましょう。
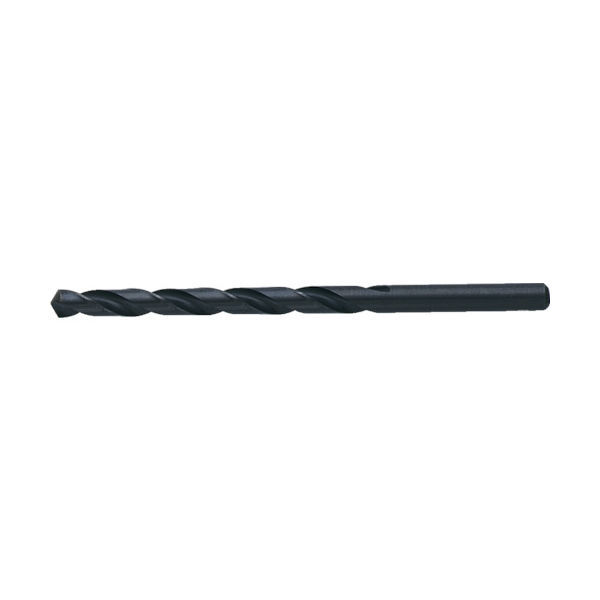
φ13以上のドリルは直接芯押し軸に装着する
ドリルチャックには基本的にφ13以下のドリルしか掴むことができません。
それ以上、つまりφ13.5以上になると直接芯押し軸にドリルを装着します。
ドリルの径が大きいとその分抵抗も大きくなるため、ワークが引っ込んでしまわないように気をつけながら穴あけ作業を行いましょう。抵抗が大きい分しっかり力を込めてハンドルを送ってやります。
φ40など径が大きくなってくると抵抗が大きすぎて一度に穴をあけるのは難しくなるため、一度小さい径で穴を開けてから大きい径で繰り広げるような形で加工しましょう。
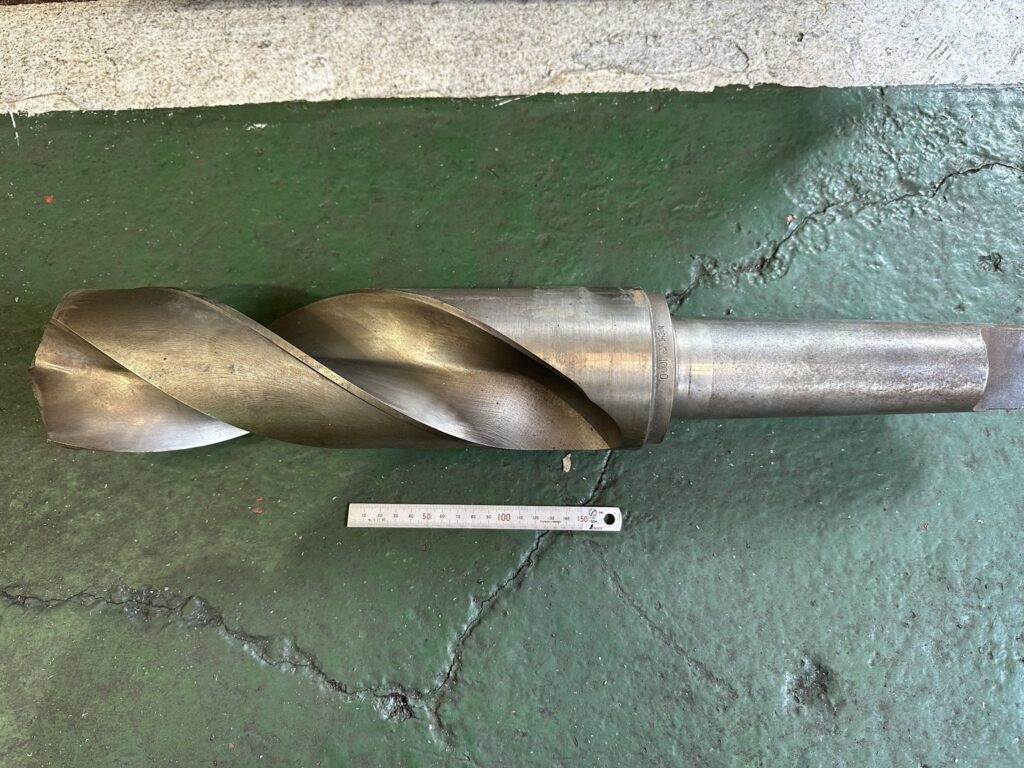
溝入れ・突切り
溝入れや突っ切りも基本的には外径切削とやり方は変わりません。
X方向に真っ直ぐ削り、中心まで刃先が届くと突っ切ることができます。
浅い溝入れよりも突っ切り加工のほうが溝深さが深くなりがちで、切粉噛み込みなどのトラブルが起きやすいです。
切削油をかけながら加工を行うようにしましょう。
突っ切りは、擦れ摩耗を防ぐため、刃物が欠けない程度に速めに送るのがコツです。
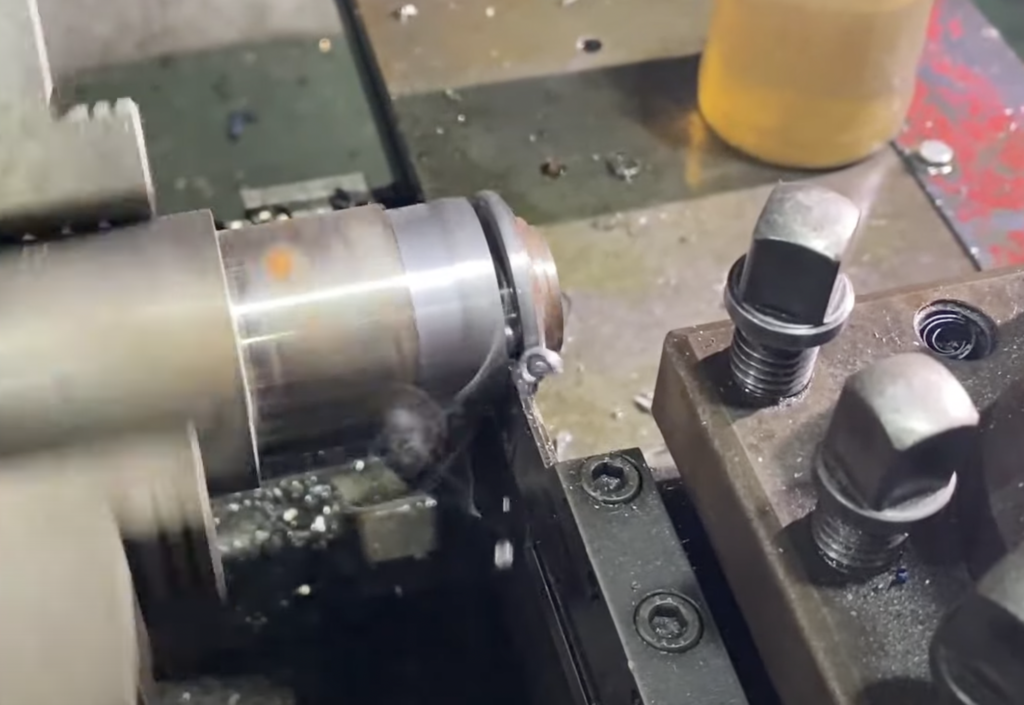
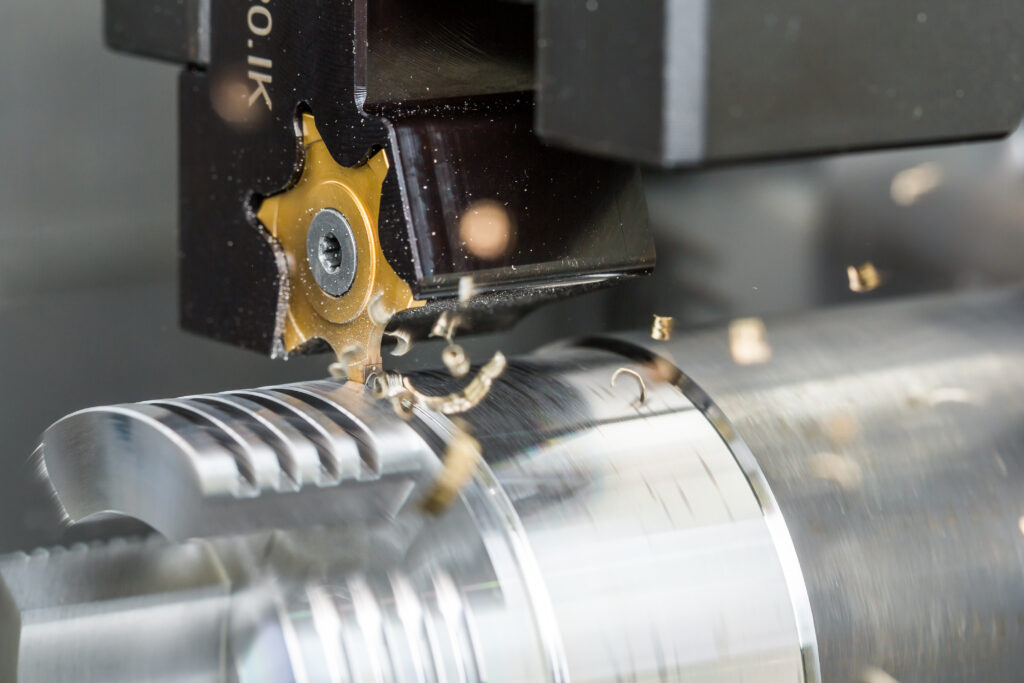
テーパー加工
テーパー加工は、刃物台を傾けることで行います。
テーパーの作業内容は、基本的にはまっすぐの内外径加工の延長です。
テーパー加工は、旋盤の刃物台を傾けて行います。
汎用旋盤のテーパー加工について、他ブログ様で大変分かりやすい画像を見つけましたので、お借りして掲載します。
下の画像のように、旋盤の刃物台は、刃物台を固定するボルトをゆるめることで、それ自体を傾けられるようになっています。
傾けたら片方で良いので刃物台のボルトを締めてクランプし、「刃物台ハンドルを使って」削ります。
そうすれば刃物台を傾けた分だけテーパーになって加工できます。
当然ですが縦送りハンドルを使うと刃物台ごと動いてしまいますのでテーパーにはなりません。注意しましょう。
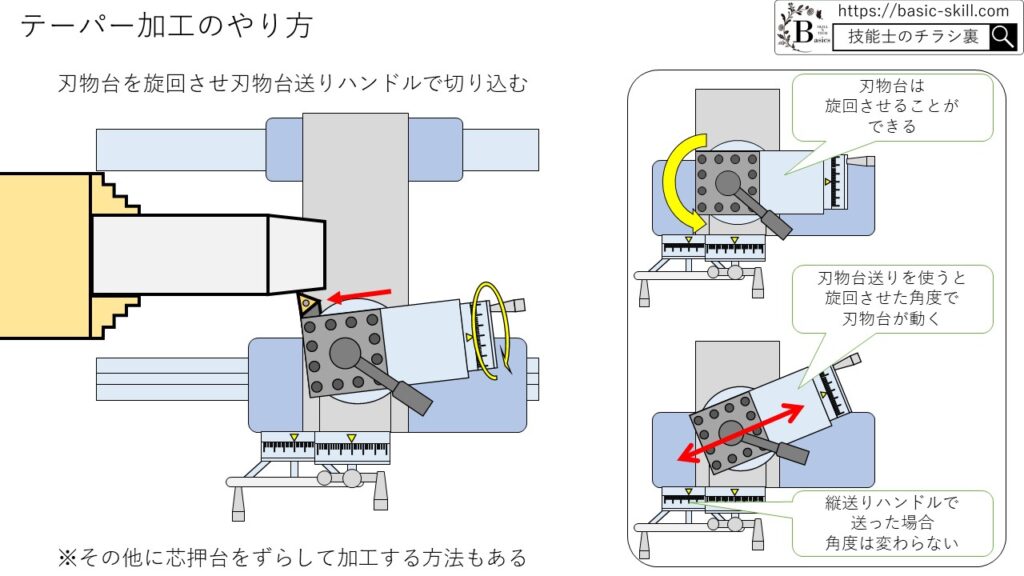
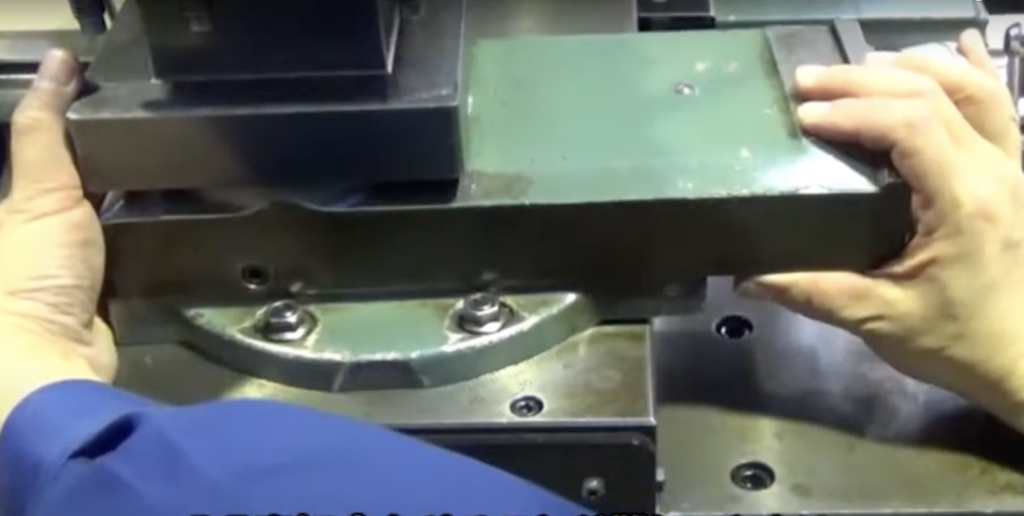
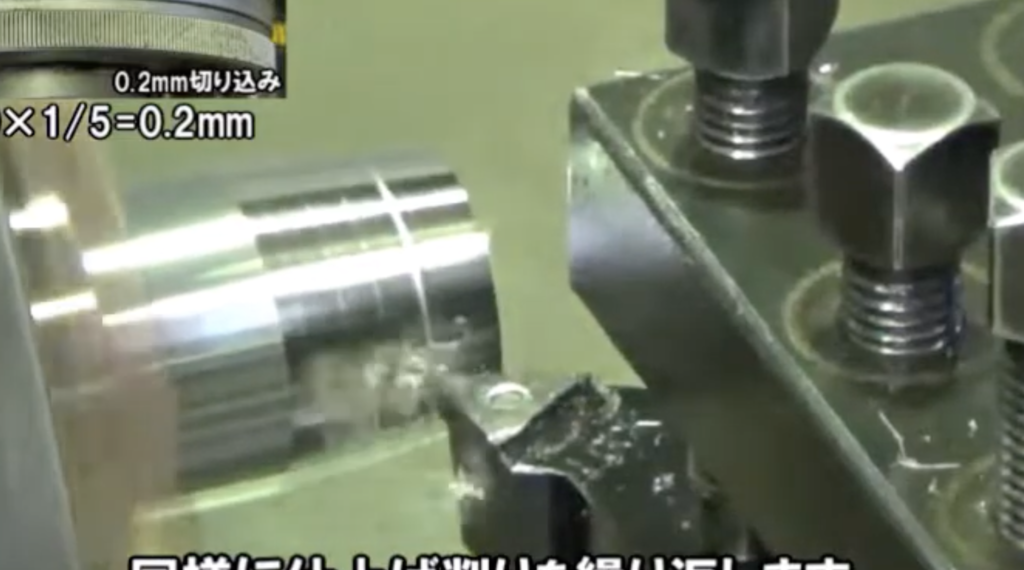
ねじ切り
最後にご紹介するのはねじ切り加工です。
経験が必要な、基本的な汎用旋盤加工の中でも最も難しい加工になります。
少々長くなりますので、ねじ切りは下に掲載した別記事で解説しています。
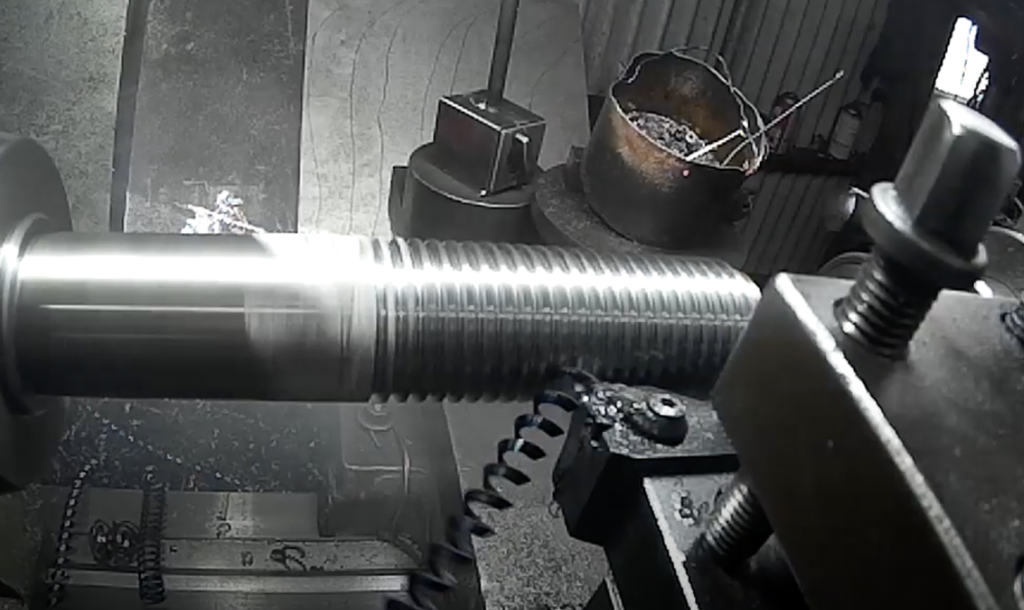
\なにわのスピードスター/
— 株式会社YSK@9月6日はスライドシャフトの日 (@ysk_info) June 17, 2020
汎用旋盤でねじ切りをしています!
弊社の加工者にはNC旋盤より速く(弊社調べ)ねじ切りができると言われている職人がいます!
職人が加工している姿はやはりかっこいいですね! pic.twitter.com/NUUdJkMMFm
他にも様々な加工ができる!
いかがでしたでしょうか?
本記事では、旋盤の使い方を、外径・内径・穴あけ・溝入れ・テーパー・ねじ切りの項目に分けて解説しました。
ローレット、タッピング、ダイス、フライス加工など、応用的な加工も含めるとまだまだ汎用旋盤には可能な加工が多いです。
こういった基本的な加工に慣れてきたら、ぜひそういった特殊な加工にも触れてみてください。
コメント