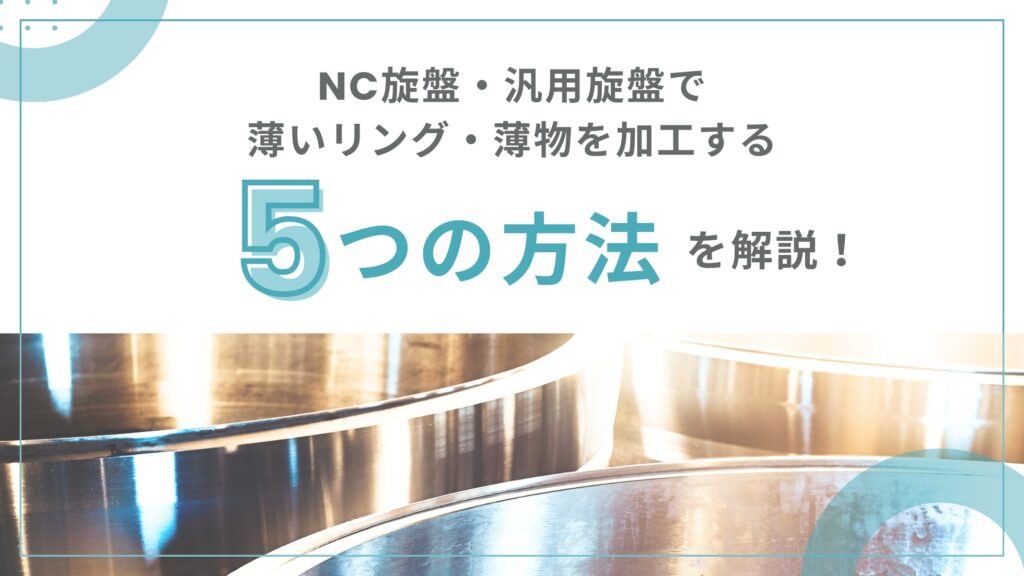
こんなものを加工したい時どうする?
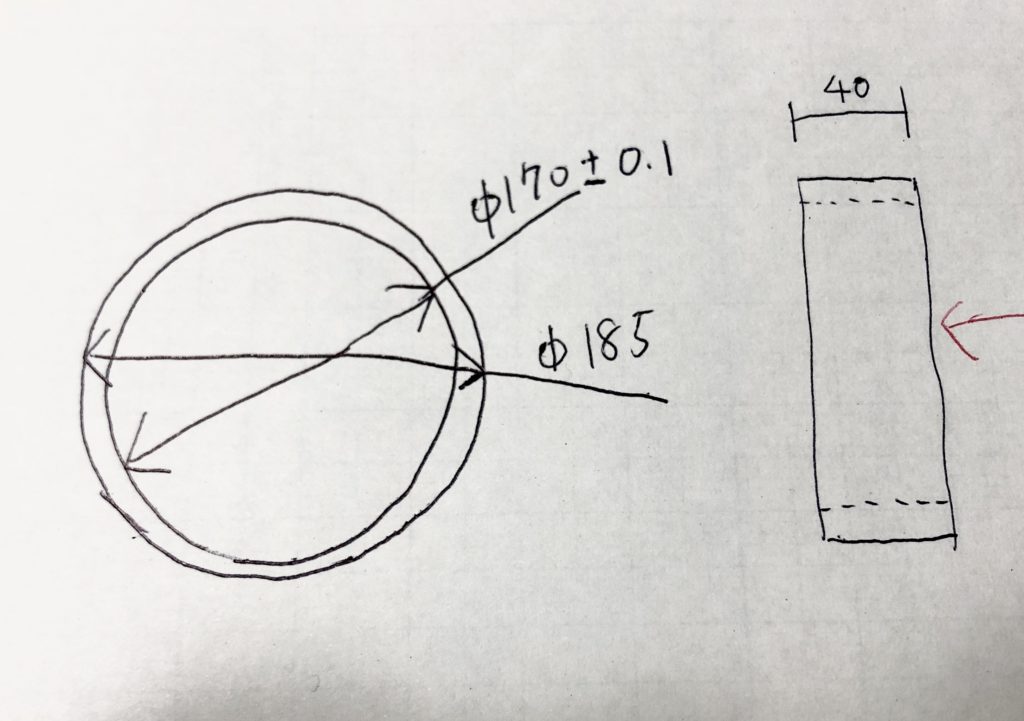
一見すると簡単そうな製品に見えますよね。
しかし、通常通り加工してしまうと、こんな形にひずんでしまいます
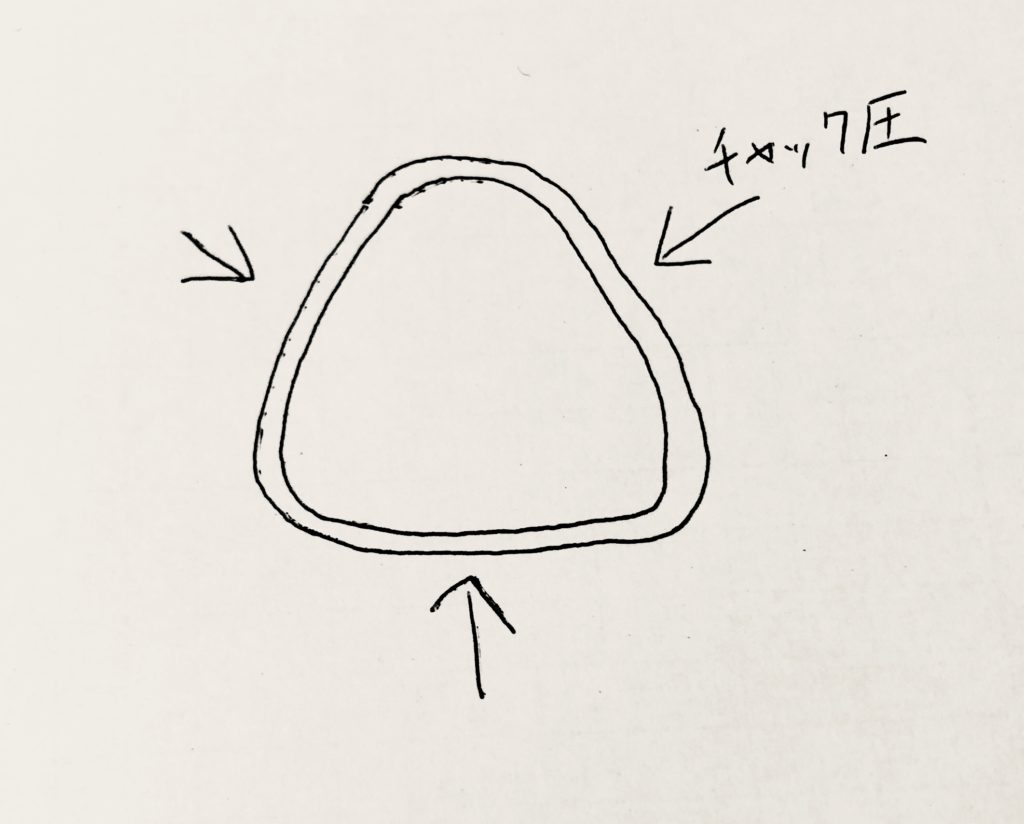
ならどうしたらいいか、これから紹介していきます
方法1.油圧を最小にして仕上げる
まずはNC旋盤の油圧パワーチャックを使うと仮定して解説します。
薄物のワークが変形してしまう理由の一つに、油圧によるものがあげられます。
チャックの3点からの圧力がかかった状態で加工するため、仕上げた直後は真円になっていたとしても、チャックから外すとその圧力がなくなるため三角に変形してしまうのです。
なので油圧を最小まで緩めて加工したいのですが、荒加工までも油圧最小でやってしまうと加工負荷によりワークがチャックから外れて飛んでいってしまいます。
そのため荒加工は通常の油圧で行い、仕上げ加工のみ油圧を最小にして行います。
ここで重要なのが、荒加工が終わってそのまま油圧を緩めて仕上げるだけだと不十分ということです。
油圧を緩めてた上でチャックを開け閉めして初めて荒加工のひずみとチャック圧の歪みが解放されます。
つまり加工は以下の流れで行います。
・通常通りの油圧で荒加工を行う
・油圧を最小にする
・チャックを開け閉めする
・仕上げ加工を行う
注意点として、油圧は必ず機械の指示する限界最小値を超えないようにしてください。
限界を超えて油圧を下げると、チャックのシリンダが焼きつく原因になります。
また、荒加工の後にひずんだ状態のワークを仕上げるため、仕上げ代は大きめにとるようにします。ワークにもよりますが目安は0.5mmです。
方法2.入れ子を使う
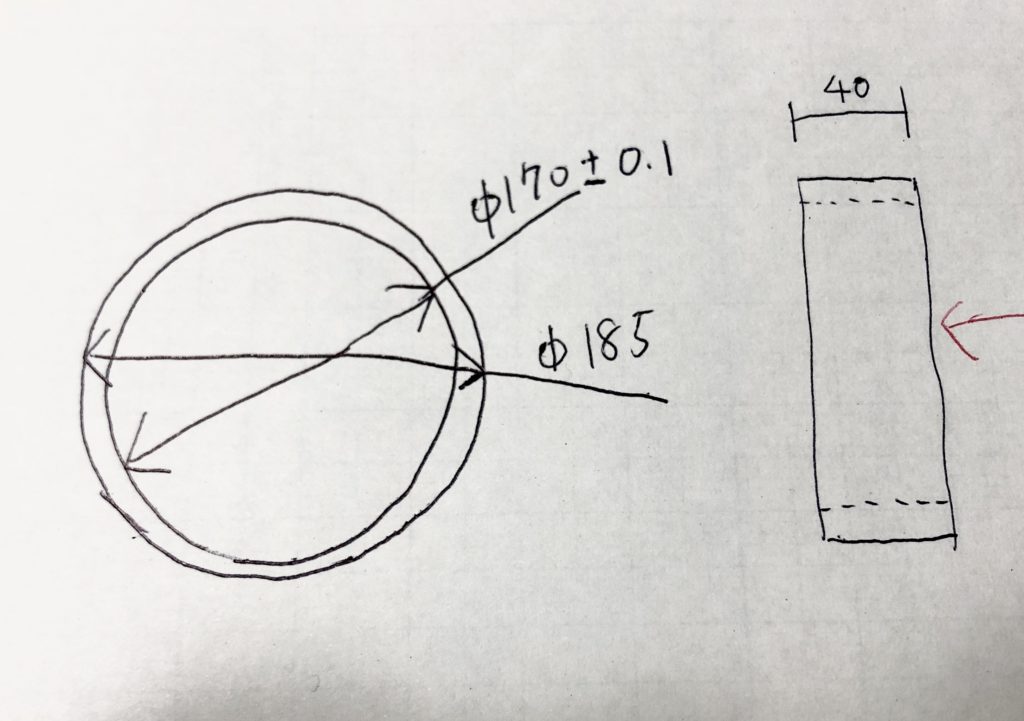
例えば全長(Z)方向に取り代をつけて黒皮からこの製品を加工する場合、右側は上で説明した【方法1】をを使えばきれいにできますね。
しかし、左側を加工するためにはワークをひっくり返し、仕上げた面をつかまなければなりません。
仕上げた薄い部分を掴んでしまうと、先ほど説明したようにチャック圧で歪が発生してしまいますよね。
そんなときは入れ子を入れてつかんでやります。
入れ子を入れていればチャック圧でひずむこともありません。
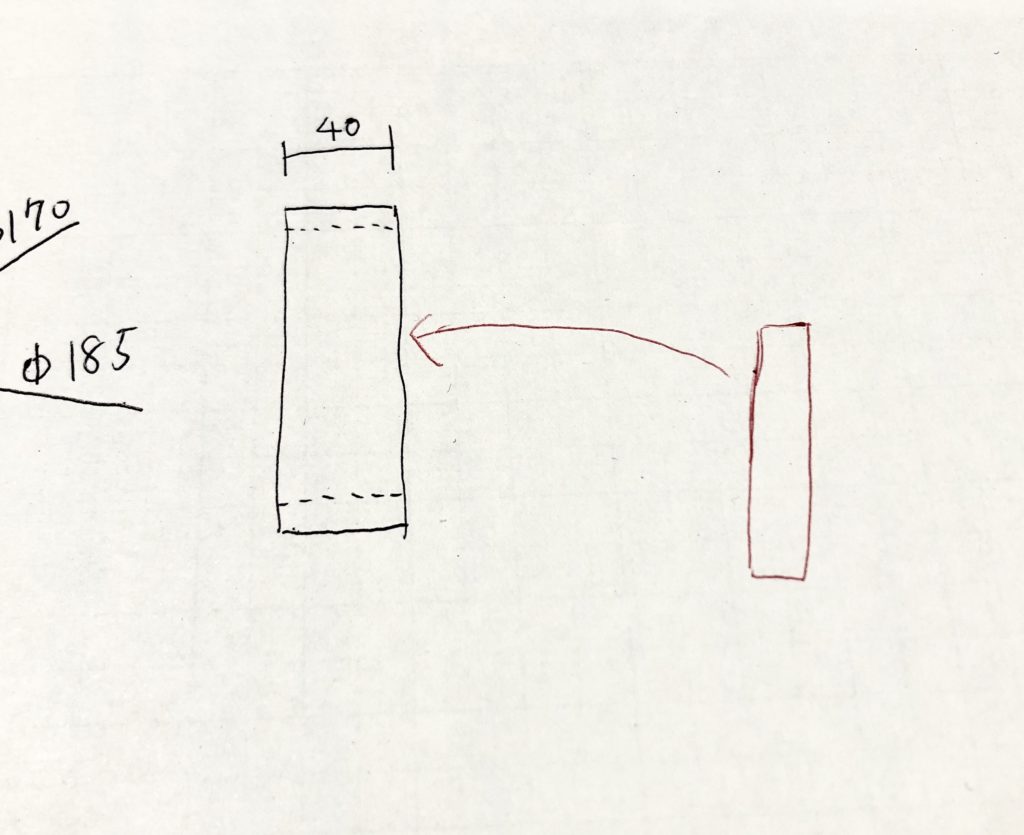
上の図で赤で書いたものが入れ子です。この丸を中に入れて掴んでやれば、チャック圧でひずむこともありません。
この加工方法を使う場合、加工時の製品の内径を正確に測定しておく必要があります。
公差が入っていれば公差のマイナスめいっぱいもしくはそれより-0.05mm以内の寸法で入れ子を作ってやれば問題ありません。
公差のマイナスいっぱいで入れ子を作れば栓ゲージとしても活用できます。
マイナスめで入れ子を作ると0.05mm分歪んでしまうのでは?と心配になるかもしれませんが、その程度であればチャックからはずすと金属の弾性によって元の寸法に戻ってくるので全く問題ありません。
公差が入っていなければ、径にもよりますが、内径のマイナス0.05mmの外径に入れ子を仕上げてやれば問題ないでしょう。
方法3.汎用旋盤(スクロールチャック)で仕上げる
方法1で表、方法2で裏を加工しても、裏を加工する際の加工ひずみにより変形してしまうことがあります。
こちらの記事でも少し解説していますが、残留応力によって削ると金属材料は曲がってしまいます。
そのような場合は、公差の入っている内径は仕上げしろを0.5mm残しておいて、内径以外は全て仕上げてしまいます。
そのあとで汎用旋盤のスクロールチャックでそ〜っと掴み、内径のみ仕上げてやれば加工のひずみがおきることもありません。
この工程では内径を削るため入れ子を入れることもできませんし、NC旋盤の油圧チャックだと限界まで圧を下げてもひずみが生じてしまいます。
そこで汎用旋盤の手締めスクロールチャックを使い、最小限の圧力のみかけて内径を仕上げてやることで内径をひずませずに加工することができるわけですね。
親子爪(スクロールチャックを油圧チャックで掴む)を利用すれば、NC旋盤でスクロールチャックを使用することもできます。
私の勤務先でも、油圧チャックより一回り小さいスクロールチャックを用意しており、それを使って加工することがあります。推奨されていない方法ですので、危険を少しでも減らせるよう注意して運用するようにしましょう。
それでもまだひずむ場合、4つ爪チャックを使えば接点が一つ増えるため、よりひずみにくくなります。とくに一品ものなど少量の加工に向いた方法です。
方法4.面盤・治具を使う
手締めのスクロールチャックでどんなに弱く締めてもひずんでしまう場合もあります。その場合は面盤や、押さえ治具を使って内径の仕上げ加工のみ行います。
面盤とは、下の図のように製品をボルトで止める円盤のことです。
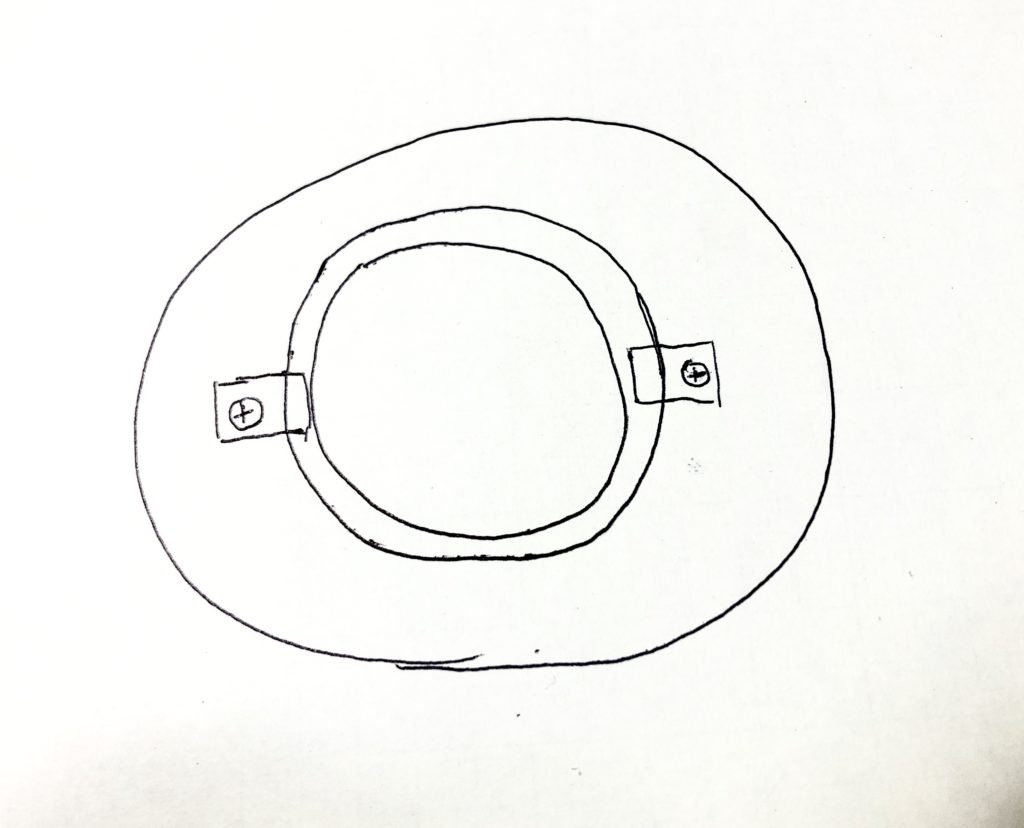
絵が下手ですが真円だと思ってください(笑)
あくまで一例ではありますが、図のように、製品よりも大きい円盤(面盤)をつくり、そこにタップを立て、ボルトと板でワークを面盤に固定します。
その後面盤をチャックでつかみ、てこ式ダイヤルゲージで芯出ししてから加工します。
この方法であれば、径方向に力は全くかからず、端面方向のみの押さえであるためひずむことはまずありません。
ですが、一個だけならこの方法で問題ありませんが、複数個となると毎回芯出しするのは時間がかかりすぎますね。
その場合、製品がはまるように、製品の外径よりわずかに大きい大きさに面盤に内径加工を施しておき、面板に製品をカポッとはめてやります。
そしてボルトと板で固定すれば、芯出しも楽になります。
方法5.幅広・円形の生爪を使う
面板はまずひずむことのない加工方法ですが、多数個の生産であれば生爪での作業が早いです。
しかし当然普通の生爪を使ってもワークがひずんでしまいますので、幅広の生爪もしくは円形生爪を使います。
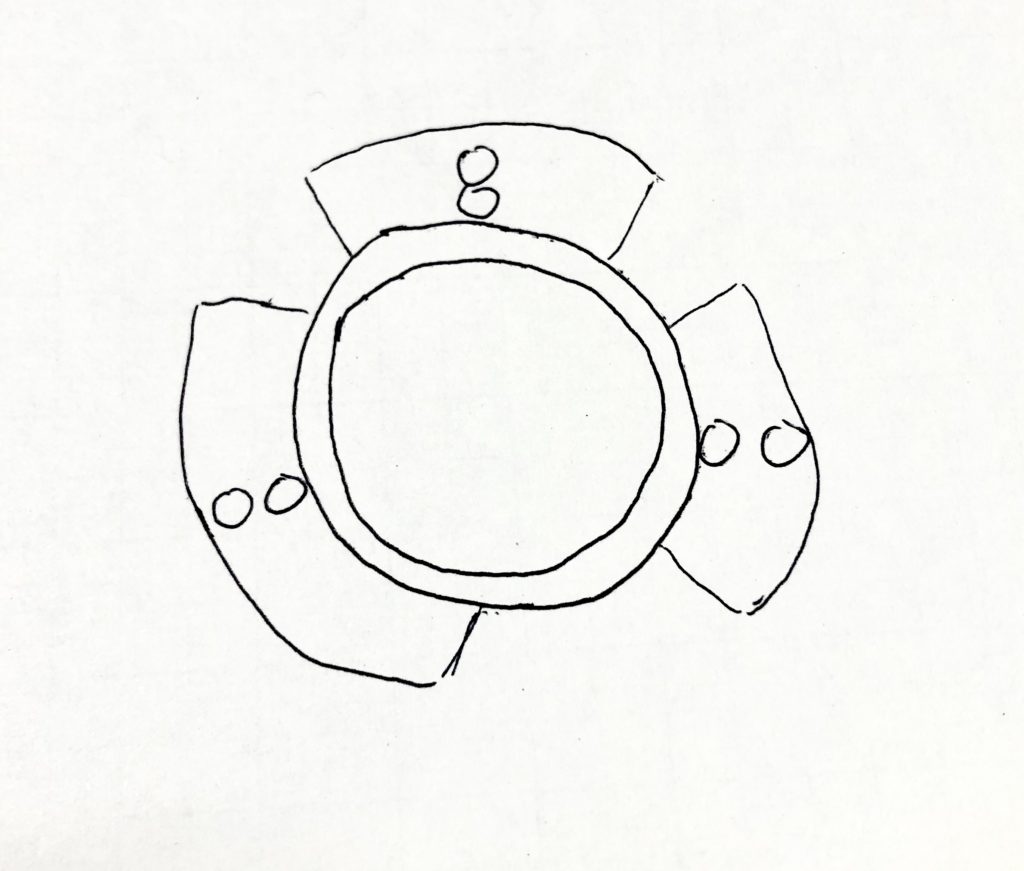
このような生爪が売っているためそれを買う、もしくは溶接などを使って幅広の生爪を用意します。
製品とぴったりの径に生爪を加工し、ほぼ掴んでいないところがないようにすると、ひずみを抑えて仕上げることができます。
内開きで掴むのもいいですね。
しかしこの方法は生爪を用意するコストがかかる上、絶対にひずまなくなるという保証があるわけではありません。
多数個生産でのみ検討する方法になりえると思います。
他にも生爪には面白いものが色々あるので、それらをまとめたこちらの記事も読んでみてください!
結局どのやり方を使えばいいの?
5つの方法を紹介したため、基本はどの方法を使えばいいか紹介します。
・基本は方法1と2を組み合わせてひずまないように加工
・それでもひずんでしまう場合は方法3を使う
・方法3でもひずんでしまう場合は方法4を使う
・多数個生産で、方法1.2.3がだめだった場合、方法5を検討
さらにペラペラなものは低融点金属を使う方法も
小さいもの限定になりますが、低融点金属を入れ子に使った加工方法もあります。
上の記事から読んでみてください!
以上、薄物はなかなか厄介ですが、歪ませずに加工する方法は必ずありますのでまずは今回紹介した方法をお役立ていただけると嬉しいです!
コメント