
旋盤加工やフライス加工などの切削現場で、避けて通れないのが切粉(きりこ)処理の問題。
その切粉の制御に欠かせないのが、「チップブレーカー」です。
刃先に刻まれた一見デザインのような溝ですが、実はそこに、加工品質や作業効率を左右する重要なメカニズムが詰まっています。
とはいえ、チップブレーカーには様々な形状や幅、適用条件があり、
「どう選べばいいの?」「うまく切粉が分断されない…」と悩んでいる方も多いはず。
この記事では、そんなチップブレーカーについて、
までを加工技術者の経験を交えて丁寧に解説していきます。
初心者から現場ベテランまで役立つ実践的な内容となっていますので、ぜひ最後までご覧ください!
チップブレーカーとは?
チップブレーカーとは、切削加工の際に発生する「切粉(チップ)」を効率よく細かくし、扱いやすくするために工具に設けられた特殊な溝や形状のことを指します。
例えば旋盤のインサート(刃物)には、様々な模様が施されているのがわかりますね。
この模様がチップブレーカー。デザインのための模様ではなく、立派な機能性がある、欠かせないものです。
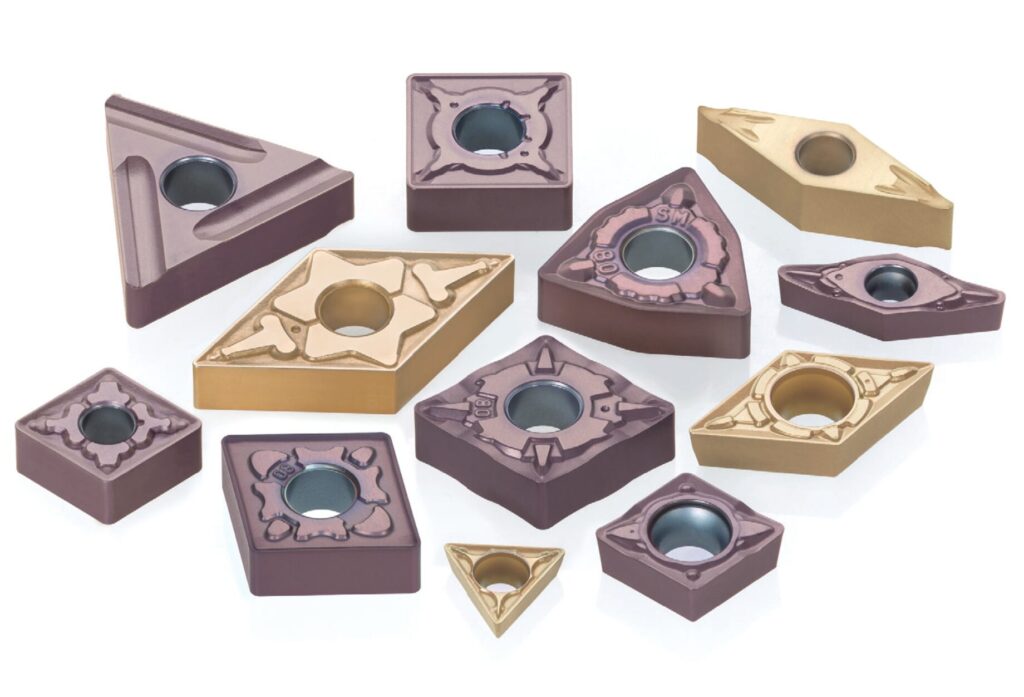
特に旋盤加工では、切粉が長く伸びすぎたり絡まったりすると、工具やワークに傷がついたり、機械の動きを妨げてしまうことも少なくありません。
刃先近くに設けられた溝や段差によって、切粉が適度に曲げられ、途中でポキっと折れて短くなるよう設計されています。
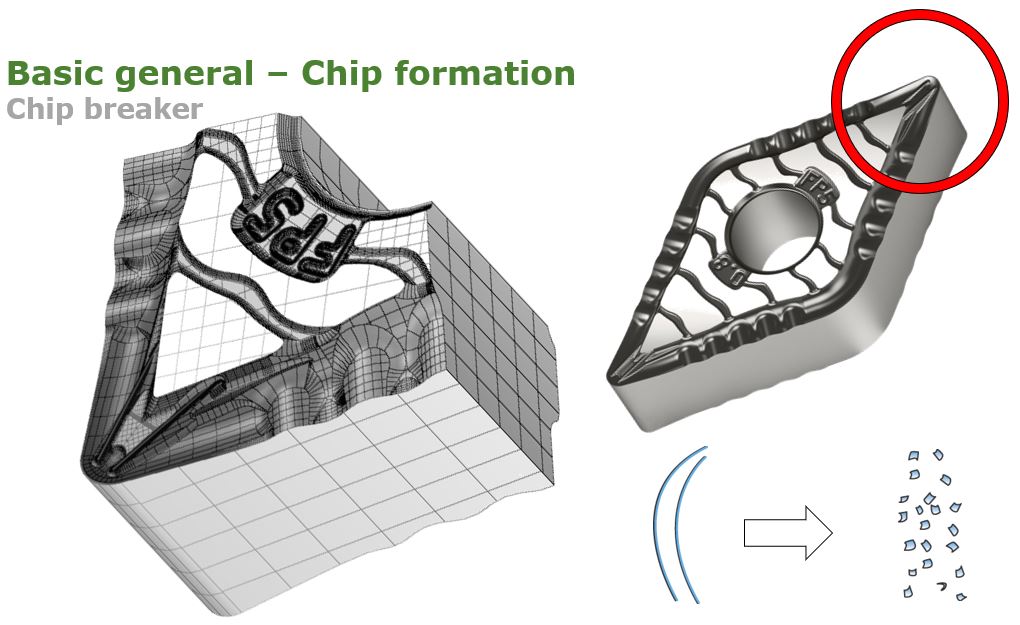
チップブレーカーが果たす主な役割は以下の3つ
- 1. 切粉(切りくず)を短く分断し、絡まりや巻き付き防止
- 2. 加工面をきれいに保つ
- 3. 切削抵抗を安定させて、工具寿命を延ばす
切粉(きりこ)が分断されないと、下画像のように切粉がからまってしまいます。
こうなってしまうと厄介です。削っているワークにキズがついたり、切粉が巻き込んで刃先が欠ける原因になったり、その他にもチップコンベアの不具合につながったり廃棄する切粉のかさが増したりなど、多くのトラブルの原因になります。
こうなってしまうと手作業で除去しながら加工しないといけませんので、作業効率も大きく落ちます。
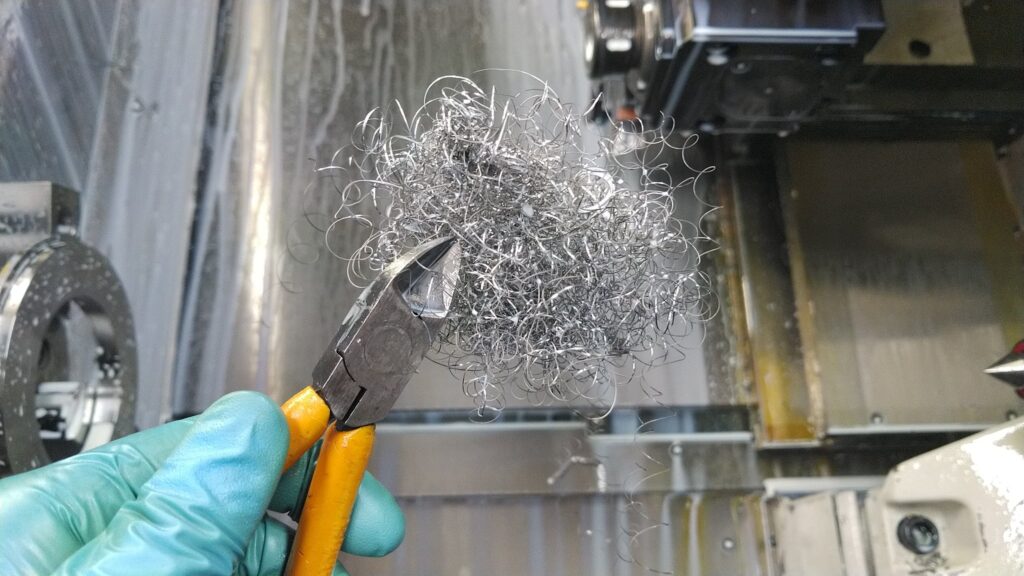
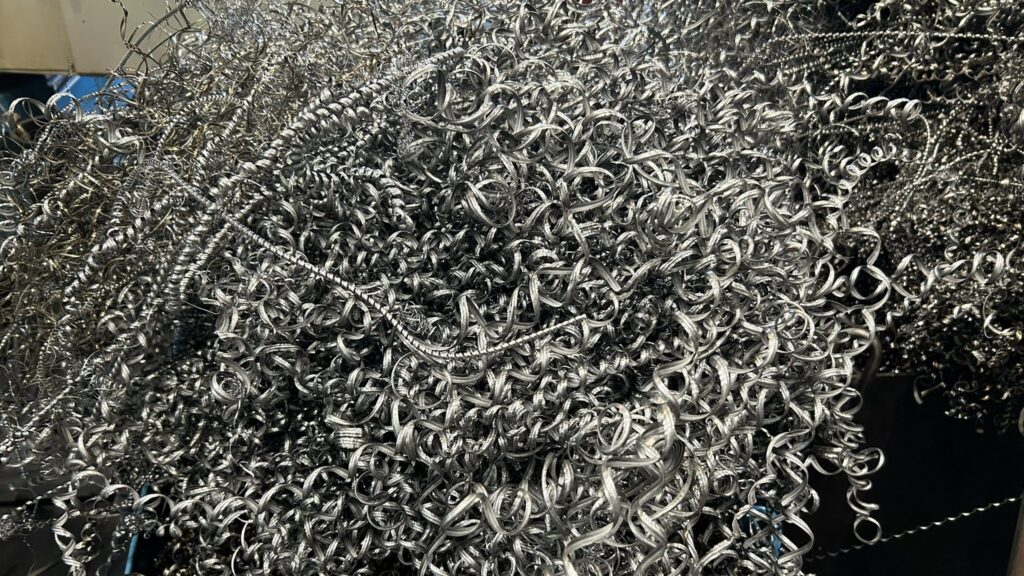
実際にブレーカーによって切粉が細かく分断された様子が下画像です。細かく分断され、処理しやすくなっています。
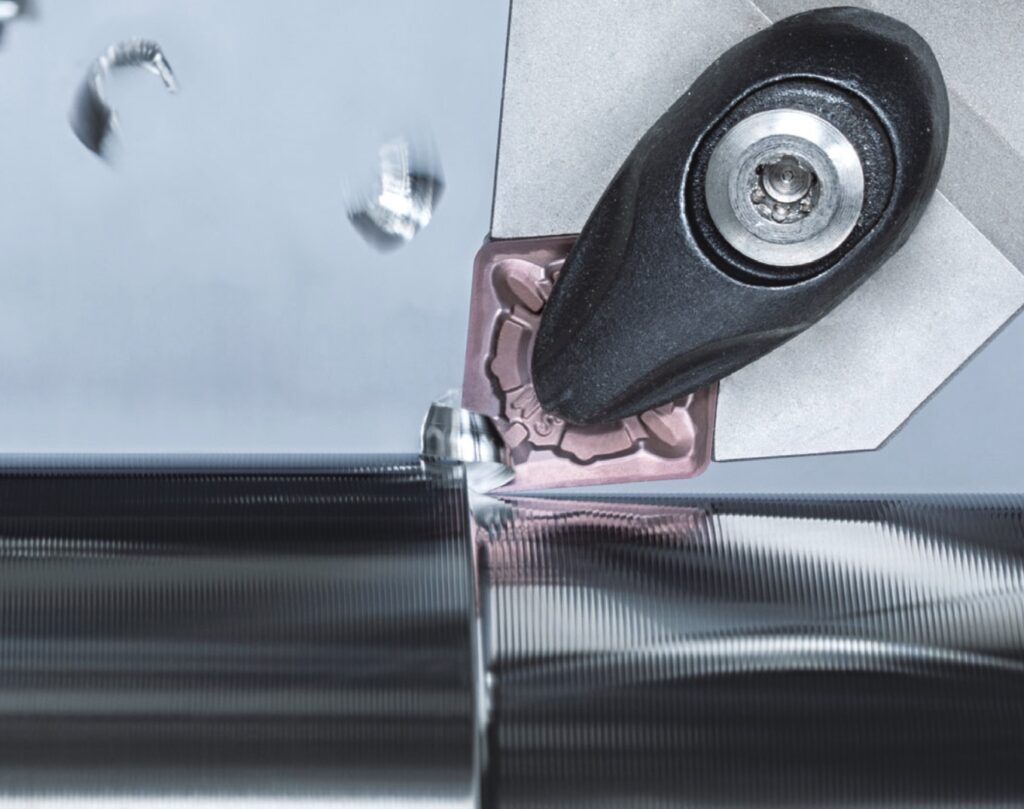
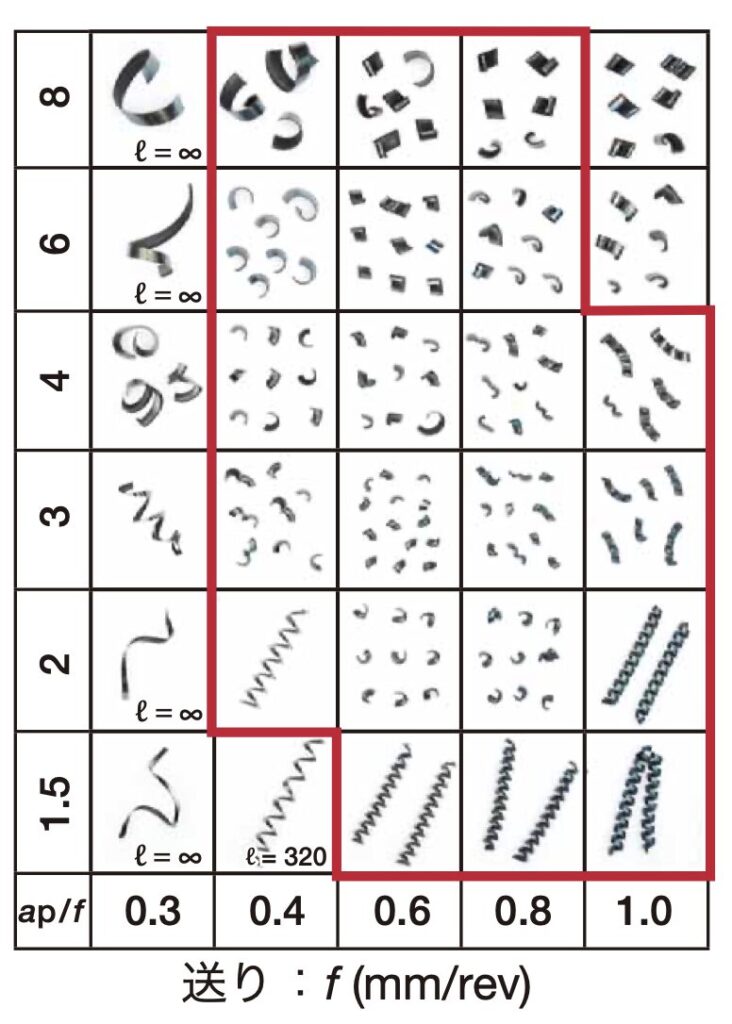
特に大量生産や自動化ラインでは、切粉の処理が安定しないと作業者が都度対応しなければならず、稼働効率が落ちがち。
チップブレーカーを上手く活用することで、生産性アップと加工品質の安定化が同時に狙えるのです。
チップブレーカーのメカニズムは?その仕組みと原理を解説!
切削加工で発生する「切粉(切りくず)」を効率よくコントロールするために欠かせないチップブレーカー。
ここでは、具体的な構造やメカニズム、その原理についてわかりやすく解説します。
チップブレーカーの構造を見てみよう
下の画像をご覧ください。これは旋盤用インサートの一例で、表面に見える独特な溝や凹凸がすべてチップブレーカーの構造です。
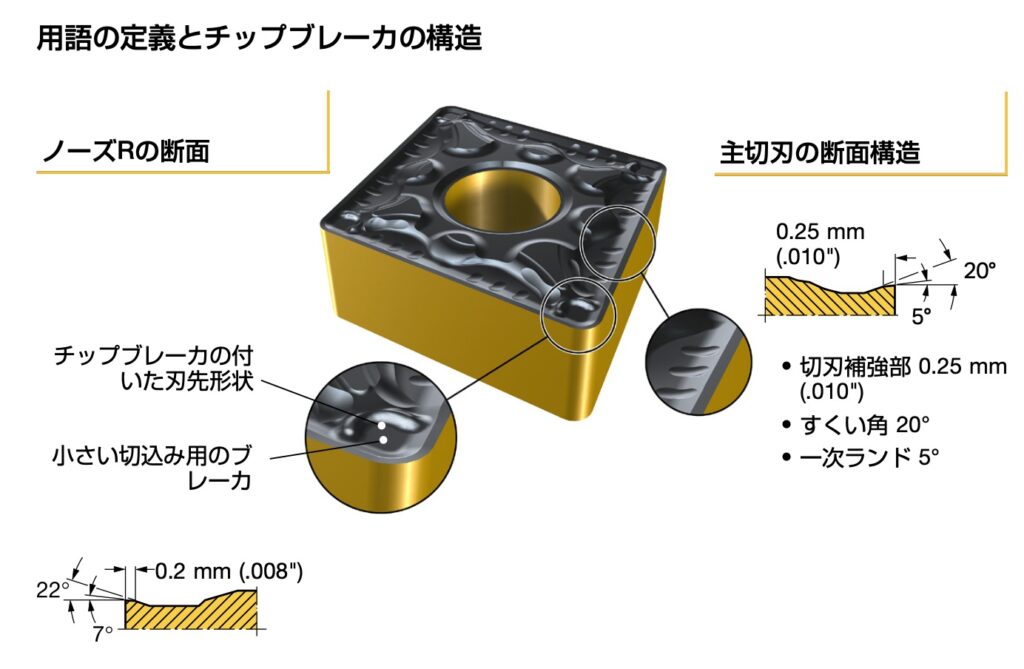
この画像からわかるように、チップブレーカーは単なる模様ではなく、以下のような要素が細かく設計されています。
✔️ 切粉を分断しやすくする溝
✔️ 切粉の曲がりやすさを調整する段差
✔️ 刃先の強度を保つための補強部
たとえば、主切刃部分には以下の特徴があります。
• 切刃補強部:画像の例では0.25mm(0.010インチ)の厚みがあり、刃先の強度を保つ
• すくい角:画像の例では20°。切粉が滑りやすい角度で設計される。
• 一次ランド:画像の例では5°。切刃の安定性を高め、切削抵抗をコントロールする。
また、ノーズR部分には小さな切り込み用のブレーカも設けられており、細かい切粉発生時にも絡みにくい設計になっています。
チップブレーカーの仕組みと原理
では、実際にこの構造がどのように切粉をコントロールしているのか?
そのメカニズムはシンプルかつ巧妙です。
1. 切削開始
→ 刃先で材料が削られ、切粉が発生
2. 切粉がチップブレーカーに接触
→ 表面の溝や段差により、切粉の流れが強制的に曲げられる
3. 切粉が折れ曲がるポイントに応力集中
→ 曲げと引っ張りの力が働き、一定の長さでポキっと破断
これにより、切粉が長く伸びるのを防ぎ、短く処理しやすい形に変えられるのです。
特に、すくい角や補強部の角度・深さが微調整されていることで、切粉の曲がり具合や破断位置が最適化されます。
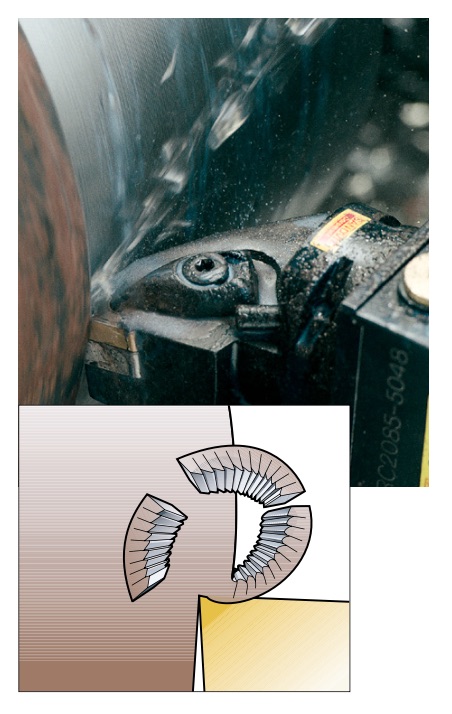
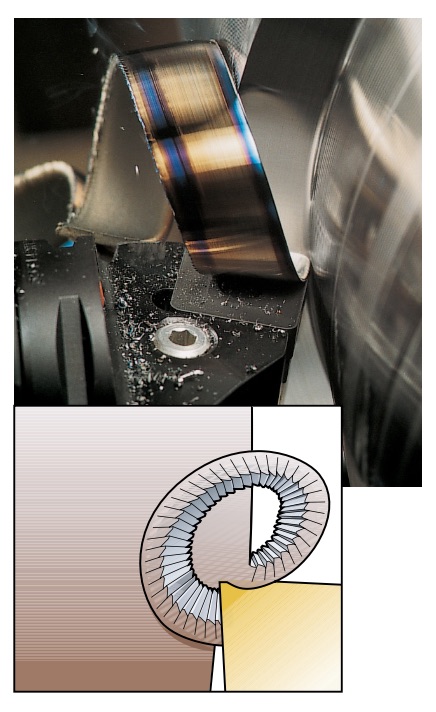
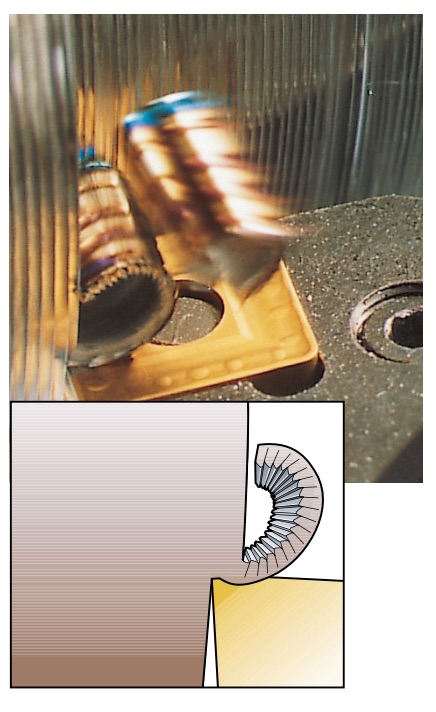
チップブレーカーは「物理的な切粉制御装置」
言い換えれば、チップブレーカーは物理的な切粉制御装置です。
加工条件(材質・送り速度・回転数など)や目的に応じて、溝の深さ・角度・幅を変えることで「狙った切粉の形」を実現しています。
このように、一見シンプルな溝や段差にも、高度な設計思想と物理原理が詰め込まれているのがチップブレーカーの特徴です。
旋盤におけるチップブレーカーの効果と重要性
旋盤加工では、切粉の処理が加工の品質や安全性、生産効率に大きな影響を与えます。
では、実際にチップブレーカーを使うことで、どのような効果が得られるのでしょうか?
具体的に見ていきましょう。
チップブレーカーの効果とは?
1. 切粉の絡まり・巻き付き防止
チップブレーカーの最大の効果は、切粉を短く分断し、絡まりや巻き付きのトラブルを防ぐこと。
特に旋盤加工では、切粉が長く伸びすぎると、以下のような問題を引き起こします。
• 刃先に絡みつき、刃先欠けの原因
• ワーク表面に傷をつけ、公差不良、外観不良
• チップコンベアや機械内部に詰まり、トラブル発生
2. 切削面の品質安定
切粉がスムーズに排出されることで、加工面に傷が入りにくくなるのも大きなメリットです。
とくに連続自動加工や大量生産ラインでは、切粉絡みのトラブルを未然に防ぐことが製品品質の安定化に直結します。
3. 切削抵抗の安定 → 工具寿命アップ
切粉の流れが安定することで、切削抵抗が一定に保たれます。
結果として、
• 工具の摩耗が均一になり
• 不意な負荷変動や折損を防ぎ
• 工具寿命を延ばす
といった効果が得られます。
【比較動画】ブレーカーあり・なしでの切粉挙動の違い
言葉だけではピンと来ない方のために、ブレーカーあり・なしの比較動画を参考にご覧ください。
参考動画:チップブレーカーあり・なしの比較
動画を見ていただくと、
✅ ブレーカーなしの場合、切粉が長く伸び絡まる様子
✅ ブレーカーありの場合、切粉が細かく折れて排出される様子
以上が一目瞭然です。
特に、絡まり防止・作業者の安全確保・効率的な切粉処理の面で、チップブレーカーの効果は絶大であることがわかります。
なぜ旋盤加工においてチップブレーカーは重要なのか?
旋盤加工は、連続的に材料を削る特性上、発生する切粉の量・長さが非常に多くなりやすい加工方法です。
もし切粉が長く連続したままだと、以下のような問題が頻発してしまいます。
• 作業のたびに手作業で切粉を除去
• 機械が停止し、生産効率が低下
• 安全リスクの増大
そのため、旋盤加工=チップブレーカー必須と言っても良いほど、安定した切粉の処理のために欠かせない存在なのです。
こちらの記事で、旋盤加工における、多様なブレーカーの種類についても解説しています。
チップブレーカーのデメリットと注意点
ここまでチップブレーカーの効果や役割についてご紹介してきましたが、
実は使い方や条件次第では、デメリットが発生することもあります。
ここでは、チップブレーカーの注意点を、デメリットと併せてまとめて解説します。
条件が合わないと切粉が破断しにくくなる
チップブレーカーは、決められた切削条件に最適化された設計になっています。
以下のような条件です。
• 送り速度
• 切り込み量
• 被削材の材質
これらが想定外の条件になっていると、せっかくのブレーカー効果がうまく発揮されず、切粉が長く伸びたままになってしまう場合があります。
この場合、切粉の絡まりや、ワークや工具への巻きつきといったトラブルのリスクが生じてしまいます。
ブレーカー形状によっては刃先の強度低下に注意
チップブレーカーは刃先に溝や段差を設けている分、刃先の剛性が若干下がるという側面も。
特に深い溝や鋭角な形状のブレーカーを選ぶと以下のような問題につながります。
• 刃先が欠けやすくなる
• 摩耗が早まる
これは切削条件を上げた場合や被削材が硬い場合などで顕著に現れるため、切削条件とブレーカー形状の相性確認が欠かせません。
また、逆もまた然りで、切れ味の悪いブレーカーによって仕上げ面が悪化する場合もあります。
適材適所のブレーカーを選択することが大切です!
チップブレーカーの形状と幅による切粉処理の最適化
チップブレーカーは、ただ「付いていれば良い」というものではありません。
実は形状や幅の違いが、切粉の処理のしやすさや加工の安定性に大きく影響します。
ここでは、チップブレーカーの形状・幅の違いによる切粉処理の最適化について詳しく見ていきましょう。
チップブレーカーの形状の違い
チップブレーカーの形状には、様々なバリエーションがあります。
主なタイプとしては以下のとおりです。
• 浅溝、研磨ブレーカー
→ 軽切削や仕上げ加工向け。研磨ブレーカーは刃先の強度を犠牲に切れ味を確保している。切粉の流れをコントロールするブレーカー。
• 深溝タイプ
→ 重切削や粗加工向け。切粉を大きく曲げ、確実に分断する効果が高い。
• 特殊パターンタイプ
→ 特定の材質(アルミ、難削材など)向けに設計されたもの。切粉の排出方向や抵抗軽減を、被削材に特化して調整。
形状選びを誤ると、以下のような問題が発生します。
• 切粉が破断しない
• 刃先が欠けやすい
そのため、加工内容に応じた形状選定が重要です。
また、下図の通り、ブレーカーの形状は被削材によって大きく異なります。同じ仕上げ加工でも、材質ごとにその違いは一目瞭然ですね。チップ材質だけでなく、ブレーカーについても被削材ごとに最適なものを選ぶ必要があるということが、感覚的に理解できるかと思います。
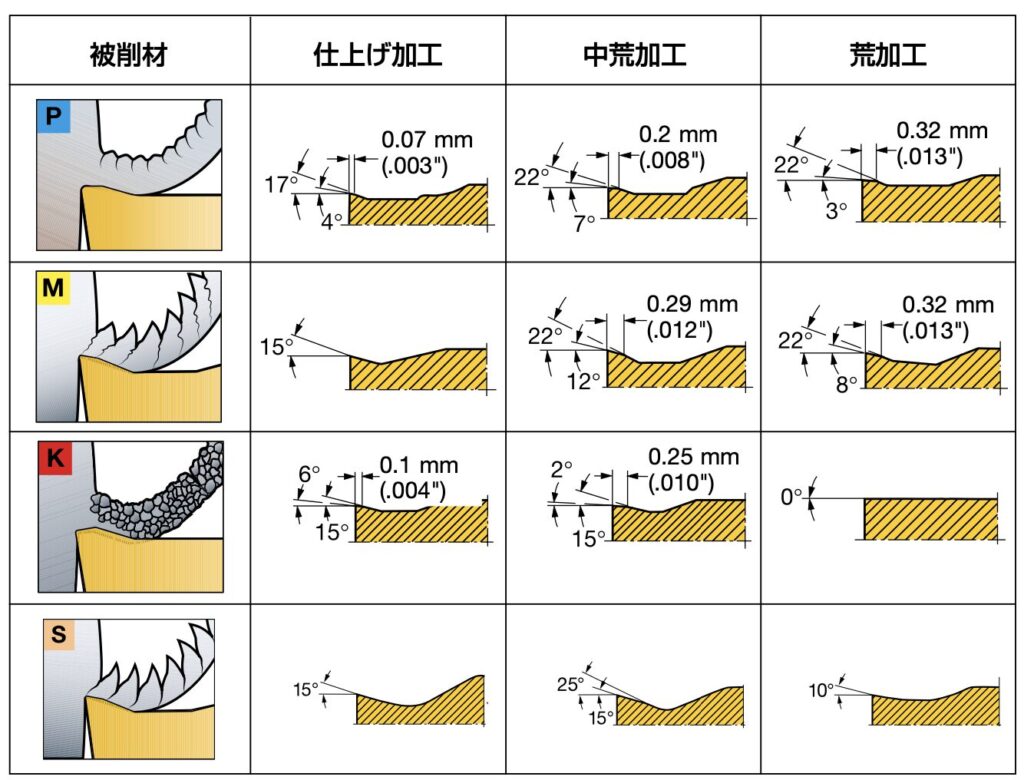
チップブレーカーの幅の役割
形状と並んで重要なのが幅の設定です。
チップブレーカーの幅が広いと以下のようなメリットがあります。
• 大きい切込み量、高い送り速度でも、切粉を大きく曲げる力が働きやすい
• 高条件下で確実な切粉の破断が期待できる
逆に幅が狭くなると、分厚く硬い切粉はブレーカーを乗り越えてしまい、破断ができなくなってしまう一方、細く柔らかい切粉をコントロールすることができます。
幅が広すぎる場合は、通常の条件下での切粉の破断が難しくなるため、汎用性の高いブレーカーを選ぶのであれば、幅の狭め(比較的低切込み低送りに対応)のものを選ぶのがおすすめです。
送り速度や被削材の特性を考慮して適切な幅を選ぶことが求められます。
最適化のポイント
形状と幅の選定は、以下のポイントを押さえると効果的です。
加工内容 | 推奨形状 | 推奨幅 |
---|---|---|
仕上げ加工 | 浅溝・研磨ブレーカー | 狭め |
中切削 | 標準溝タイプ | 中間幅 |
粗加工・重切削 | 深溝タイプ | 広め |
特殊な材質・難削材加工 | 特殊パターンタイプ | 材質ごとに最適幅設定 |
さらに、切削条件の変化(送り速度・切込み量)に応じてチップブレーカーの幅・形状を使い分けることで、切粉の処理と工具寿命の両立が可能になります。
とはいえ実際の現場では、加工ごとに最適なブレーカーを選ぶというよりは、自社が加工する上で汎用的に使える数種のブレーカーに絞って使う場合が多いです。常に最適解のブレーカーにこだわっていると、チップ交換に手間がかかって効率が落ちてしまう原因になってしまいます。
切粉の分断性能や工具寿命と、自社における汎用性のバランスをとりながら選定するのが大切です。
チップブレーカー選定のポイント
チップブレーカーは、形状や幅、角度などのバリエーションが豊富で、加工条件に応じて最適なものを選ぶことが非常に重要です。
ここでは、加工対象や切削条件に合わせたチップブレーカーの選び方の基本を解説します。
1. 被削材に合わせて選ぶ
チップブレーカーを選ぶうえで、まず押さえておきたいのが被削材(加工する素材)の特性です。
それぞれの材質で、切粉の形状や性質が大きく異なるため、適切なブレーカー形状を選ばないと、切粉処理に失敗してしまいます。
以下は、材質ごとの切粉の違いを比較した参考画像です。
材質 | 特性・傾向 | ブレーカー選定のポイント |
---|---|---|
P:鋼 | 比較的安定した切粉が出る | 標準形状が最適 |
M:ステンレス鋼 | 切粉が粘りやすく絡みやすい | 流れをコントロールしやすい深めの溝、かつSUS304などは難削材のため、強い刃先のもの |
K:鋳鉄 | 脆くて細かく砕けやすい | 切粉は自動的に分断されるため、ブレーカー不要な場合も。 |
N:非鉄金属 | 切粉が柔らかく、分断しにくい | 大きめのすくい角で滑らかに排出できる形状が有効 |
S:耐熱合金 | ねばりが強く高温になる | 強い流れ制御+耐熱性に配慮した設計が必要 |
H:高硬度鋼 | 切削抵抗が高く、刃先への負荷が大きい | 刃先強度を重視した形状 |
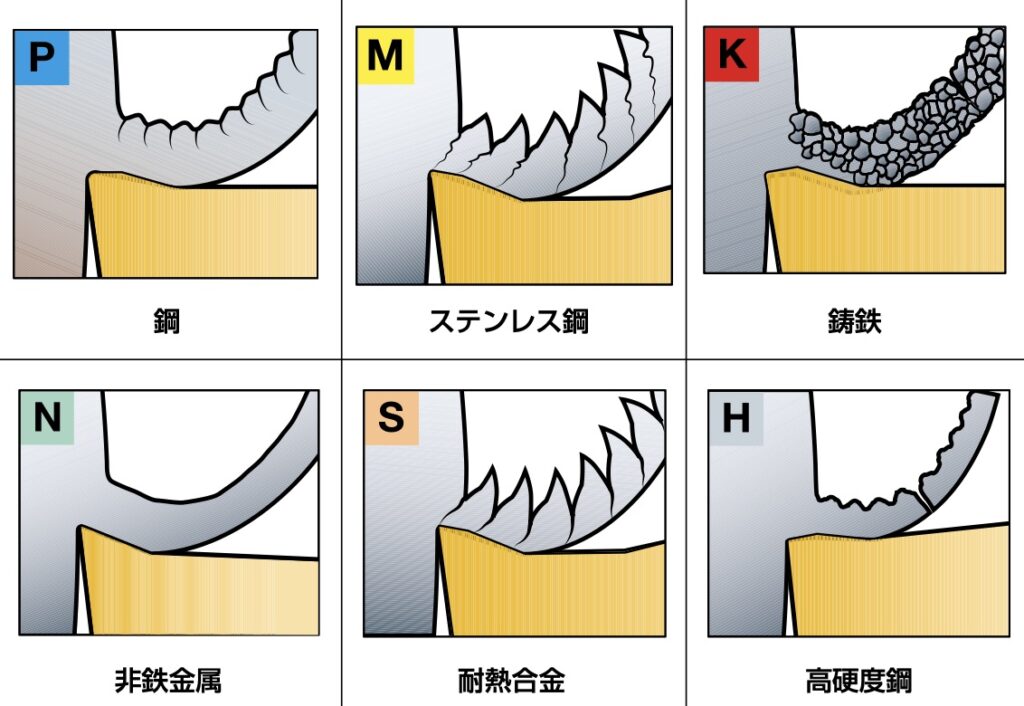
2. 加工目的に合わせて選ぶ(荒加工・中仕上げ・仕上げ)
加工のステージによっても、選ぶべきブレーカー形状は変わります。
加工ステージ | 推奨ブレーカー形状 |
---|---|
荒加工 | 深溝タイプ、幅広タイプ(切粉をしっかり破断) |
中仕上げ | 標準溝タイプ(切粉処理と仕上がりのバランス) |
仕上げ | 浅溝・狭幅タイプ(滑らかな表面、低抵抗) |
切粉の量や勢い、工具への負荷が段階ごとに異なるため、常に加工目的と工具性能のバランスを取ることが大切です。
3. 切削条件に適しているか確認する
送り量や切り込み量、回転数などの切削条件とブレーカー設計が合っているかも、非常に重要です。
• 送りが遅すぎる → 切粉の太さがブレーカーで破断される太さに届かず、破断できない
• 切り込みが浅すぎる → ブレーカーに届かず破断できない
•高送りすぎる → 切粉が太くなりすぎてブレーカーを乗り越えるため、破断されない
ブレーカーの効果を最大限に発揮するには、カタログの推奨条件と自社の実条件を照らし合わせて調整することが求められます。
このように、材質・加工ステージ・切削条件の3点を軸にチップブレーカーを選定することで、切粉の処理性・加工品質・工具寿命のいずれも安定しやすくなります。
チップブレーカーの種類と、おすすめブレーカー
こちらの記事で、チップブレーカーの種類について深堀りして解説を行っています。
多様なバイトのチップブレーカーと、ブレーカーの良さを活かしたHORN社のおすすめバイトをご紹介していますので、ぜひ併せてご覧ください!
チップブレーカーの効果を最大化するための実践的アドバイス
チップブレーカーは正しく選定することも大切ですが、その性能を最大限に引き出すには“使いこなし”が重要です。
ここでは、実加工で得られた現場の知見を交えながら、効果を引き出すための具体的な活用ポイントをご紹介します!
荒加工で切粉が分断されない?まずは送り・切り込み量を上げてみよう
実際の加工現場では、切粉が分断されずに長くつながってしまうという悩みは少なくありません。
このような場合、まず試してほしいのが次のアプローチです。
✅ 送り(f)を上げる
✅ 切り込み量(ap)を上げる
この2つを組み合わせることで、切粉が太くなるため折れやすくなり、切粉が大きくなることで切粉がブレーカーの溝に届き効果がしっかり発揮されるようになることが多いです。
慣れてくると、切粉の出かたでどの切削条件をいじれば上手くいくのかがわかってきます。
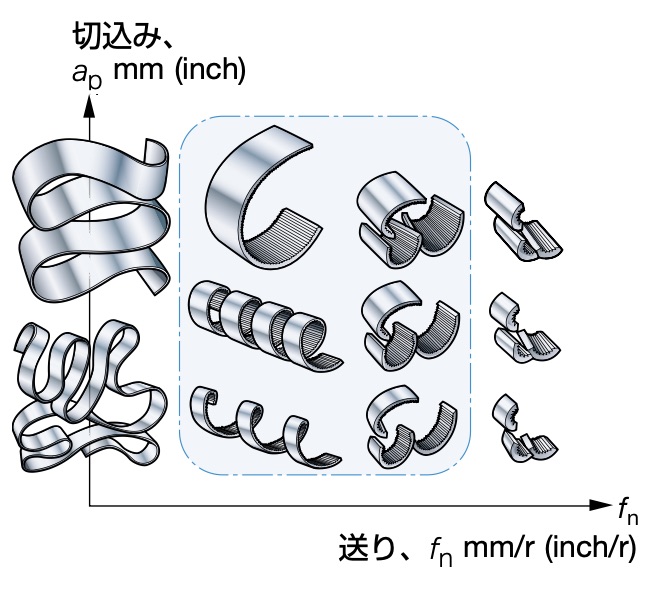
おかしいと思ったらカタログの推奨値を確認
切粉をうまく分断できないとき、闇雲に条件をいじってもうまくいかない場合があります。
その場合は、切削条件がメーカー推奨の範囲内に収まっているかどうかを確認しましょう。
ブレーカー形状は、それぞれ「この範囲で使ってください」という最適条件が決まっています。
• 最小/最大の切り込み量(ap)
• 適正な送り速度(f)
• 推奨される材質別適用範囲
これらはインサートのカタログに明記されていることが多いため、加工に入る前の確認が非常に重要です。
一方で、カタログの条件が全て正しいとも限らないことに注意しましょう。クランプ条件や工具、ワークの状態など、その他の要因で加工条件を調整しなければならない場合も多々あるからです。
柔らかいアルミには専用のブレーカーを。
現場でありがちなのが、「とりあえず同じインサートを他の材質にも流用して使っている」ケース。
私もよくやっており、SUS303のような削りやすいステンレスと、鋼材、アルミの仕上げは全て同じチップで加工してしまうことが多いです。
ですが、たとえばA5052のようなやわらかいアルミの荒加工は、鉄やステンレスと同じようにやろうと思うとうまくいきません。
このような材質を削る場合は、アルミ専用のブレーカーを使うようにするのが得策です。
滑りやすく、変形しやすい材質ですので、すくい角が大きく、表面が滑らかに仕上げられたブレーカー形状が効果的です。
端面荒加工には「低切込み用ブレーカー」がおすすめ
意外と見落としがちなのが、外形加工時と端面加工時のチップブレーカーの使い分けです。
外径加工では問題ないブレーカーでも、端面を1mmずつ加工するような工程では、メーカー第一推奨の荒加工用ブレーカーでは切粉がうまく分断されないことがあります。
その理由は単純で、切込み量が小さすぎて推奨の切削条件から外れてしまうためです。「切粉が細すぎてブレーカーの機能を活かせていない」わけですね。
このようなケースでは、以下のように対処すると効果的です。
✅ 「低切込み専用ブレーカー」を使う
✅ できる範囲で切り込み量を調整し、切粉の太さを確保する
ぜひ実加工にも活かしていただければと思います。
現場で気づく!実加工から得られるフィードバックの重要性
カタログや理論だけではわからないのが、現場での“リアルな経験”です。どんなに最適な形状を選んでも、実際の切削条件に合っていなければ、期待した効果は得られません。
例えば以下のようなトラブルがあります。
• 切粉が絡む
• 切粉が分断されず長く伸びる
• 刃先にダメージが蓄積する
• 加工面に傷が残る
こうした現象には、工具そのものではなく、使用条件に原因があるケースも多々あります。
だからこそ、カタログの値はもちろん、実加工の結果からもフィードバックを得て、条件を見直すサイクルがとても大切なのです。
ぜひ当サイトのトップページにも訪れていただき、様々な加工に関する記事もご参考にしてください。
まとめ:チップブレーカーを「知って使いこなす」ことが、加工品質の安定化につながる
チップブレーカーは、単なる「切粉を折るためのパーツ」ではありません。
その構造、形状、幅、適用条件のすべてに意味があり、加工品質・効率・安全性を左右する重要な要素です。
今回の記事では、以下のような知識を現場目線で総合的にご紹介しました。
ポイントは、「チップブレーカーを知る」ことに加え「正しく選び、条件に合わせて使いこなす」こと。
送りや切り込み量の調整、材質ごとの使い分け、カタログの推奨値の確認など、ちょっとした工夫で大きく結果が変わるのがチップブレーカーの面白さであり奥深さです。
切粉の処理に悩んでいる方や、より効率的な加工を目指す方にとって、この記事が少しでも現場改善のヒントになれば幸いです。
コメント