
旋盤加工やフライス加工において、材料と刃物がぶつかるスピードが切削速度(m/min)です。
切削速度は、速すぎても遅すぎても不都合が出てくるため、適正な切削速度を保つ必要があります。
本記事では切削速度が”遅い“とどうなるかを解説しました!
以前書いた適正切削速度の記事と合わせてご覧いただくと理解が深まると思います。
「切削速度が遅い」デメリット
刃先の摩耗が大変はやくなる
特に旋盤の内外径の仕上げ加工に使うチップでよく起こる現象で、サーメットのチップでは特に顕著です。
いきすぎた低切削速度域で加工すると、摩耗が大変速くなります。
低切削速度域での加工において、刃先は、Belag(削ったときに発生する酸化物の皮膜)や構成刃先が剥離するごとに、1~2μmずつの粒子を剥離しながら削っています。
そのため激しく摩耗が進行し、すぐに仕上げ面がテーパーになってしまいます。
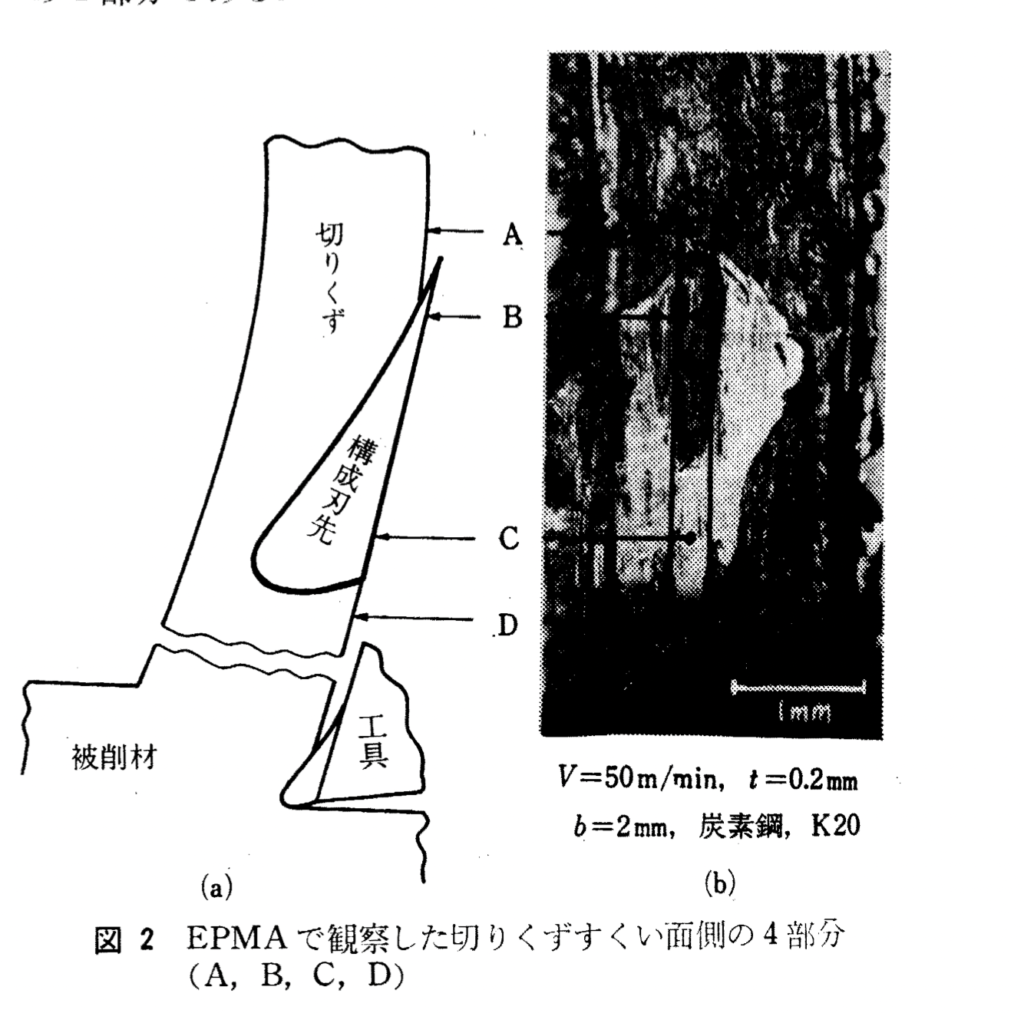
(参考:https://www.jstage.jst.go.jp/article/jjspe1933/38/446/38_446_261/_pdf)
チッピングしやすくなる
低切削速度域でのチッピングは旋盤・フライス問わず超硬工具で起こるトラブルですが、特に断続切削になるフライス加工で顕著です。
チッピングの主な原因は「構成刃先」と「送り速度」です。
超硬工具ではハイスと比べて刃物の靭性が低く、1刃あたりの送り量が上がってしまいがちな低切削速度域では、刃先が負荷に耐えられずチッピングしてしまうことが多いです。
また、前項でも触れた構成刃先も原因の一つ。低切削速度域で発生する構成刃先が脱落する際、靭性の低い超硬工具ではチッピングが起きやすくなります。
一方でハイス工具であれば、以下の理由から低切削速度域でも通常通り安定して削れる場合が多いです。
- 超硬と比べて刃先を鋭利にでき、切削抵抗が少ない状態で削れるため、構成刃先が発生しにくい。
- 工具の靭性が高いため、構成刃先が発生しても、構成刃先が脱落する際にチッピングが起こりにくい
- 低切削速度、送り速度高めの条件で刃先に負荷をかけても、靭性が高いため刃物がチッピングしにくい
特にフライス加工ではハイスと超硬のエンドミルを使い分けられる場合も多いため、低切削速度域では積極的にハイスのエンドミルを使ってみましょう。
ハイスは切削速度は上げられませんので、両方のいいとこ取りができるような使い方が理想ですね!
旋盤加工でも同様に、低切削速度の条件で、刃先が鋭利な刃物(仕上げ用のチップなど)で送り速度を上げるとすぐにチッピングしてしまいますし、前項で解説した摩耗も激しく進行しますので、適正な切削速度で加工するようにしましょう。
表面が荒れる
切削速度が遅いと起こる構成刃先によって、表面がガサガサになってしまう場合があります。
下図のように、構成刃先が起こると切れ味の良い本来の刃物ではなく、切れ味の悪い構成刃先で材料を削っていくことになります。さらに構成刃先は成長と脱落を繰り返すため表面も均一にならず、表面が荒れてしまいます。
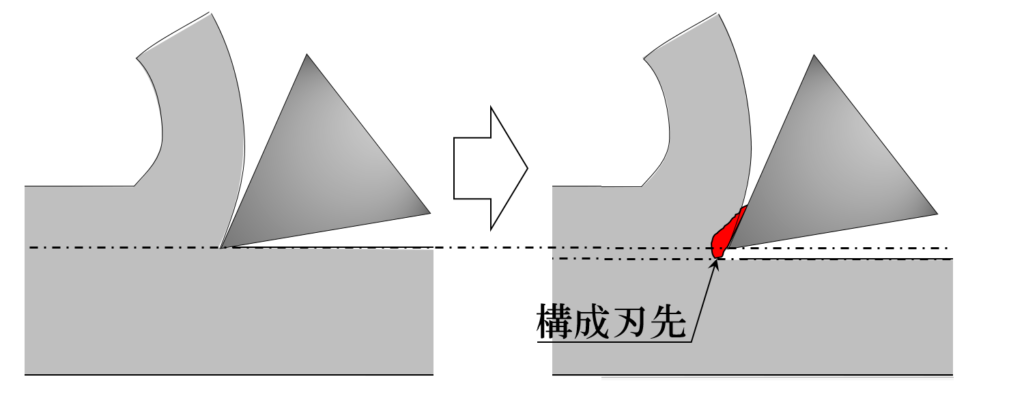
寸法がズレる
前項と同様に、構成刃先ができると、その分刃先が一時的に本来の刃先よりも長くなります。
すると削りすぎてしまい、寸法もマイナスしてしまうことがたびたび起きます。
私も経験がありますが、それによってH7、h7のような公差を外してしまうことも十分ありますので、仕上げの際は構成刃先が起こらないように切削速度を適正値まで上げる、そして刃先の状態に気を配ることが大切です。
構成刃先がおきても表面品質が問題になりにくいSUS304といったステンレスでもこの寸法の問題は起こるため、注意しておくと良いですね。
加工が遅い
送り速度は、旋盤では1回転あたりの送り速度f(mm/rev)、フライス加工では1分あたりの送り速度F(mm/min)で指令するのが基本ですが、どちらも切削速度を遅くした上で同じ理論表面粗さを保とうと思うと加工スピードを落とす必要があります。
そのため切削速度を落とすとサイクルタイムが長くなることがほとんどで、加工に時間がかかってしまいます!
どの仕事でもそうかとは思いますが、特に加工の仕事においては「時間」が大変重要です。倍の速さで加工できれば売上は倍近くになるわけですからね。(仕事があればですが。)
特に10個以上くらいの数ものやサイクルタイムの長い加工を行う場合、摩耗が激しくならない範囲でなるべく切削速度を上げて、加工時間を短縮するのが理想です。
「切削速度が遅い」メリット
切削速度が遅いことによるデメリットを様々書いてきましたが、低切削速度ならではのメリットもあります。
びびりにくい
切削速度を遅くすると、工具やワークの振動である「びびり」が減少します。
びびりは、3つの要素から起こる現象で、その中でも切削速度は「切削抵抗」に関わってきます。
切削速度を落とすことで切削抵抗が低くなり、びびりが少なくなるため、びびりが問題になった場合は切削速度を落としてみましょう!
びびりについてはこちらの記事で詳しく解説しています。
焼入れ鋼など、硬い材質は低切削速度が適する場合も
デメリットの項でもご説明したとおり、通常、特に旋盤加工では、切削温度が低くなる低切削速度域で構成刃先が発生してしまいます。
しかし焼入れ鋼をはじめとした硬度が高めの材料でしたら硬い分刃先に材料がくっつきにくくなるため、構成刃先が起こりにくいです。
その代わり通常の切削速度で削ると逆に摩耗が激しく進行してしまいます。
そのため、焼入れ鋼など硬い材質を加工する場合は、あえて切削速度を低め(40mm/minくらい)にすることで、摩耗も大きく改善されてテーパーになることなく加工することができます。
CBN等の焼入れ鋼用のチップでしたら100mm/minくらいで加工しても問題ありません。
フライス加工でも同様に硬い材料の加工には低切削速度の方が適しますが、断続切削になる分、通常の超硬工具では厳しい加工になります。
しっかりと切削条件を落とし、ゆっくり加工の様子を見ながら安全に加工を行いましょう。
より硬い材料には、高硬度用のエンドミルを適正条件で使用するのが望ましいです。
摩耗・チッピングが少ない
デメリットの項で書いた「摩耗・チッピングが多い」と真逆のことを書いてしまい、混乱してしまいますよね^^;
切削速度が遅いと摩耗・チッピングが起こりやすい場合もありますが、材質や断続切削、刃物によっては、切削速度を遅くしたほうが摩耗・チッピングが起こりにくくなります。
具体的には、断続切削や硬い材質です。前項で書いたように硬い材質では構成刃先も起こらず摩耗が少なくなりますし、刃先にダメージの大きい断続切削では切削抵抗の少ない低切削速度のほうが有利です。
例えばSS400といった鋼材の連続切削では、“適正速度の範囲内では”切削速度が遅いほど摩耗が少なくなります。
このことは三菱マテリアルのカタログにも記載されており、記事にもしていますのでぜひご覧ください!
低切削速度での加工にはハイス工具を活用しよう!
低切削速度域では、切削抵抗が大きくなると構成刃先が発生するため、できるだけ切れ味の良い刃物を使う必要があります。
旋盤加工においては、鋭いブレーカーの超硬工具を低切削速度域で使うとチッピングの原因になりますので、靭性の高いハイスの刃物を切れ味よく研いで使用することをおすすめします!
フライス加工においても、低切削速度での加工が必要な場合は、超硬エンドミルより、靭性がありチッピングしにくいハイスエンドミルのほうが向いています。
繰り返しになりますが、ハイスと超硬の使い分けについてはこちらの記事で解説しています!!
まとめ
切削速度が遅いことには、デメリットも多いですが、メリットもあります。
同じ材質で同じ刃物を使っていても、クランプ状況などによって使うべき切削速度は異なってきますので、その時々でベストな条件設定に近づけると良いですね。
コメント
読みやすい記事で大変に参考になりました。ありがとうございます。
ちなみにこの記事は何のフォントですか?
お読みくださりありがとうございます!参考にしていただけたとのこと大変うれしいです。
確認しましたところ、フォントは”游ゴシック体ヒラギノ角ゴ”を使用しておりました。