
QRコードは、1994年に株式会社デンソーウェーブが開発した二次元コードの一種で、バーコードと比較して大容量のデータを収納することが可能です。これにより、チラシ・ポスターやディズニーリゾートでの入園など日常で目にする機会も増えました。
そしてそれだけでなく、QRコードはバーコードとともに、普段目にする機会のない工場の中でも活用されています!
例えば、商品の詳細情報や生産履歴などを一つのコードにまとめて在庫管理に活用したり、製造ラインの検査に活用するなど、アイデア次第で様々な活用ができるようになりました。
本記事では、その活用事例と小規模の工場での現実的な活用方法について、バーコードの活用とともに解説しました!
記事のポイント
- QRコードはデンソーウェーブが開発した二次元コードで、大容量のデータを収納可能
- 工場内では、QRコード・バーコードは商品の詳細情報や生産履歴の在庫管理、製造ラインの検査などに活用されている
- 工程管理において、QRコード・バーコードを利用することで複数の工程の進捗状況をリアルタイムで把握し、効率的な作業進行が可能
- QRコードとバーコードの技術は、IoTやAIとの連携を通じて、さらなる効率化や新たな利用シーンの発展が期待される
- QRコードの活用事例
- QRコードとバーコードの比較
- バーコード活用の具体例:町工場専用の管理ソフト<PR>
- まとめ:QRコード・バーコードは工程管理や在庫管理をはじめ、多くの工場での活用事例がある。
QRコードの活用事例
工程管理
工程管理は、工場、ひいては製造業全体でQRコードを有効に活用できるポイントです。
QRコードを読み取ってから作業開始することで、複数工程あるような作業でも現在どの工程なのか管理者側から把握しながら仕事を進めることができます。
また、客先から製造の進捗状況について質問があったときなども、現場に確認することなく、営業担当者がすぐに回答することができるようになります。
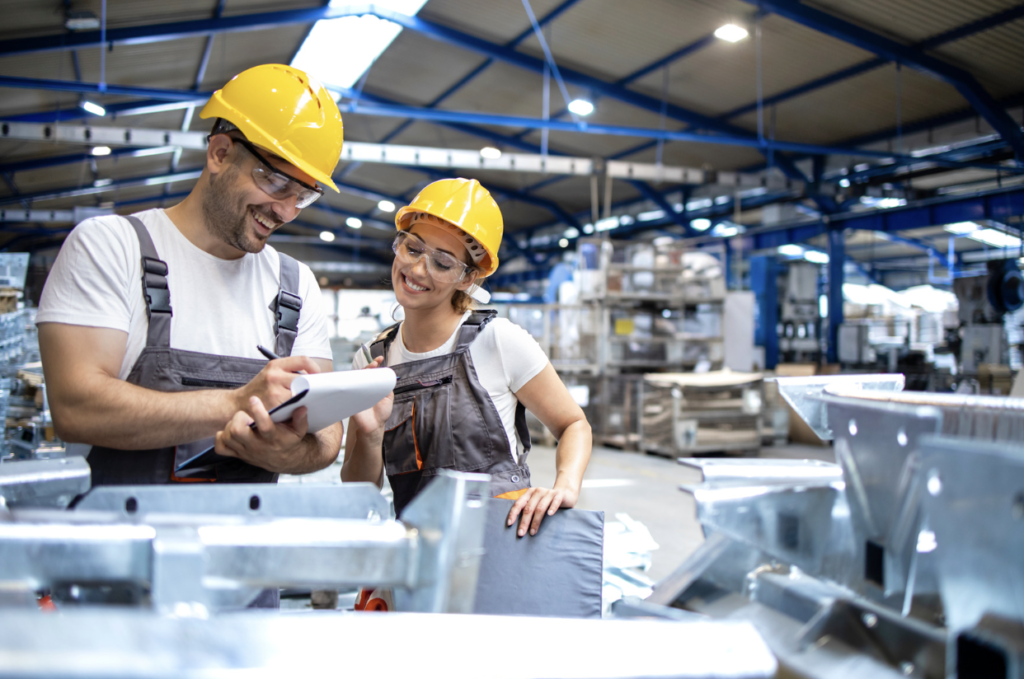
在庫管理
特に小規模の工場に多いかと思いますが、商品の在庫を長期間管理することが多く、必要なときに在庫を見つけられなかったり、在庫があるかどうかの確認に時間がかかるという問題が起こりがちです。
そんな場合も、在庫にQRコードを貼り付けた上で管理することで、すぐに在庫があるかどうかの確認ができ、場所も把握することができるため、ものを探す必要がなくなります。
在庫のQRコードを読み込めば、客先や制作日、ロットナンバー等の情報を入れておくことで、似た製品であっても取り違いをすることはありません。
さらに比較的規模の大きい工場では、原料の入庫時から使用時、そして製品としての出庫時までの流れを一貫して追跡することが可能となり、無駄やミスを大幅に削減することができます。
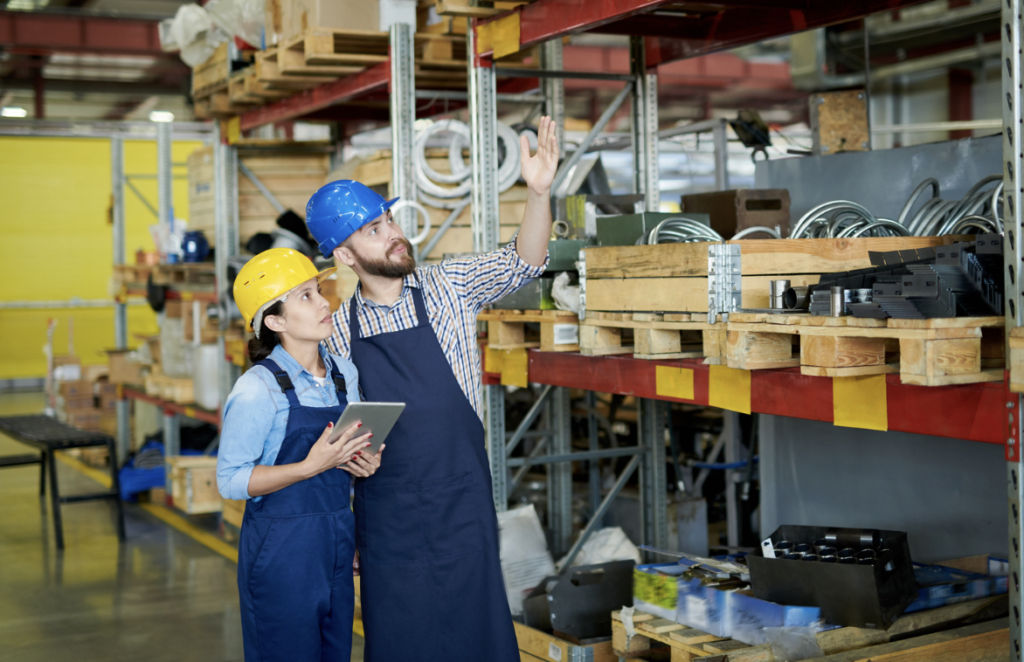
その他にもこれだけの活用事例が!ミス削減にも大きく貢献。
他にも下画像のように、入荷から始まり、部品入庫、部品ピッキング、部品投入、工程管理、梱包、製品入庫、製品ピッキング、棚卸し、備品管理など、様々なタイミングで活用されています。
QRコードの生みの親であるデンソーウェーブの公式HPに掲載されていたものだけでこれだけの種類の活用方法があることが分かります。
特に規模の比較的大きい工場で目立つ活用方法が、部品・製品の入庫、ピッキング等を管理するものです。ヒューマンエラーによるトラブルは、製造業において大きな損失をもたらすことがあります。しかし、QRコードの導入により、これらのミスを未然に防ぐことができるようになりました。
QRコードの活用は、部品入庫のような製品の製作前段階から始まり、工程管理のように製作中も活用され、製作後も在庫管理で活用。やろうと思えば製造業の全ての段階で活用できることが分かりますね。
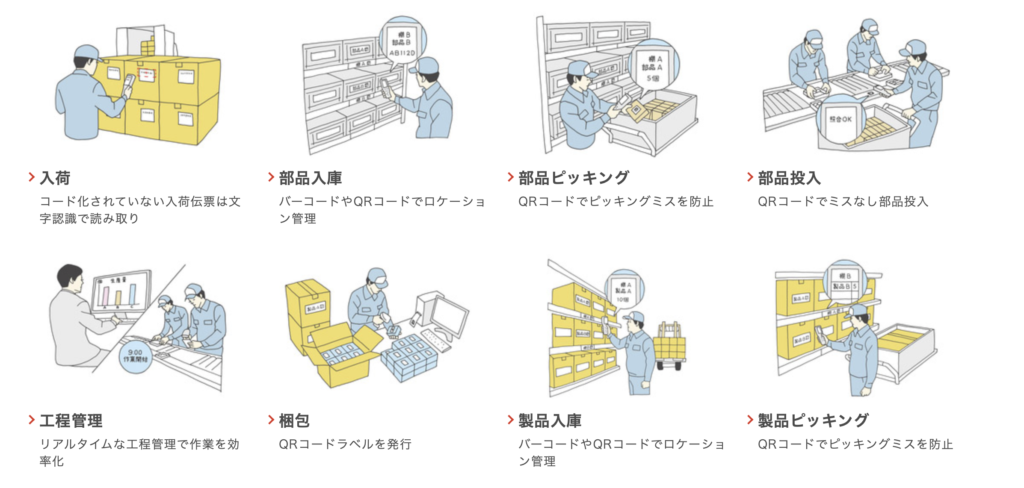
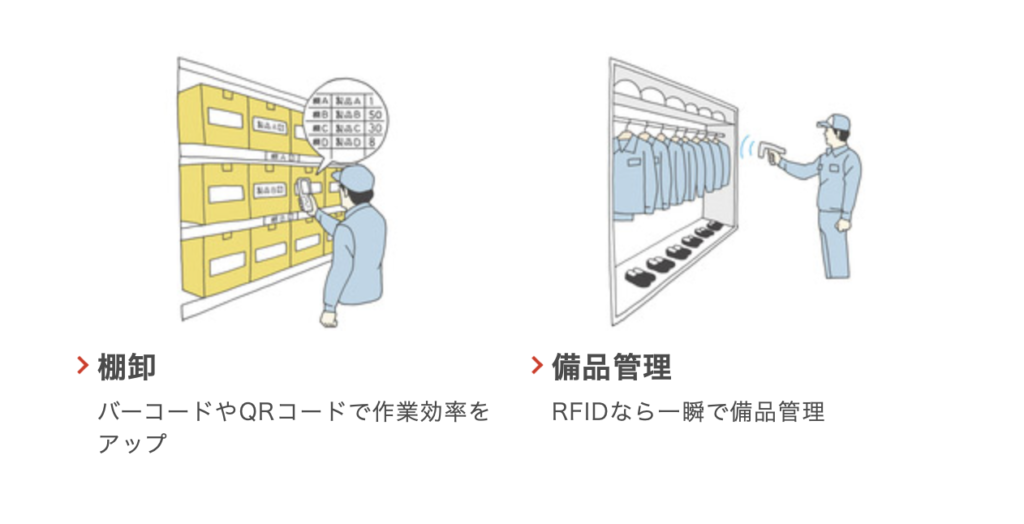
QRコードとバーコードの比較
バーコードとQRコード:工場における違いと活用点
工場で使用するにおいて、QRコードとバーコードにはそれぞれにメリットがあります。
QRコードとバーコードの違いは以下のとおりです。
スキャンの角度
バーコードは水平方向にのみスキャンが可能ですが、QRコードはさまざまな角度からのスキャンが可能です。また、QRコードはスマートフォンでも簡単にスキャンできるため、より柔軟な利用が可能となっています。
情報量
QRコードは、バーコードより記録できる情報量が圧倒的に多いです。
その差はなんと200倍。
QRコードが記録できる最大データ量は、数字のみなら7089字、英数字が4296字です。
これだけの差が生じる理由は、従来のバーコードが1方向にしか情報を持たないのに対し、QRコードは縦・横の2方向に情報を持つためです。
読み取り端末の価格
バーコードはQRコードより歴史があるため、読み取り端末が広く普及しています。
そのため、読み取り端末の価格がバーコードは1500円〜6000円くらいなのに対し、QRコードは3000円〜12000円と、大きく価格差が開いています。
専用端末を使った場合の導入のしやすさがバーコードのメリットといえますね。
スマホでの活用のしやすさ
スマホでのQRコードの読み取りは日常にも浸透し、自分のスマホで活用することに慣れている人も多いです。
一方でバーコードはスマホでの読み取りも可能ですが、日常で行う機会はかなり少ないです。
そのためこの点に関してはQRコードにメリットがありますね。
とはいえ工場内では専用端末を使用するため、従業員が自分のスマホを活用することもほぼないかと思います。
アイデア次第では、会社用のスマホを用意してQRコード読み取り端末とし、さらにアプリと連携することも可能になります。
バーコード活用の具体例:町工場専用の管理ソフト<PR>
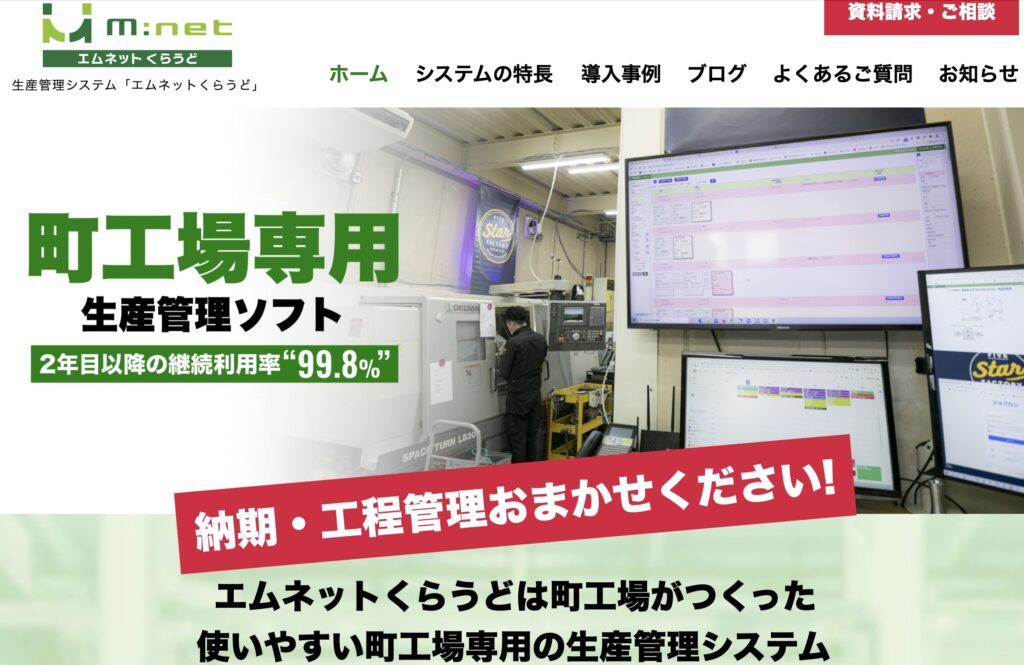
「小規模な町工場で予算は少ないけど、バーコードを活用しながら仕事を効率化したい」
そんなニーズに答えたのが日本ツクリダス社のエムネットくらうどです。
当サイトからも自信を持っておすすめできる、評判の良い高コストパフォーマンスの管理システムです。
エムネットくらうどはこんなソフト
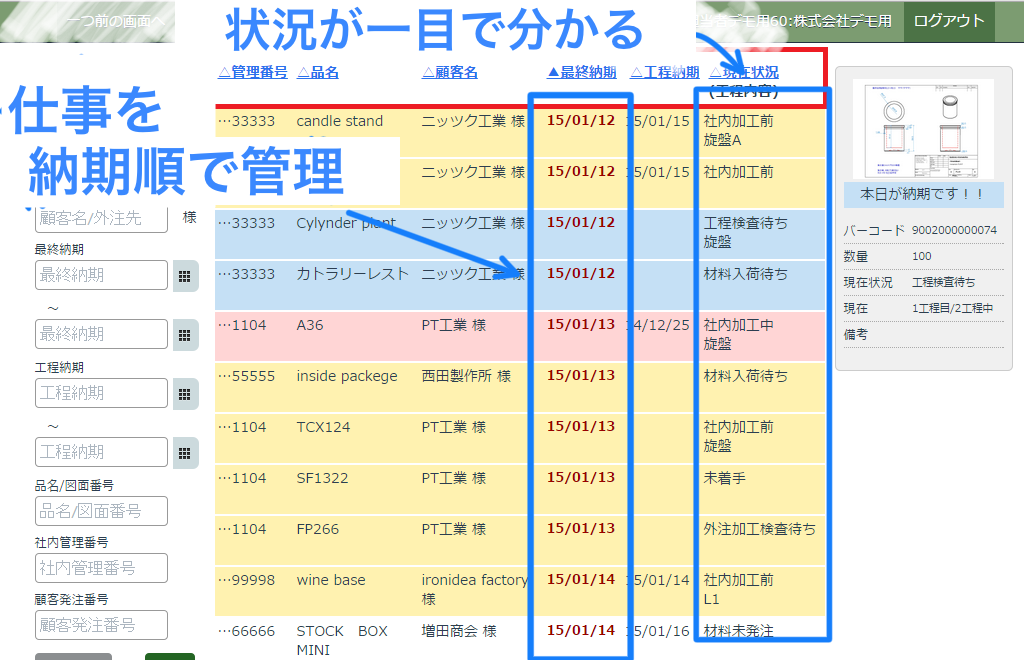
上図のような、加工品を納期順で管理する表を作成し、焼入れ等の後工程の進捗状況や、色分けによる納期の切迫度を視覚的にリアルタイムで管理することができます。
この表は図面等の情報にも紐付いており、クラウド上のシステムなので事務室からはもちろん、スマホなどで出先からも確認することができます。
とにかく簡単に使えることが特徴で、管理ソフトに慣れていない職人さんでも入力はバーコードを使って簡単に行えます。
そして何より安い!他商品と比べて圧倒的なコストパフォーマンスです。
バーコードの活用
本記事のテーマの一つである、「バーコード」が存分に活用されているのがエムネットくらうどの特徴の一つです。
必要な部分以外はシンプル・低コストにこだわった管理ソフトですので、あえてQRコードでなくバーコードが使われています。
バーコードを図面に貼って管理
入力した案件(図面)ごとの情報は、バーコードに紐付いています。
案件ごとのバーコードは簡単に発行、印刷ができるため、バーコードを図面に貼っておくだけで案件の管理が可能です。
図面に貼ったバーコードを読み取ることで、発注者や納期といった、入力した情報が確認できるようになっています。
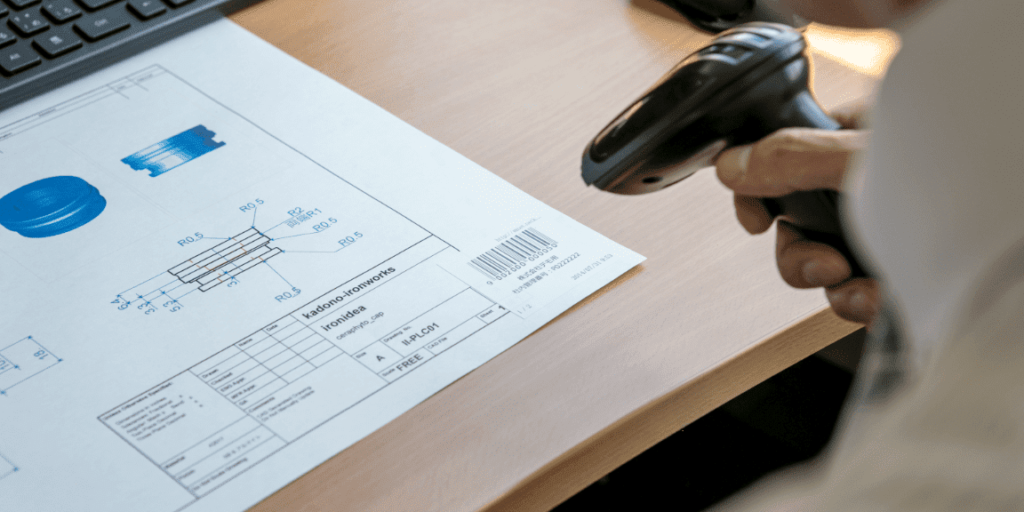
図面情報の入力
エムネットくらうどは案件の入力作業が最小限で済むように考えて作ってあるため、もともと入力作業は楽なのですが、バーコードを使うことでさらに省力化しています。
下画像のようなバーコード表を入力に活用することで、手で打ち込む労力がかからないよう工夫されています。
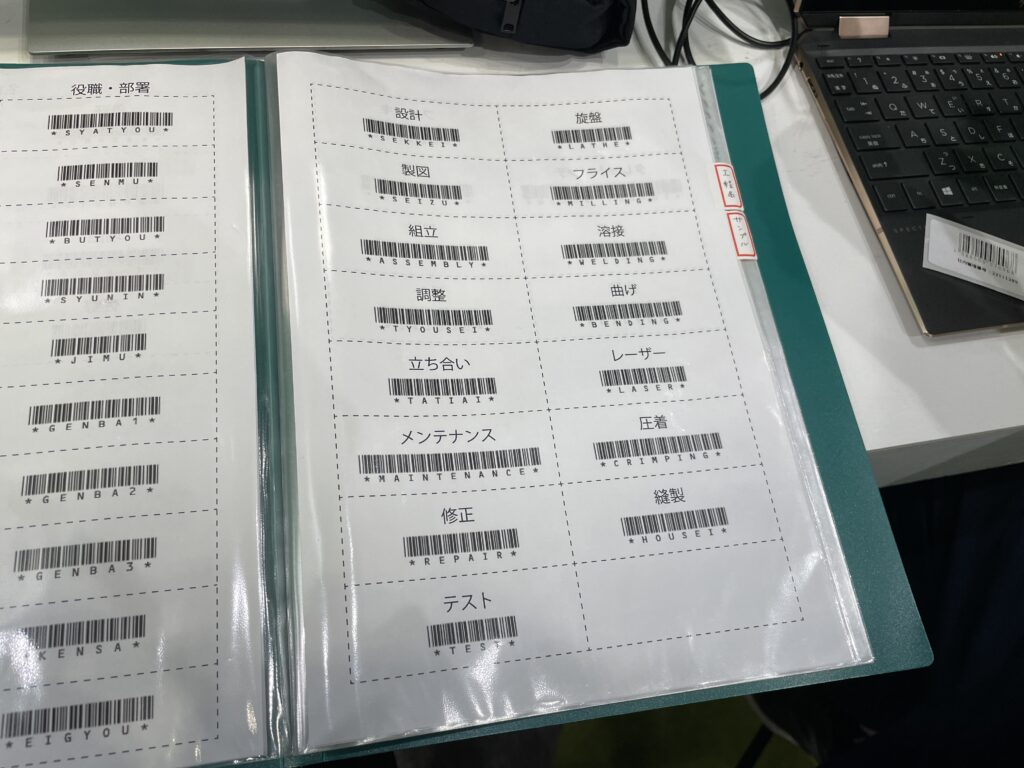
作業開始・終了時間の記録
例えば図面の加工を始めるとき、図面のバーコードを読み取って、さらに自分の名前のバーコードを読み取ることで作業開始時刻の打刻が簡単にできます。加工完了時も同様です。
簡単な打刻作業で、作業者の手を止めることなく加工時間を把握し、見積もりなどに活用することができます。
バーコードを在庫に貼って在庫管理!
図面と同じように、製品在庫にバーコードを貼っておくことで、その在庫がどのお客さんからの仕事で、どの図面を誰が何時間かけて作ったものか、その他保管場所も含めて全て記録しておくことが可能です。
「この在庫、納め先どこだっけ?」「あの在庫どこに片付けた?」といった、非常に無駄な「探しもの時間」がなくなります。
工場のバーコード管理のメリット
工場でバーコード管理をするメリットは、入力の簡略化、そして定型化です。
日本の製造業は古い体質の会社が多く、管理ソフトを導入するとなった際に精神的なハードルが高いです。経営者が良くても従業員が賛成してくれないということが起こり得るんですね。
そのため、エムネットクラウドでは導入のハードルを下げるためにバーコードで可能な限り入力が簡略化されています。
加工開始、終了もバーコードを読み込むだけ。難しい操作は全く無いため、従業員の技術者にとっても、むしろこれまでの紙での管理から開放されるメリットが出てきます。
他にも、バーコードには簡単に印刷できる、図面以外のものにも貼れる、そして安いというメリットもありますね。
バーコードの活用前後の変化
バーコード活用の代表として、エムネットくらうど様HPより、導入した会社へのインタビューを一部掲載します。
経営者の生の活用事例なので、管理ソフトを導入する際のイメージが大変湧きやすくなります。
その他のインタビューについてもこちらのURLで数多く掲載されています!
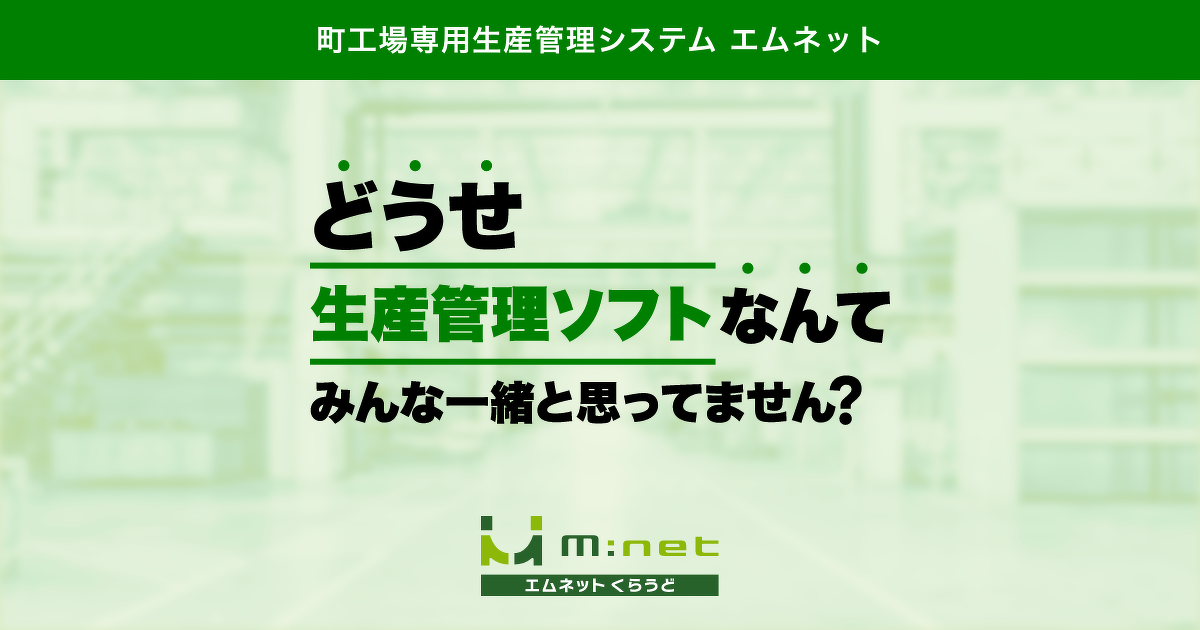
産業機械をはじめ、製鋼所向けの設備、自動化・省力化設備、各種機械の設計から、材料の購入、溶接、加工、組立まで一貫して行っている延行機工株式会社様。
今回は、そんな延行機工株式会社の宮原社長に、エムネットくらうどを導入しようと思ったきっかけや決め手、実際に使ってみた感想をインタビューさせていただきました!【導入のきっかけ】“利益”と“現場”を見える化したい
ー 今エムネットでどんなことを管理していますか?
今は、特に“原価の管理”に力を入れています。
これまで「この仕事って利益出てるの?出てないの?」って部分が、はっきり見えていなかったんですよ。エムネットくらうど公式 https://mnet.netkojo.biz/voice/昔は「何月何日に誰が何分作業をやったか」みたいな作業日報を手書きで書いてもらってたんですけど…はっきり言って正確に集計するのって難しいですよね(笑)
きちんと利益を把握したかったので、システムを入れたらそこを徹底できるようにちゃんとデータを取ろうと考えていました。
ー コスト面を見える化したかったというイメージでしょうか。
そうです。特に、弊社はアッセンブリーなので、コストを算出しにくいという点があったので尚更ですね。
特定の部品だけであれば、まだ計算しやすいと思うんです。
部品1つ作るときにかかる時間などは計測しやすいし、それに対して1つあたりいくらの利益が出たのかも算出できます。ただ、アッセンブリーだと部品点数も何百点になるし、最終的に組み立てて機械を作って…と作業していると、それぞれどれだけの工数がかかったのかってことが集計しづらいんですよね。
ー 確かに集計がきちんとできていないと、正確な原価は計算できないですもんね。
そうそう。
細かくデータを取れていたわけじゃないので、利益の残るもの、残らないもの(赤字になってしまうもの)がはっきり判別できませんでした。それぞれの理由もきっちり説明できませんでしたし。それは経営的に良くないよね、と常々感じていたので、システムを使って利益やコストを見える化したいという想いが強くありました。
ー システムでは原価の管理をメインに行う予定だったのでしょうか。
他にも、「現場が見えない」という問題をどう解決するべきかも考えていました。
当時は、事務作業をやりながら、僕も現場で作業してたんですよ。
現場で機械を動かしつつ、他の作業もしながら事務仕事もやって…といった具合に。そのときは、1日中じゃないにしても定期的に現場に行くので、「あのスタッフは今この作業をしてるんだな」というふうに、現場の状況はすぐに見えていました。
でも、いずれは経営に集中するために、事務所側の仕事に専念しようと決めてたんです。
そうなると、「自分が現場にいなくても現場の状況を見えるようにしておく必要がある」ので、そのための環境を整えたいという想いもありましたね。アナログ仕事をいかにデジタル化するか悩む日々
ー システムを入れるにあたって、どのような課題がありましたか?
「事務所側のアナログ部分をどうやってデジタル化していくか」が大変でした。
仕入れの記録などもずっと手書きで付けてたし、何かを購入するときの発注や協力会社さんへの依頼なんかも全部アナログでやってて…。
だから、「前回の実績が見たい」って言うと、このファイル(写真のファイル)をガサっと渡されて「はい、どうぞ」みたいな(笑)
原価なんかも、ここに書かれてるやつを全部拾い上げて計算しないといけなかったんですよ。当時は経理も全部手書きでやっていたし、集計1つするだけでも大変でしたね。
それらを解決するために必要だったのが、工程管理と原価管理をシステム化することだったわけです。
だから工程管理と合わせて、日々の日報収集もできるようなシステムを探していました。【導入の決め手】現場が使い続けられるカンタン・シンプルなシステム
ー システムを探すときに意識したことはありますか?
「現場が続けられるかどうか」ですね。
展示会などで色々なシステムを見ていると、高機能なんだけど凝りすぎてるものが多かった印象があります。デジタルデータを使えるかどうかって、きちんとデータを入力できてることが前提になると思うので、まずは「現場の作業者が無理なく使い続けられる(データを入力し続けられる)かどうか」が大事なんですよ。
高機能なシステムを導入しても、使いこなせなかったらもったいないじゃないですか。
だから“なるべくシンプル”なものを探してましたー 確かに先ほども「正確にデータを取ることが大事」とおっしゃってましたもんね。
それに関しては、日本ツクリダスさんが実際社内で使ってるのが大きかったですよ。
社内の人、それも作業者の人が使ってても継続して使えるシステムってことが伝わったので。同じような機械を使って、その管理を実際に社内の人たちがエムネットを使って実践して、かつ継続できてて…って部分に安心感がありました。
ー バーコード1つで管理を進めていけますからね。
あと、導入にあたっては料金が安いのも判断材料になりましたよ。
例えば、やりたいことがたくさんある場合に、1000万円程かけてシステムを組むこともできますけど、それが機能しなかったら元も子もないですよね。でも、エムネットの料金は「ダメだったらしょうがないか」と割り切れるぐらいなので。
とりあえずやってみよう、と試験的に始められる印象がありました。あっ、あとは「社長のキャラクターが面白かった」というのもちょっとありますね(笑)
ー そのお言葉は必ず伝えておきます、ありがとうございます(笑)
【導入後の感想】生産管理を徹底すれば売上につながる
ー 実際、導入前にやろうと思っていたことはできるようになりましたか?
そうですね。集計もちゃんとできるようにやったし、こんな感じでエムネットから取り出してきたデータを応用して、原価管理表も作りました。
ー え!これ全部エムネットのデータを活用してるんですか?!
(宮原社長が見せてくださった表には、原価だけでなく、機械ごとにかかったコストなどの情報が詳細に表示されていました。)
エムネットから取り出せるログのデータを組み合わせて、作業者の作業実績を集計してきてるんですよ。
これを使えば、バーコードを読み込むだけで弊社の機械加工にかかる経費がいくらで、この部品の原価がいくら…みたいな情報がすぐに出せるんです。つまり、利益がいくら出てるか、もしくは赤字になってしまったのかがすぐに把握できるようになりました。
ー 実際、売上面でも成果につながりましたか?
ありましたよ。
利益の出てるもの、赤字のものが見えるようになれば、赤字になるような仕事はできるだけお断りしていかないといけないじゃないですか。そうやっていくうちに、エムネットを導入してから2年ほど経ちますが、粗利率も経常利益も着実に上がってきました。
エムネットくらうどは、職場環境の改善にも
実はシステムを導入するときにもう1つやったことがあって、それは“年間カレンダーの作成”です。
毎月必ず、3連休以上の休暇を取れるようにして、年間休日もドンっと増やしました。その分、労働時間が減るんで、普通なら給料も減っちゃうじゃないですか。
でも、そのときに「休日増やしても給料は減らさない」って約束したんですよ。その代わりにこういうシステムを始めるから協力してほしいと伝えました。
「やらなくても良い残業や休日出勤を減らそう。短い労働時間で利益が上がる組織を作ろう」ってね。ただ、それを実践するためには、やっぱり第一に利益がちゃんと確保できていることが大事で、そのためにも現状を知る必要があったんです。
だから、システムへの登録などはちゃんとやってもらう必要があるから…それで利益がちゃんと出れば、無理に働かなくても良いから!というふうに、従業員にシステムへの理解を促していきました。
ー エムネットが職場環境の改善にもつながったんですね…!
いや、ほんとその通りですよ。
そこを心がけていると、若い世代の人たちも働き続けてくれますし。僕は「途中でタバコを吸おうが、コーヒーを飲もうが、設定している納期通りに仕事を仕上げてくれたら何にも言わない。その納期にちゃんと製品が仕上がってるのに赤字…というのは経営側の責任やからね。」と伝えています。
現実は何でもかんでも予定通りいくわけではないってのが製造業のジレンマなんですけど、それを少しでも解消するために、こういう管理をしていくことが大事だと考えています。
ー よく考えると、休みを増やしたけど売り上げは上がってるってことですよね?
そういうことです。休みを増やしても売上が上がるって面白いですよね。
それだけ「実態を見えるようにすること」って大事なんだと思います。これってダイエットとかも一緒の考え方ではないかと。
僕自身、体型をキープするために毎日体重を測って記録をつけてるんですけど、その日の体重によって今日は食べられる、今日はやめておこうってことを考えてます。経営も一緒で、数字を見ていないと利益の出ない仕事でも「まぁ今回は良いですよ」と受けてしまうんですけど、損することが目に見えると、「ちゃんと交渉しよう」とか「ここは折れられないな…」って部分が見極められるようになりますから。
やっぱり「数字を見ること」って大事なんですよ。
エムネットくらうどを導入して、まさにそれが可能になりました。業務を効率化するための秘訣は「探し物の時間をなくすこと」
ー 見える化することって業務を効率化するうえで大切なことですね。
そのとおりですね。
あっ、最後に、生産管理システムを導入して感じたメリットをもう1つ。
それは「探し物の時間がなくなる」ってことだと思います。会社で一番の無駄は「探すこと」なんですよ。
分厚い書類の束をめくって資料を探している時間などがあると、それってすごくもったいないんですよね。
だから、ファイリングしてパソコン上でもフォルダを作って…といった具合に管理すると一気に業務効率が上がるんです。フォルダが増えていくとややこしくなるかもしれないんですけど、エムネットを使えばすぐにフォルダも見つけられるし、集計も検索も一瞬でできて便利だなと思いますね。
そんな観点も持ちながら、これからもエムネットを使いこなしていきたいと思います。
インタビューを終えて
延行機工株式会社様は、エムネットくらうどで徹底的に「原価管理」と「工程管理」を行っておられました。
特に、原価管理に関しては、エムネットくらうどから取り出した実績データをエクセルに取り込み、独自の原価管理表を作成されているのが印象的でした。「休日を増やしても、売上は上がった」とおっしゃっていたように、原価も工程も見える化することで、これまで気づけなかった経営の課題が見つかるかもしれません。
もし「原価や工程をはじめ、社内の状況がいまいちよく見えない」というお困りごとがあれば、一度お気軽にご相談ください!
QRコードとバーコードの未来展望
デジタルと現実をつなぐ役割を担うQRコードとバーコードの技術は、今回ご紹介したエムネットくらうどに代表されるように、今後も進化していくことが期待されます。
特に、IoTやAIとの連携により、さらなる効率化や新たな利用シーンが生まれることが予想されます!
AIの分野では、下画像のようにイラストをQRコードとして読み取れる画像生成技術も開発されているそうです。工場にとって、今後どんな利用の仕方が実用化されていくのか楽しみですね。
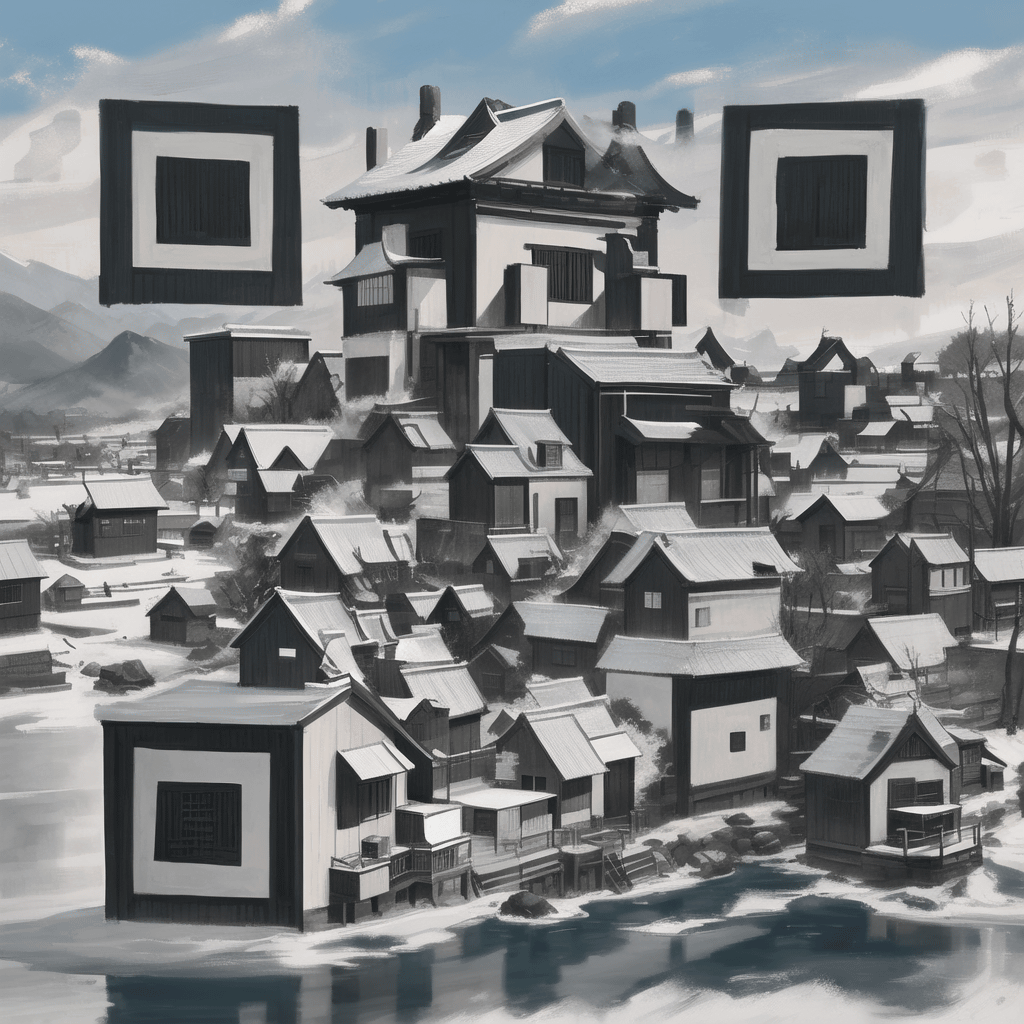
まとめ:QRコード・バーコードは工程管理や在庫管理をはじめ、多くの工場での活用事例がある。
- QRコードはデンソーウェーブが開発した二次元コードの一種
- QRコードとバーコードは工場内での在庫管理や製造ラインの検査に活用
- 工程管理ではQRコード・バーコードを用いて複数工程の進捗状況を把握
- 在庫管理においてQRコード・バーコードを利用することで迅速な確認と取り違いの防止が可能
- QRコード・バーコードの導入によりヒューマンエラーによるトラブルを未然に防ぐ
- 製品の製作前段階から製作後の在庫管理まで、製造業の全ての段階でQRコードが活用可能
- バーコード管理のメリットとして入力の簡略化と定型化が挙げられる
- エムネットくらうどは小規模な町工場向けの高コストパフォーマンスの管理システム
- バーコードを活用することで、加工開始から終了までの管理が簡単に
- IoTやAIとの連携によりQRコードとバーコードの技術の進化が期待される