
ライター:SAKAHOMO
研削作業は熱との闘いと言っても過言ではありません。
私が研削盤で研削を始めた時、先輩から言われた言葉が今でも忘れられません。
その言葉とは『素材は生きている。機械も生きている。研削は生き物を扱った作業なんだ』です。
最初はこのおっさんは何を言ってるんだと思いましたが、いろいろな研削を経験していくにつれこの言葉の意味が段々と分かってきました。
「生きている」の意味とは、熱による変位だと。それくらい研削作業者にとって、熱変位をしっかりと理解することはとても重要な事なのです。
本記事では、平面研削業界に携わる私が、高精度な研削をするために熱をコントロールするポイントについて詳しく解説しました!
熱変位の影響を受けすぎると、再現性の高い研削は難しい・・・
良い研削を行うためには、同じワークを同じ精度で研削できる再現性が重要です。
この再現性の大きな敵になるのが素材の熱変位です。
皆さんご存じの通り、素材は温度が上がると、伸びて膨らみます。
鉄道のレールはこの熱変位を計算して、隙間を開けて設置されているのは有名な話です。
この素材の熱による膨張率には線膨張率と体積膨張率の2種類によって表されます。
この2種類の膨張率には計算式がありますが今回はそこまで難しい話ではなく、少し感覚的な内容でお届けしたいと思います。
とにかく素材によって変化しやすい、しにくいの特性はありますが、素材は熱によって、温度が高くなれば膨張し、温度が低くなれば収縮するということをしっかりと覚えておいてください。
私がいる職場では、『1℃ 1ⅿ 10㎛』と言われています。
一般的な鉄で言うと、温度が1℃上昇すると10㎛伸びるというイメージを持つための言葉です。
研削における再現性を高めるためにはこの熱変位を抑える研削や、温度変化を見越した研削を行う必要があります。
金属の具体的な伸び縮みについてはこちらの記事に詳しくまとめています!
なんで熱変位による精度不良が起こるの?
基本的にどんな研削を行っても研削直後にそこまで精度が悪化する事は少ないです。
もし研削直後に精度が悪化した場合は、機械精度の不良が考えられるので直ぐに機械精度の確認を行うことをお勧めします。
熱変位による精度不良はその多くが研削から時間がたった後に測定した際に発生します。
研削においてはワークの平面度や真直度において熱変位による精度不良が多く発生します。
研削直後にくらべ平面度の数値が悪化しているケースや、研削直後は中高の真直度だったのが、中低になってしまっているケースなどです。
ここではその代表的な原因と対策を説明したいと思います。
研削環境と、研削した製品の組み立て環境における温度の不一致
研削盤で研削するワークは、その多くが機械に組み込まれる部品であったり、摺動面に使用される鋳物の研削だと思います。つまり研削後必ず組み立て作業が行われるのです。
ですから研削環境と組み立て環境の温度に大きく差がある場合、研削時の精度と組み立て時の精度に大きな差が生じてしまいます。
例えば研削するエリアの室温が20℃だったとします。
2Mの摺動部分の研削を行い、全長で中高5㎛の真直度を実現できたとします。
その後、室温が30℃の組み立てエリアにワークを移動させ、数日後に組み立てを開始するとどうなるでしょうか?
研削した環境に比べ10℃も温度が高い環境になると、その摺動部分の真直度は中高5㎛から中高20㎛前後まで大きくなっている事でしょう。
もし図面上必要な真直度が中高10㎛以内であった場合、研削精度不良で再研削が必要になってしまいます。
現在の工場で研削エリアの温度と組み立てエリアの温度が大きく違う環境で製品を制作している工場はほぼ皆無だと思います。
ただ、研削エリアは外気温や機械から発生する熱など、熱の発生源が多くなるため精密温度管理空調設備を備えているケースが多いと思います。
それに比べ組み立てエリアは大まかな温度管理になっている工場が少なくありません。
よくあるケースとして、夏は組み立てエリアの温度が研削エリアに比べ数度高くなってしまい、中高が大きくなってします。
冬は研削エリアに比べ組み立てエリアの温度が低くなってしまい、中低になってしまうケースです。
全てのエリアを精密温度管理のできる空調に出来ればよいのですが、そこには大きなコストが発生しますので簡単ではありません。
【対策】寸法の変化を見越して研削を行う
それぞれの季節の研削エリアと組み立てエリアの温度の差の傾向を把握し、基本的には組み立てエリアの温度環境でどのような精度を目指すのかを考慮して研削する必要があります。
もし冬に研削エリアよりも組み立てエリアの方が低い温度になるのであれば、研削時、中高を少し大きくなるような研削を行えば、組み立てエリアに移動した際、丁度良い中高になるといったような工夫を行います。
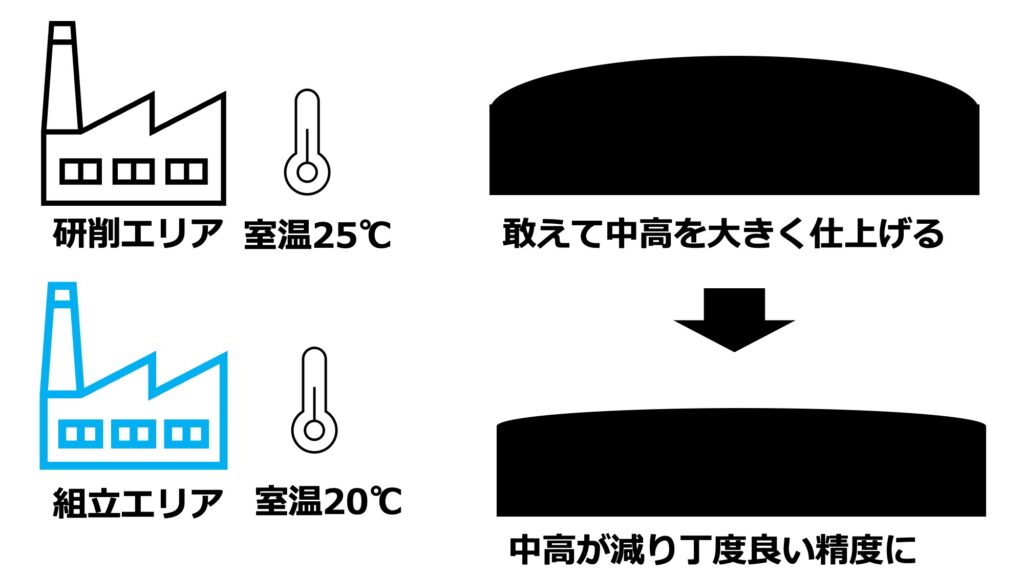
このように研削エリアと実際に組み立てるエリアの温度が違う場合は、最終的に使用する(製品を組み立てる)エリアの温度でどのような精度になるのか研削盤オペレーターが予想して研削を行う必要があります。
一番良いのは研削エリアと組み立てエリアの温度差を無くす事ですが、コストがかかりますので難しいかもしれません。
研削熱による温帯と冷帯との精度差が原因の精度不良
研削や切削加工では必ず研削熱・加工熱が発生します。
切削加工の場合は、その加工熱の約80%が切粉によって排出されると言われていますが、研削の場合は切粉(スラッジ)によって排出される熱はそこまで多くないような気がします。
研削は切削加工に比べより研削熱による影響を受ける作業であり、精度出しを行う場合この研削熱をいかに抑えるかが重要です。
研削盤を使用したワークの精度不良の多くはこの研削熱の影響を受けていると思われます。
【対策】研磨になっていないか注意する
削る作業で切粉(スラッジ)が大きく多く発生すれば、ワークに伝わる研削熱を少なくすることが可能です。
よく研削と研磨の2つの言葉が使われますが、個人的に研削盤はあくまで素材を削るための機械であり、この機械を使用して行う作業は研削であり研磨ではないと考えます。
研磨は磨く作業です。
砥石を使用し磨く作業は、砥粒の小さな砥石や、目詰まりに近い状態の砥石で行うケースが多く、その際削っているのではなく磨く(なでる)作業になるので、研削熱(摩耗熱のイメージ)がより多く発生し、尚且つその熱が逃げにくくワークに多く伝わってしまいます。
研削熱を完全になくすことは不可能です。
ですからその研削熱をいかに少なくするのかを考えなければなりません。
そのためには砥石の負荷計の数値や火花の出方、研削目をしっかりと確認しながら、今は研削を行っているのか、研磨になっていないかを見極めなければなりません。
そして研磨の状態を無くしていくことが重要になります。
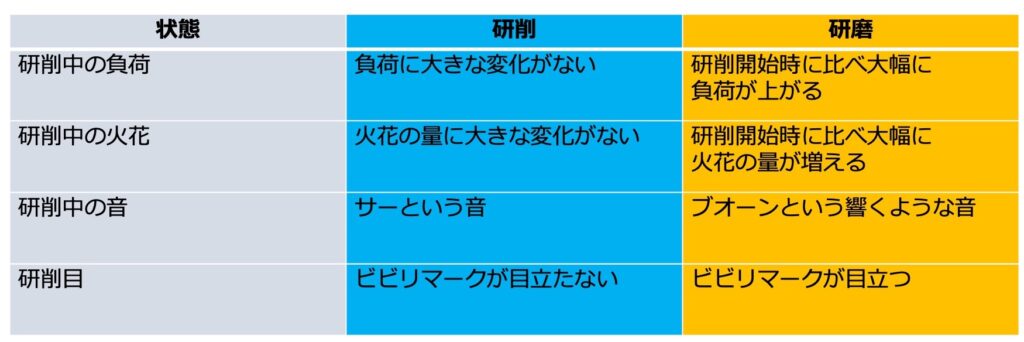
研削作業者が研削中に中々目を離せない理由が、研削中のこのような変化をしっかりと確認しなければならないからです。
荒研削中は比較的目を離しても問題ありませんが、中仕上げ・仕上げ研削はしっかりと研削中の状態を確認しなければ精度や面品位において不良を起こしてしまいます。
話が少しそれますが、私も研削作業の業務改善を考えることがありますが、精度が厳しい・面品位が厳しいワークになればなるほど、自動化や無人化は難しいと感じます。
最終的に研削盤操作者の感覚が重要になるからです。そういった意味では、機械を使用した研削作業は、経験のない人からすれば、無人化・自動化がやりやすい作業のように思われますが、研削作業こそ作業者の知識と経験が必要な作業であり人を介してでないと出来ない作業と考えます。
【対策】研磨にならないためにはしっかりとした研削プランが必要
研磨にならないためには先ほど説明した音や火花に注意する必要がありますが、それよりも重要なのは研削のプランニングにあると考えています。
研削は、①荒研削②中仕上げ③仕上げの3つの構成で成り立っています。
荒研削は気にせずに進めてOK
荒研削とは全体が研削されるまで、ドレスを荒くし、一回の切込み量も比較的大きく設定し、熱や精度や面品位を無視してとにかく全体を削る作業です。
ここで注意しなければならないのが、荒研削では、削った取り代が場所によって大きく異なるという事です。
このように荒研削を行った後は、取り代が大きかった部分ほど低くなる傾向が現れます。
これは研削熱による熱膨張の影響です。
ただし荒研削においてはこの熱膨張の影響を深刻に考える必要はないです。
当然起こる現象として気にせず、早く全体を一度削ることを心がけましょう。
中仕上げはしつこく何度も研削しない
中仕上げとは、荒研削後のワークを一旦冷帯状態に戻し、再度研削を行う工程です。
その後行う仕上げ研削を素早く終わらせるためにも、この中仕上げ作業が研削ではとても重要な工程です。
中仕上げで大切なのは、しつこく何度も研削しない事です。
せっかく荒研削後時間を空けて熱膨張が無い状態に戻したのに、中仕上げでまた時間をかけて何度も何度も研削してしまうと、再び熱膨張が発生し、荒研削で説明したように膨張しているワークを研削する状態に逆戻りとなってしまいます。
私は普段比較的研削面積の大きなワークを研削しています。
ですので、一回の研削でワーク全面を研削する事はまずありません。
研削開始時の砥石負荷の数値が変化し始めたら、研削をストップしドレスを行います。
恐らくワーク全体の三分の一程度の研削になると思います。
早く全体を研削し仕上げに移行した気持ちは理解できますが、中仕上げで重要なのは、とにかく熱膨張を可能な限り抑え、研磨の状態にならない事です。
負荷を見ながら、ドレスを行い、徐々に一回の研削で研削できる面積が拡がってきますので、徐々にドレス速度を遅くして、仕上げの研削面品位と同等に近づけていきます。
中仕上げでは、研削する面にマジックを塗り、削れている部分が目視できるようにしておきます。
そして最終的にマジックがすべてしっかりと消えるのではなく、うっすらと消えている状況で研削を完了する事が重要です。
どんなに気を使って研削を行っても熱膨張は発生します。ですので冷えた時に高低差が出ないように、最終的にマジックがしっかりと消えている部分とうっすら残っている部分がある状態で止めるのです。
この全面マジックがしっかりと消えるまで研削しないというポイントは是非覚えてほしいと思います。
仕上げ研削には時間をかけすぎない
仕上げ研削は中仕上げ研削から最低でも半日は空けてから実施してください。
精度を決定する重要な研削となることから、完全に熱膨張を無くした状態で研削を行う必要があるからです。
中仕上げ以上に仕上げ研削は時間をかけないことが重要です。
仕上げ研削では、面品位を上げるために、ドレス速度を遅くし、表面がツルツルに近い状態に仕上がります。つまり研磨の状態になりやすいのです。
ドレス速度を遅くした砥石は、切れ味は悪く目詰まりも比較的早く起こります。
ですからしっかりと削れる状態がとても短くなり、短時間の削れる状態で仕上げ研削を行う必要があります。
研削から研磨へと状態が変化したまま削り続けると、ワークを砥石で磨く状態が続き、研削熱が多く発生し、冷帯でのワーク精度悪化に繋がってしまいます。
この時、何度削っても中々削れる部分が増えないケースがありますが、それは中仕上げで時間をかけすぎ熱膨張が多く発生した事が原因です。
この仕上げ研削を短時間で終わらせるためにも、中仕上げ研削がとても重要なのです。
この仕上げ研削も、マジックを塗り、全面がしっかりと消えるまで研削をしないように注意してください。うっすらとマジックが残っている状態で止めることがポイントです。
研削盤自体の熱膨張による精度不良
研削盤にも多くの熱発生源が存在し、研削盤を長時間動かせば動かすほど機械自体の熱変位が発生します。
機械の各摺動部分はレールとなる摺動面の熱膨張の影響を受けないように、組み立て段階で各メーカとも対処しています。
熱変異を防ぐ「静圧構造」を採用した研削盤メーカー
摺動面の熱膨張はレールと動くものとの摩擦による熱膨張が多く発生します。
この摩擦による熱変位を防ぐための構造が静圧構造です。
静圧構造は完全非接触で摩擦熱が発生しないため、機械の連続稼働時間によって精度が変化する事がない優れた構造です。
この構造の研削盤で最も上質な研削盤を制作しているのがナガセの研削盤です。
最近は岡本も非接触摺動面に力を入れているようですから、この2メーカーの動向は注視する必要があるかもしれません。
研削盤設置時の温度管理も重要!
摺動面の熱変位は各メーカーが対応してきていますが、注意が必要なのは機械設置場所の温度管理です。
夏と冬とで5度以上温度差がある工場は要注意です。
5度の変化では、例えばテーブル運動の真直度が夏は中高、冬は中低の状態になってしまう危険があります。
夏と冬で同じ削り方をしてもワークの真直度の形状に変化が発生してしまいます。
ですから極力研削エリアの温度は1年を通して安定するように空調管理を行う必要があります。またメーカーに機械を発注する場合は必ず使用エリアの管理温度の情報をメーカーに伝え、その環境下でしっかりと希望の精度が実現できる機械の作りこみをお願いするようにしてください。
またどうしても夏と冬とで温度差が発生する環境であれば、その情報もしっかりと伝え、実際に工場に据え付けする時は、温度の中間である春か秋に据え付けを依頼する事をお勧めします。
マグネットチャックの熱にも要注意!
機械自体の熱膨張による精度不良はメーカーの努力や設置エリアの温度環境整備で防ぐことができますが、注意が必要なのはマグネットチャック仕様の研削盤です。
チャックは研削中ワークを固定するために長時間通電しなければなりません。
この通電中にチャックは非常に高い熱を発生させてしまいます。
これによりチャック上面が徐々に中高になる傾向があり、またその熱がワークにも伝わりワーク自体も中高になってしまいます。
チャック仕様の機械を持っている人は、一度チャックとチャックの間をシムで測ってみて下さい。必ず隙間が空いています。
これはチャックが熱によって膨張してもチャック同士が干渉しないための処置です。
長く研削を行うと、いつのまにかワークの真ん中しか削れない状態になることが多々あります。
この様な状態になったら、一度機械を止めて冷やすか、研削液温度を下げてやる必要があります。
もしチャック仕様の研削盤を購入する際は、すこしコストは上がりますが熱を発生させない永電磁チャック仕様を選択する事をお勧めします。
永電磁チャックであれば長時間通電しても熱は発生しないので、精度に影響が出ることはありません。
特に薄物のワークを削る場合は、通常のチャックですと反りが発生しやすくなるので、少しでも熱の発生源を無くすために永電磁チャックの採用をお勧めします。
研削液は温度調整機能によってしっかりと管理しよう!
精密な研削を行う場合、研削盤を導入する際には、必ず温調機がついた研削液タンクを選択してください。
コストが安いからと言って、温度調整のできない研削液タンクを購入する事はやめた方がいいです。
温調機はダイキン製が安心して使用できるためお勧めです。
常に一定の温度に設定したり、室温や機械温度と同調させたり様々な研削液の温度管理が可能になります。
例えば室温がいつもより高くなってしまった場合には研削液の水温を下げることによって、ワークが過度に中高になるのを防ぐことができます。
仕上がりを中高にしたい時には、敢えて水温を下げることにより、研削後の冷帯状態で中高状態を作ることも可能です。
様々な環境の変化に対応するために研削液の温度調整は大きな武器になるので、温度調整機能付きの研削液タンクは必ず必要な機能と考えます。
研削加工ではより精密な加工を行う分、温度にもかなり細かく気を遣う必要があります。
熱のコントロールがうまく行かない方は、本記事に書いたような対策を一度試してみてください(^^
コメント