
リーマとは、わかりやすく言うと精度の出ていない穴を高精度のきれいな穴に整えるための工具です!
下穴をくり広げることで精度を高め、真円度や表面粗さを向上させます。
この「リーマ」加工、穴に通すだけといえば通すだけなのですが、やってみると意外とトラブルの多い加工です。
本記事では、現役加工技術者である私が、マシニングセンタ・フライス盤を使ったリーマの使い方と加工手順、上手く加工するためのコツを解説しました!
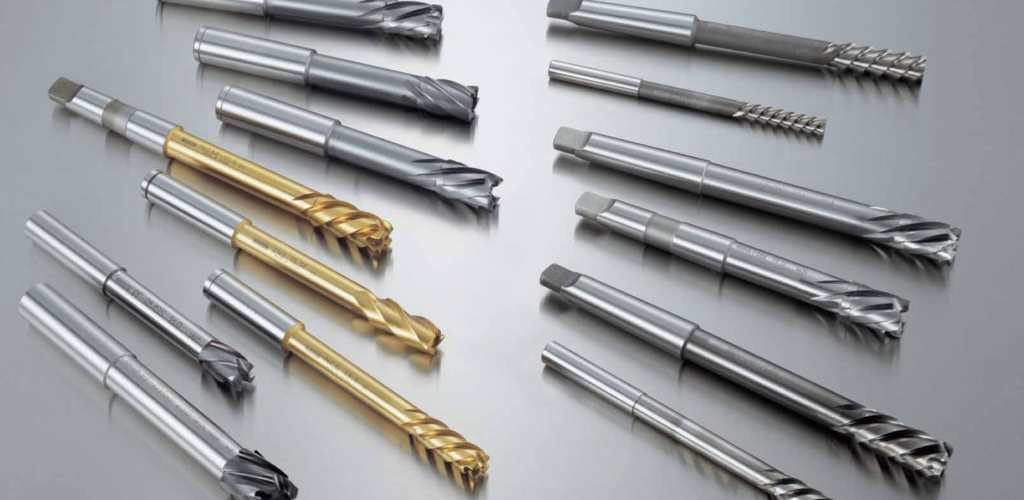
どのリーマを使う??
リーマには様々な種類があります。
ですが、私が普段使うのはその中でもハイスのブローチリーマとスキルリーマの2種類のみです。
私の勤務先では少量多品種加工が大半を占めるため、コスト面を考慮してハイス製のものを使う場合がほとんどです。
この2種類をどのように使い分けるのかというと、止まり穴にはスキルリーマ、貫通穴にはブローチリーマです。
ブローチリーマは刃先に耐久性がある一方、15mmほど余分に切り込む必要があり、貫通穴にしか対応できません。スキルリーマは比較的刃先が傷みやすいですが、その分止まり穴でも加工することができます。


切れ刃がストレートの”ハンドリーマ”も使えますが、上記リーマと比べて表面が悪くなりがちのため、在庫のサイズがないなどの理由がなければ使いません。
リーマ加工の手順
では、早速リーマの使い方の説明に入っていきます。
まずはリーマ加工の全体の流れをご説明します。
ブローチリーマを使った貫通穴加工、スキルリーマを使った止まり穴加工、どちらも手順は以下のとおりです。(φ10の場合)
〜φ10H7公差穴の加工手順〜
- 芯もみ
- 9.5キリ穴開け
- φ10のエンドミルを通す
- φ10のリーマを通す
(リーマ径が変わっても、キリはリーマ径-0.5mmのもの、エンドミルはリーマと同径のものを使います)
以上の通り、リーマ穴を加工するだけで4本もの工具を使用します。
そのため汎用フライス盤などで工具を手作業で付け替えながら作業を行っていると大変な時間がかかってしまいます。特に2穴以上の場合、マシニングセンタで自動加工を行うことをおすすめします。
マシニングセンタを使っても、リーマ加工はそこそこ時間のかかる加工です。
下図、日研様のカタログでは、推奨の手順として面取りが入っていますね。
もちろん面取りはあるに越したことはありませんが、リーマと同じ径のエンドミルを使う場合は面取りがなくても問題なくリーマ加工が可能です。
私も面取りは、時間短縮のため、リーマ加工後に手作業で行うことが多いです。
ただしエンドミルを使わない場合など、仕上げしろが0.1以上残っている場合には、食い付き時のリーマの振れを防ぐために面取りは行っておきましょう。
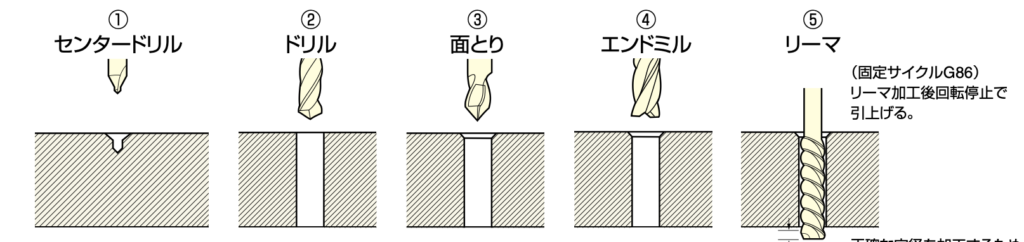
手でリーマ加工を行う方法は?
ハンドリーマを使えば、手でリーマを通すこともできます。
リーマは後端に4面取りが施されていますので、その部分をタップハンドルでつかみ、手回しでリーマを通します。
手で作業するときの問題点は、機械で作業を行うときのようには直角が出ない点です。食い付き時はもちろん、加工中もこまめにスコヤを使って直角を見ながら作業するようにしましょう。
注意する点は、タップのように逆転をさせないことです。切粉が噛み込んでキズだらけになってしまいます。加工後にリーマを抜く際も、正転方向に回転させて抜くようにしましょう。
下穴については、手作業ではエンドミルを通すことは難しいため、ドリル穴から通すことになるかと思います。その場合でも、仕上げしろは0.2未満程度にしておくと良いです。
どちらにせよ、手では大変時間のかかる作業ですので、ボール盤など機械での作業をおすすめします。
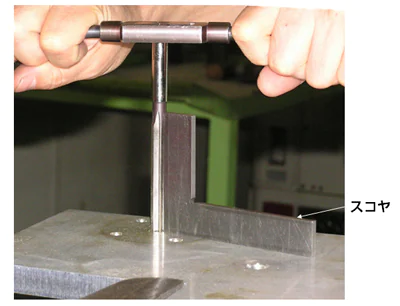
貫通穴と底づき穴の切り込み深さの違い
貫通穴でしたら切粉が逃げるため難しくありませんが、比較的厄介なのが”止まり”のリーマ穴です。
そのため、貫通穴と止まり穴で加工方法を変える必要があります。
貫通穴の切り込み量
貫通穴の場合は難しくありません。
ドリル穴とエンドミルは貫通するまで通してしまい、リーマの有効部分を全て通せばOKです。
ブローチリーマの不完全部は見た目より長いです。そのため私はφ12以下のリーマで15mm余分に切り込むようにしています。
15mmあれば不完全分が残ってしまうことはありません。
スキルリーマで貫通穴を加工する場合は、不完全分が0.5mmくらいのため、1mmも余分に切り込めば全く問題ありません。
止まり穴の切り込み量
止まり穴は、エンドミルとリーマを通す際に気を遣います。
切粉の逃げ場がないため、切粉が悪さをして穴径が大きくなり、公差を外してしまうことがあるためです。
止まり穴の中でも底に平らな部分が必要な底づき穴では、切粉によって穴径が拡大してしまうリスクがさらに大きくなります。そして下部が完全に平らな部分にリーマを通すのはかなり危険ですので、特別な理由がない限りは行いません。
通常の止まり穴では下穴は少し深めに入れておきましょう。特別な理由がない限り、図面上で底面が平らになっていても、ドリル先端部が残っても問題ない場合が多いです。(要確認ですが)
私の場合は通常であれば、下穴は有効長+2mmであけ、エンドミルを有効長+0.6mm、リーマを+0.5mmで加工するようにしています。
そして、エンドミルやリーマを通す際に特に注意が必要なのが底づき穴です。
安定した加工のため、底づき穴でもドリル先端部は径の最低3分の2くらいが残るようにしておきたいところです。言い換えると底の平らな部分が穴径の3分の1以下くらいです。
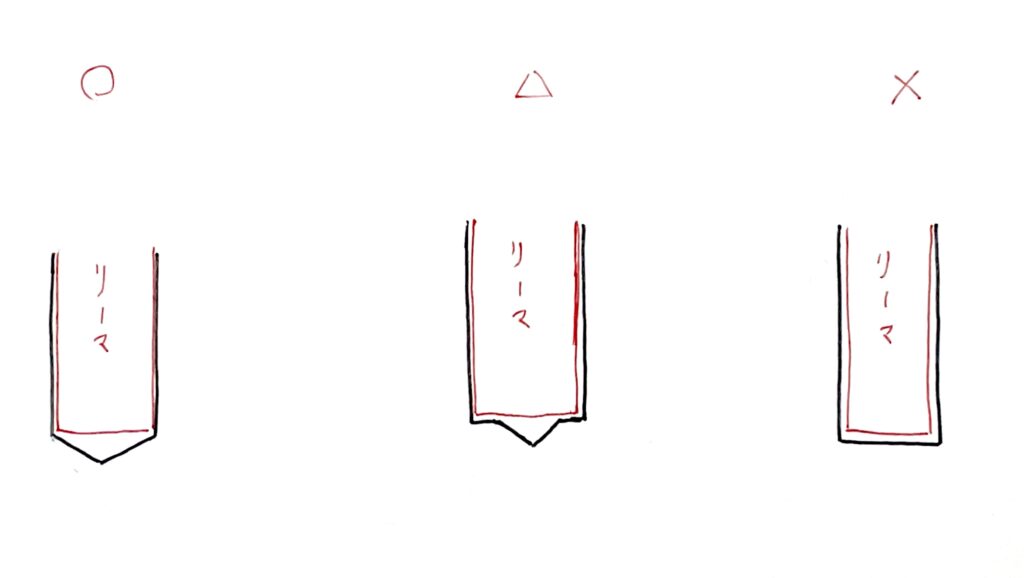
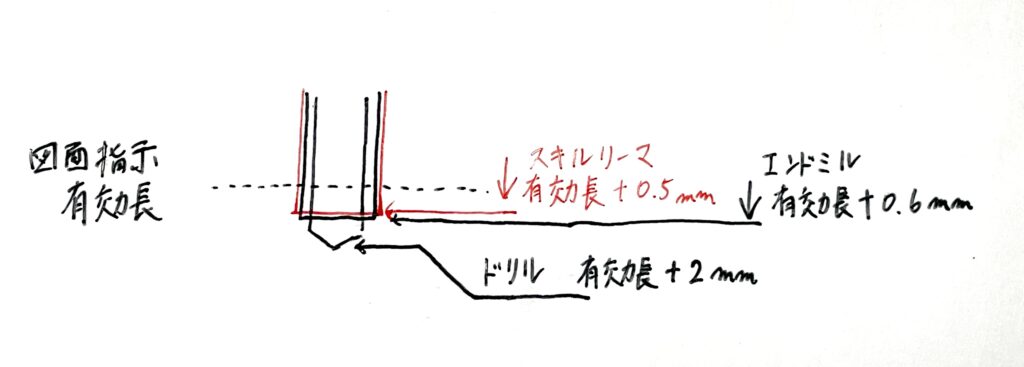
それでは次に、各手順の解説に入っていきます。
芯もみ、キリ穴あけ
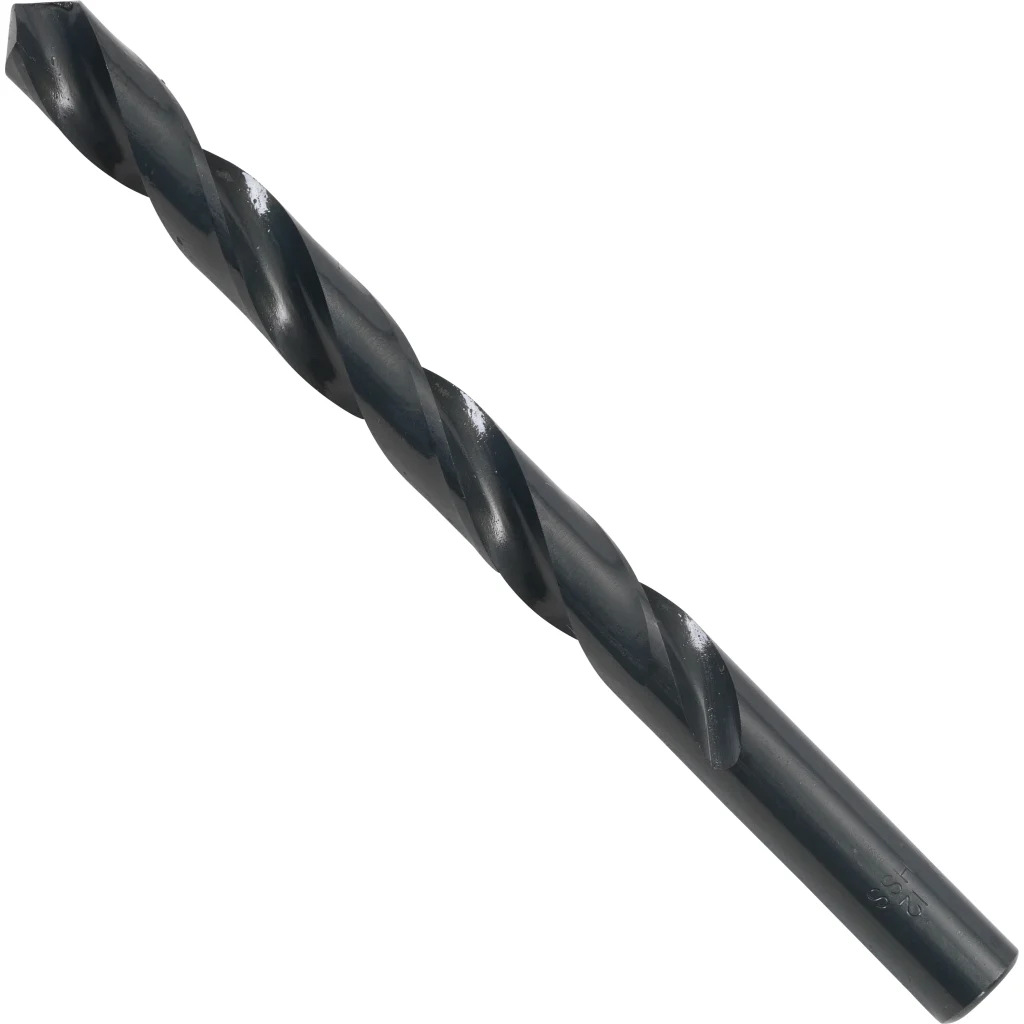
まずは普通にキリ穴をあけます。
キリ穴径は仕上がり径マイナス0.5mmのものを選びましょう。
例えばφ10に仕上げたいのであれば、φ9.5のドリルを使います。
取りしろはなんで0.5?
0.5mm小さいドリルを使うのには理由があります。次の工程でエンドミルを通すのですが、その際に取り代が大きすぎると切粉が多く出るため、切粉で穴内部がむしれてしまい、ガバガバの大きい穴になってしまう可能性があります。
かといって取り代が小さすぎると、ドリルの研ぎ具合で穴径が拡大してしまったときや、穴曲がりが起こったときに仕上げきることができず、リーマを通してもキリ穴の面が残ってしまう可能性があります。
取り代のバランスが最も良いのが約0.5mmなんです。
エンドミルを通す
キリで下穴をあけたら、次にエンドミルを通します。
エンドミルを通す目的は以下の2つです。
- 穴曲がりを修正するため
- 仕上げしろを減らすため
リーマは下穴になじみながら進入していくため、下穴が曲がっていると、リーマ穴も曲がってしまいます。キリ穴はどうしてもわずかに曲がりながら切り込むため、その曲がりをエンドミルで修正します。
そして、リーマのトラブルで最も多いのが「切粉」によるものです。切粉が排出しきれないと、切粉が穴を削ってしまい、リーマ穴がガバガバに大きくなってしまいます。エンドミルを通す理由には、そういったトラブルを防ぐために仕上げしろを減らし、切粉の出る量を極力減らす目的もあります。
エンドミルを通す際の切削条件
ハイスエンドミルを使った場合の切削条件を記載しておきます。
切削条件は、切削速度からいちいち計算しても良いですが、
鋼材でφ10以下であれば1000rpm、ステンレスであれば600rpm、アルミであれば1600rpmで統一してしまっても良いです。
私はだいたいそのように加工しています。
φ5以下など、さらに細いエンドミルを使う際に速く加工したい場合、1500rpmなどに上げて加工しても大丈夫です。
逆にφ10より大きいエンドミルであれば、径が大きくなるに従って回転数を下げてやりましょう。
送り速度はf0.1mm/revくらいが丁度良いと思います。つまり1000rpmだとF100mm/minということです。
ロングのエンドミルを使ってこの切削条件でびびりが発生する場合、送り速度Fと回転数を同じ割合で落としてやると良いです。
エンドミルを通す際のポイント
エンドミルを通す際にも意外とトラブルは多いです。特に止まり穴で注意しておかなければなりません。
エンドミルを通す際に切粉が悪さをしてしまい、エンドミルを通した時点で仕上がり寸法より大きくなってしまうことがあります。
こういったトラブルを防ぐためには、いくつかのコツがあります。
ロング、2枚刃のエンドミルを使用する
エンドミルを通す際のトラブルは切粉によるものがほとんどです。それを解決するために、切粉の逃げ場、チップポケットが大きいエンドミルを選ぶことをおすすめします。
具体的には2枚刃のエンドミルです。刃数が少ない分4枚刃よりチップポケットが大きくなります。
そして、エンドミルは有効長の全てを通すと切粉の逃げ場がなくなってしまいますので、有効長の4分の3くらいまででとどめておくと良いです。
とはいえ通常のハイスエンドミルは2L/Dの長さしかなく、それ以上の深さのリーマ穴をあけたい場合も多いです。
そんなときに活躍するのがロングのエンドミル。有効長が長いので、深くまで切り込みながら切粉を逃がすことができます。
私もそうしていますが、2枚刃でロングのエンドミルをリーマ用として、よく使う径の分を数本分けて管理しておくのがおすすめです。
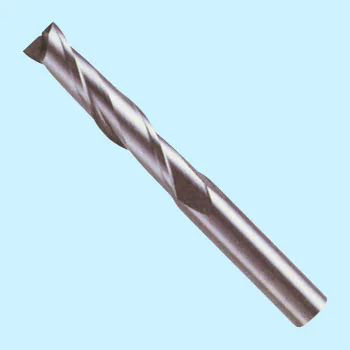
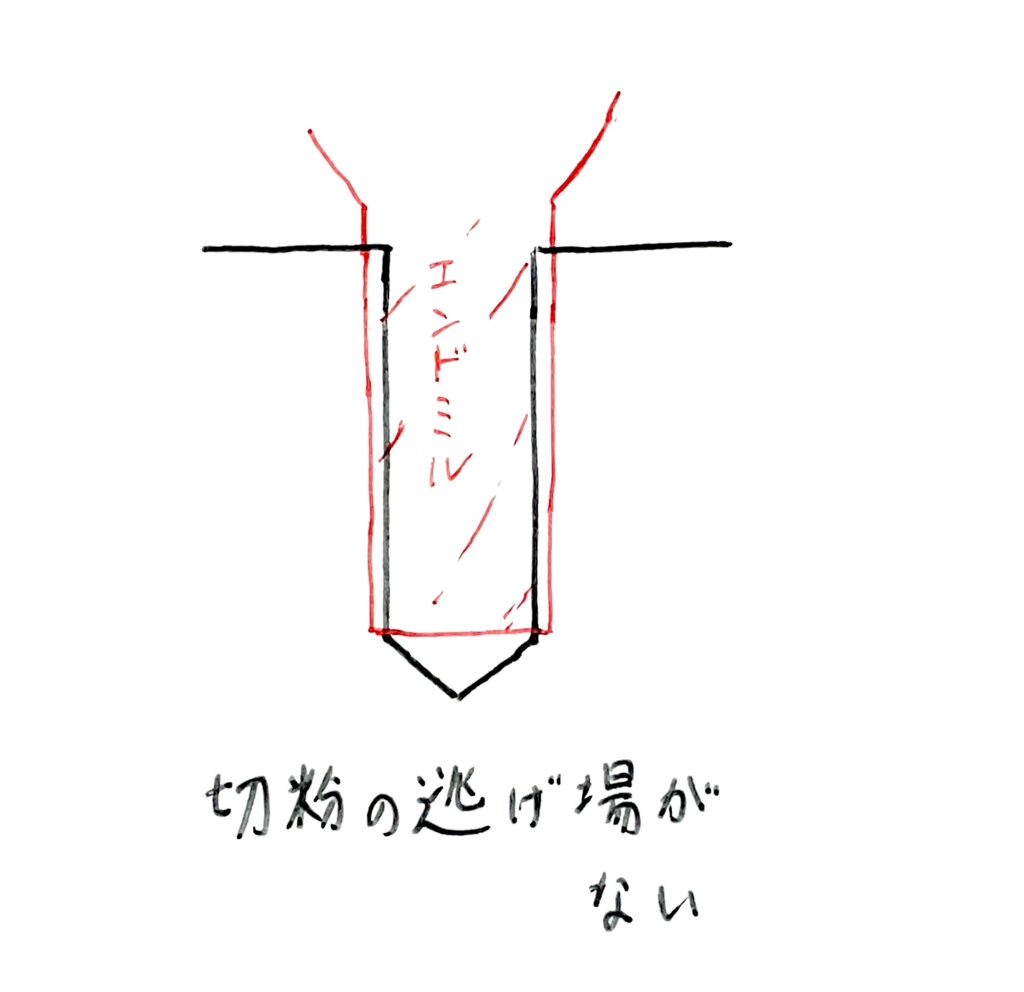
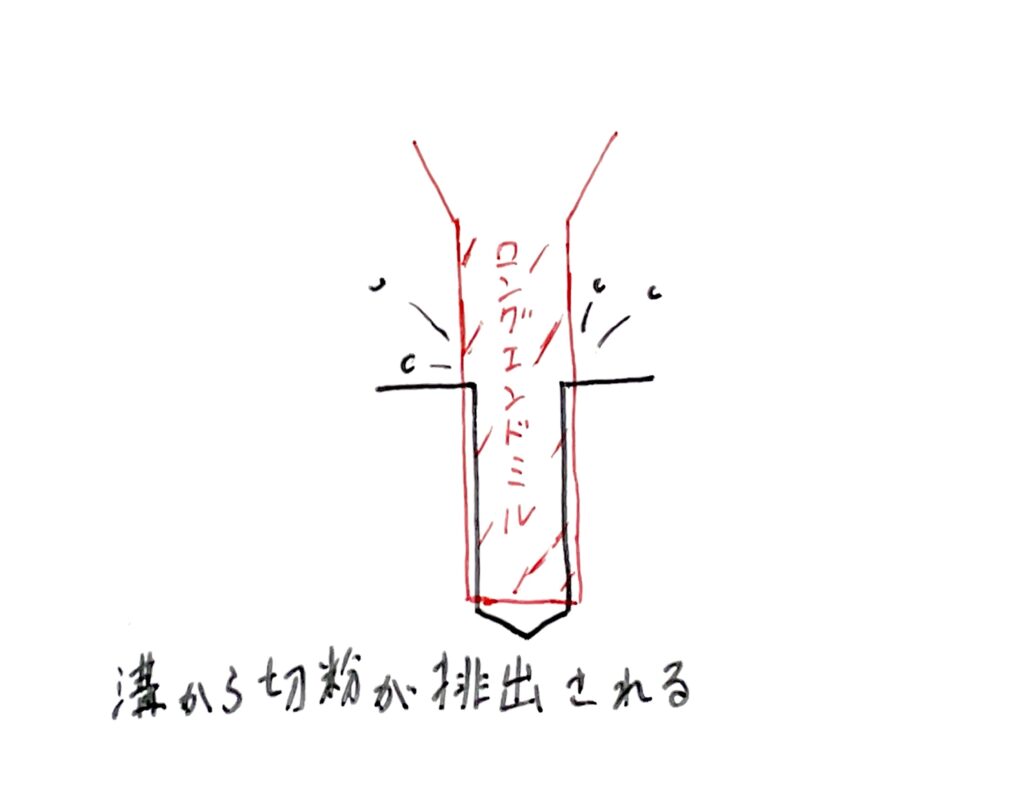
エンドミルの刃先の状態を確認する
エンドミルを通す際は、先端の刃で削っていくことになります。
そのため、先端が刃こぼれした状態ではエンドミルが踊ってしまったり、切粉の出かたが悪くなりやすくなり、穴径拡大の要因になります。
加工前にエンドミルの刃先が悪くない状態であることを確認しておきましょう。
G83[深穴あけサイクル]を活用する
切粉を効率的に排出するため、エンドミルを通すプログラムはG83[深穴あけサイクル]を活用することをおすすめします。
G83は、1ステップ進むごとにR点(工程開始点)まで戻るプログラムです。
通常の穴あけでしたらG73を使う場合が多いですが、引き抜くごとに切粉を除去できるG83の方が切粉のトラブルが起こりにくいです。
ステップは0.5mmごとに入れておくとより安心できます。
私は少量多品種加工の町工場で勤務していますのでサイクルタイムが長くなってもほぼ影響はありませんが、個数や穴数が多い場合は様子を見ながら条件を攻めることもできます。
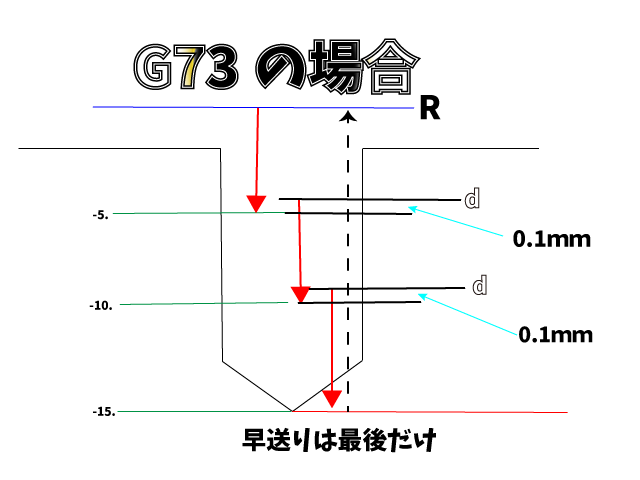
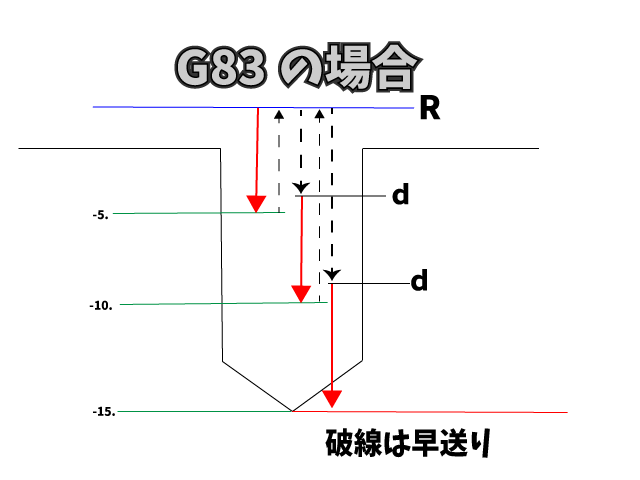
アルミの加工では特に注意
アルミではほんのわずかな切粉のつまりで穴径が拡大し、公差を外してしまいます。
アルミで失敗できないワークの場合は特に慎重に切り込みましょう。
クーラントをしっかりと供給し、潤滑しつつ切粉を飛ばすこともかなり重要です。
底づき穴は、最後はゆっくり加工する
底づき穴にエンドミルを通すのは、通常よりリスクが大きいことを手順の項の最後にご説明しました。
下図に掲載の通り、下穴(ドリル穴)の先端部の全てを有効長より奥に入れられている状態(下図の○)が、エンドミルを通す場合の理想の状態です。下図△や×の状態ではエンドミルで底面を削らなくてはいけないため、”起動・停止ボタン”を交互に連打して慎重に加工しないと切粉によって穴径が拡大してしまうことが多いです。
先述の通り、私の場合は通常であれば下穴は有効長+2mmであけ、エンドミルを有効長+0.6mm、リーマを+0.5mmで加工するようにしています。(径が大きくなれば合わせて下穴深さを深くしますが、基本はこの深さで加工しています)
下部に図をもう一度掲載しておきますね。
繰り返しになりますが、エンドミルやリーマを通す際に特に注意が必要なのが底づき穴です。
安定した加工のため、ドリル先端部は径の最低3分の2くらいが残るようにしておきたいところです。言い換えると底の平らな部分が穴径の3分の1以下くらいです。(最低でも下図△)
こういった底づき穴加工(下図の△のような底形状の加工)を行うときに、ドリル先端部の残った部分をエンドミルで削る必要がありますよね。エンドミルを通す際は、その残った部分を削る箇所だけで大丈夫ですので、送り速度を半分程度までおとし、さらにマシニングセンタの起動停止ボタンを交互に連打することで細かく止めて切粉を切りながら送ったほうが良いです。
これをやっておかないと、切粉が悪さをして穴径が大きくなり公差を外してしまうリスクが高くなってしまいます。
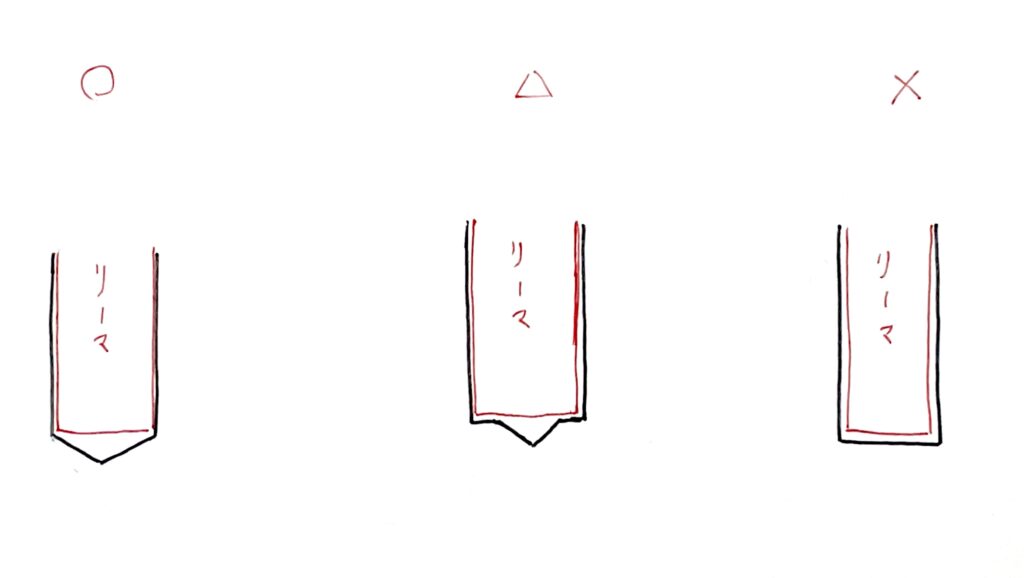
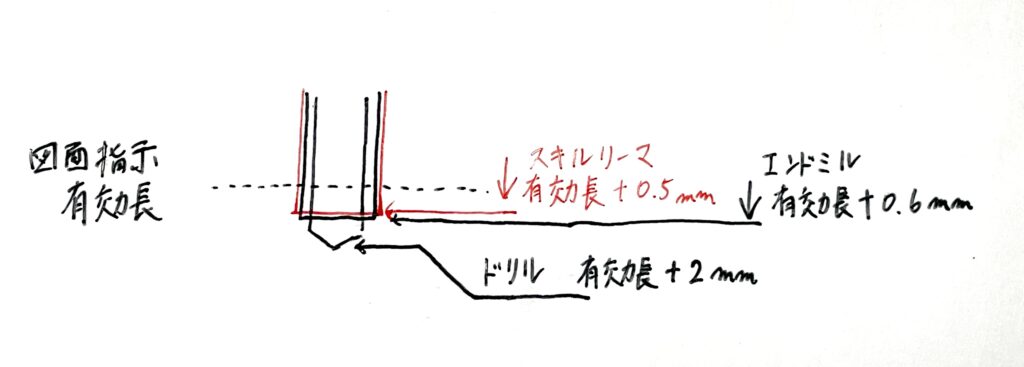
リーマを通す
エンドミルを通したら、いよいよリーマを通していきます。
リーマを通す際の切削条件は?
リーマを通す際の切削条件は、切削速度を計算するのも良いですが、φ12以下のリーマでしたら以下の通りでOKです。
使用するリーマは、ハイスのブローチリーマ、もしくはスキルリーマです。切削条件はどちらも共通で大丈夫です。
・回転数 200rpm
・送り速度F 40mm/min
φ12を超える大きいリーマの場合は合わせて回転数と送りを落とすようにしましょう。
逆にアルミでは回転数と送り速度を同じ比率で2倍、送りを4倍くらいに上げてやっても良いです。
超硬リーマの場合はハイスと比べて大きく切削速度が上がり、回転数が低すぎると逆に刃物を傷めますので注意しましょう。その分高速での加工が可能です。
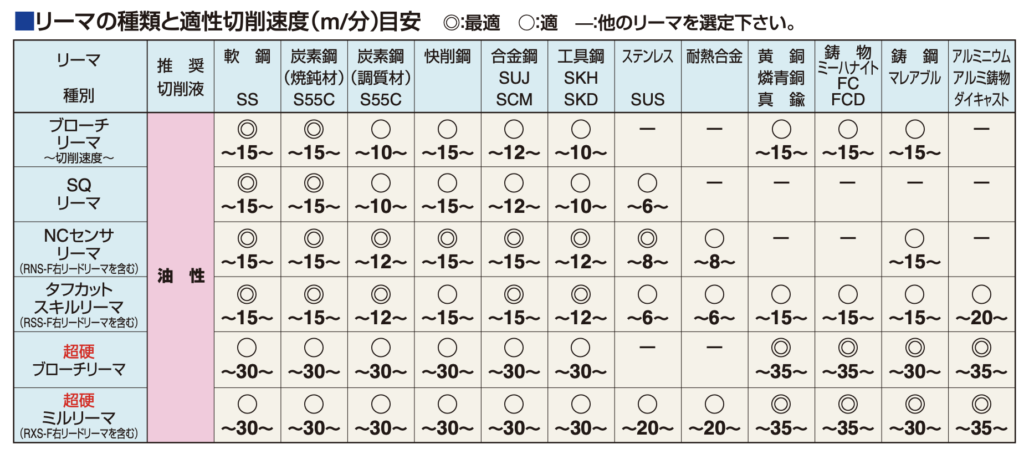
ブローチとスキルカットで条件は変える必要はない
上記の条件であれば、径にもよりますが低めの条件ですので、スキルカットで止まり穴を加工する場合でも、ブローチで通し穴を加工する場合でも同じ切削条件で大丈夫です。
多くの穴数を加工したいときなどサイクルタイムを可能な限り短縮する必要がある場合は、通し穴であればカタログ値の切削条件まで上げられます。ですが、止まり穴も同じ条件まで上げてしまうと切粉トラブルの可能性が増えますので、注意しながら条件を上げるようにしましょう。
リーマのプログラムはG81[スポットドリリング]を使う
リーマのプログラムはG81[スポットドリリング]を使います。ノンステップの穴あけ加工プログラムです。
ステップがあるとステップの跡が穴表面に残る場合がありますし、サイクルタイムも伸びますので、深穴を除いてノンステップで問題ありません。
といっても、取り代を0.1以上つけており、φ5以下の小径リーマで加工深さが3D以上の場合は切粉を除去するため引き抜きのステップを入れたほうが良いです。その場合はG83【深穴あけサイクル】を使いましょう。
切削油はしっかりかける
潤滑性を高める目的、そして切粉を飛ばす意味でも、リーマ加工時は切削油をしっかりかけるようにしましょう。
切削油は水溶性切削油でも問題ありませんが、ベストなのは油性の切削油です。
数物などで連続加工が必要な場合は油性の切削油をおすすめしたいところですが、火事の危険性がありますので、“油性と同等の切削性を持ちつつ燃えない”インプラス社のBLEDIOのような切削油をおすすめします。

インプラス社公式HP カタログはこちら→http://inplus.co.jp/catalog/
ボール盤でのリーマ作業は便利!!
ボール盤でリーマ加工は割とよく行う作業です。
作業方法は簡単で、ワークをバイスに掴み、油を塗って最低回転でゆっくりリーマを通すだけです。(エンドミルを通すまではあらかじめマシニングセンタ等で行っておく必要があります。)
タッピング等と同様に、バイスはボール盤のテーブルに固定はしません。
「マシニングセンタ等でリーマ加工を行ったものの、仕上がり径が小さくなって栓ゲージが入らない」といったときも、ボール盤でもう一度リーマを通せば入るようになることが多いです。
アルミだとむしれて穴径が大きくなることもありますが、ボール盤であれば問題なく加工できたりします。
位置決め精度もマシニングセンタやフライス盤で同径のエンドミルを通した後であれば問題ありません。
また、リーマ穴に対する横穴のバリをとるため、機械ではリーマ穴部をエンドミルを通すまでで終わらせておいて、横穴を加工してからボール盤でリーマだけ通すということもあります。
大変便利なので、ぜひ活用してみてください!
クーラントを流せないこともあり、機械で通すより仕上げ面が荒くなる傾向にあるのでご注意を。
リーマ加工のよくあるトラブルとその解決策
穴径、寸法が拡大する
本記事で書いた手順通りに作業を行っても穴径が拡大して公差が外れてしまう場合、まずはエンドミル加工直後に穴径を測定し、エンドミル加工で穴径が大きくなっているのか、リーマ加工でそうなっているのかを確認、原因を特定しましょう。
エンドミルが原因で穴径が大きくなる場合
まず、エンドミル工程が原因とわかった場合の解決方法です。
エンドミルを通す作業は、φ10の穴に対してφ9.98程度のエンドミルを通すため、少しの原因でわずかに穴径が拡大しただけでも不良になってしまいます。
エンドミルが原因で穴径が大きくなる場合、考えられる要因は以下のとおりです。
- エンドミルの刃先の状態が悪い
- 切粉がうまく排出できていない
- エンドミルの振れ
エンドミルの刃先の状態が悪い場合は穴径が拡大してしまいます。エンドミルの交換もしくは刃先の再研磨を行って解決しましょう。
切粉の排出が上手くいかない場合は、G83の深穴あけサイクルで切り込み0.5を試してみましょう。クーラントをなるべく高圧で切削点にあててやるのも切粉排出のポイントです。
そして最後の原因”エンドミルの振れ”はあまりありませんが、主軸の衝突があった場合や、ミーリングチャックの精度、工具クランプ時の切粉噛み込みなどのミスによってエンドミルが振れていると穴径が拡大してしまいます。振れを確認の上で使用しましょう。
リーマが原因で穴径が大きくなる場合
エンドミルを通した際は問題なかった場合、リーマが原因になります。
考えられる要因は以下のとおりです。
取り代が大きすぎるため、切粉が出ている
穴径が、0.05mmなどどうしようもないほど拡大してしまう場合は大抵切粉が原因です。
切粉のトラブルは特にスキルリーマを使った止まり穴で起こりやすいです。
まずは下穴部に底あたりしていないか確認してみましょう。底あたりしていなくても、下穴が完全にフラットだと切粉の逃げ場がなくなり、穴径が拡大しやすいです。
また、貫通穴でエンドミルを穴奥まで通せなかった場合など、取り代が大きい場合はその分切粉がでるためむしれやすいです。
ロングのエンドミルを使うなどして穴の奥までエンドミルを通し、切粉を少なくすることで解決できることが多いです。
リーマ刃先の状態が悪い
特にスキルリーマでは、リーマの刃先に摩耗やチッピングがあると穴径にも影響します。
刃先が傷んでいると加工表面も荒くなってしまいます。
工具を取り付ける前に刃先の状態を確認してから使用するようにしましょう。
取り代が小さすぎる
通常、取り代は0.02mmくらいで十分ですが、穴径が拡大して上手く行かない場合は0.2mmほどの取り代でリーマを加工してみましょう。
実際のところ、メーカーの推奨値も0.2mmほどが多いです。
面取りを行っておらず、食いつき時にリーマが踊る
面取りを行わずにリーマを通した場合、入り口でリーマが踊ってしまい、入り口の方だけわずかに穴径が拡大してしまうことがあります。
面取りを行っておくことで解決できる場合があります。
リーマの振れ
通常、リーマはしなるため、ドリルチャックで掴んでも問題ありません。
ですが、振れが穴径の拡大に与える影響はあると思いますので、振れを抑えて穴系の拡大を防ぎたい場合はミーリングチャックを使ったほうが良いです。
【アルミ】切削条件が適正でない
アルミのリーマ加工では、通常の条件だと穴径が少しだけ大きくなってしまうことがあります。
そういった場合は回転数に対して送りを上げることで、わずかに穴径が小さくなります。体感的には5μmくらいでしょうか。
送りを2倍にしてみるなど、少々大胆に送りを上げてみましょう。
穴径、寸法が小さくなる
リーマ加工を行っていると、逆に寸法が小さくなってしまうこともあります。
その原因は以下が考えられます。
リーマの摩耗
穴径が小さくなる一番の原因はリーマの摩耗です。
まずはリーマを新品のものに交換してみてうまくいくようになるか試してみましょう。
切削条件が適切でない
リーマ穴の寸法は、回転数に対して送りが高いと小さめに、送りが低いと大きめになる傾向があります。
穴径が小さくなる場合、送りを落としてみると改善される可能性があります!
それでもまだ小さい場合は、ボール盤を使ってリーマを通しましょう。丁度よいくらいに穴径が大きくなってくれることが多いです。
同径のエンドミルを通していれば、ボール盤でも問題ない位置決め精度でリーマを通すことができます。
表面粗さ、面粗度が粗い
リーマ穴表面の粗さが気になる場合、以下のような原因があります。
- リーマ刃先の傷み
- 削る材質や、油の潤滑性の低さによるむしれ
- 下穴に曲がりや拡大があり、下穴の面が見えている
- 切削条件が適正でない
- 仕上げしろが大きすぎる
このあたりの原因が考えられます。
表面が荒くなる一番多い原因は、リーマの刃先が傷んでいることです。
まずはリーマを交換して試してみましょう。
その際、刃物の形状がストレートのハンドリーマより、ブローチリーマやスキルリーマのようなねじれているもののほうがきれいに仕上がりやすいです。
他の原因としては、切粉によるキズによって荒くなってしまうことも多いです。
引き抜く際の螺旋状のカッターマークが気になる場合、主軸の回転を止めてから引き抜いたほうが目立ちにくいです。
加工完了したら栓ゲージ等で寸法測定
加工が完了したら、寸法の測定を行います。
寸法測定には栓ゲージを最もよく使います。私の勤務先をはじめ、ほとんど工場ではリーマ穴の多くがH7公差だからです。
中途半端な径の場合、栓ゲージを旋盤で製作したり、キーエンス製の画像測定機やハンディプローブ三次元測定機を使ったりして対応しています。
位置決め精度は、ピンゲージを入れて測定しても良いですが、キーエンスの測定器を使って測ることがほとんどです。
まとめ
少々長くなりましたので、簡単に内容をまとめておきます!
どのリーマを使う??
私の勤務先では基本的に貫通穴にブローチリーマ、止まり穴にスキルリーマを使っています。
リーマ加工の手順
- 芯もみ
- キリ穴開け
- エンドミルを通す
- リーマを通す
手順の通り、まずは芯もみ、キリ穴あけを行います。
注意が必要なのはエンドミルを通す作業からです!
エンドミルを通す際のポイント
・ロング、2枚刃のエンドミルを使用する
・エンドミルの刃先の状態を確認する
・G83[深穴あけサイクル]を活用する
・アルミの加工では特に注意―特にアルミは、クーラントをあてるなど、切粉の排出にしっかり注意を払って加工しましょう。
・底づき穴(止まり穴)は、最後はゆっくり加工する
リーマを通す際の切削条件
切削条件は、基本的にS200rpmのF40mm/minで加工しています!
エンドミルを通す際の切削条件についても本文で記載しています。
リーマを通す際のポイント
・ブローチとスキルカットで条件は変える必要はない
・リーマのプログラムはG81[スポットドリリング]を使う
・切削油はしっかりかける
リーマ加工のよくあるトラブルとその解決策
・エンドミルが原因で穴径が大きくなる場合―エンドミルの刃先の状態、エンドミルの振れ、切粉の排出を確認しましょう!
・リーマが原因で穴径が大きくなる場合―取り代の大きさ、リーマ刃先の状態、面取り、リーマの振れを確認しましょう!アルミの場合、切削条件(Fが低すぎる)も原因になることがあります。
・穴径、寸法が小さくなる場合―リーマの摩耗、切削条件(Fが高すぎる)を確認しましょう。
表面粗さ、面粗度が粗い―リーマ刃先の傷み、材質にあった加工条件、油の潤滑性、下穴の曲がりや拡大、仕上げしろの大きさを確認しましょう。
以上です!
いかがでしたでしょうか?
リーマは精度が必要な公差穴を加工する場合がほとんどですので、トラブルがあったら製品がオシャカになってしまい、再製作になります。(気休め程度に修正する方法もありますが・・・。)
私もリーマ加工が原因で製品をオシャカしてきた経験が何度かありますが、本記事に書いたコツさえ押さえればトラブルはかなり減ります。
ぜひ本記事を参考にしていただいた上でリーマ加工にトライしてみてください(^^)
コメント
すばらしい説明ですね