ライター:SAKAHOMO

平面研削の精度や面品位を追求していくうえで、ドレッシングはとても重要な作業です。
とくにビビリマークや送りマークを解消するために、どのようなドレッシングを行うかの判断をいかに適切に行えるかが研削盤作業者の腕の見せどころではないでしょうか。
本記事では、ドレッシングについて、手順からそのポイント、コツまで網羅的に詳しく解説しています!
ドレッシングって?
ドレッシングとは簡単に言うと砥石の研削面をしっかりと整える作業です。
野菜にかけるアレではありません!(整えるという語源は同じようですが・・・)
一般的なドレッシングは、砥石の研削面を真っ直ぐに整える型直しの作業となります。
ここでの真っ直ぐというのは幾何学的な意味での真っ直ぐで、表面を直線に近づけ、尚且つ砥石頭の左右運動と平行にしなければなりません。
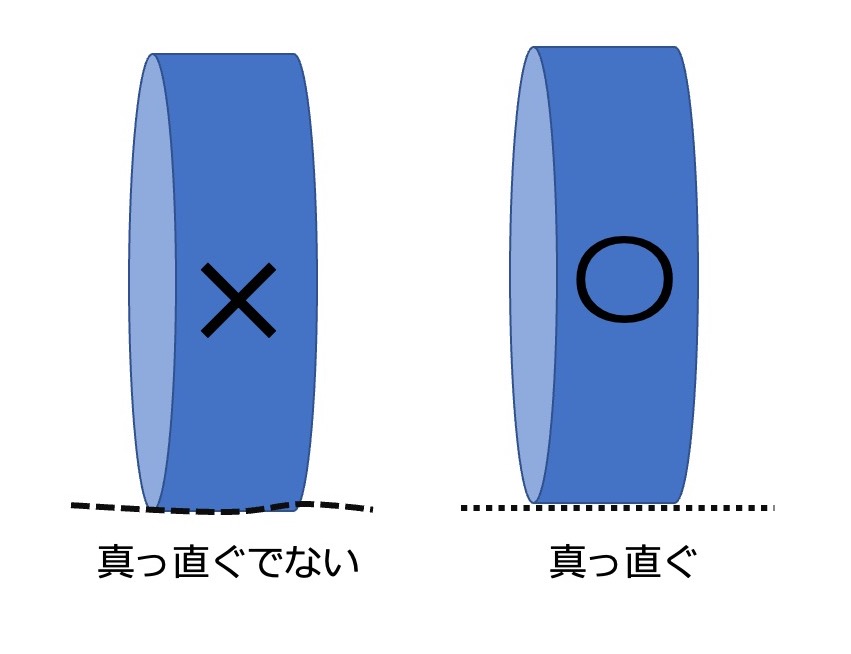
また研削砥石は砥粒が突出した構造ではないので、研削を繰り返すと砥粒が丸みを帯びてしまい、切れ味が悪くなってしまいます。
研削盤は研削、つまり削るための作業ですので、定期的に砥粒を鋭利にしてやる必要があります。
ドレッシングはその役割を果たす作業でもあります。
多くの研削盤は機械にドレッシングツールが搭載されており、NC制御によって自動ドレッシングが出来るようになっています。
古い機械だと、ドレッシングツールやNC制御が搭載されていないケースもあり、そのような機械ではドレッシングツールをテーブル上に取り付け、手動で砥石頭を動かしドレッシングを行います。
なんでドレッシングが必要なの?
ドレッシングは研削作業では必ず行わなければならない大変重要な作業です。
ドレッシングによって、ワーク仕上がり面の面品位に大きく影響します。
ビビリマークや送りマークの有無はもちろん、研削したワークの面粗度(粗さ)もこのドレッシングによって自由自在に調整できます。
また、研削精度にも影響を与えます。
例えばドレッシングによって、砥石の研削面がとても滑らか(ツルツルに近い)にドレッシング出来れば、ワークの研削面はツルツルに近い仕上がりになります。
しかしながらその状態で研削を行えばワークに多くの研削熱が発生し、ワークが冷えた際に変形が起き、精度が大きく悪化します。
また、砥石の研削面が真っ直ぐになっていても、平行が悪ければ、ワークは段々に削れてしまい、平面度の悪化を招きます。
他にも、研削を続けていくと、砥粒の脱落によって
砥石研削面の状態が悪化したり、研削スラッジが砥石に付着し(目詰まり)、研削効率が大きく悪化するので、こまめなドレッシングが必要になります。
例えばワークを0.2mm研削する場合を考えたとき、まずは粗目のドレッシングで0.05mm研削し、同じ条件でドレッシングを行い再度0.05mm研削を行うことを繰り返します。
そして残り0.05mmとなった時に、ドレッシング条件を中仕上げの条件に変更しドレッシングを実行し、残り0.01mmになったら、仕上げ条件でドレッシングを行い研削を行う・・・といった研削スケジュールを考え、その都度必要な条件でのドレッシングを行わなければなりません。
ドレッシングの手順
ドレッシングの手順はそれほど難しいものではありません。
NC制御で行う方法と、手動で行う方法の2種類がありますので、それぞれ分けて解説していきますね。
NC搭載研削盤でのドレッシング
現在販売されている研削盤はその多くがNC制御でドレッシングを自動で行える機械となっています。この様な機械では、ドレッシングの手順はとても簡単となっています。
手順としては、まず砥石の動バランスの調整を行います。その後に、ドレッシングを行う砥石頭の座標の設定を行います(砥石合わせ)。
砥石合わせ
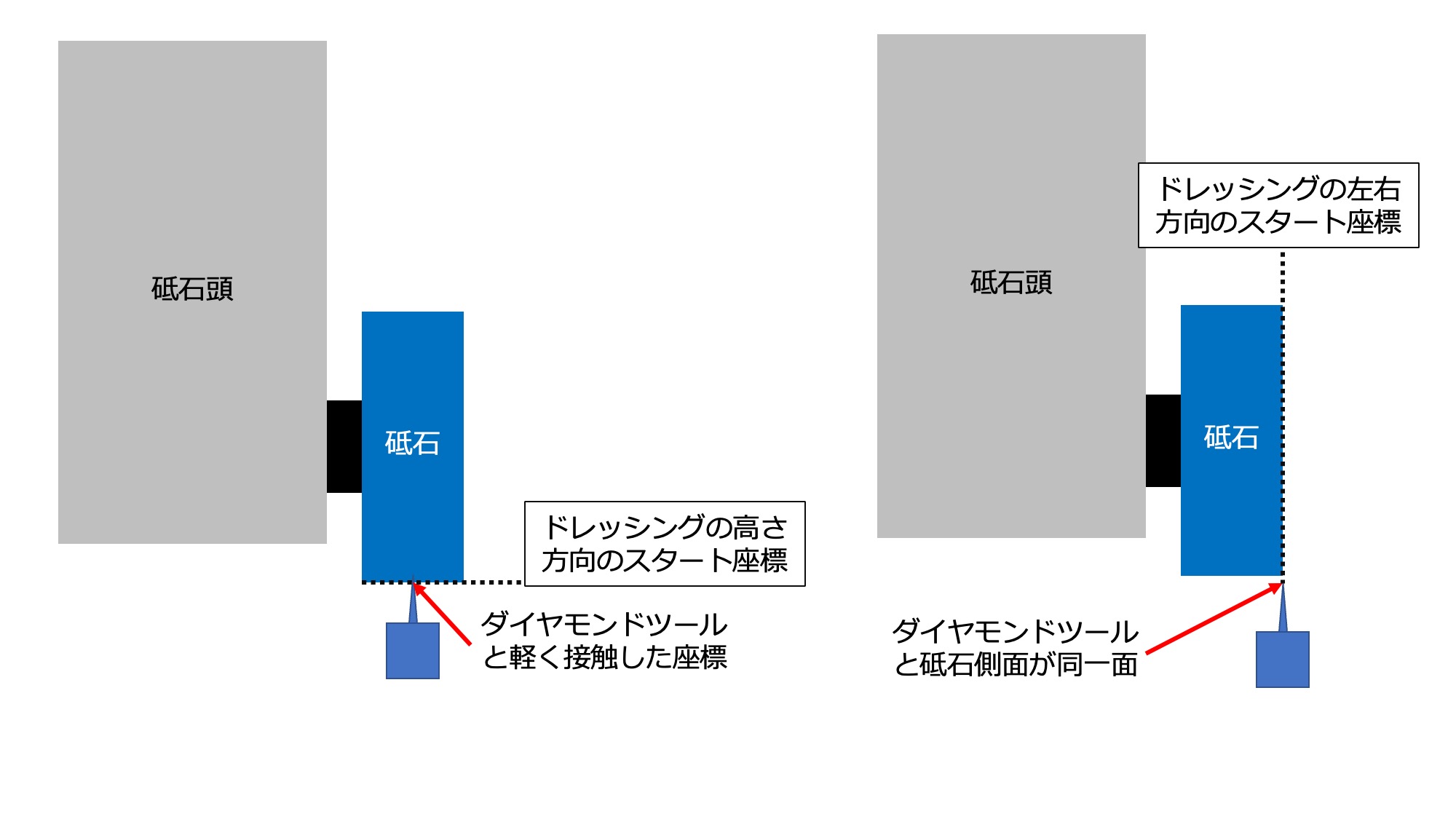
この砥石合わせは、大きく2つの方法で行われます。
一つ目の方法では、まずダイヤモンドツールの先端に、砥石頭をゆっくりと下降させ、砥石とダイヤモンドツールが近づいたら、手で砥石を回しながらさらにゆっくりと下降させ、砥石とダイヤモンドツールが接触したときの「ガリッ」と音が鳴った砥石頭の上下方向の座標を記憶させます。
その後少し砥石頭を上に逃がした上で、向かって左側に砥石を移動させ、図のようにダイヤの先端と砥石の右端が同じになる位置を確認し、その左右方向の座標を記憶させます。
機械によっては同じになった位置から5mm更に離れた位置がスタート位置の場合もありますので、そこは機械仕様を確認する必要があります。
もう一つの方法は、熟練の方が多くやっている、少し難易度の高い方法です。
まずは先程と同様に砥石が回転している状態でゆっくり砥石頭を下降させ、ダイヤモンドツールと接触する音を確認、その位置を高さ方向で記憶させます。
その後がポイントで、砥石頭を逃がさずにそのまま左右に砥石頭を移動させ、最後にダイヤモンドツールと砥石の側面が同一面になるところで左右方向の座標を記憶させます。(ドレッシングの開始位置の座標設定はメーカーにより異なりますので必ずご使用の機械に合った座標の設定をしてください)
この方法は、作業時間も早く終わりますが、砥石が高速回転している状態で行いますので、砥石頭の加工速度を最低速度に設定し、慎重に作業を行わなければなりません。
もし大きく下降させてしまうと、砥石にダイヤモンドツールが食い込み、砥石の破損に繋がったり、飛散した砥石でケガをする危険があるので慎重に作業しなければなりません。
いずれかの方法でドレッシングのスタート座標を記憶させたら、砥石頭を上方向に逃がしてやり、NC画面にてドレッシングの各条件を入力し、サイクルスタートを行えば、自動でドレッシングが実行されます。
尚、新品の砥石の場合ドレッシング後に砥石バランス確認・調整を行い、その後もう一度ドレッシングを行う事をお勧めします。
手動で行うドレッシング
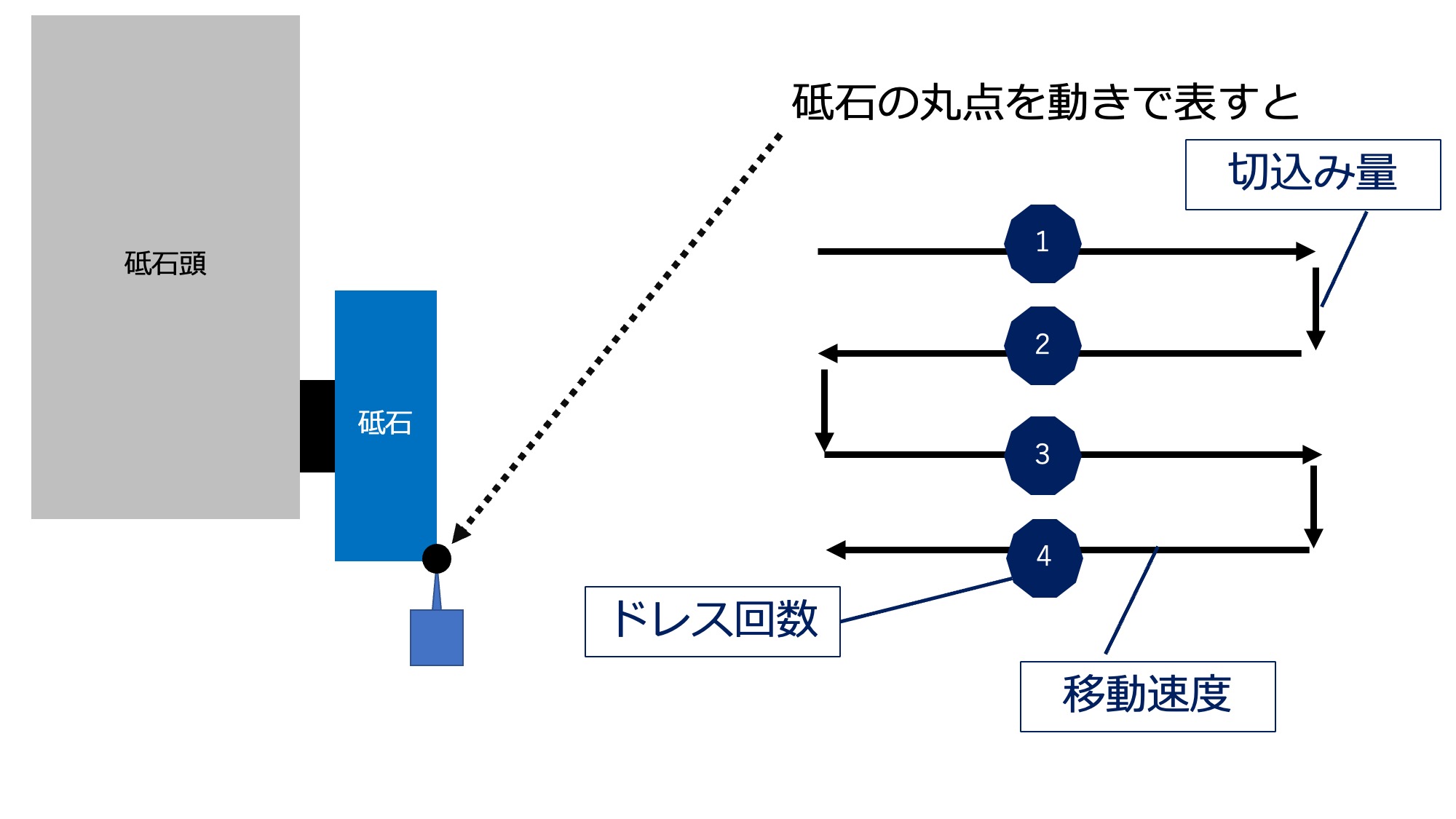
ドレッシングを手動で行う場合は、まずテーブル(チャック上)にマグネット式ダイヤモンドツールを設置します。
その後、先程の方法と同様に砥石を下げていき、ダイヤモンドツールと砥石を軽く接触させ、砥石頭を手動で左右に移動させます(右左共に砥石が完全にダイヤモンドツールから外れるまで)。
そこから、砥石頭を0.2mm程度下げ、再度砥石頭を左右に移動させドレッシングを行います。この作業を繰り返し行い完了です。
ドレッシングの条件
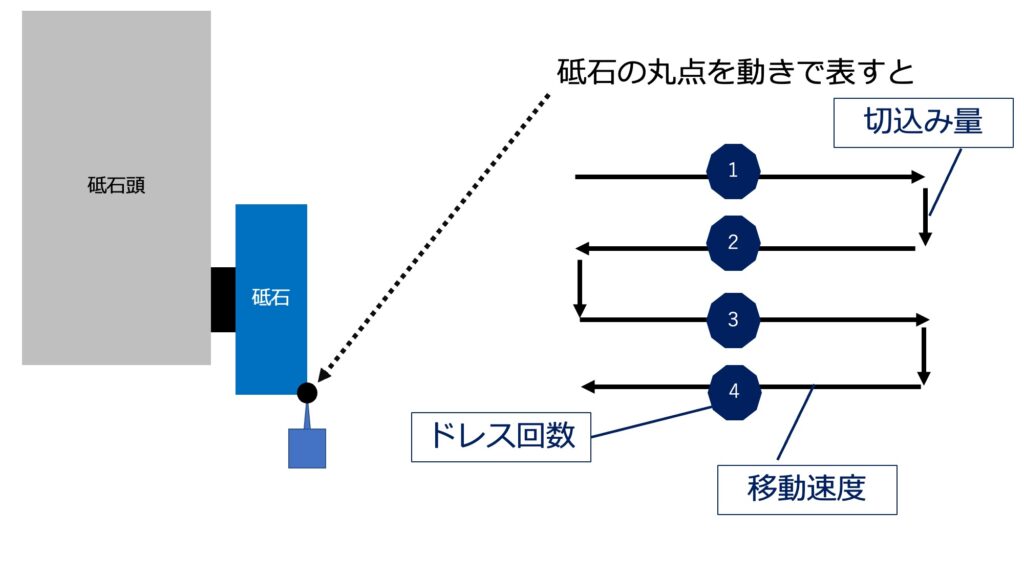
ここでは代表的なドレッシングの種類や条件をご紹介します。
まずドレッシングには3つの条件が存在し、それぞれをしっかりと設定する必要があります。その条件とは、1)一回の切込み量2)移動速度3)ドレス回数です。
ドレッシングの動きは上に載せた動画の通りです。
動きは非常に単純ですので、切込み量・移動速度・ドレス回数はすぐに理解できると思います。
先程掲載した図に記載したとおりですが、もう一度載せておきますね。
切込み量
まず切込み量ですが、一回毎にどのくらい切り込むかの数値となります。この数値が大きくなればなるほど砥石が削られる量も増加するので、砥石の寿命は短くなります。
感覚的に一回の切込み量は0.1mm~0.2mmくらいが標準ではないかと思います。
切込み量を抑えた方がよりきめ細やかな表面が形成されると言われていますが、個人的に0.1mmでも0.2mmでも大差が無いように感じます。
移動速度
次に移動速度です。ドレス速度とも呼ばれます。
この移動速度はワークの仕上げ面に大きな影響を与えるとても重要な項目です。
移動速度が早ければ早いほど表面に凹凸ができやすく、切れ味も向上します。逆に遅ければ遅いほど表面はより滑らかになり、切れ味は低下します。
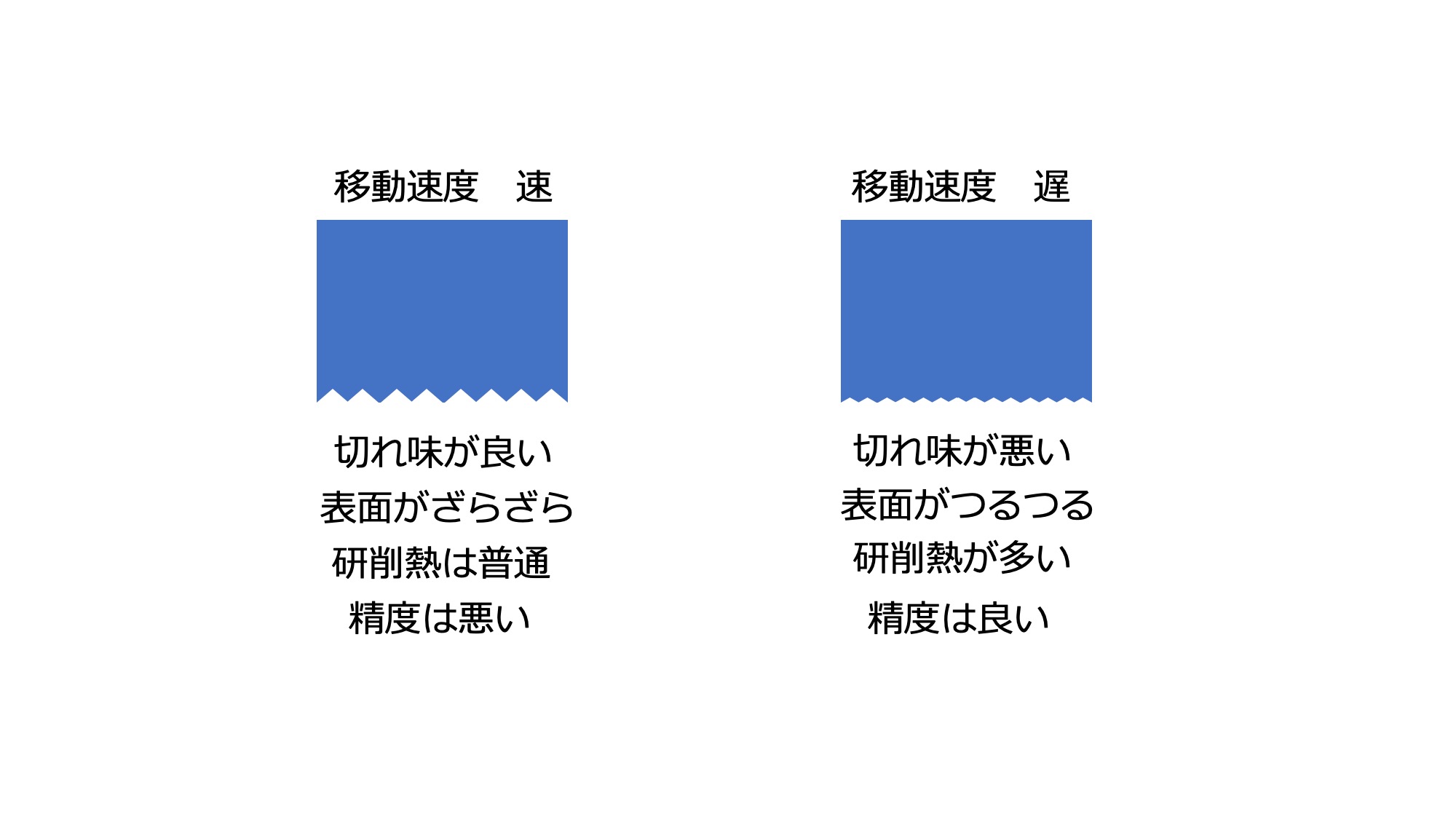
この違いを理解し、取り代に対しての研削プランを立て荒・中仕上げ・仕上げそれぞれで移動速度を設定します。
イメージ的にやすりをイメージすると分かりやすいかもしれません。
大きくやすりで削る場合は、ギザギザの大きな荒いやすりを使用しますね。この状態を研削では移動速度を早くすることで実現します。
対してやすりで仕上げを行う場合はギザギザの小さな目の細かなやすりを使用しますよね。この状態を移動速度を遅くすることで実現します。
ドレス回数
ドレス回数はメーカーによって異なるかもしれませんが、私が使用している研削盤では2回で一往復です。ですので一回と指令すると半往復です。
回数も基本は二回(一往復)で大丈夫かと考えます。
ただし、移動速度を早く行った砥石で研削する場合、荒研削を行うケースがほとんどだと思います。
荒研削後は砥石表面が荒れている事が多く、ドレス一回の切込み量が少量の場合、一往復ではしっかりと砥石表面を整えることができないケースが発生します。
また砥石幅全面を使用しての研削ではなく、砥石幅の半分程度の幅のワークを研削した場合、砥石の摩耗に偏りが発生していますので、そういった場合も一往復では砥石表面が整えられないケースがあります。このような時はドレス回数を二往復にした方が良いかもしれません。
また機械の特性によっては、同一方向のドレッシングを行った方が面品位が向上するケースがあります。砥石頭の左右運動の右行きと左行きの姿勢変化や真直度の違いによってこのような現象が起こるんですね。
そのためどうしても面品位が悪化する場合は、片ドレスといわれる、一歩方向のみ切込みを行うドレスを行ってみるのもよいでしょう。
また、片ドレスにせずとも最後の移動方向のみを変えてみても改善できるかもしれません。
偶数回数のドレスを奇数回数にすれば最後の移動方向は変わりますので簡単に試すことができます。
このように特に移動速度と回数との組み合わせにより様々な面品位が実現できます。
面取りドレスとRドレス
ドレッシングを行う事で砥石の研削面は真っ直ぐになりますがそこで注意が必要なのが、砥石の側面と研削面が直角になってしまうことで、送りマークの発生が生じてしまうことがあるということです。
面取りドレス
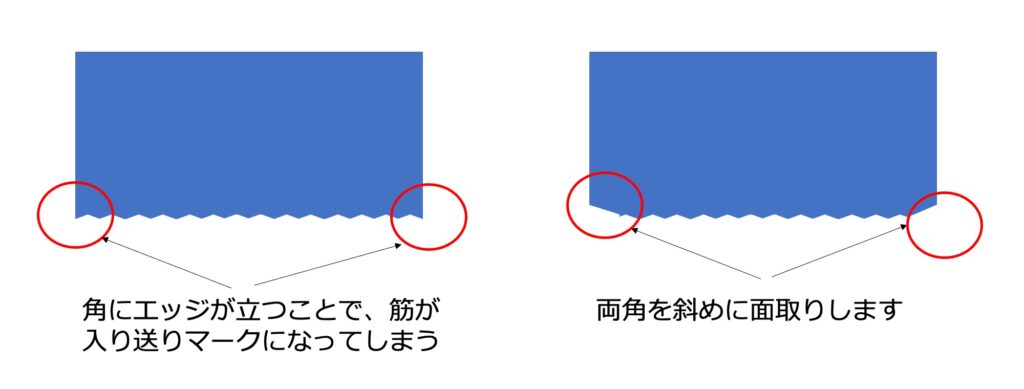
このようなエッジが立つ状態を回避するために、面取りドレスというドレッシング方法があります。この面取りドレスは通常のドレッシングを行った後、両角を指定した幅と高さで面取りするドレッシングです。
このように角を落とすことで、送りマークの低減が期待できます。この時の高さと幅の関係性をしっかりと把握しておかなければなりません。私としては、面取り高さは面取り幅に対して1000分の1程度にするべきと考えています。
例えば面取り幅5mmであれば面取り高さは0.005mmとなります。幅に対して面取り高さを大きく設定しすぎると、逆に送りマークが発生してしまうので注意が必要です。
またこの面取りドレスは手動では不可能となります。
Rドレス
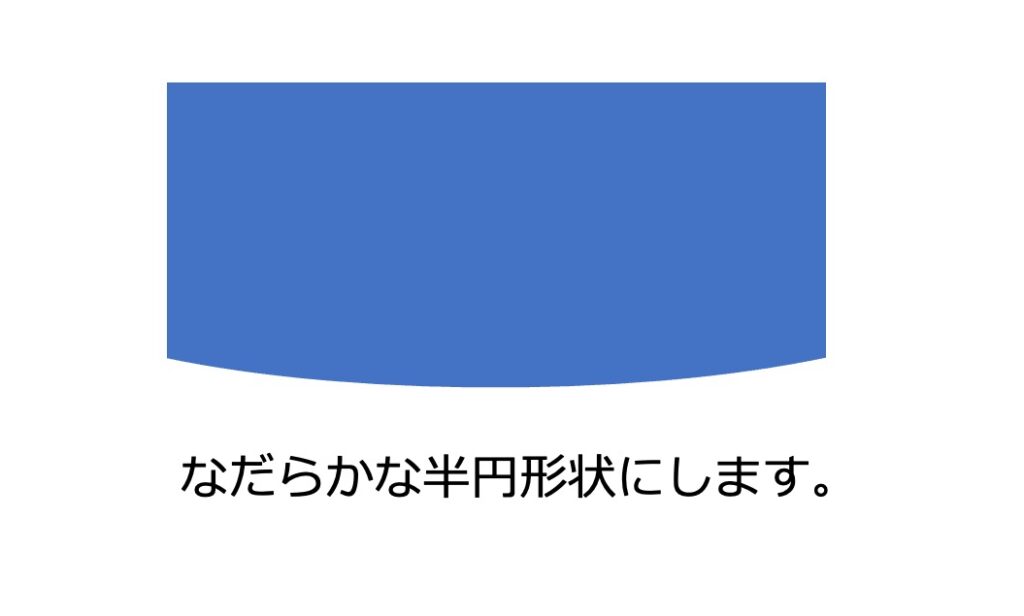
他にもRドレスというドレッシング方法もあります。
この方法では砥石頭を横方向に真っ直ぐ動かすのでなく、NC制御により敢えてなだらかな半円形状を作り、エッジが無い状態を作り上げるドレスです。
このRドレスは研削盤の質によっては上手くなだらかな半円形状が作れず、全く使い物にならないケースもあり難しいドレッシングですが、しっかりと半円形状が作れれば、送りマークはかなりの確率で解消されます。
但し研削の方法によってはびびりマークが発生しやすいデメリットもあります。
ドレッシングのポイントと注意点は?
ドレッシング条件をしっかりと計画しておく
研削は熱変位との戦いです。
いかにワークに研削熱を伝えず素早く仕上げ研削が出来るかにかかっています。
仕上げ研削は数マイクロメートルの取り代です。仕上げ研削で長い時間研削をしてしまうと精度は大きく悪化します。
素早く仕上げるためには仕上げ研削に至るまでの荒研削・中仕上げ研削が非常に重要です。
それぞれの段階でドレッシングの条件をしっかりと計画してから行うようにしましょう。
特に移動速度(ドレス速度)は重要な要素であり、この速度を誤らないよう注意が必要です。
必ず十分な研削液をかけるようにする
またドレッシング中は必ず研削液がダイヤモンドツールの先端に流れるように調整してください。
研削液が掛からないと、ダイヤに熱が発生しダイヤの先端が伸びてしまい、しっかりとしたドレッシングが出来なくなります。研削液の流し方にも十分注意してください。
機械潤滑機能を停止させておく
ドレッシング中の注意事項でとても重要なのは『絶対に機械潤滑を行わない』事です。
研削盤には多くの摺動面があり、そこには定期的に潤滑油やグリスなどを供給するようになっています。
おそらく多くのメーカーの研削盤は〇〇分に一度〇〇CCの潤滑油を自動供給といった設定になっていると思います。
この潤滑供給は機械に必要ですし、行わなければ機械の故障に繋がります。ただし、ドレッシング中にこの潤滑が行われるとしっかりとしたドレッシングが出来ないので、潤滑をストップしておく必要があります。
私が使用している研削盤には潤滑停止ボタンがあるので、ドレッシング時はこのボタンをONにしています。
なぜ潤滑が行われるとだめなのでしょうか。それは摺動面に油が入り込む瞬間、砥石頭が5㎛ほど、一瞬上昇してしまうためです。ドレッシング中に潤滑が行われたら、真っ直ぐなドレッシングが出来なくなり、いびつな形状になってしまいます。ですのでドレッシング中は強制潤滑機能をストップする事が大切です。
研削において避けては通れないドレッシングですが、意外と多くのポイントがありますね。
びびりが発生したときや、送りマークが気になる際は、本記事に書いたことを参考にしていただき、ポイントを押さえたドレッシングを行ってみてください(^^
コメント