この図面、30°角度つきのH7公差の部分はどう加工する?
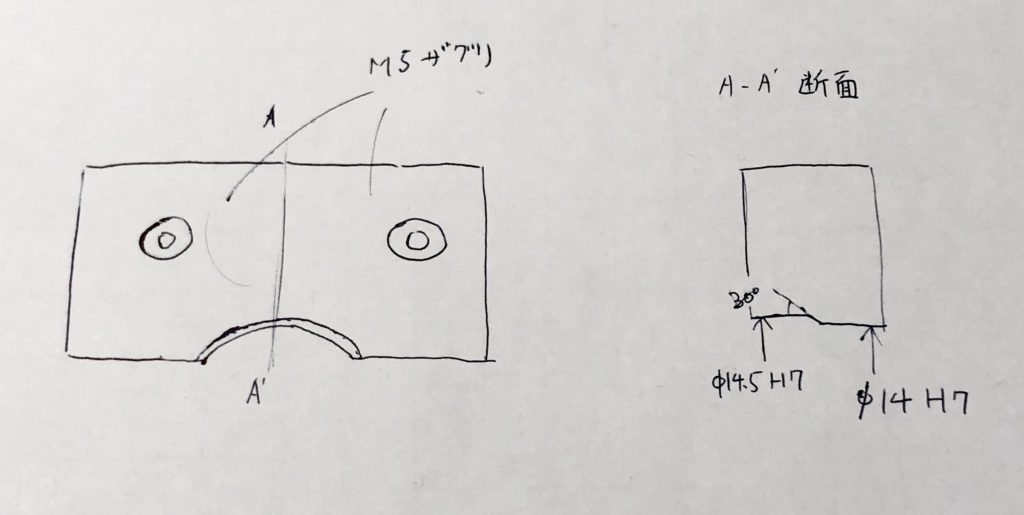
こんな形の製品を加工する際、マシニングでエンドミルを使った加工だと30°の部分が加工できません。
そのため、旋盤を使って加工します。
しかし普通のNC旋盤ではつかめないですよね?
H7公差は測定不能!! なので先に別のものを削っておく
半円の製品となると、栓ゲージもシリンダーゲージも使えないため、H7公差を測定することができませんね。
そのような場合は、先に通常の丸棒を削って公差を合わせておきます。
私は45Cの黒皮材にφ13のキリ穴をあけ、内径バイトでφ14に削り、栓ゲージで公差をあわせました。
そのとき、内径仕上げ加工は2回行うようにしたほうが良いです。
内径バイトや丸棒の逃げで寸法が微妙にずれてしまうことがあるのですが、2回仕上げることで、そのような寸法のずれを防ぐことができます。
面盤を使って旋盤で加工する!
そんなときは面盤を使います。
私は今回、φ270で厚さ20mmの面板を使いました。絵で書くとこんな感じになります↓
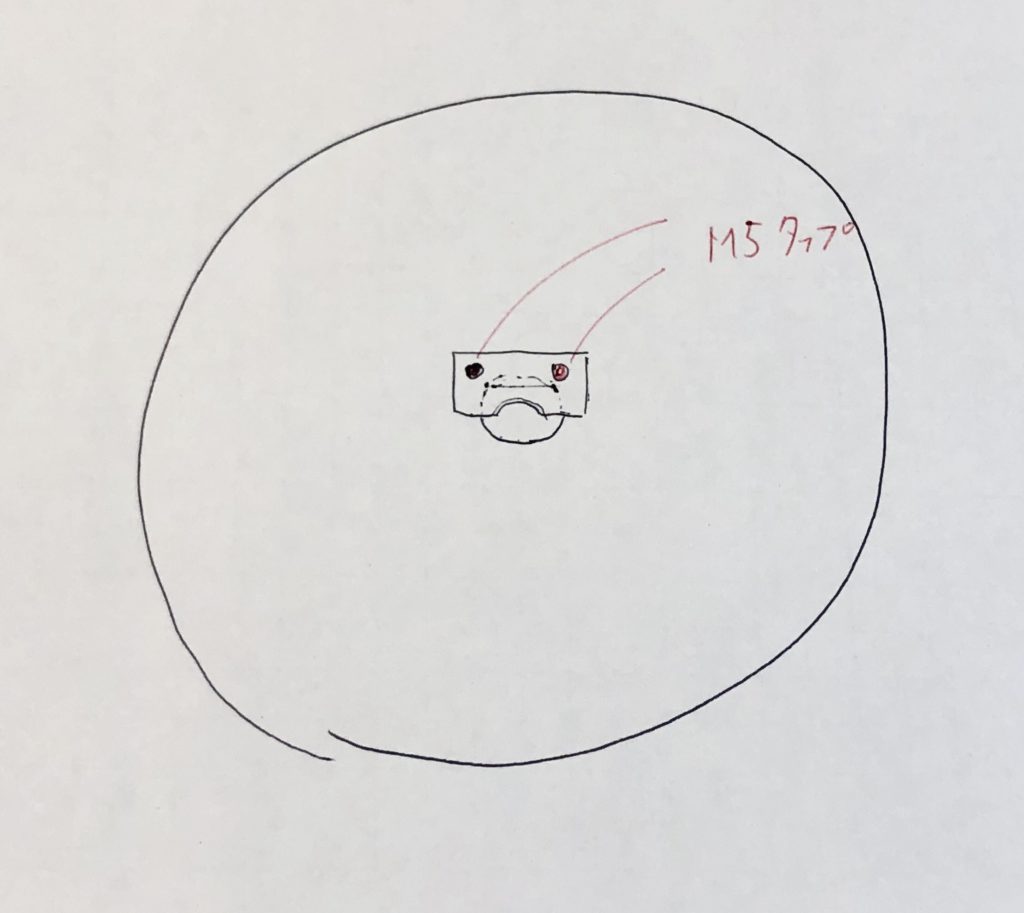
マシニング加工の半円部分は荒加工で終わらせておく
まず製品のマシニング加工は、半円の部分は荒加工のみで終わらせておいて、その他の部分は普通に加工します。
穴位置を計算し、面盤にタップを立てる
そして、製品半円の円中心と面盤の円中心が合うように、マシニングで面盤にタップをあけます。(旋盤で線をつけて、ボール盤で開けることも可能ですが、マシニングで穴位置を正確に加工したほうが旋盤での芯出しがやりやすくなります。)
面盤に製品を固定し、芯出しを行う
それからボルトで面盤と製品を固定し、芯出しをしてやります。
このとき、ボルトがザグリのある側だったら問題ありませんが、そうでない場合必ずワッシャーをかませるようにしましょう。 そうでないと製品にボルトの傷がついてしまいます。
芯出しは、てこ式ダイヤルゲージを半円の部分に使って行います。ボルトをゆるめに締めておいて、プラスチックハンマーでダイヤルゲージの目盛りが動かなくなる位置まで叩いて調節しましょう。
切削条件、特にapは落として加工する
調節が終わったら、ボルトを本締めして加工開始です。
面板でのボルト固定なので、切削不可をかけると動いてしまう可能性があります。なので、切削条件を落として加工しましょう。
切削時間はそうかかりませんので、切り込み量を0.25mm程度にしておけばまず動くことはないでしょう。
そして、断続切削になりますので、荒加工は断続切削用のチップを使うことを忘れずに。
それから、丸棒の試し削りで2回仕上げたのであれば、本番の加工の際も2回仕上げるようにしましょう。
加工完了!3次元測定器があれば測定もできる
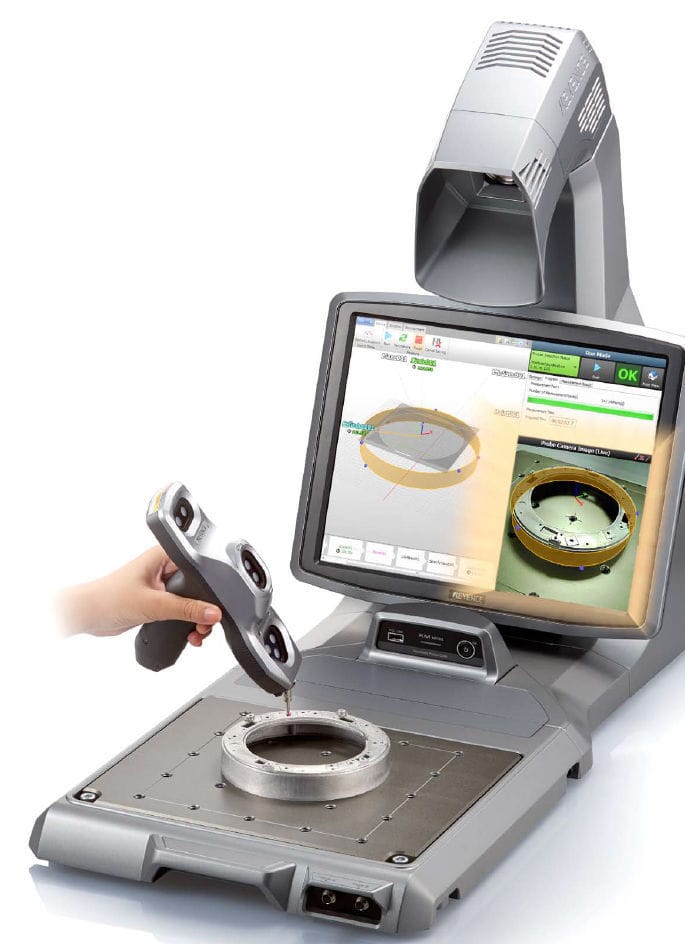
勤務先にはコレがあるので、半円のワークでも公差に入っているか測定することができます。
このような特殊な加工をした場合にはこういう測定器は便利です。
他にもこんな2つの加工方法がある
今回はマシニング加工をすべて終えてからH7公差を仕上げる方法で加工しました。
ですが2つ目の方法として、丸の状態から先に旋盤加工を行い、後からマシニングセンタで製品の形状にくり抜く方法もあります。
この方法であればひずみがでる可能性はあり、マシニング加工に時間はかかってしまいますが、H7公差をシリンダーゲージや栓ゲージで正確に測定することができます。
最後に3つ目の方法ですが、真四角の板を面盤でつかみ、真ん中に旋盤でH7公差を加工してからマシニングセンタで製品のかたちに削って残りを加工する方法があります。
この方法であれば円盤から削り出すよりも材料が小さくなるため、マシニングで形状をつくった際のひずみを小さく抑えられる可能性が高いです。
コメント