
ライター:SAKAHOMO
平面研削盤には大きく分けて3つの研削パターンが存在しています。
それぞれの特性を理解する事で、ワーク別に適切な研削パターンを選択できより良い研削が可能となります。
本記事では、主要研削パターンである「プランジ研削」「間欠トラバース研削」「連続トラバース研削」の3つに関して説明をしていきます。
※今回の説明では、砥石頭の上下運動の軸をZ軸・左右運動の軸をY軸として説明を行います。(軸名称はメーカーや機種によって異なりますのでご使用の機種の軸に合わせて読んでください)
プランジ研削
プランジ研削とは?
プランジ研削とは、平面研削盤の研削パターンの中で最もシンプルで扱いやすい研削種類となります。
その動きはX軸(1軸)のみのテーブル運動で、Z軸が切込みを行うものです。
ですのでプログラムで指令する数値は「1回の切込み量」と「トータルの切込み量」の2つになります。

例えば0.005mmずつ、トータルで0.05mm研削したいとします。その場合、「1回の切込み量」を0.005と「トータルの切込み量」を0.05と設定します。
動きとしては「0.005mm切り込み、テーブルを動かして削る」操作を10回繰り返すことで0.05mmを研削します。
このときにテーブルのY方向は固定しておき、X方向のみ動かすことがプランジ研削の特徴です。
《プランジ研削、正面方向から見たイメージ動画》
《プランジ研削、横方向から見たイメージ動画》
この研削では、砥石幅以内の幅のワークの場合でしか使用することが出来ません。
一度の切込みでワーク全体を研削出来る事から、研削時間もより短くすることができます。
過去の記事で説明したドレッシングをしっかりと行えば、大きな研削トラブルは発生しないと思います。
プランジ研削のメリット
・比較的短時間で目標の取り代を研削出来る。
・作業者の経験に左右される要素が少なく、製品の質に差が出にくい。
・プログラム研削でなく手動でも簡単に行うことができる。(切込み過ぎによる事故に注意)
プランジ研削のデメリット
・砥石幅以上のワークには使用できない
プランジ研削は、横方向の動きがありませんので砥石幅以内の大きさのワークにしか対応できません。
プランジ研削のまとめ
プランジ研削はとても単純な研削パターンで、特に研削テクニックが必要ではなく、研削盤を使用する作業者にとって最初に学び実行するパターンです。
デメリットも一つしかありませんが、実際に砥石幅以内のワークはそう多くは無いので、意外と使用頻度が少ない研削パターンとなります。
また砥石幅以内であれば使用可能ですが、砥石幅と同じような幅のワークでのプランジ研削はお勧めできません。
砥石の中央と端とでは、砥石の脱落に若干の差が出てしまい(端の方が脱落しやすい)、どうしてもR形状になってしまいますので、砥石幅の3分の2くらいまでのワークでの使用をお勧めします。
間欠トラバース研削
間欠トラバース研削とは?
間欠トラバース研削とはZ軸の移動運動と共に、Y軸の移動を同時に行う研削動作です。
traverse(トラバース)とは「横断」という意味の英単語で、ここではY軸での移動のことを指します。
プログラム上では、プランジ研削でも指令した「1回の切込み量」と「トータルの切込み量」に加え、「1回のトラバース量」と「トータルのトラバース量」の指令も必要になります。

動きの流れとしては以下のようになります。
・指令した量だけ切込み、テーブルのX軸が動いて削っていく
・テーブルの反転の際、指令したトラバース量だけ砥石頭がY軸移動を繰り返す
・トータルトラバース量に達したら再び砥石頭が切込みを行い、再びテーブル反転ごとに砥石頭が今度は反対方向にY軸移動を行う
《間欠トラバース研削を横方向から見たイメージ動画》
間欠トラバース研削は、砥石幅より広い幅のワークの研削に使用されます。
恐らく研削パターンの中で最も使用頻度が高いと思います。
荒研削・中仕上げ・仕上げとどの状況でも使用できます。
「一回のトラバース量」と「トータルトラバース量」の決め方
例えば幅が100mmのワークを削りたいとします。
その場合、「トータルトラバース量」はワーク幅より少し多めの120mmに設定します。
「一回のトラバース量」は砥石幅にもよりますが砥石幅75mmの砥石を装着していれば半分程度の30~40mmが目安です。
間欠トラバース研削のメリット
・どのような研削段階でも使用できる。
・ワークの幅に左右されない
・一回のトラバース量を多くすれば研削時間を短縮できる
・ある程度の重研削でも対応できる
間欠トラバースのデメリット
・送りマークが発生しやすい
・一回のトラバース量が多すぎると精度不良が発生しやすい
・長時間の研削では面品位が悪化する
間欠トラバースの注意点
間欠トラバースは、使用頻度が高くオールマイティーな研削パターンだと思います。
但し、色々と注意すべき点が多いという一面もあります。
トラバース量が大きすぎると発生する「段差」に注意!!
間欠トラバースにおける一回のトラバース量には注意が必要です。
荒研削であれば比較的大きなトラバース量でも問題ありませんが、中仕上げ以降は大きすぎるトラバース量では精度不良や研削面品位の低下を引き起こしてしまいます。
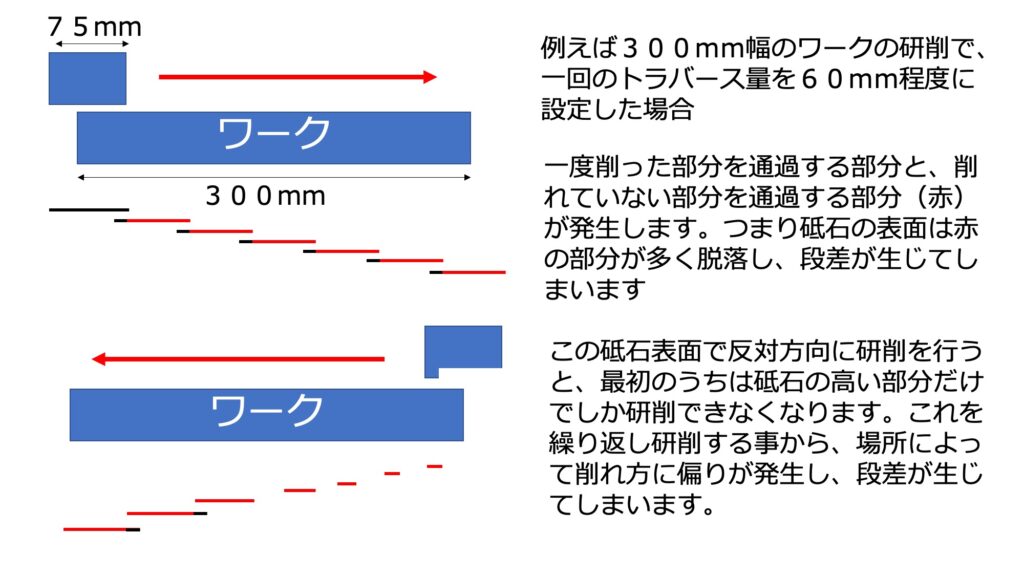
このような状況を避けるために、特に中仕上げ以降は一回のトラバース量を砥石幅の半分以下に設定する必要があります。
また一回のトラバース量を小さくしてもどうしても砥石に段差がついてしまいます。
長時間繰り返し研削を行うとこの段差の傾向がどんどん強くなりますので、面品位を悪化させたくない研削の時には、時間をかけない事が重要です。
ワークの種類にもよりますが、最高でも2往復くらいで研削を終える事が重要です。
砥石頭の姿勢変化で送りマークが現れることも・・・
また、この間欠トラバースで最も厄介なのが送りマークの出現です。
送りマークの発生には先に述べた砥石の偏摩耗により発生する微小な段差が原因のケースもありますが、どのように対策してもどうしても送りマークが発生してしまうこともあるのです。
その原因は機械の組み立て精度の不良による送りマークの発生です。
この要因には砥石頭の姿勢変化が深く関わっています。
プランジ研削では砥石頭がY軸方向に移動しないため問題になりませんが、Y軸移動を伴う間欠トラバースでは、この砥石頭の姿勢変化の影響がもろに送りマークとして発生してしまいます。
研削作業者の方であれば経験があると思いますが、機械によっては手前側は送りマークが発生しないのに、奥に行くと送りマークが発生してしまう癖を持っているケースがあります。
この原因は、手前側では砥石頭の姿勢がドレス位置での姿勢と一致している一方、奥側にいくにつれ姿勢が変化し、ドレス位置のそれと一致しなくなっていくことにあります。
この姿勢変化によって砥石の当たり方が不均一になり、送りマークが発生してしまいます。
《間欠トラバース研削で、砥石頭が傾くイメージ動画》
送りマークが出てしまった場合どうすれば?
門形平面研削盤を例にすると、これはクロスレールの砥石頭摺動面の真直度不良により発生します。
この傾向は研削テクニックでは中々修正できるものではありませんので、すぐにメーカーに問い合わせ、クロスレール摺動面の修正を依頼して下さい。
砥石頭の姿勢変化が原因の送りマークかどうかは、砥石頭のY軸方向の傾き変化が読み取れるよう、砥石頭に角レベルを取り付け、場所ごとの傾きの差を測定してみて下さい。
傾きの差がメートル当たり60㎛あれば、砥石幅100mmの砥石で場所により6㎛の傾きが生じることになります。
砥石頭の場所により傾きが大きく生じていれば、砥石頭の姿勢変化が原因と仮定できます。
高級機械であるナガセの機械はこのあたりの対策をしっかりと行っていますが、値段が高額かつ温度管理コストが高くなります。
コストを抑えるのであれば、岡本の研削盤がこの砥石頭の姿勢変化の削減に力を入れていますのでお勧めです。
連続トラバース研削
連続トラバースとは?
連続トラバース研削とは、間欠トラバース研削の弱点を補うために誕生した研削パターンです。
連続トラバース研削は切込みを行った後、砥石頭がY軸方向に移動します。
ここまでは間欠トラバースと同じですが、そのY軸の移動方法が異なります。
間欠トラバースでは「一回のトラバース量」を指定し、テーブル反転のたびにその量だけY軸移動を繰り返す方法でしたね。
一方連続トラバースでは「一回のトラバース量」は指定しません。
「トータルトラバース量」だけ指定します。

動き方としては、切込みと同時に砥石頭がトータルトラバース量に達するまで動き続けます。
指定したトラバース量に達したら再度切込みを行い、逆方向に移動を再開します。
この繰り返しをトータル切込み量に達するまで行います。
《連続トラバース研削のイメージ動画》
この研削方法は、中仕上げの最終研削や仕上げ研削で多く使用されます。
私自身も仕上げ研削はこの連続トラバースを使用します。
ただしこの連続トラバースでは、砥石頭の移動スピードの設定が必要になります。
この移動速度が速すぎると送りマークが発生してしまい、逆にあまりにも遅すぎると熱変位や砥石の研削効率の悪化を招き、精度不良やびびりマークが発生してしまいます。
この適切な移動速度はワークの材質や大きさにより変わってきます。
作業者に経験が必要になるポイントです。
連続トラバース研削のメリット
・面品位の向上が期待できる
・送り速度がマッチすれば、送りマーク・ビビリマークの発生を抑えられる
・間欠トラバースの弱点である段差の発生を抑えることが出来る。
《間欠と連続の、段差のでき方の違いについてのイメージ動画》
③―2 連続トラバースのデメリット
・低速でY軸移動を繰り返すため研削時間は長くなる
・仕上げ研削では、長時間の研削には向いていない(1往復~2往復が限界)
・送り速度に関しては作業者の経験が必要になる
連続トラバースの注意点
連続トラバース研削は、仕上げ研削に最も適した研削パターンです。
研削条件によっては送りマークが発生する事も・・
仕上げ研削で使用する場合は、送り速度と共に、一回の切込み量にも注意が必要です。
あまり大きな数値を設定すると送りマークが発生しやすくなります。
個人的に仕上げ研削時の一回の切込み量は2㎛~3㎛がベストだと思います。
また時間をかければかけるほど面品位が悪化するので、長くても2往復で終了する必要があります。
砥石の手前か奥かどちらが強く当たっているのか把握しよう
また連続トラバース研削では、しっかりと研削中の状態を確認し、砥石の手前・奥のどちらが強く当たっているのか把握してください。
強く当たっているのが手前であれば最後のトラバース方向は手前から奥に設定してください。
逆に奥が強く当たっているのであれば最後のトラバース方向は奥から手前に設定してください。
連続トラバースでは砥石頭が常に動いています。
ですから動いている方向と反対側が強く当たっていれば、研削がしっかりとできるのです。
これは中々言葉では上手く伝わらないかもしれませんが、研削作業者の方であればイメージが付くかと思います。
連続トラバースの仕上げでの移動速度は、間欠トラバースに換算すると、恐らく一回のトラバース量が10㎝程度と非常に少ない数値となります。
ですから初めて連続トラバース研削を見ると、動いているのかどうか分からないと思います。
そのくらい低速で動かすことによって、間欠トラバースの弱点であった、砥石の変摩耗や変摩耗によって強く当たる部分が生じて段差が発生してしまう事を防いでいるのです。
砥石の変摩耗が生じてもゆっくりと左右運動を繰り返すことで、すき間なく全面をしっかりと砥石で削ることができるのです。
まとめ
本記事では、主要3種類の研削パターンを紹介しました。
砥石幅より小さな幅のワーク研削ではプランジ研削で対応できますが、場合によっては間欠トラバースや連続トラバースを使用するケースもあります。
ここは面品位・精度に応じて臨機応変に対応しなければなりません。
例えば幅の広いワークでは、荒・中仕上げ・仕上げ研削のプランに合わせた研削パターンを選択する、といった判断が必要になります。
私自身の経験では、荒研削は間欠トラバースで一回のトラバース量や切込み量を可能な限り大きくし、早く全体を研削します。
中仕上げの中盤までは、一回のトラバース量と切込み量を徐々に小さくしていき、中仕上げの最期では連続トラバースで研削面を整えていきます。
そして仕上げ研削でも連続トラバースで最小の切込み量で半往復~1往復のみの研削を行い研削を完了します。
皆さんのご使用の研削盤のメンテナンスでテーブルのセルフ研削を行う事があると思います。
その時の手順も同じように行えば、わざわざメーカーを呼んで高額なお金を支払わなくても自分で十分対応可能なので試してみて下さい。
また個人的に、送りマーク・ビビリマークを抑える研削の組み合わせは、ドレッシングの記事で紹介したRドレス+連続トラバース研削であると考えます。
送り速度を低速にして研削すればとても綺麗な面品位を実現できますので、機会があれば試してみて下さい。
コメント