振動切削を使った旋盤加工の様子
A5052やA5056などのねばっこいアルミや銅なんかは旋盤加工を行う上で本当に厄介です。
荒加工では切り屑が絡まってワークがボロボロになってしまいますし、仕上げ加工ではワーク表面がむしれたり切粉の傷が入ったりして、せっかく公差に入れた部分が台無しになってしまいます。
そんな厄介なワークを加工するために、私達加工技術者は下の記事のように日々知恵や経験を総動員して加工しているわけですが・・・
最近は冒頭の動画のように振動切削という加工方法が実用化されています。
工具に微細な振動を加えながら削ることで切粉を切断しながら加工できるんです!
機械にこんな機能がついていれば、粘っこい材質の加工は随分楽になりますね。
表面粗さもほぼ理論値通りに出る
振動切削と聞いて、はじめに気になるのは振動させた分表面粗さが悪くならないかというところですよね。
結論から言うと、表面粗さの数値にはほぼ影響なく加工することができます。
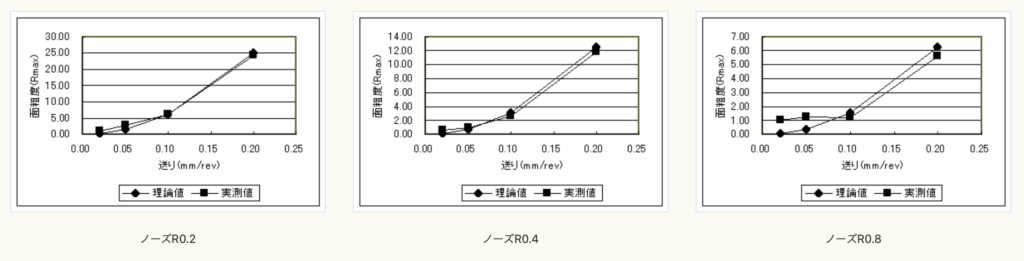
図のように、ノーズR0.2、R0.4、R0.8のいずれにおいても面粗度の実測値が理論値とほぼ同じ値を示しているのがわかります。
なんで振動しているのに表面粗さにほぼ影響がないの?
このように表面粗さにほぼ影響しない理由がひと目でわかるのが下の画像です
この画像は振動切削でS45Cを削った表面を拡大したものです。
旋盤で右から左に削っていったと思ってください。
まっすぐな縦線が刃物の送りによってできた線で、少し波打っている横線が振動によってできた線です。
ひと目見て分かるように、振動でできた横線は、送りでできた縦線より明らかに浅いですよね。
これほど微細な振動なので、表面粗さにはほぼ影響がないんです。
振動切削には他にもこんなメリットが
・切削抵抗が減少する。
・加工温度が上がらないため、熱による歪みが生じない。
・構成刃先が付着し難い。
・工具寿命が延びる。
これらのメリットが得られる理由は一つ
これらのメリットは、振動切削のある一つの性質によって得られるものです。
その性質とは、振動切削は連続的な切削を断続的な衝突に変える加工方法だということです。
例えば板に釘を打ち込むとき、同じ総量の力でも、釘の頭を1秒かけて押し込むより、ハンマーで一瞬だけ力を加えた方が楽に打ち込めますよね。
それと同じ原理で、振動切削では切削抵抗が減少します。
切削抵抗が減少すると、加工温度が上がりにくくなるため、工具寿命も伸びます。
ですが瞬間的な切削速度は上がるため、構成刃先は付着しにくくなるといった仕組みです。
これだけのメリットがあるのであれば、もしかすると近い将来、振動切削機能付きの旋盤が当たり前になってくるかもしれませんね。
(出典:DMG森精機HP https://www.dmgmori.co.jp、多賀電気㈱HP http://www.tagaele.com)
コメント