
旋盤での内径加工(ボーリング、穴ぐり、中ぐり)は、旋盤加工の中でも特に奥が深い加工です。
逃げ、びびりに影響され、図面をぱっと見た印象では簡単そうなものでも加工してみると上手く行かない場合も多いです。
本記事では、現役旋盤工である私が内径加工の方法とポイントについて詳しく解説しました!
内径加工ってどんな加工?
内径加工とは、穴をくり広げる加工です。穴ぐり・中ぐりとも呼ばれます。
まずはドリルでワークに穴を開けたり、パイプ材を用意することで、材料に穴が空いた状態にします。
そしてその穴を指定された寸法までくり広げるのが基本です。
旋盤では高精度な内径加工が可能なため、熟練者は0.001mm単位での寸法調整が可能になります。
どんな工具を使う?
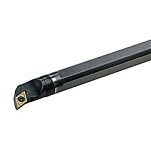
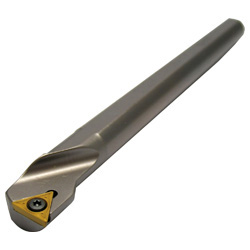
内径加工に使うのは内径バイトと呼ばれる工具です。ボーリングバーとも呼ばれます。
内径バイトの形状は様々
その形状には様々なものがあり、荒加工用の形状、仕上げ加工用の形状があります。
また、バイトの形状には荒加工と仕上げ加工を兼用できるものも多いです。
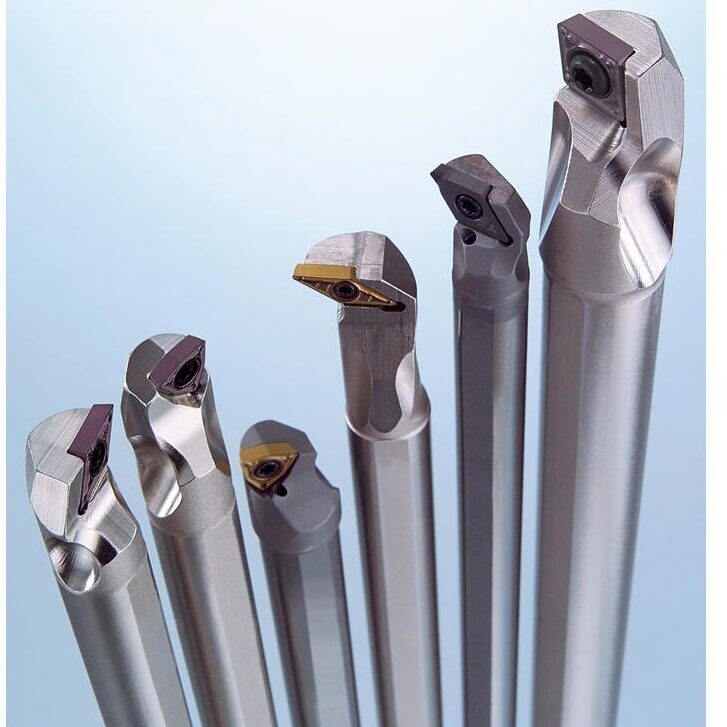
手研ぎのバイトも利用可能
特に汎用旋盤においては、内径加工に手研ぎのバイトを使うこともあります。
汎用旋盤ではアールの加工など複雑な形状は難しいため、基本的に総形バイトと呼ばれる、刃物の形をワークに転写して加工する刃物を製作して加工します。
そのような場合に手研ぎのバイトは大変活躍します。
他にも深くて細い内径溝入れや、内径の段を加工する際など、そのためだけに高価な既製品を購入してはいられないような加工にも手研ぎのバイトを使います。
基本的な穴ぐり加工はやはり時間単位のコスト面からスローアウェイの内径バイトが選択されることがほとんどです。
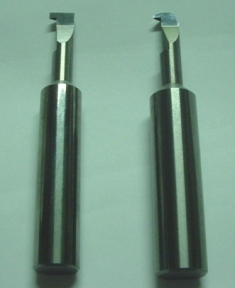
チップは荒加工用と仕上げ加工用に別れている
例えば三菱マテリアルのディンプルバーのような内径バイトは、荒(中荒程度までが限界)と仕上げ、両方のチップを装着することができます。
主に荒加工に使うのは欠けに比較的強い超硬のもので、例えば下画像の黄色いチップのような見た目のものです。
そして仕上げ加工用には、欠損しやすい分光沢が出やすいサーメットのチップを使います。
下画像のグレー(本来は光沢のあるシルバー)のような見た目です。
(画像はボーリングバーにはあまり使わない形状のものですが、材質のイメージのために掲載しています。)
現在は京セラのPV720というコーテッドサーメットを使っています。こちらのほうが少々の断続にも耐え、刃物の持ちも良いです。
これらの材質のチップを使い分けて加工を行います。
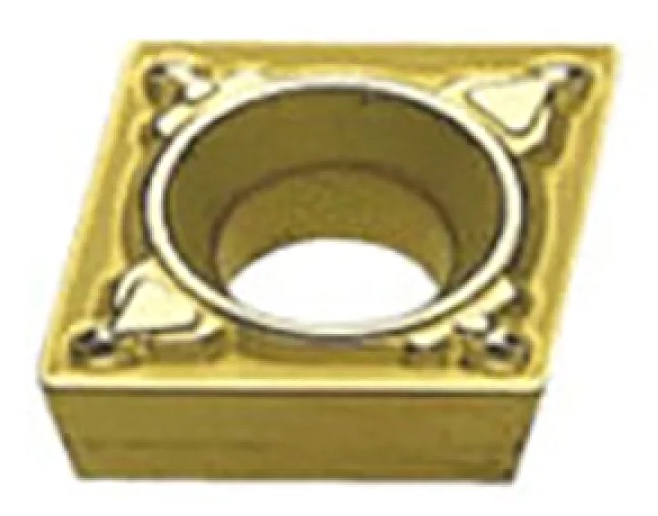
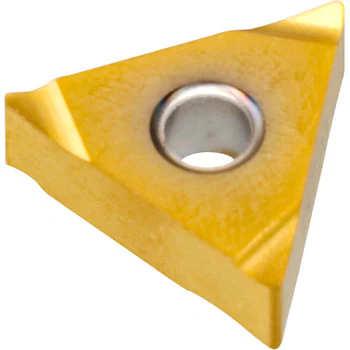
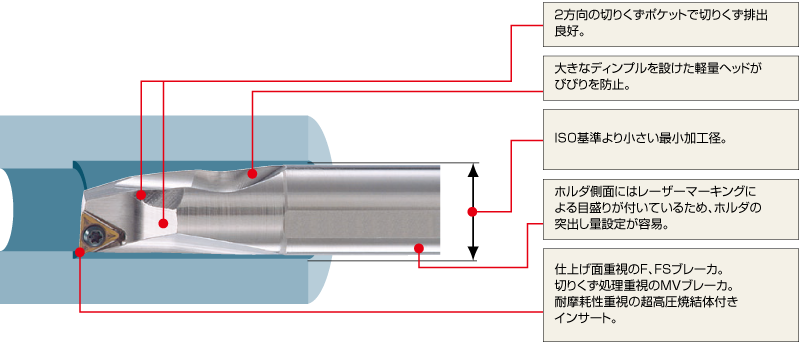
内径バイトのシャンク材質も様々
内径バイトのシャンクの材質は、通常は鋼材ですが、硬ければ硬いほどびびりを抑えられる性質から、超硬の素材も使われます。
また、例えば京セラのエクセレントバーと呼ばれる商品のように、価格は超硬より抑えながら、鋼材よりびびりにくい材質のシャンクを使ったものもあります。超硬と鋼材の中間のものといえますね。
内径バイトってどれを揃えればいいの?
内径加工用のバイトは、なるべく深い形状に対応するために様々な径のものを用意しておいたほうが良いです。
また、荒加工用のものと仕上げ用のものは両方あったほうが良いでしょう。
そうなってくると揃えなければならないバイトの数はそこそこのものになってしまうため、どれを買い揃えればよいか悩むところかと思います。
私が勤務先で使っている内径バイトを例に、どういった内径バイトを揃えておくのが良いかこちらの記事で解説していますので、是非参考にしてください!
加工のポイント
ここからは、内径バイト(ボーリングバー)を使って内径加工を行う際のポイントを解説していきます!
基本的に、内径加工は「びびり」と「逃げ」の2点との戦いになります。
突き出し長さはこのくらいにしておく!
内径加工において、びびりを制御することは大変重要なことです。
びびりが発生してしまうとワークに振動の模様ができてしまい、必要な表面粗さ(面粗度)を達成できないだけでなく、寸法が狂ったり外観を損なったりしてしまいます。
びびりについてはこちらの記事で詳しく解説しています。
上記の記事内でも解説しているように、突き出し長さはびびりの三要素の一つで、内径加工のびびり対策を行う上ではかなり大きなウエイトを占める要素です。
具体的には、内径バイトの突き出し長さを3L/D程度にしておくのが良いです。
(L/Dとは、シャンクの直径に対してどれくらい突き出すかということで、例えばφ16のシャンクでしたら48まで突き出したら3L/D、64まで突き出したら4L/Dということになります。)
これは鋼材の場合で、SUS304などの難削材を削る場合はさらに2.5L/Dなど、さらに短く設定してやっと理想的な切削ができます。
これも使用しているバイト等によるところがあり、一概には言えませんので、目安として考えて設定してみると良いかと思います。
内径加工の切削速度はこのくらい!
内径加工の切削速度は、びびりに大きく関係してきます。
前項で掲載した記事内でも解説していますが、びびりの3要素の一つである切削抵抗に大きな影響を及ぼすからです。
基本的に切削速度を上げたほうが切削点の温度が上がり、構成刃先が起こりにくいため寸法や表面品質が安定します。
ですが、びびりやすい加工の場合は切削速度を落とすことで切削抵抗を下げ、びびりを抑える必要があります。
構成刃先についてはこちらの記事で解説しています!
具体的にはこちらの条件を使っています。
特にびびりやすい状況では、場合に応じて臨機応変に切削速度を変えています。
NC旋盤では周速制御をOFFにして一定回転で加工することも多いです。
荒加工ではびびってしまっても特に加工に支障はないため、びびるのを気にせずに切削条件を上げ、サイクルタイムを短くすることも多いです。
ゴムバンドを巻くことでビビり防止に
ワークの突き出し長さが原因でびびりが発生する場合、トラックのシートを止めるようなゴムバンドをワークに巻いてみてください。ワークの剛性が上がり、びびりを抑えることができます。
固定振れ止めも選択肢に。
固定ブリョ(振れ止め)を使えば、長物のワークでもびびらせずに 内径加工を行うことができます。
固定振れ止めについてはこちらの記事でまとめていますので、ご参考にどうぞ!
内径加工のよくある問題点とその対策
内径加工を行う中で、特に起こりやすい問題が「びびり」「逃げ」「摩耗」の三点です。
びびりについては前項で詳しく解説しているため、逃げと摩耗について重点的に説明しますね。
内径バイトの逃げが発生する
内径バイトは加工時の抵抗により、わずかに曲がった状態で加工が行われています。
それによって、加工後の仕上がり寸法が狙った寸法よりも小さめになってしまうんです。
バイトには、切削抵抗によってワークから逃げる方向に力がかかるからですね。
内径バイトの突き出しが2.5L/Dなどの短い状態だと逃げは無いに等しいくらいですが、4L/D以上くらいの長さになるとバイトの逃げを実感できるようになります。
逃げると寸法公差に入れる難易度が大きく上がる
バイトに逃げが発生すると、寸法が狙い通りになりません。
そのため寸法公差に入れる難易度が大きく上がります。
よくある公差であるH7のレベルでしたら、経験を積まないと安定して精度を出せないでしょう。
逃げはコントロールが難しいです。
中仕上げで測定を正確に行ったはずなのに仕上げを行うと削り残してしまい、もう一度公差内を狙って仕上げると削りすぎて修正不可能になってしまう・・・。というのは初心者あるあるです。
次項で逃げに対する対策をご紹介しましたので、是非参考にしてください!
逃げの解消方法
突き出し長さを短くする・バイトを太くする
逃げの解消に最も効果的なのが、バイトの突き出し長さを短くすることです。
突き出し長さといっても、シャンク径に対する比率(L/D)で短くなればOKです。
そのため、突き出し長さは同じでバイト径だけ太くするのも効果的です。
びびりを抑える方法と共通ですね。
同様に、シャンクを超硬に変えることも効果的です。
切込量を減らす
バイトの逃げは、切削抵抗によって起こります。
つまり、切削時の抵抗が少なくなるように、削る量(切込量)を減らすのが効果的です。
具体的には「ゼロカット」と呼ばれる、同じ寸法で2回仕上げ削りをする操作を行いましょう。
そうすることで、1回目の加工でバイトが逃げてわずかに削り残してしまった箇所を、2回めの加工でほぼ寸法通りに仕上げることができます。
内径の精度を出したい場合これを応用し、
中仕上げで2回加工→測定→仕上げで2回加工
の順序で加工を行うと狙った寸法に入りやすいです。
ただ、この方法には弱点があります。それは削る長さが長い場合は使いにくいという点です。
その理由は、刃物が大きく摩耗するからです。
ゼロカットは、刃先がワーク表面に食いつかず、こする現象が起こりやすいです。
これが起こると刃先がみるみる摩耗していきます。こすれ摩耗という名前があるほどです。
そのため削る長さが短い場合や、品数が少ない場合にのみ有効な方法と言えます。
削りしろを一定にする
逃げが発生する条件下で精度を出したい場合、中仕上げ・仕上げで切込量を一定にすることで狙った寸法通りの加工が成功しやすいです。
荒加工の段階でしっかりと寸法を測っておき、仕上がり寸法とのぴったり真ん中の寸法を狙って仕上げを行いましょう。
例えばφ20.01を狙っており、荒加工後の寸法がφ19.75だったとすると、中仕上げではφ19.88を狙います。
全く同じ切込量であれば逃げの量も同じなので、寸法が狂うのを防ぐことができます。
こすれ摩耗によってテーパーに削れてしまう
逃げ、びびりの他に問題になるのが摩耗です。
例えばφ20.01の寸法を狙っていた場合、φ19.99に仕上がってしまったとしましょう。
この状態で0.02mm切り込んで加工を行うと、削る長さが短い場合はうまくいきますが、ある程度長い場合はこすれ摩耗によってテーパーになってしまいます。
こすれ摩耗は、先述の通り刃先がワーク表面に食いつかず、こすれることによって生じる摩耗です。
これが起こると刃先がみるみる摩耗していきます。
そのためこのようなわずかに切り込んで削る方法やゼロカットは、削る長さが短い場合や、品数が少ない場合にしか使えません。
これを防ぐために、基本的には径で0.1mmほど仕上げしろを残した上で仕上げ加工を行うようにしましょう。
それができない場合は、NC旋盤であればプログラムでわずかなテーパーにすることで摩耗を相殺する方法がありますが、安定する方法ではないため数が少ない場合にのみ有効です。
極小系の内径加工
φ6未満のような極小系の内径加工には、耳かき形状のステッキ型工具を使用しましょう。
以下の記事でHORN工具を中心に解説していますので、興味がある方はご覧ください。
最小加工径φ0.2の超極小ボーリングバイトなど、小径の内径加工や溝入れ加工等について解説しています!
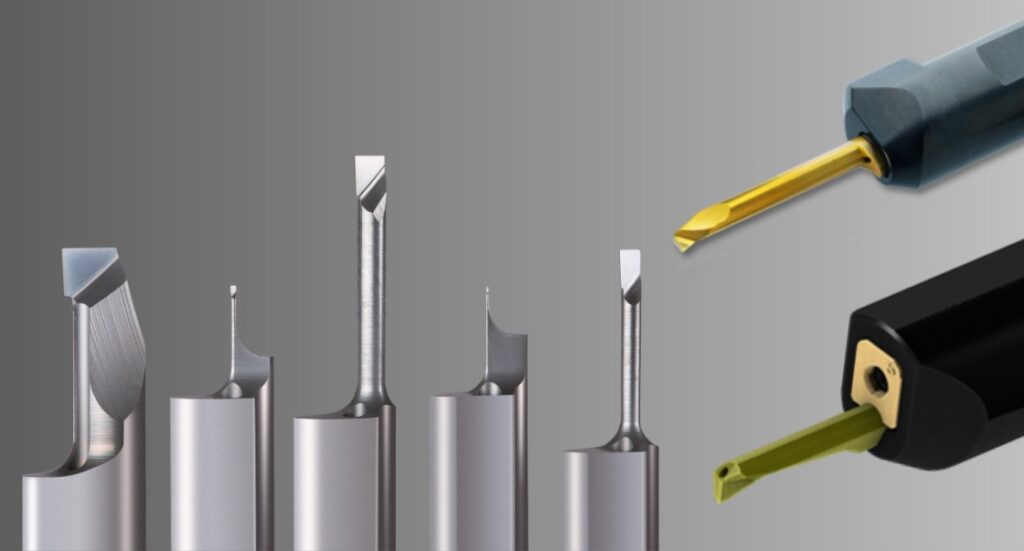
逃げ・びびり・摩耗の悪条件下ではボーリングにこだわらない
内径加工で突き出し長さがあまりに長くなる悪条件下では、どうしようもなく逃げやびびりが発生してしまうことがあります。
そういった場合は無理にボーリングに拘る必要はありません。
リーマやスパロール、ワイヤーカットといった方法での加工を試したほうが安定する場合が多いです。
スパロールは馴染みが無い方も多いかと思いますが、下画像のような工具で仕上げ面を押しつぶして加工する方法です。
0.01~0.02mmくらい仕上げしろをつけておいて加工を行います。
別途工具が必要なのがデメリットですね。
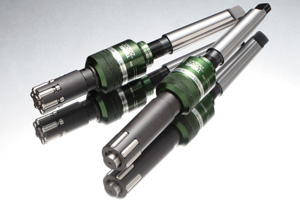
経験を積むほどに上達するのが内径加工
内径加工は加工者の経験がものをいう加工の一つです。
どの程度の条件下ならびびるのか・逃げるのか把握すること、そして逃げが発生する条件下での寸法精度の出し方などは一朝一夕で身につくものではありません。
ですが、失敗があったときにきちんと理由を理解できていれば次に加工する際に経験を活かすことができるので、上達が感じられる加工でもあります。
本記事を、技術を高めるきっかけにとして参考にしていただければ幸いです。
コメント