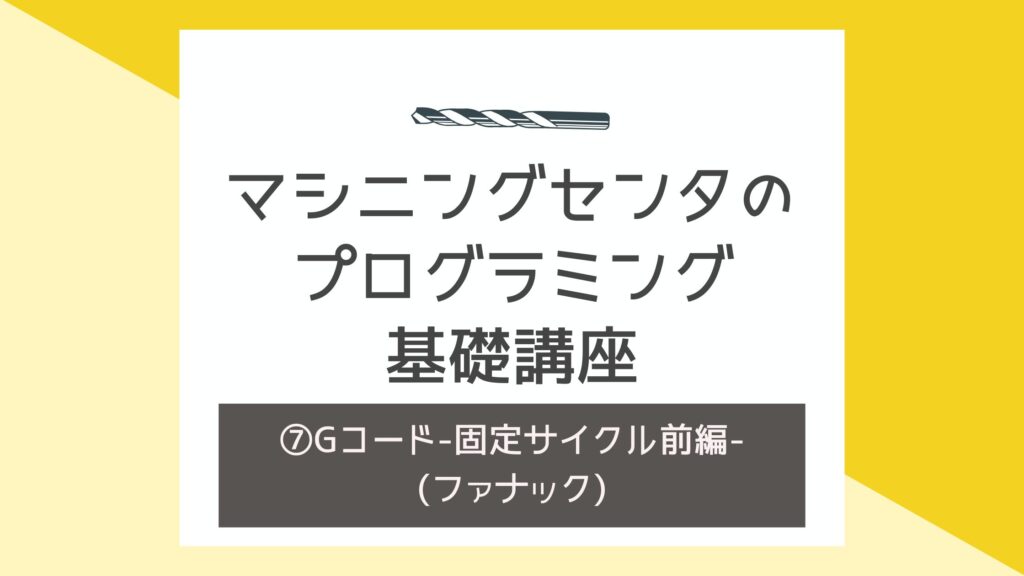
前回の講座では、G90や、G01〜G04といった最も基本的なGコードについてご紹介しました!
今回は、応用的なGコード「固定サイクル」についてご紹介します。
CNC加工では、穴あけやタッピングなどの作業を効率的に行うために固定サイクルが活用されます。固定サイクルを使用することで、プログラム作成が大変楽になり、加工時間も短縮できます。
応用的とはいっても、加工のたびに使用するといっても過言ではないほど使用頻度が高く、重要なコードになります。
また、私の実務経験を踏まえ、実際に現場でどのように使われるのか、どのサイクルを優先的に覚えるべきか についても触れています。
これからCNCプログラムを学ぶ方や、より効率的な加工を目指したい方の参考になれば幸いです。
固定サイクルとは?
ドリルによる穴あけ(ドリリング)、タップによるねじ立て(タッピング)、ボーリングバーによる(ボーリング)など、通常は複数のブロックで構成される一連の動作を1つのブロックで指令できるようにした機能を固定サイクルといいます。
特にマシニングセンタにおける穴あけ加工は固定サイクルを使うことがほとんどです。
ちなみに固定サイクルのGコードはすべてモーダルであり、表のGコードを実行すると固定サイクルモードになります。 モーダルについては前回の講座をご参照ください!
固定サイクル一覧
まずは固定サイクルの種類をざっとご紹介します。
Gコード | 穴あけ動作 | 穴底位置における動作 | 逃げ動作 | 用途 |
---|---|---|---|---|
G80 | * | * | * | キャンセル |
G73 | 間欠送り | * | 早送り | 高速深穴あけ |
G74 | 切削送り | ドウェル…>主軸正転 | 切削送り | 逆タッピング |
G76 | 切削送り | 主軸オリエンテーション | 早送り | ファインボーリング |
G81 | 切削送り | * | 早送り | スポットドリリング |
G82 | 切削送り | ドウェル | 早送り | カウンタボーリング |
G83 | 間欠送り | * | 早送り | 深穴あけ |
G84 | 切削送り | ドウェル…>主軸逆転 | 切削送り | タッピング |
G85 | 切削送り | * | 切削送り | ボーリング |
G86 | 切削送り | 主軸停止 | 早送り | ボーリング |
G87 | 切削送り | 主軸正転 | 早送り | バックボーリング |
G88 | 切削送り | ドウェル…>主軸停止 | 手動 | ボーリング |
G89 | 切削送り | ドウェル | 切削送り | ボーリング |
固定サイクル復帰モード
Gコード | 説明 |
---|---|
G98 | イニシャル点復帰 |
G99 | R点復帰 |
固定サイクルの動作
固定サイクルのプログラムでは、工具のアプローチ位置と加工深さ、復帰位置の3点を指令する場合が多いです。
そのために、まずは以下の3つの点を理解しておきましょう!図をご覧いただくとわかりやすいです。
- イニシャル点: 位置決めの真上の位置決め点
- R点: イニシャル点から早送りでアプローチする点(穴加工の開始点)
- Z点: 加工終了点
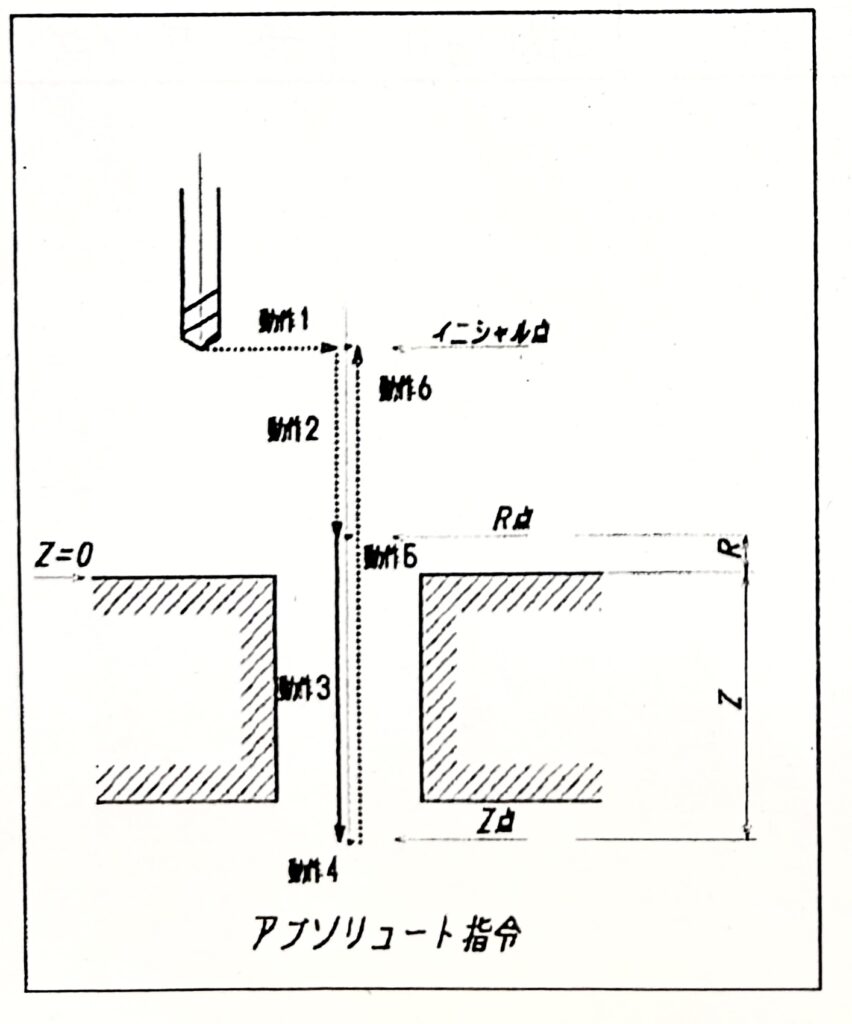
固定サイクルの動作は、以下の6つの動作で構成されています。
- 動作1: XY軸の位置決め(早送り)
- 動作2: R点までの早送り
- 動作3: 穴加工
- 動作4: R点までの早送り
- 動作5: 次穴位置までの位置決め動作
- 動作6: イニシャル点までの早送り
これらの動作を行おうと思うと、通常何行ものブロックで構成する必要がありますが、固定サイクルを使うことで、それらを1ブロックで指令することができます。
固定サイクル紹介
本項では、G73(高速深穴あけ)、G83(深穴あけ)、G81(ドリルサイクル)、G82(カウンターボーリング)、G84(タッピング) など、実務でよく使われる固定サイクルの、具体的な指令方法やその特徴について解説しました!
G73(高速深穴あけ固定サイクル)
G73は、ステップ送りによる穴あけ加工を行うGコードです。特に、深穴加工や切りくずが絡みやすい加工に適しています。一定量ずつ切り込みながら進むため、切粉を切りながら効率的に加工できます。
基本的にドリルを使って穴あけを行う際はこの固定サイクルを使用すると思っておきましょう。
G73を使うメリット
• 深穴加工時の切りくず詰まりを防止
• 1回の切り込み量を調整できるため、工具寿命と切りくず処理のバランスを調整できる
• スムーズなステップ送りにより、高速加工が可能
G73の指令方法
G73 X** Y** Z** R** Q** F** K**;
G73の各パラメータの解説
コード | 意味 |
---|---|
X, Y | 穴位置データ |
Z | 穴底位置またはR点から穴底までの距離 |
R | R点位置またはイニシャル点からR点までの距離 |
Q | シフト量(毎回の切り込み量) |
F | 送り速度 |
K | 繰り返し回数(FANUC 15Mでは「L」になる) |
G73を使用する際のポイント
シフト量(Q値)の最適設定
Q値は1回の切り込み量を示し、一般的にドリル径の1/5程度が適切とされています。大きすぎると工具負担が増し、小さすぎると加工効率が低下します。 というのが基本情報ですが、私のオススメとしては、 ハイスドリルを使用する際は常に1に設定しておくと スピードと切粉処理をバランスよく加工することができるでしょう。(φ3以下の小径のドリルについてはもっと小さい値に設定しましょう。)
深穴加工での注意点
• 穴の深さがドリル径の2.5倍以上の場合に適用推奨
• 3D(ドリル径の3倍以上)を超える穴は、適切なQ値の設定が必要
• 5Dを超える加工など、切りくずが詰まりやすい場合は、G83(深穴あけサイクル)を検討
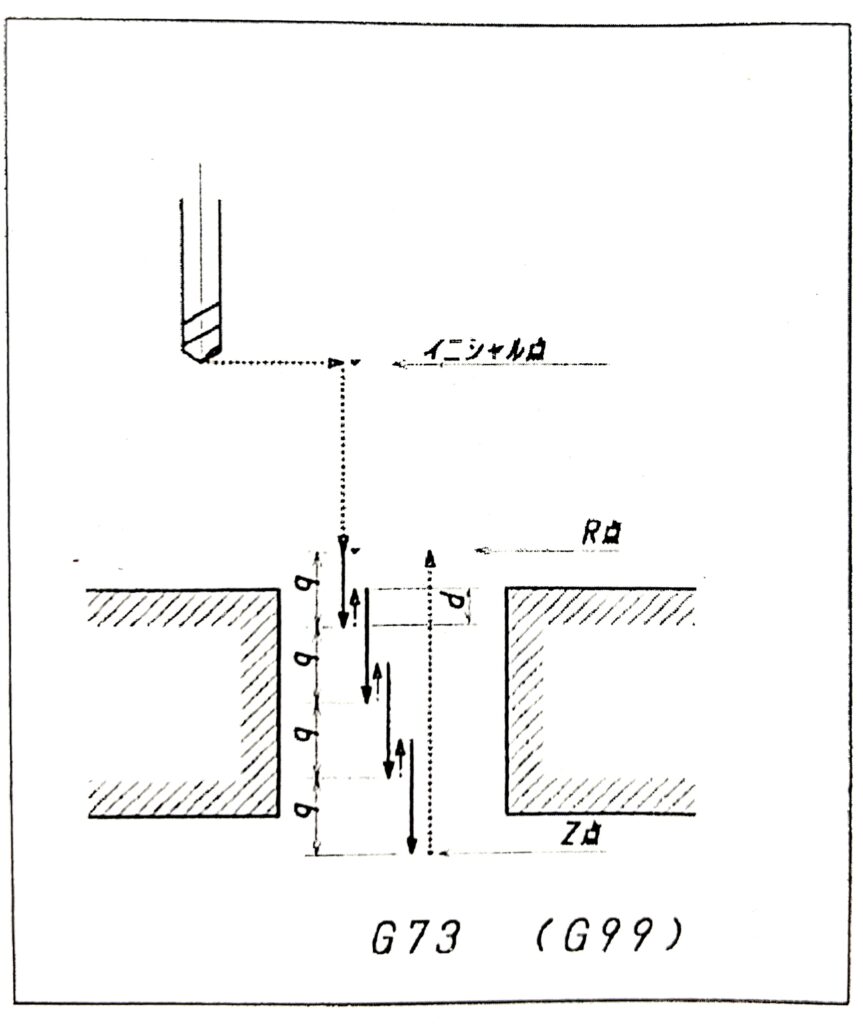
G83(深穴あけ固定サイクル)
G83は、深穴加工向けの固定サイクルで、毎回R点まで戻ることで切りくずを完全に排出するのが特徴です。G73と同様にステップ送りで穴をあけますが、G83はドリルがR点まで戻るため、クーラントがしっかり浸透し、冷却・潤滑効果が向上します。
そのため、切りくずが詰まりやすい材質や深穴加工に最適です。 ステップなしだと内部給油が必須であるフラットドリルでの加工も、G83を使えば問題なく行うことができます。
ただし、G73より加工時間が長くなるというデメリットがあります。
G83を使うメリット
• G83は毎回R点まで戻るため、切りくずの排出がスムーズ(G73はR点まで戻らず加工するため、時間短縮できるが、切りくずの排出が難しい)
• 切りくずが詰まりやすい材質(アルミ、銅など)や深穴加工、 外部給油でのフラットドリルにはG83が適している
G83の指令方法
G83 X** Y** Z** R** Q** F** K**;
G83の各パラメータの解説
コード | 意味 |
---|---|
X, Y | 穴位置データ |
Z | 穴底位置またはR点から穴底までの距離 |
R | R点位置またはイニシャル点からR点までの距離 |
Q | シフト量(毎回の切り込み量) |
F | 送り速度 |
K | 繰り返し回数(FANUC 15Mでは「L」になる) |
G83を使用する際のポイント
シフト量(Q値)の最適設定
G73と同様ですが、Q値は1回の切り込み量を示し、一般的にドリル径の1/5程度が適切とされています。同様に、Q=1と統一する形でも問題ないでしょう。
G83特有のポイント
• G83は毎回R点まで戻るため、クーラントの供給がしっかり行われる
• G83は加工時間が長くなるが、切りくずの排出能力が高い
• 切りくずが詰まりやすい材質や、5Dを超える深穴加工では、G73よりG83の方が適している
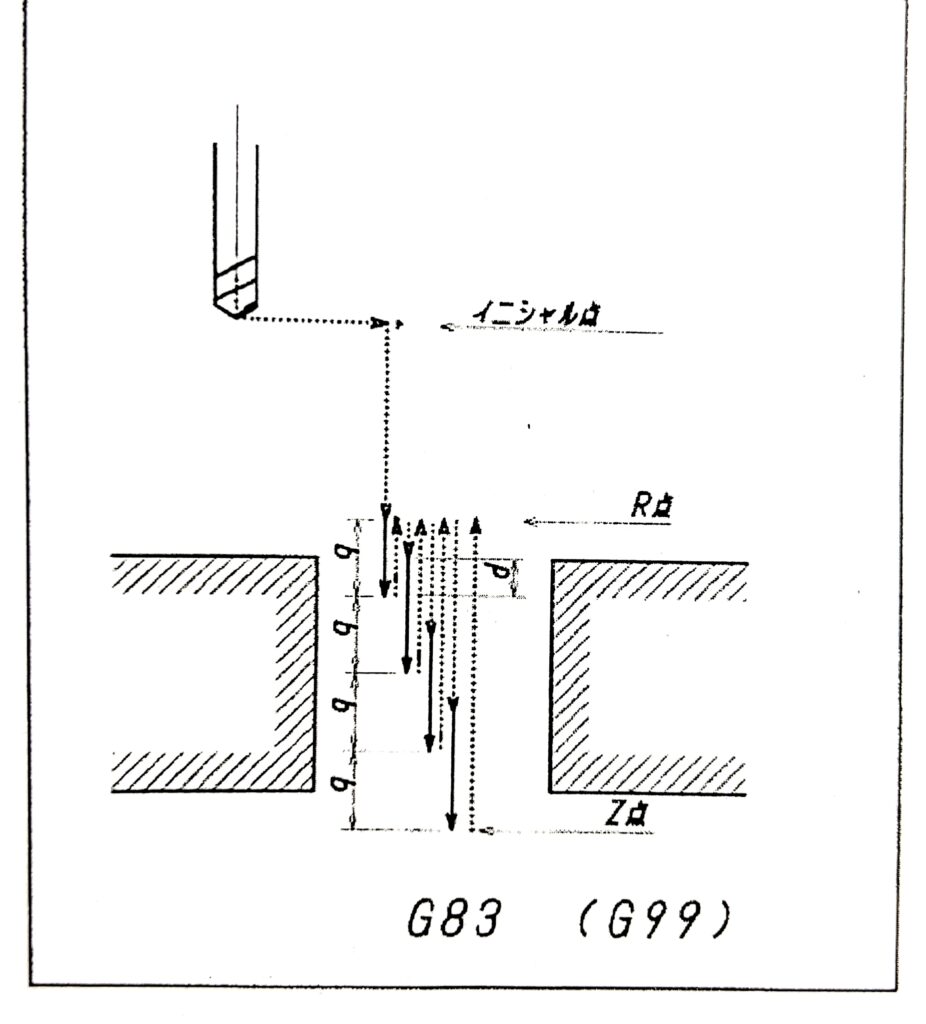
G81(ドリルサイクル)
G81は、ノンステップ送りで一気に穴の底まで工具を送る固定サイクルです。G73やG83のようにステップ送りは行わず、一定の送り速度で加工点まで進んで穴を開けるのが特徴です。
私の場合、主にセンタリング加工に使用します。
切りくずを排出できない固定サイクルのため、 よほど浅い穴でない限りは穴あけ加工にはあまり使用していません。
G81を使うメリット
• ステップがない分、加工硬化が発生しにくい → 工具寿命が伸びやすい
• 加工時間が短縮できる → 一度に穴の底まで到達するため、素早く加工可能
• センタリング加工に最適 → センター穴を開ける際に、スムーズな切削ができる
G81を穴あけ加工に使用しない理由
G81は切りくずを排出せず、加工中に切粉が詰まりやすいため、穴あけ加工にはあまり向いていません。
特に、深穴加工では切りくずが切れず、工具破損や加工不良のリスクが高まるため、実際の現場ではあまり使いません。
そのため、穴あけにはG73(高速深穴あけサイクル)やG83(深穴あけ固定サイクル)を使用することが一般的です。
G81の指令方法
G81 X** Y** Z** R** F** K**;
G81の各パラメータの解説
コード | 意味 |
---|---|
X, Y | 穴位置データ |
Z | 穴底位置またはR点から穴底までの距離 |
R | R点位置またはイニシャル点からR点までの距離 |
F | 送り速度 |
K | 繰り返し回数(FANUC 15Mでは「L」になる) |
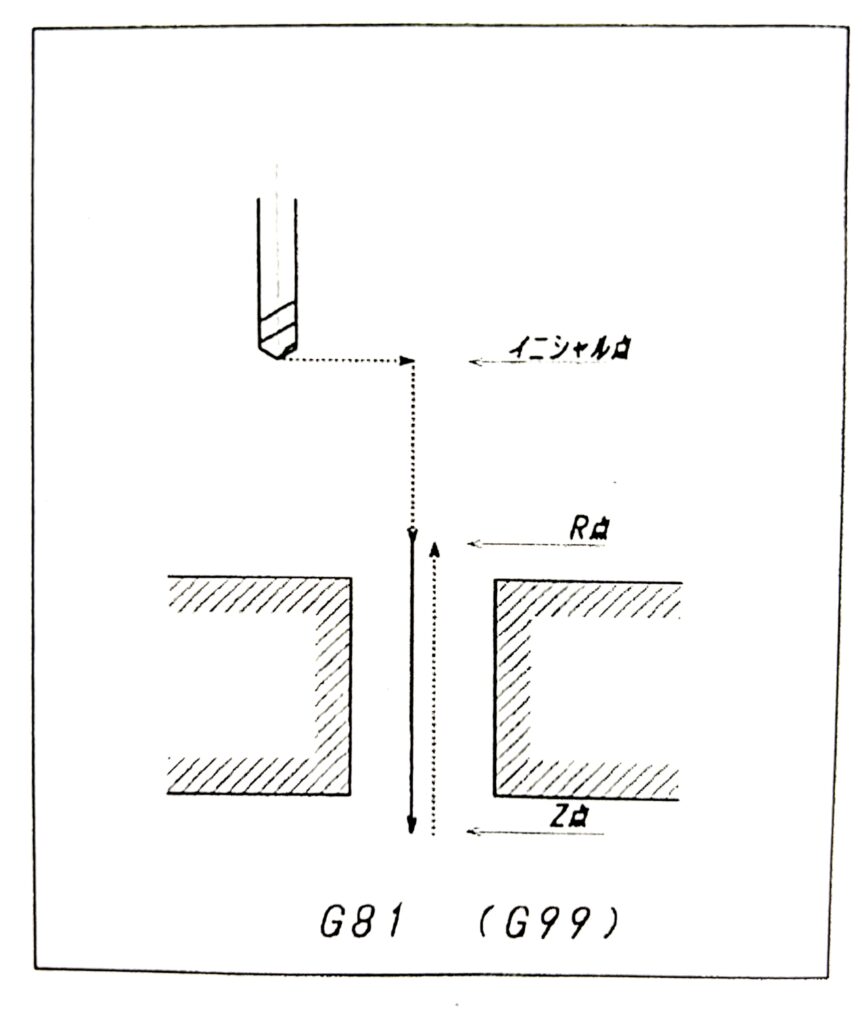
G82(カウンターボーリング)
G82は、穴底でドウェル(一時停止)を行う固定サイクルです。座ぐりや面取りなど、穴底の仕上げ精度を求める加工に使用されます。
基本的にはG81と似た動作ですが、穴底で一定時間停止する点が異なります。
ですが、私が加工するうえではほぼ使うことはなく、必要になったときに覚えれば十分な固定サイクルです。
G82を使うメリット
• ドウェル機能により、穴底面の仕上げ精度が向上
• 座ぐり加工や面取りに適している
• G81と同じ指令形式で、追加パラメータ(P値)を指定するだけ
G82がほぼ使われない理由
G82は、G81やG83で十分対応できる場合が多いため、 習得の優先順位は低いです。
穴底面の平面度を向上するため、エンドミルなどを使った ザグリ加工などに使用するのは良いかもしれません。
G82の指令方法
G82 X** Y** Z** R** P** F** K**;
G82の各パラメータの解説
コード | 意味 |
---|---|
X, Y | 穴位置データ |
Z | 穴底位置またはR点から穴底までの距離 |
R | R点位置またはイニシャル点からR点までの距離 |
P | ドウェル時間(1/1000秒) |
F | 送り速度 |
K | 繰り返し回数(FANUC 15Mでは「L」になる) |
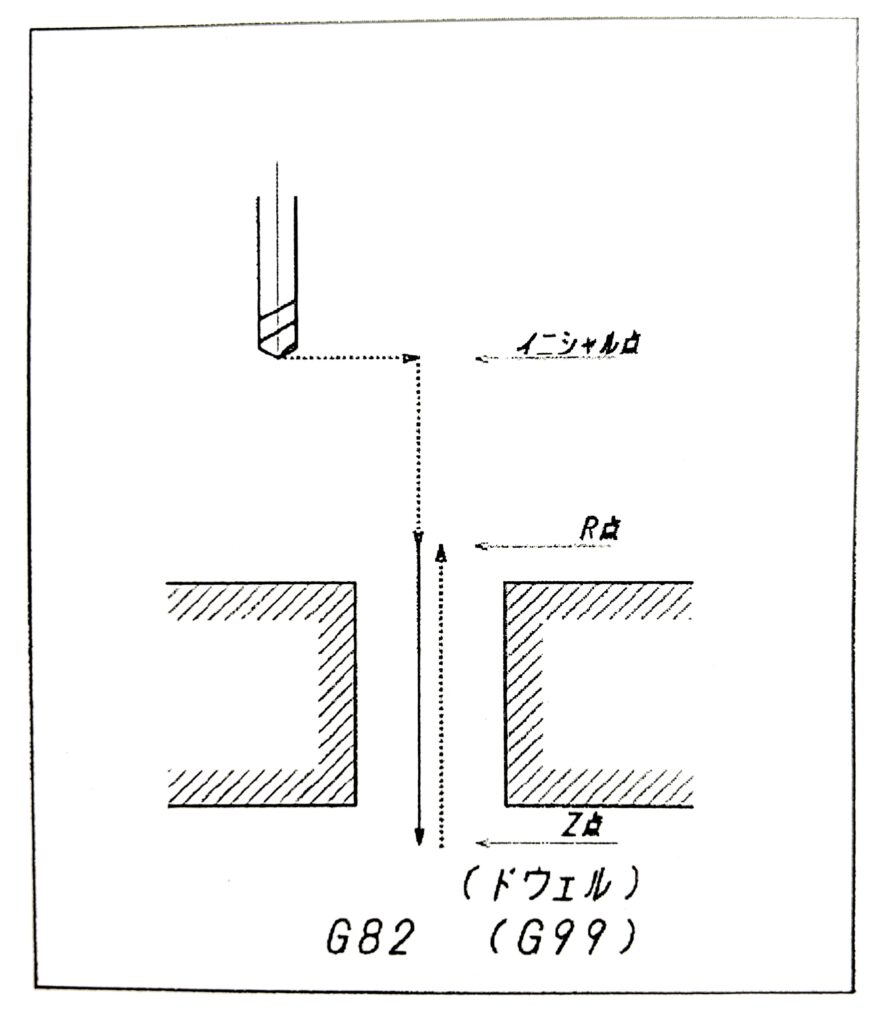
G84(タッピングサイクル)
G84は、CNCマシンでタッピング(ねじ切り加工)を自動化するためのGコードです。手作業では難しい精密なタップ加工を、自動で高速に行うことができます。
G84タッピングのメリット
• 高精度なねじ切り加工が可能
• 手作業よりも大幅に時間を短縮
• タップの折損リスクを低減
• 複数の穴加工を一括で実行できる
同期タップ(リジッドタップ)とは?
最近のCNCマシンには同期タップ(リジッドタップ)機能が搭載されているものが増えています。これは、主軸の回転と送りモーターが同期することで、高速かつ正確なタッピングを可能にする技術です。
同期タップを使用する場合、機種によっては**Mコード(例:M29)**の指定が必要になることがあります。
G84タッピングサイクルの指令方法
G84を使ったプログラムは以下のように記述します。
G84 X** Y** Z** R** P** F** K**;
G84の各パラメータの解説
コード | 意味 |
---|---|
X, Y | 穴位置データ |
Z | 穴底位置またはR点から穴底までの距離 |
R | R点位置またはイニシャル点からR点までの距離 |
P | ドウェル時間(1/1000秒)、1回転に要する時間=1/(N/60) |
F | 送り速度 F = 回転数×ピッチ |
K | 繰り返し回数(FANUC 15Mでは「L」になる) |
G84を使用する際のポイント
R点(リトラクトポイント)の設定
R点はタップが切削を開始する前の位置です。適切に設定しないと、ワークとぶつかってしまったり、加工時間が伸びてしまう原因になります。
送り速度(F値)はねじピッチ×回転数に合わせる
タッピングでは、送り速度Fは「F = ねじピッチ×回転数」の関係にする必要があります。間違えるとタップの破損につながるので注意しましょう。
ドウェル時間(P値)の最適化
P値(ドウェル時間)はタップの底部での停止時間を設定します。素材によっては少し設定すると、タップ抜けがスムーズになります。
一方で、私が普段使用するマシニングセンタでは同期タップがついておらず、タッパーを使用しているため、ドウェルは使っていません。
同期タップ(リジットタップ)使用時のMコード
同期タップ機能を利用する場合、Mコード(例:M29)を追加する必要がある機種もあります。機械のマニュアルや、メーカー、前任者に事前に確認しておきましょう。
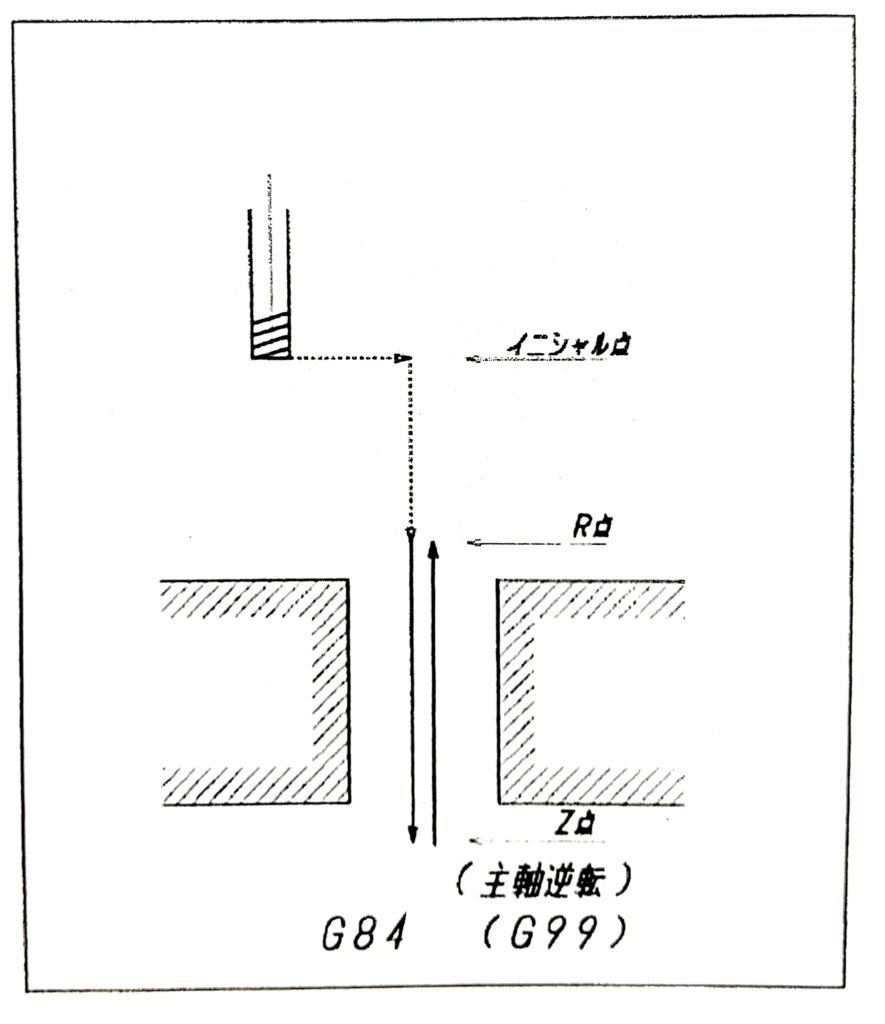
まとめ
今回は、CNC加工で頻繁に使用される固定サイクルについて詳しく解説しました。G73(高速深穴あけ)、G83(深穴あけ)、G81(ドリル)、G82(カウンターボーリング)、G84(タッピング)など、用途に応じて選択することで、加工の効率化や精度向上が可能になります。
特に、G73とG83の使い分けは深穴加工において重要であり、G81はセンタリングに最適ということなど、現場での実用的な視点も交えてご紹介しました。
固定サイクルは、一度習得すれば、穴あけ加工の効率を格段に向上させる重要な技術です。今後の加工プログラム作成に役立ててください!
次回の記事では、さらにボーリング加工の固定サイクルについて解説予定です。お楽しみに!
コメント