
ライター:SAKAHOMO
平面研削におけるクランプ
研削盤を使用して研削作業を行う場合、テーブルと呼ばれる台にワークをセットしテーブルと砥石頭が動くことによりワークを研削します。
このテーブル上にワークを固定する作業がクランプです。
研削作業者の間ではワークセッティングと呼ぶことが多いのではないでしょうか。
たた固定するだけといってしまえばそうなのですが、その割に奥が深い作業で、上手くやらないと精度不良を引き起こしてしまいます。
ただ単にしっかりと固定するのではなく、いかにワークのありのままの形状で、尚且つワークがずれる事の無いように安全にセッティングするかが重要になります。
クランプの重要性
研削において精度が変化する要因は大きく分けて2つあります。
1つは研削熱の影響です。研削熱による温度変化が精度に大きな影響を与えてしまいます。
もう一つの要素が今回のテーマに繋がるワークの弾性力です。この弾性力を抑えるためにクランプ方法はとても大切になるのです。
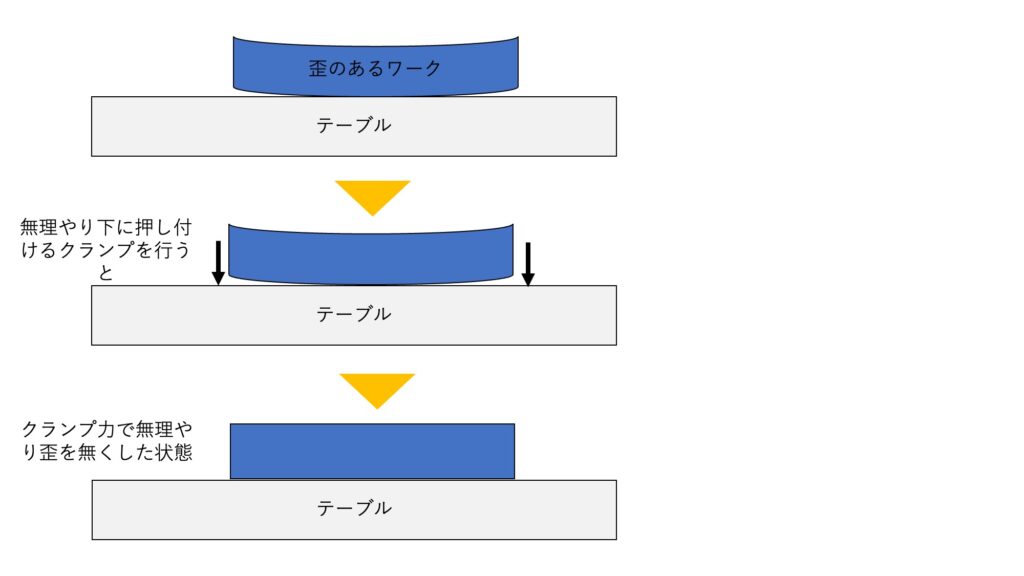
上の図のようにワークには大なり小なり歪や反りがその製作過程で発生してしまいます。
この歪や反りを無視してがちがちにクランプしてしまうと、研削の後ワーク単体で精度を測定すると精度不良になるケースが多発してしまいます。
クランプによる精度不良を把握するためには精度に関して把握しなければなりません。
平行度と平面度
少し回りみちになりますが、まずは平行度と平面度の違いを解説しておきますね。
大丈夫という方は次の見出しまで飛ばしてください!
平行度とは?
まずは平行度の解説です。
平行度とは読んで字のごとく平行の寸法測定となります。例えば下の図のようなワークを削った場合
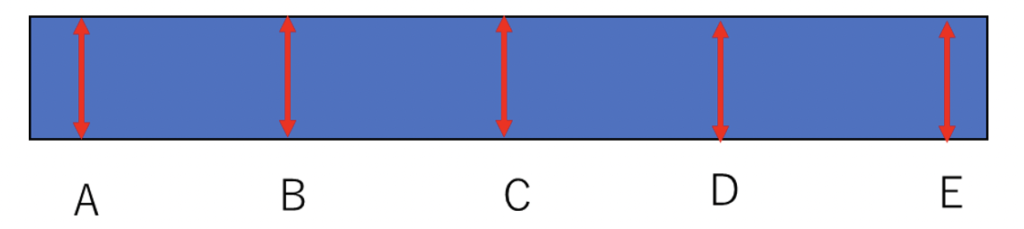
AからEの厚みを測定し、最小値と最大値の差が平行度となります。
例えば最少がAで5.513mmで最大がDで5.520mmであればこのワークの平行度は5.520―5.513=0.007となります。
平行度は機械精度特にテーブル上面の平行度がしっかりとしていれば、比較的簡単に出すことが出来ます。
平面度とは?
では平面度ではどうでしょう。
平面度は上面の凹凸の差を測定しその最大値と最小値の差を求めます。
定盤上にワークをのせ、ダイヤルで高さの差を測定していきます。
下の図のようにAからEまでをダイヤルで測定し、差が無ければ平面度は0となります。
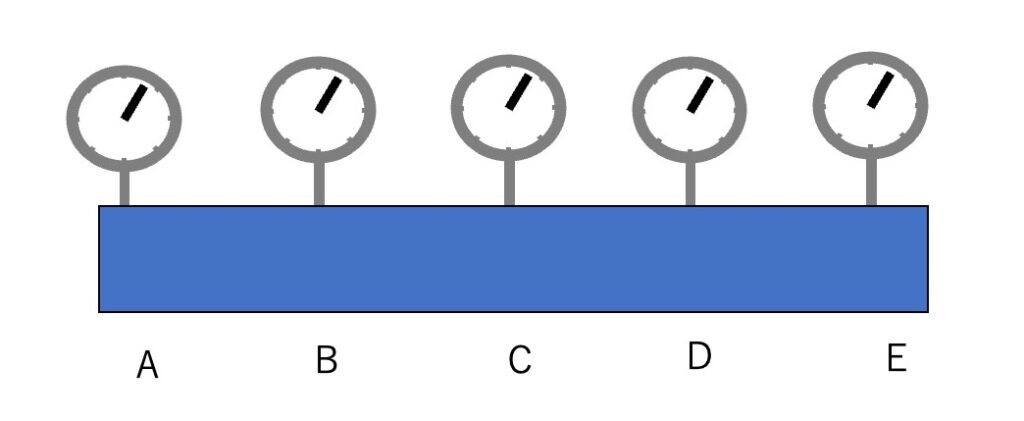
しかしながら下の図のようであればAとEの場所はダイヤルの数値が他の場所に比べプラス方向になると思います。
この様な状態だと平面度は悪化してしまいます。もちろんワークの縦幅・横幅が広くなればなるほど測定点が増加するので平面度をしっかりと出すことは難しくなります。

平行度より平面度の精度を出すのが難しい
この図を見て気づいた方がいるかもしれませんが、平面度が悪い=平行度が悪いとはなりません。
平行度が良くても平面度が悪いケースが多く発生します。
なぜ平行度は良いのに平面度が悪いケースが発生するのでしょうか。
様々な原因がありますが、その一つに今回のテーマであるクランプ方法があります。
クランプというと押し付けるというイメージがあるかもしれませんが、押し付けるイメージでクランプしてしまうとワーク素材の自然な状態を壊してしまう事になり、その結果クランプ力を解放したときにワークが元の形状に戻る力が発生し、特に平面度が悪化してしまいます。
研削におけるクランプはワークが飛散しないように安全かつワークの自然な形状を極力変化させない優しい固定が重要になります。
マグネットチャック仕様の平面研削盤の場合
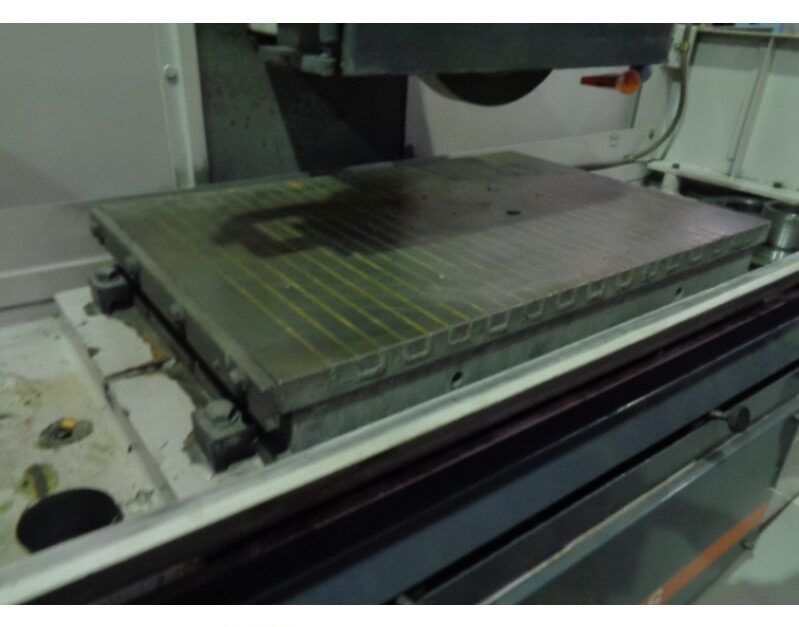
比較的小型の研削盤で使用される電磁チャック
チャック仕様の研削盤は比較的小型の研削盤が多いと思います(勿論大型機でもチャック仕様はあります)。
小型の研削盤では、比較的小さなワークを研削するケースがほとんどです。
チャックの場合、クランプの作業は比較的簡単です。
チャックの磁力がクランプ力となるので、基本的にワークをチャック上にのせ、磁力をONすれば完了です。
チャック上面の平行度が維持されていれば、この状態で裏表研削すれば平行度は問題なく出るでしょう。
薄いワークの研削は反りとの戦い
小型研削盤では比較的薄いワークの研削が多いですよね。
ブロックのような形状のものであれば簡単に研削できますが、薄物の研削は注意が必要です。
ライナーのようなモノとモノの間に挟むような使用方法のワークであれば平行度がしっかりと出て指定寸法に仕上がっていれば問題ありません。
しかしながら例えば楔のような摺動面に使用されるようなワークでは摺動面とのアタリが重要になり(アタリは最終的に人の手によるきさげ作業が行われます)、このあたりが悪いと修正作業に時間がかかってしまいます。
薄物の研削で厄介なのはワークの反りです。
元々、素材が作られ加工されたワークはそれまでの過程で必ず反りが発生します。
研削ではこの反りを可能な限り取り除き、自然な状態でいかに真っ直ぐな状態を作り出すかが重要です。
ですので平面度が抜群・反りがほとんどないワークに仕上げれる研削盤操作者が一流の操作者と言われるわけです。
この反りを取り除くためにクランプ方法が非常に重要になります。(研削熱による反りは今回は除く)
反ったワークをそのままチャックの磁力で固定すると、自然な状態ではなく無理やりチャックに引っ張られた状態になってしまいます。
その状態でワークを削ると平行度はしっかりと出ますが、チャック磁力を脱磁すると反りが戻ってしまい、反った形状は残ってしまいます。
平面度が要求されるワークではこの反りが残ると使い物になりません。
シムを使用したクランプ方法
では、このような反りを解決するためにはどのようにクランプすれば良いのでしょうか?
反りを残してクランプするために、チャックとワークの間に新聞紙などを挟んで研削する方法が有名かもしれません。
ですがより反りとなくすために、シムを使用した研削をお勧めします。
この方法を使うことで、チャック磁力によって引っ張られても反りが残っている状態を作ることが重要です。
中高・中低の確認
では、このシムを使ったクランプ方法の具体的なやり方を説明していきます。
まずワークをセットしたときに、チャック吸着側が中低か中高かを確認します。
チャック上面にワークをのせ、磁力オフのまま、ワークの端を軽く押してやります。この時反対側の端付近を視点にワークが動けば中低の状態です。逆にワークの中心を視点にワークが動けば中高の状態です。
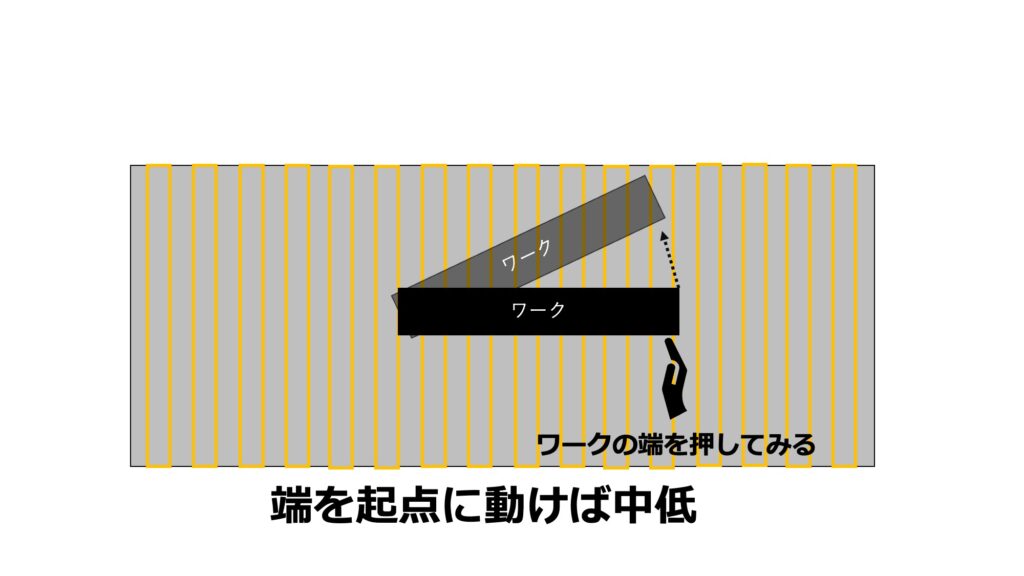
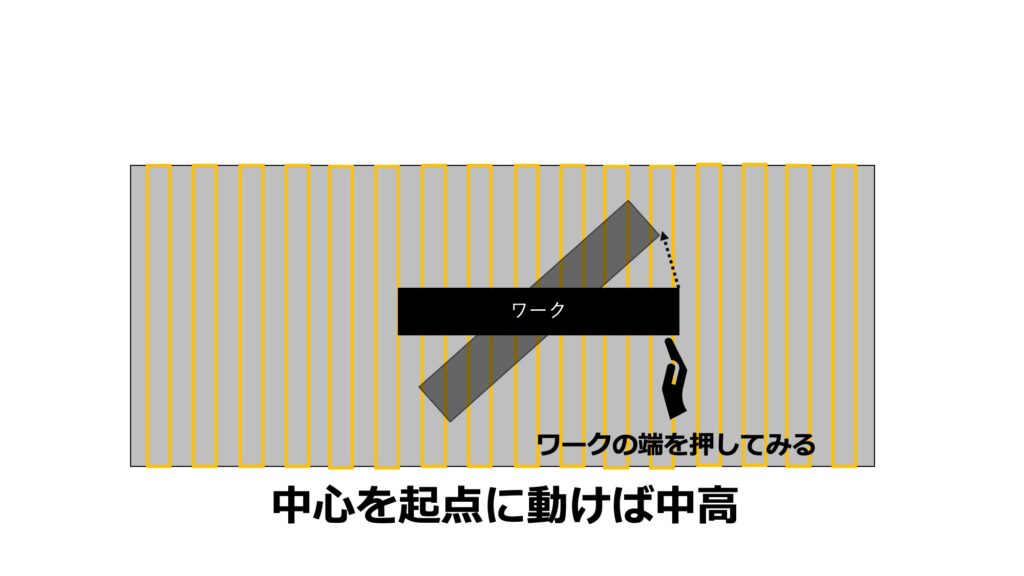
シムを差し込む際のポイント
では中高の状態を仮定して説明していきます。
チャック吸着側が中高ということは、自然な状態ではワークの中心がチャックに当たっていて両端は浮いている状態になります。
この浮いている部分にシムを入れていきます。
両端に同じ厚みのシムを入れていき、徐々に厚みを厚くしていくとある厚みで起点が外側に変わるはずです。
そして起点が両端に変わる厚みよりも少し薄いシム(10~20㎛)を再度両端に差し込むと、起点が両端より少し内側の2点になります。
この様な状態になってからチャックの磁力をONにします。
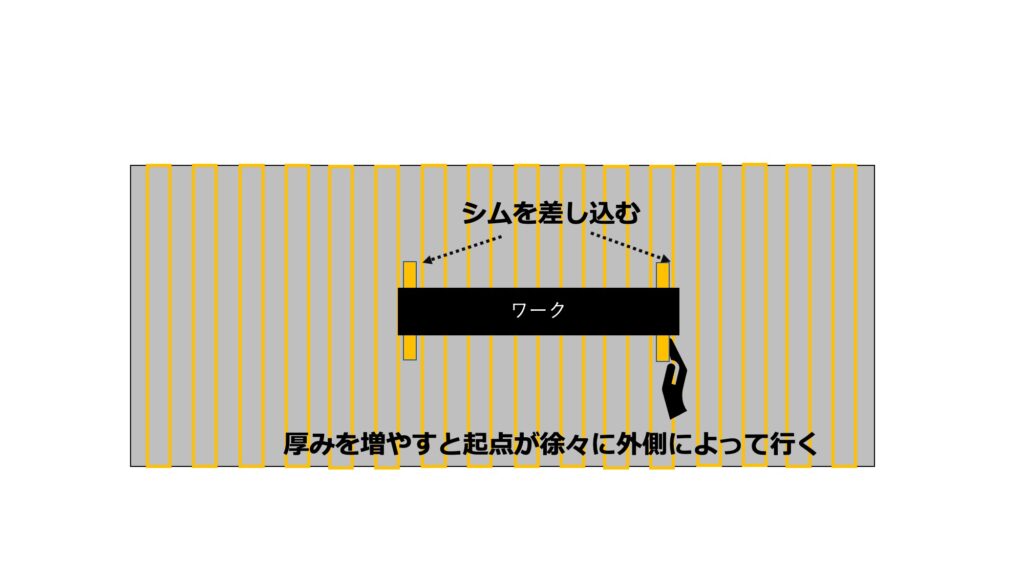
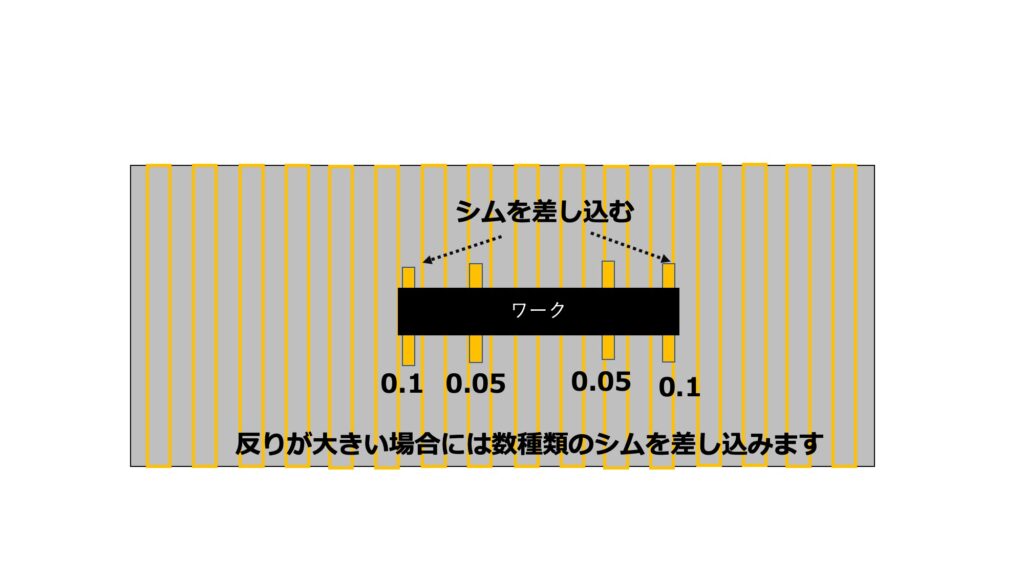
起点が両端からワーク全長の1/4くらいの位置で大丈夫です。
この状態でセットし研削を行うと反り通りに削れていくので、接地面が中高の場合は研削はワークの外側から研削されていきます。
全体の研削が完了したら、ワークを反転させ、再度接地面が中高か中低化を確認し、再度シムを差し込みセットします。
これを繰り返すと、徐々にセットするシムの厚みが薄く薄くなってきます。
この薄くなっていく過程が反りを取る過程となります。
最終的にシムを差し込まなくても、ワークを押したときの起点が両端からワーク全長の1/4くらいの2点になると思います。
この状態になると反りはほぼ取れているはずです。どのような厚みのシムをどの位置にどのくらい差し込むかが経験の差になってくるところです。
チャックを使用したクランプの注意点
よくチャック仕様の研削盤で正直台の上に載せて研削する場面も見ますが、これはワークの飛散の危険が高くお勧めしません。
また反りをとるためにチャック磁力を落としクランプ力を極力抑える方法もあります。
この方法では無理やりワークをチャックに吸着する事が防げるメリットがありますが、この時もワークが飛散しないようにワークの前後左右に必ずせらしをセットしておいてください。
チャックでの吸着は、上方向に引っ張っても中々取れませんが、横方向には意外と簡単に動きます。
一般的に上方向の吸着力に対して横方向の吸着力は1/10程度になると言われています。
一度ワークをチャックに吸着した際に試してほしいのですが、意外と横方向の力には弱いことを理解しておく必要があります。
T溝仕様の研削盤の場合
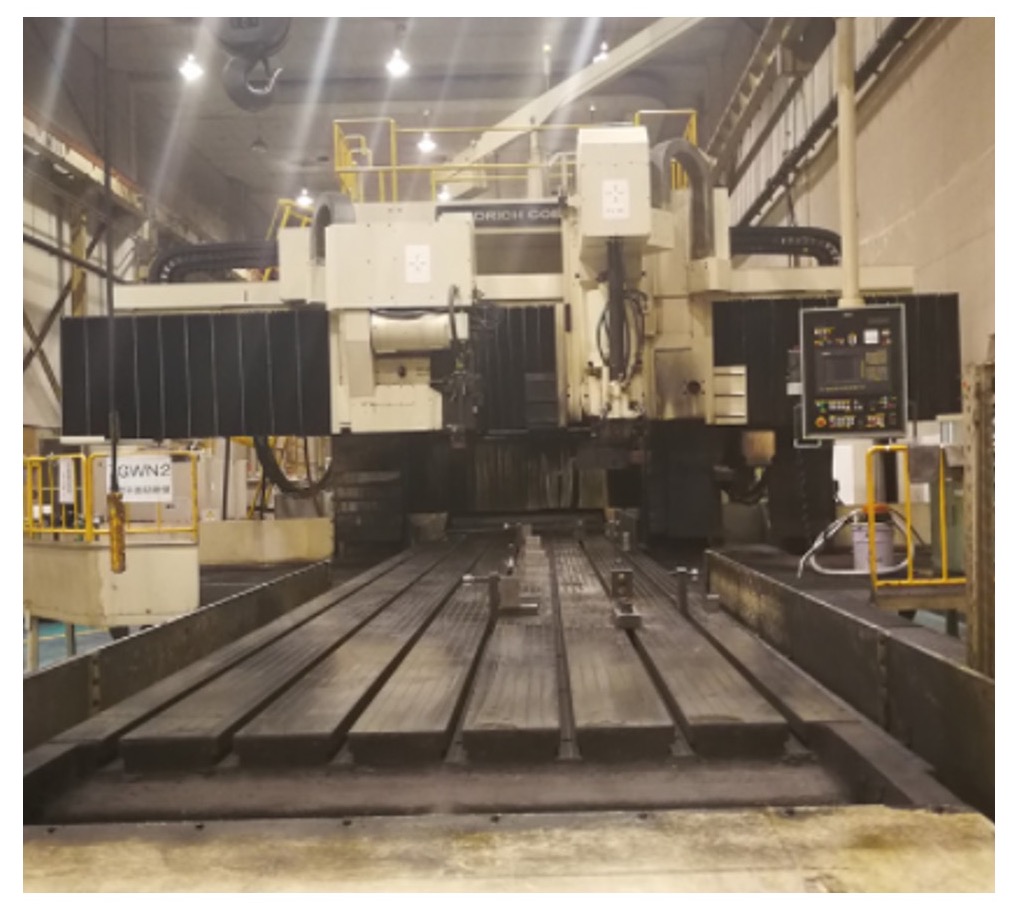
大型機に多く使用されるT溝タイプのテーブル
T溝仕様の研削盤は主に門型研削盤の大型タイプによく見られます。
テーブルにT溝が加工されていて、治具を使用しT溝ナットでワークをクランプします。
主に大型工作機械の鋳物をはじめとした大型ワークの研削に使われることが多く、薄物の小さなワークにはあまり使われないタイプです。
ワークは比較的大きく、重量も数百キロ~数トンに及ぶ大型ワークの研削になると思います。
T溝タイプでは多くのクランプ治具が必要
チャックに比べT溝仕様はクランプ作業が面倒になります。
基本的にテーブルにべた置きのセッティングは行われず、正直台やレベリングの上にセットするケースがほとんどです。
ですのでそのワークや求められる精度に応じたセッティング治具を用意する必要があります。
ワークセッティングの基本「3点受け」
基本的にワークはまず3点受けでセットします。
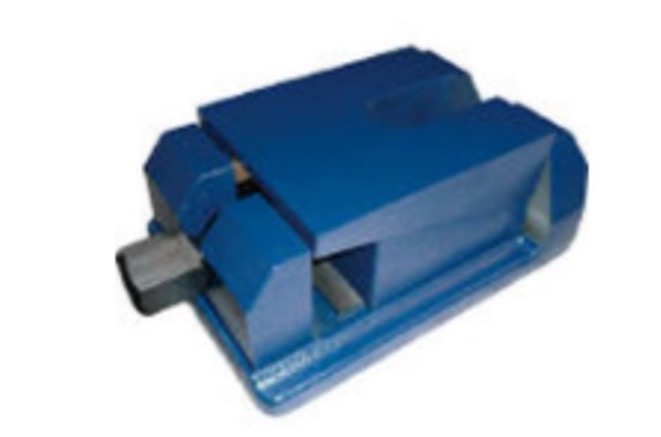
そこで使用するのが、画像のようなレベリングです。これを使用すると、ワーク全体の高さを揃え研削代を最小に抑えることが出来ます。
あるいはワーク下面の加工がしっかりとした精度で行われていれば、高さのそろった正直台でも問題ありません。
ただ、レベリングブロックでしっかりと基準となる4面の高さの差を記録することによって、一度ワークを研削盤から降ろし、再度研削の必要が出た時に基準値とすることができ、セットの再現が簡単に行えるメリットがあるのでケースバイケースで選択する必要があります。
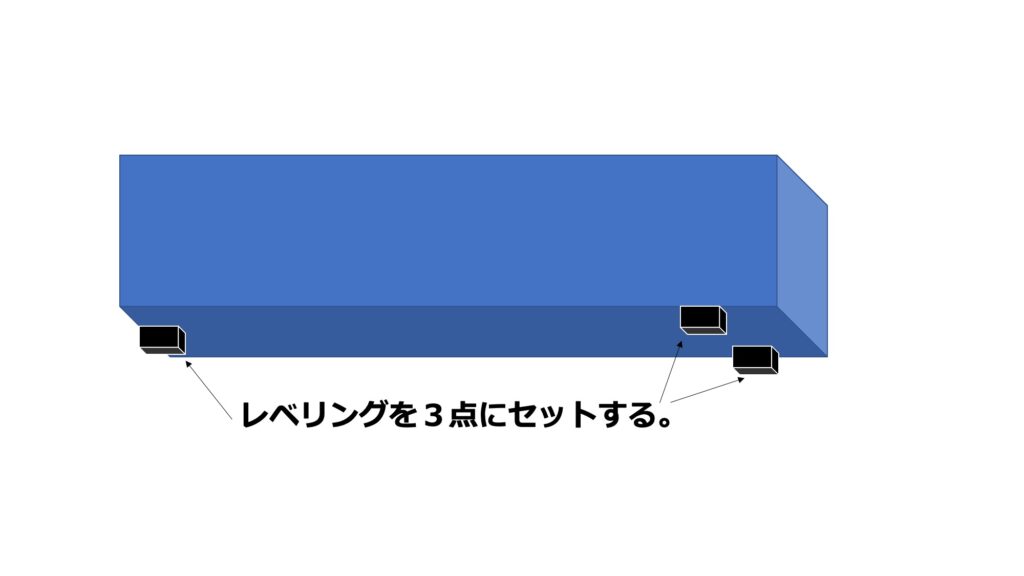
基本的に大型のワークには下面に組み立て時に受ける場所が加工されているので、受けるときも必ずその受ける場所にレベリングをセットしてください。
調整には必ずダイヤルで確認を
3点受けが終われば、レベリングにてワーク上面の左右・前後を機械砥石頭につけたダイヤルで測定し、両端(4隅)が0に近づくよう調整を行います。
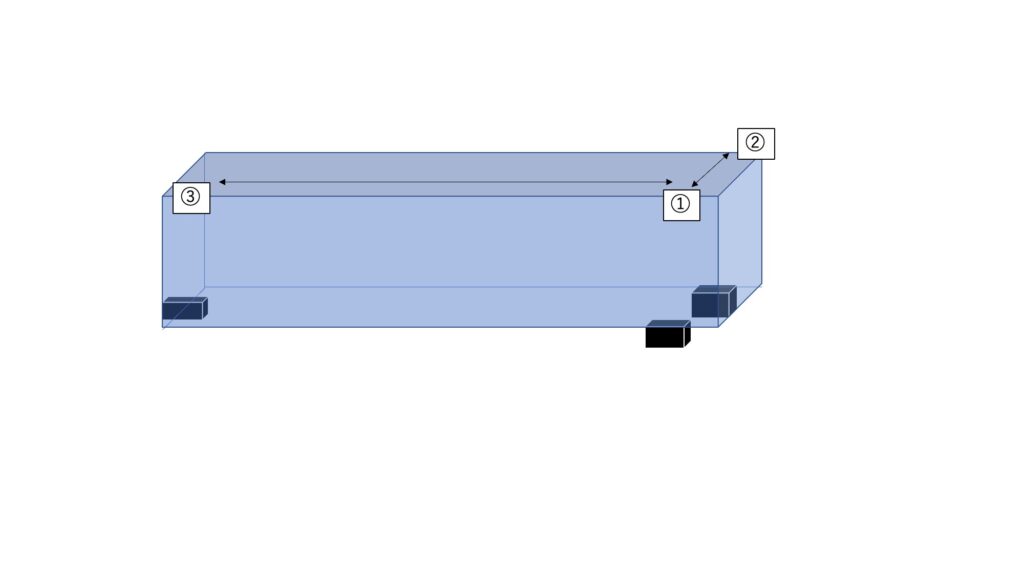
調整の手順を解説しますね。
まず、左右方向に2個レベリングをセットしている所の①にダイヤルを当て0にセットします。
次にダイヤルを②に移動させ、0になるようレベリングを調整します。
さらに③にダイヤルを移動させ③を0になるよう調整します。
何度か調整確認を行い、➀②③のダイヤル数値の差が小さくなればOKです。
この時、①と②はしっかりと調整できても③側の左右方向が悪い場合がありますが、これは元々のワークの精度となるので無理に直さないよう注意してください。
この作業が終われば、3点以外の受ける場所にレベリングをセットしていきます。
この時、レベリングを軽く効かせますが、必ず受ける位置にダイヤルを当て、効かす前とダイヤルの数値が変化しないよう注意してください。
あくまで3点受けで出した状態が自然な状態なので、他の部分でレベリングを効かす場合は、数値が変化しない事が鉄則です。
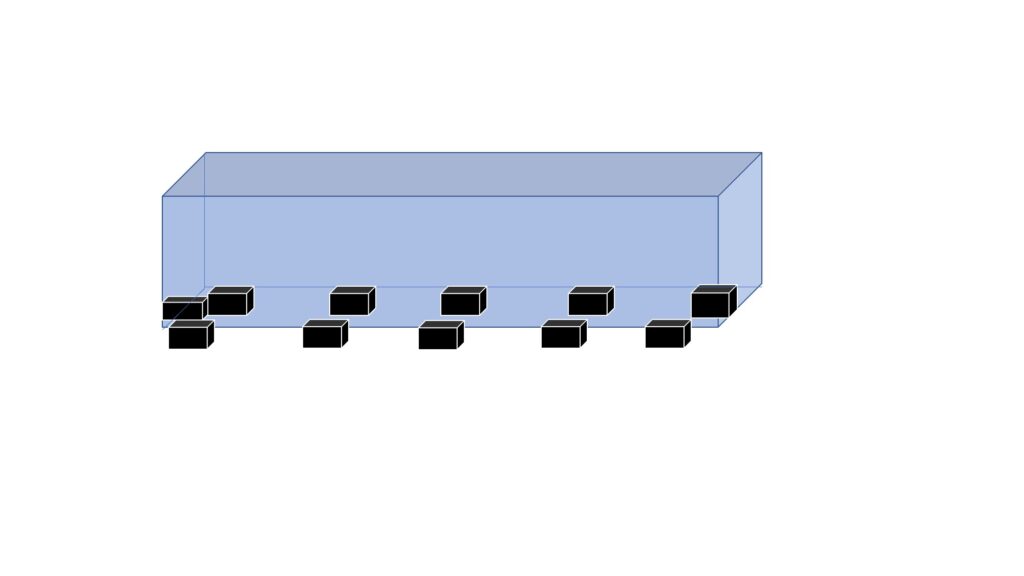
クランプは芯出し精度が変わらないよう優しく
この状態になったら、マツバ等を使用してレベリングで受けている部分のワークを軽くクランプします。
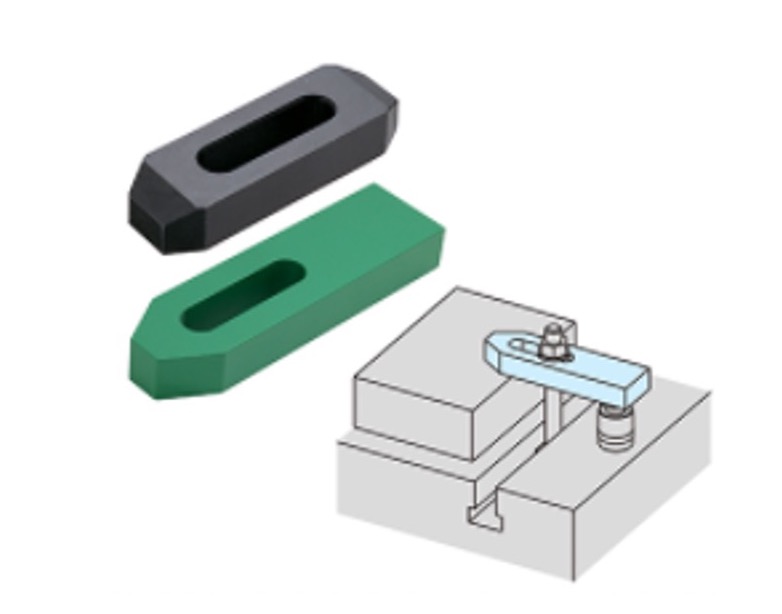
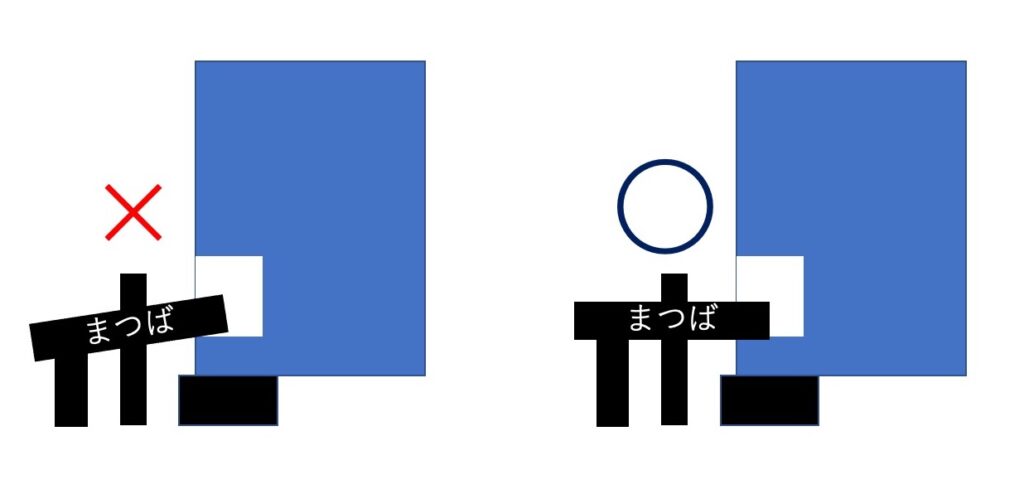
マツバは斜めにならないように注意してください。クランプ力が上手く伝わらず危険です。
この時もクランプする前に必ずダイヤルをセットしクランプして数値が大きく変わらないように慎重にクランプを行ってください。
その後、前後左右にせらしをセットすればクランプ完了です。
研削盤におけるクランプでは3点受けでレベルを出した後、他のレベリングを効かしたり、せらしをセットする時必ずワークにダイヤルを当て、効かす前と後で数値が変わらないよう慎重に作業を行う事が重要です。
無理に形状が変わるほどクランプすると、いざ製品として使用しようとした時、精度不良となりますので注意してください。
ワークのダレに関して
おおきなワークをクランプした時、そのワークのダレが問題になることがあります。
先述の通り、3点受けで両端(4隅)の芯出しを行った状態では、ワークによっては中央が大きく下がっている状態になります。これが「ダレ」と呼ばれるものです。
ワークの自然な状態という観点ではこのダレが発生している状態で研削するのがベストかもしれません。
しかしながらダレが大きいとそれだけ研削量が増えてしまい研削時間が多くかかってしまいます。
また取り代が増加することにより、指定寸法以上に削らなければならないケースが出てくるかもしれません。
もしそのワークが製品として使用する時、中央にもレベリング等を使用しレベル調整するような製品であれば、このダレを残したまま研削するのも有効です。
「ダレ」を解消するためのテクニック
ダレを解消するためのテクニックをご紹介しますね。
概要としては、3点調整で芯出しを行った後、ワーク中央に差し込んだレベリングを徐々に効かせていきます。
この時、中央に当てたダイヤルの数値はどんどんプラスになってきます。
ではどこまで効かせばよいのでしょうか。
両端に対して中央も同じ高さになれば良いのですが、その時注意しなければならないのが、両端のダイヤルの数値が絶対に変わらない範囲で中央を効かす事です。
中央を突き上げた時、両端の数値も変わってしまうと、ワーク全体が中央の突き上げによってねじれなどの変化が生じていることになります。
この状況になると3点受けをして芯出しをした意味が無くなってしまいます。
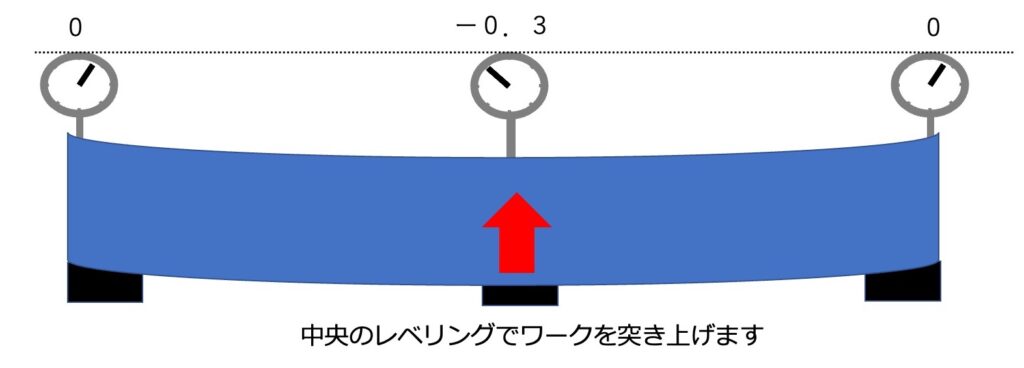
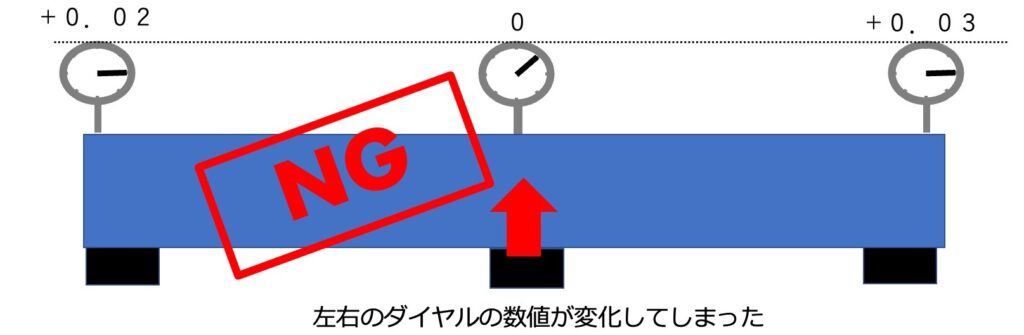
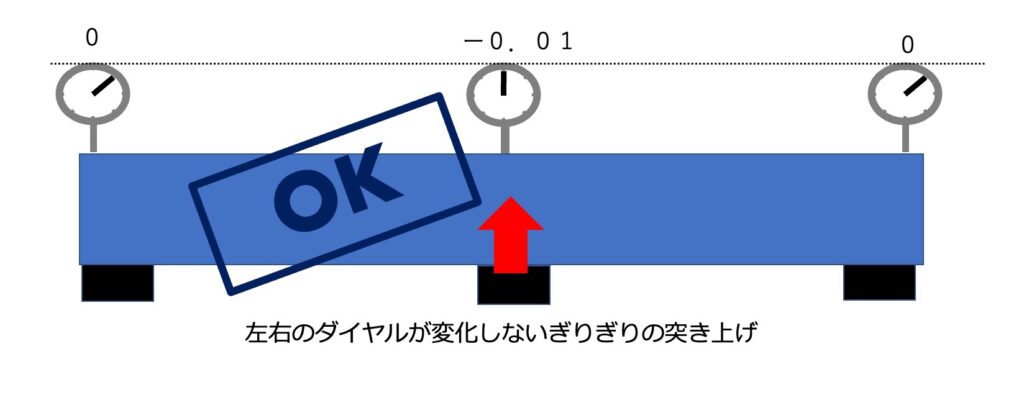
きっちり中央も0にならなくても、左右のダイヤルの数値が変化しないぎりぎりの突き上げで大丈夫です。
この様な方法で突き上げを行い研削を行ったときは、製品として組み立てする人には、中央を○○㎛ほど突き上げたよと教えてあげるようにしましょう。組み立ての人が助かると思います。
この方法はあくまで中央に受ける場所がある場合に有効であり、製品として両端しか受けることが無い製品であればこの方法は使用しないよう注意してください。
研削でのクランプは最新の注意が必要
このように、クランプと一言で言っても様々な注意点とテクニックがあります。
本記事で書いたことを参考にしていただき、精度がしっかりでるクランプを心がけるようにすれば、おのずと高精度な製品に近づきますよ。
コメント