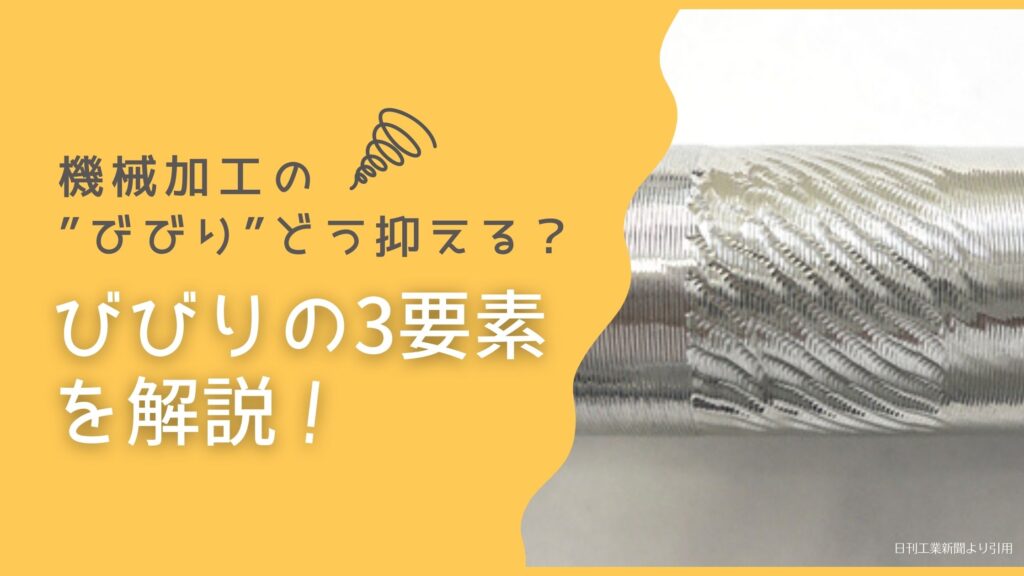
機械加工を行うにおいて、びびりはときにかなり厄介ですよね。
本記事では旋盤工の私の立場からびびりを抑える方法を、経験と理論両面から解説していきます。
旋盤目線の記事にはなってしまいますが、内径バイトをエンドミル等に読み替えていただければフライス加工にも応用できる話かと思います。
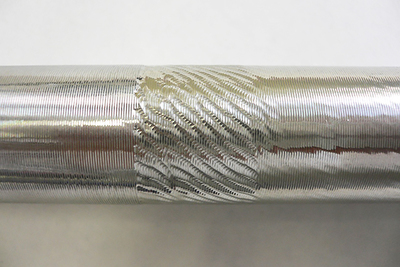
びびりとは小さいたわみの連続
旋盤やフライス加工を行っているいる人であれば、誰もが経験することになるびびり。
びびりとは刃物もしくはワークが振動してしまう現象ということはなんとなく分かると思います。
そしてその振動は、非常に小さいたわみの連続によって起こるものです。
つまり、たわみを制御できればびびりも減るということです。
びびりの原因には3つの要素が存在する
ここで計算式を一つ紹介します。
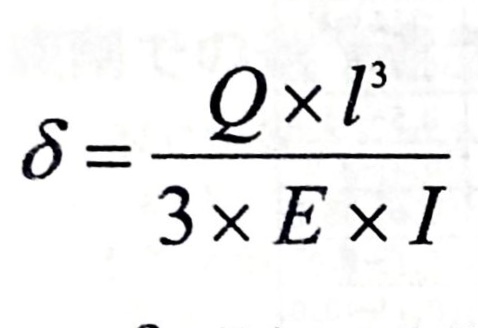
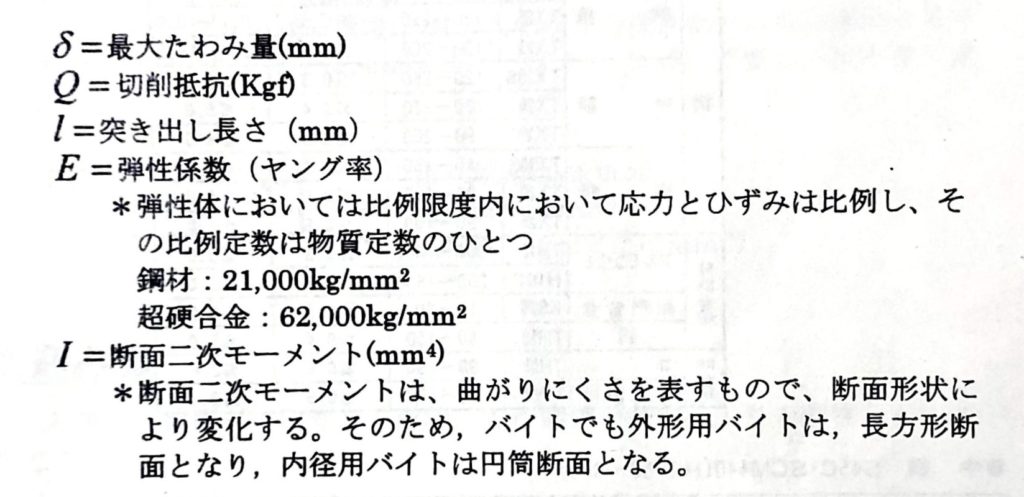
こちらはたわみの計算式です。
すこしわかりにくいので、わかりやすく書き直したのがこちら
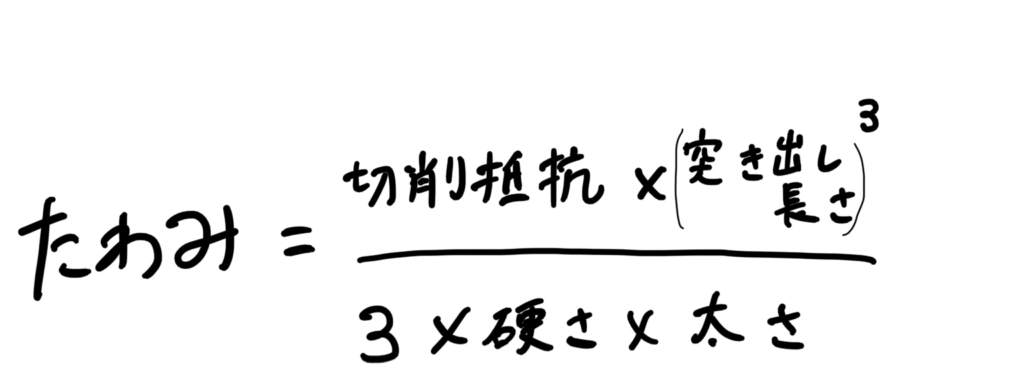
字が下手でごめんなさい^^;
厳密には違いますが、公式を日本語に直すとこのようなイメージです。
もちろん実際に加工する際にこの公式を使ってびびり量を計算することはありません。
ですが、この式からびびりの原因には大きく分けて3つの要素があることがわかります。
突き出し長さと工具・ワーク太さ
その要素の1つ目が突き出し長さと工具・ワーク太さです。
びびりの原因として一番初めに思いつく要素がこれですね。
要するに、何D(直径)突き出しているかということです。
工具やワークの突き出しが長ければ長いほどびびりやすくなります。
突き出し長さ・太さはびびりに大きく影響する
前項の計算式を見て分かるように、突き出し長さの3乗がたわみ量に比例します。
このことからも、突き出し長さがいかにびびりに大きい影響を与えるかがわかりますね。
ちなみにワーク・工具の太さに関しても、詳細は省きますが、工具の太さ(厳密には曲がりにくさ)を表す弾性二次モーメントという数値が工具・ワーク半径の4乗に比例しており、太さも同様にびびりに大きな影響を与えることがわかります。
実際に加工で突き出し長さを考えるときは、太さと突き出し長さを別々に考えるのではなく、まとめて何D突き出すかで考えていきます。
ワークを3D以上突き出す場合芯押しを行う
ここからは具体的な加工の話に入っていきます。
まずはワークのびびりについての対策。 長いシャフトの外径を加工するような場合のびびり対策についてです。
私が細長いワークを加工する際、3D以上の突き出し長さがあれば芯押しを行うようにしています。
例えば仕上がり径がφ20であれば突き出し60以上、φ30であれば90以上で芯押し、といった具合です。
芯押しを行っても突き出しが長すぎると真ん中の方でびびりが発生してくるので、その際はセンタ穴を広げたり、芯押しセンタを太いものに交換したり、後述する切削条件や工具を変えたりして対応しています。
ちなみに芯押しセンタは先端交換式のものを使うと素早くセンタ太さを変えられるのでとても便利です。
NC旋盤で先端交換式を使っていない人はこちらの記事を読んでみてください。
【非推奨】汎用旋盤ではワークを手で抑える方法も
これから紹介する方法は危険な方法で、万一軍手を使って行ってしまうと死の危険さえ伴いますので推奨はしません。
そのためどうしても行う場合も必ず素手で行わなければなりません。
その方法とは、シャフトを削っている際にびびり止めのためにワークを素手で抑えながら加工する方法です。
こうすることで、ワークの突き出し長さを実質短くしている状態になり、びびり止めになります。
当然ですが手が熱くなるのでそこまで回転数は上げられません。
私もたまに使う方法ですので、推奨はしませんが一応紹介しておきました。
安全第一ですので、このような方法は使わずに作業を行うのが王道です。
段取りの手間はありますが、移動振れ止めを使うのが大変効果的なびびり止めになります。
内径バイト(仕上げ)の突き出し長さは基本は3Dほど
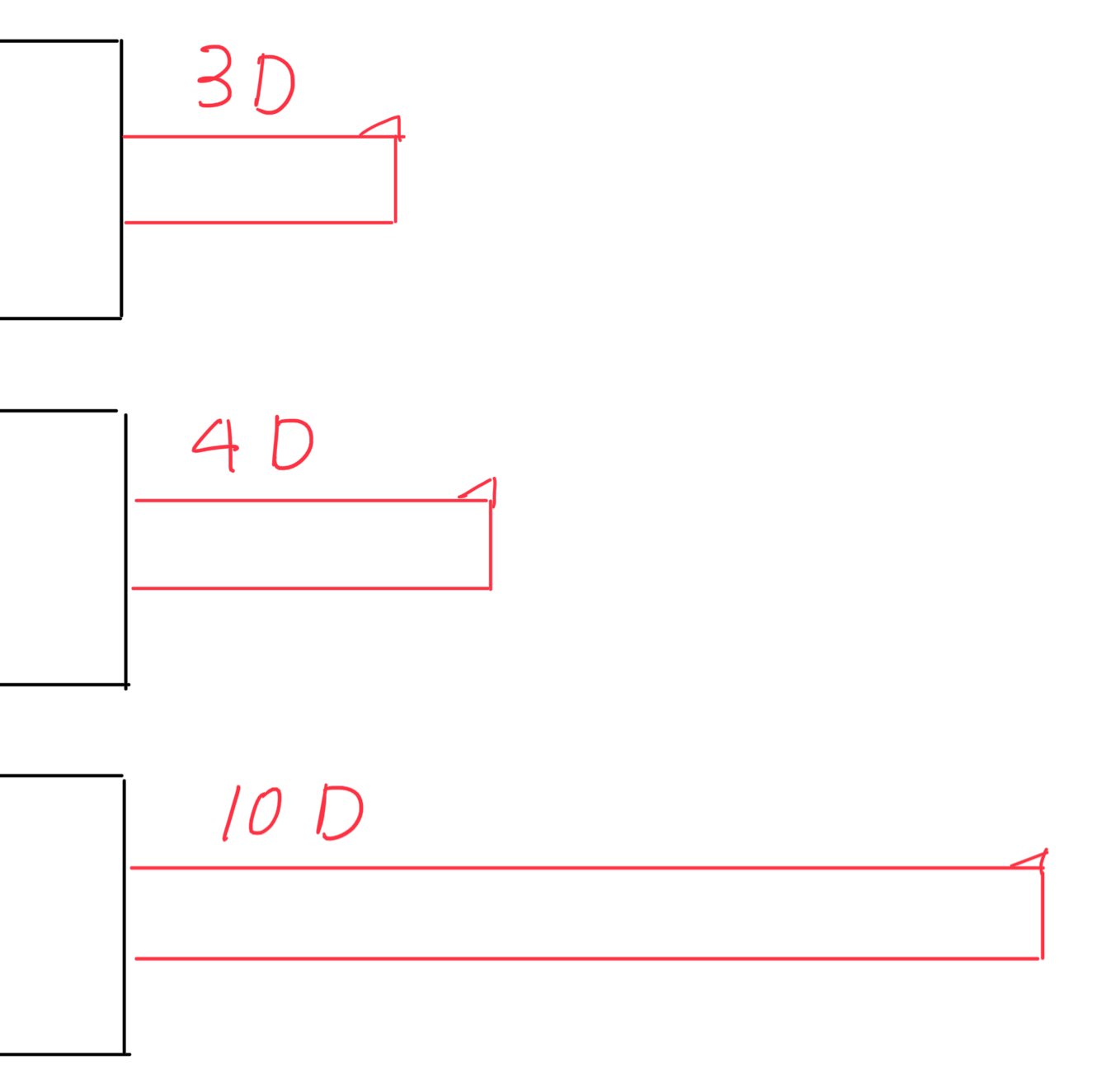
次は、内径バイトがびびってしまう場合の対策です。
仕上げ用の内径バイトは、私の場合基本は3Dの突き出し長さ(図の一番上)で取り付けています。
びびりやすい材料を加工する際や、より長い突き出し長さが必要な場合は後述するようにノーズRを小さくしたり、条件を下げる、超硬バイトを使うなどして対応しています。
防振効果のあるマグネシウムスリーブを使ってみるのも一つの手です。これ、かなり防振効果があります。
ですがマグネシウムスリーブはクーラントによって腐食しやすいので、使用は最低限にし、使用後はクーラントをすぐに拭き取るようにしましょう。
ときには図の一番下のように無理やり10D程度の突き出し長さで加工することもあります。
荒加工用の内径バイトの場合はびびってもきれいに仕上げれば製品に影響は出ないため、5Dなど長めに突き出して加工することも多いです。 長めに突き出す必要がなければ大体4Dほど突き出して加工しています。
内径加工については下の記事でも解説していますので、気になる方はぜひご覧ください!
切削抵抗
2つ目の要素は切削抵抗です。
計算式にも出てきましたよね。
切削抵抗というと馴染みが無いかもしれませんが、要するに回転数やワークの硬さ、刃物の抵抗の大きさのことです。
では切削抵抗を決める要素を一つずつ見ていきます。
回転数
当然ですが、加工の回転数が高ければ高いほど刃先にかかる抵抗は大きくなります。
そのことからも、びびりを減らすために回転数を落とすということが理にかなっていることがわかりますね。
ワークの硬さ
こちらも当然のことですが、柔らかい材料より硬い材料を削っているときの方が切削抵抗は大きくなります。
たとえばSUS304で加工を行っている場合、可能であればSUS303を使ってみるといった方法で多少びびりも軽減されるでしょう。
刃物の抵抗
次は刃物の抵抗。旋削の場合、ノーズRやブレーカー形状(刃物の切れ味)がこれにあたります。
ノーズRの小さいチップを使う
この方法でびびりを抑えるために最も簡単なのは、ノーズRが小さいチップを使うことです。
例えばノーズR0.4のチップで仕上げている場合はノーズR0.2のチップを使ってみてください。
研いでノーズRを小さくする方法もある
手研ぎバイトを使っている場合は、ノーズRはグラインダーで簡単に小さくできますよね。
それと同じ要領で、スローアウェイチップもグラインダーで研いでノーズRを小さくし、びびりを低減することができます。


画像はノーズR0.4のチップをグラインダーで削り、ノーズRを小さくしている様子です。
このようにして削れば切削抵抗が下がるため、びびりを減らすことができます。
刃物の切れ味にも注意
刃物の切れ味も切削抵抗に関わります。
びびりに困っている場合、より刃先形状の切れ味がよい刃物を選択すると改善するかもしれません。
また、同様に刃物が傷んできている場合は切削抵抗が大きくなってしまっているので、チップを交換する、もしくは研ぎ直すことでびびりが改善されます。
工具の硬さ
最後に工具の硬さ。弾性係数です。
例えば旋盤の内径バイト場合、通常の工具鋼のバイトよりも超硬バイトのほうが弾性係数が高く、びびりにくくなります。
超鋼バイトは通常の炭素鋼の約三倍の弾性係数を持っています。
多くのメーカーが超硬バイトを取り扱っているため、ある程度は揃えておくと便利です。
私の勤務先では、シャンク径φ4,5,6,8,10,12,16の超硬内径バイトを揃えています。
超硬バイトは高価ですが、仕上げでは使う機会もかなり多く効率よく加工する助けになりますよ。
また、メーカーによっては超硬と通常の工具鋼を混ぜた、比較的安価でありながらびびりにくいバイトもあります。
例えば京セラのエクセレントなんかがそうです。
私が使っている内径バイトについてはこちらを参照いただければと思います。
追記:超硬でありながら価格が抑えられているインプラス社のボーリングバーが、どなたにでも大変おすすめです!こちらに公式HPへのリンクを貼っておきますので、ぜひご活用ください。
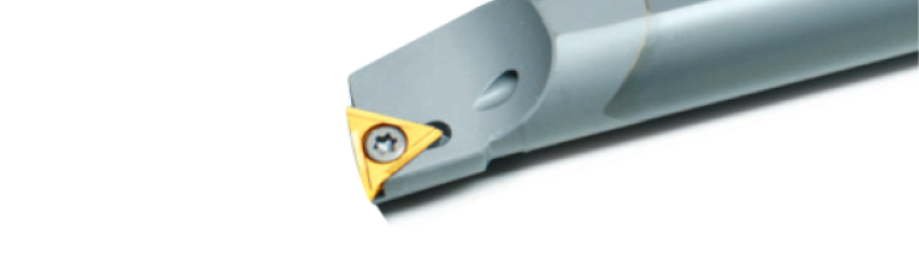
びびりは単純計算では制御できない
以上、びびりの基本的な3要素を解説しました。
ただ、必ずしもこの基本通りにびびりを抑えられるかというとそうではありません。
送りを上げたり、芯高を上げたりすることでびびりが収まることもありますし、稀に回転数を上げたほうがびびりを抑制できることさえあります。
私もびびりやすいワークを加工するときは、常に経験と勘で手探りで条件を探しなから加工を行っています。
ちなみに今はこういったびびりさえコンピュータで制御できる機械もあります。
例えばオークマの加工ナビに、びびりが起きないような回転数に自動調節してくれる機能があります。主軸に振動を感知するセンサーが埋め込まれており、その情報をもとに回転数を調節するそうです。
とはいえ町工場などの現場ではそういった高価な機能が搭載されている機械は少なく、加工現場では職人としての経験と勘が頼りです。
それは蓄積していかなければ身につかないことですが、今回紹介した3要素が基本となる最も大きい要素であることには間違いありません。
今回紹介した知識があなたのお役に立てば嬉しいです!
コメント