
S45Cの削り方
S45Cは最も簡単で基本的な材質です。切粉が切れやすいため切削性が良いのが特徴です。
全ての材質の切削条件は、S45Cの切削条件を基準に考えていきます。
温度が上がると焼きが入って固くなってしまうため、クーラントをかけながらの加工が無難です。
外径荒加工
切削速度V200m/min
切り込みap2.0mm
送りf0.3mm/rev
これが外径加工の基本的な切削条件です。適正なチップブレーカーであれば切粉もサクサク分断されます。
もちろんクランプがしっかりしていることが前提ですので、掴みが浅い場合などは切り込みを下げ、対応するようにしましょう。
ちなみに断続切削の場合、鋼材に限ったことではありませんが、切削速度を70%、送り速度を50%程度にして加工することが多いです。数が多くサイクルタイムを短縮する必要がある場合は、そこから刃物寿命を見ながら条件を上げていきます。
内径荒加工
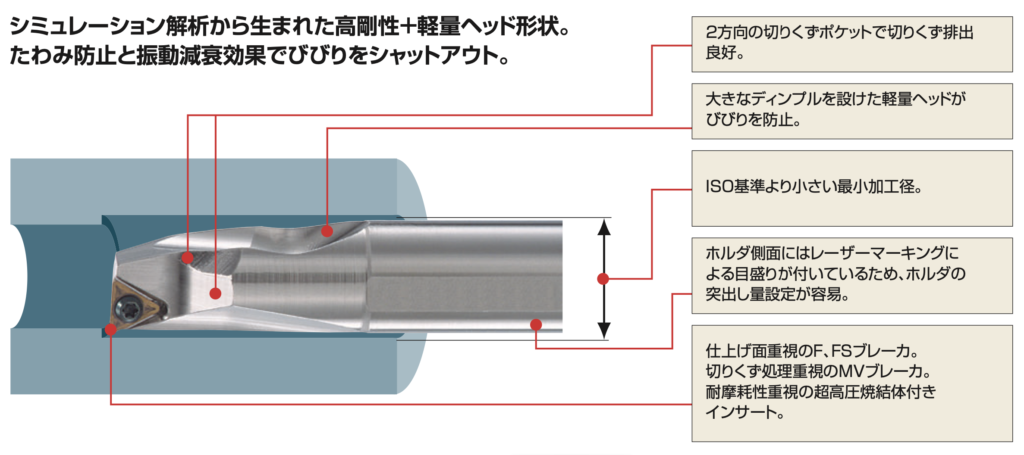
切削速度V140m/min
切り込みap1mm
送りf0.2mm/rev
内径荒加工にディンプルバーを使う場合、切削条件は上のように低めに設定してやったほうが良いです。
内径の荒加工は、慣れないうちは切粉が噛んで「ゴゴゴゴゴゴッ!」と嫌な音がしてチップが割れ、バイトが変形し使えなくなってしまうということが起こりやすいです^^;
深めの穴ぐりの場合、1000回転を超えるようであれば切粉がバイトに噛んでしまう可能性が高くなるので、慣れないうちは内径加工は1000回転で留めておくと良いです。
錆びないように防錆油を吹き付けておく
45CやSS400などの鋼材は当然ながら錆びるので、錆びる原因になるクーラントは加工後きちんと拭き取り、防錆油を吹き付けて錆びないようにしておきましょう。
防錆油は私の勤務先では、霧吹きに入れて吹き付けるタイプのものを使用しています。
SS400の削り方
SS400。俗に生材といわれるやつです。
S45Cよりねばっこく、切粉が切れにくいです。切削性は良いとは言えませんが、問題なく削れるレベル。
ですが稀に削りやすいSS400もあります。
つまり材質にかなりばらつきがあるのがSS400です。
基本的には焼きを入れることはできません。ですが、高温によって硬くならないわけではないので、45Cと同じようにクーラントでしっかり材料を冷ましてやることは大切です。
外径荒加工
切削速度V220m/min
切り込みap2.0mm
送りf0.3mm/rev
45Cと違って、SSだと切削速度が低いと削っている最中「ゴッ・・・ゴッ・・・ゴゴ・・・」と引っかかるような音がします。
削る際に材料がむしれているような音です。
この音がしているとチップに材料がくっつきやすく、さらに材料にも傷が入りやすい状態になります。
これを防ぐためには、切削速度を上げてやるのが効果的。
なのでSSは45Cよりも切削速度を高くします。
45Cより感覚的に柔らかい材質のため、高めの切削速度でもチップは傷みにくいです。
速く加工したい場合はV300くらいまで上げても全く問題ありません。
内径荒加工
45Cと違って、SSのディンプルバーでの荒加工はそこそこ厄介です。
先程書いたとおり、SSは切削速度を上げないとゴリゴリ音がして、むしれてしまいます。
とはいえ内径加工ではびびりや切粉のはけの関係で、そこまで大きく切削速度をあげることはできませんよね。
なので切削条件的には45Cの内径荒加工と同じでよいということになってしまいます。
まずひとつ目なる対策として、なるべくディンプルバーを使わずに、下図のような荒加工用の内径バイトを使いましょう。
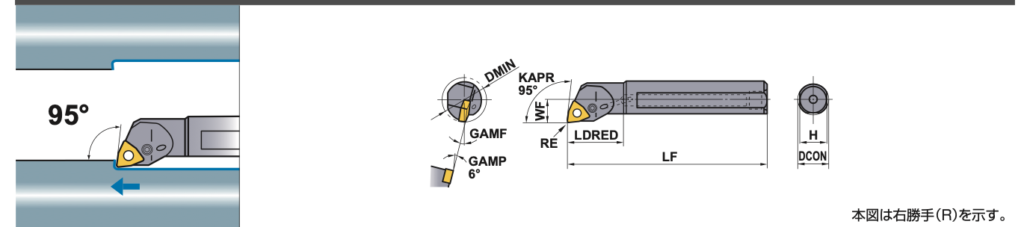
これであればまだ切粉も切れやすく、比較的削りやすいはずです。
その場合の切削条件は
切削速度V140m/min
切り込みap1.5mm
送りf0.3mm/rev
この条件で加工しています。もっと大きいバイトを使うときは、切込みや送りをさらに上げることもあります。
やむを得ずディンプルバーを使う場合は、むしれにくい切削速度を探して削るようにしましょう。SSは材料のロットによって切削性が違うため、一概に切削速度を示すことができません。
そして、どうしてもゴリゴリいうようであれば、仕上げしろを多めにとって、そのむしれ部分が仕上げでとれるようにしておきましょう。
SSでしたら仕上げ加工は45Cと同じようにやれば綺麗にできるはずです。
SUS304・SUS316の削り方
SUS304は比較的削る機会の多い材料かと思いますが、削りにくい材料の代表格と言えるような材料です。
ねばっこいので切粉が切れにくく、なにより切削性が悪いため刃物がすぐ痛みます。
今でも深めの内径H7仕上げ加工なんかは苦労します。
SUS316は304より少しだけ刃物が傷みやすい感覚があります。ですがSUS316も304と同じ条件で削って大丈夫です。
なるべく刃物を痛めない削り方を紹介しますので、参考にしてみてください。
外径荒加工
切削速度V70m/min
切り込みap2.0mm
送りf0.3mm/rev
304の加工では、45Cよりも切削速度を落とすようにしましょう。刃物が傷みにくくなります。
切り込みや送りを落としたとしても刃物の痛み方はあまり変わりません。速く削ろうと思う場合、高切り込み高送り低切削速度の条件がおすすめです。
ステン用の刃物を使っている場合だと、V100m/minくらいでしたら大丈夫です。私はいつもこちらの条件で削っています。
汎用旋盤ではいちいち切削速度の計算なんてしていられませんので、サーメットの刃物でS400〜500m/minで削ることが多いです。
切粉が切れにくいとはいっても、外径加工だとさすがに切れてくれます。外径では切粉に悩むことは少ないと思います。
内径荒加工
切削速度V70m/min
切り込みap1.0mm
送りf0.2mm/rev
これはディンプルバーで荒加工を行う場合です。
ですがディンプルバーで304を削る場合は切粉が切れにくく、切粉が詰まってトラブルになることが多いです。
なのでSS400のところで説明した荒加工用の内径バイトを使うのが一番ですが、小径の場合ディンプルバーに頼らざるをえないこともあります・・・。
単品ものだとこまめに機械を停止させて切粉を掃いてやり、数物の場合は荒加工にキリやエンドミルを使うなどして、切粉のトラブルに気をつけて加工しましょう。
ですがこれは小径の話。
φ24以上の穴ぐりで、荒加工用の内径バイトが使える状況であれば、以下の条件で削っています。もちろんステンレス用のチップであることが前提です。
切削速度V100m/min
切り込みap1.5mm
送りf0.3mm/rev
私の使っているチップでしたらこの条件でしっかり切粉も切れ、問題なく加工してくれます。
この材料はタップにも注意する
SUS304や316は、タップが折れやすいです。
なのでタップの下穴は、径が0.1mm大きいドリルを使うと良いです。
少しだけタップのガタツキは多くなりますが、実用上全く問題ありません。
そしてスパイラルタップでしたら、機械を使ってタップを立てる深さは、M3は有効2Dまで、M4~M8は2.5Dまでにしておきましょう。
それ以上の深さを立てる場合は手で立てるようにした方がいいです。
機械で立てると折れることがあります^^;
SUS303の削り方
SUS303は私の一番好きな材料です。
おそらく多くの旋盤技術者がそう思っていると思います。
切粉も切れやすいし、刃物も傷みにくい。そしてアルミのように傷に気を使う必要もなく、錆びない。
削っていて楽しいです。
一番好きな材料はSUS303。
— 旋盤工のTAK (@NCsenban_tak) July 28, 2020
旋盤やってる人なら同意できる人も多いはず!
これは私のツイート。これをつぶやいたら今までにない数のいいねがつきました。
それだけ共感してくれる人が多いということですね!
切削条件はS45Cと同じでOK
ステンレスとはいえ切削条件はS45Cと同じで構いません。
チップの痛みが早いようでしたら、切削速度だけ落としてやれば良いです。
削る上でも特に気をつけることはありません。
A5052等50系アルミの削り方
お次はアルミです。
アルミは速く削れる反面傷やむしれなどのトラブルが多く、意外と苦労させられます。
特にA5052やA5056などの50系はかなり難しい材料です。
削っていても切粉がほとんど切れず、仕上げ加工でもむしれてしまうほどねばっこい材質をしています。
外径荒加工
切削速度V400m/min
切り込みap2~2.5mm
送りf0.3mm/rev
まず荒加工時の初めの大切なポイントが、仕上げしろを多めに残しておくことが必要です。
具体的には径で0.5mm以上は残すようにしましょう。
その理由は、むしれが発生した際に、むしれた面を仕上げ加工で除去できるようにするためです。
私は鋼材などを削る際は仕上げしろを通常0.2mmにしていますが、50系のアルミを削る際は0.5mmにして削っています。
基本的にはアルミ用のチップを使う
50系のアルミは本当に切り粉が分断されにくいです。
鋼材用のチップでも加工することはできますが、ある程度の数を加工するのであればアルミ用の荒加工チップを購入して使用することをおすすめします。
アルミ用のチップはブレーカー形状が特殊で、粘っこいアルミでも切り粉が分断できるように設計されています。
アルミの荒加工で困っているのであれば導入する価値は十分にありますよ。
鋼材用のチップでもA50系の荒加工が可能
鋼材用のチップでも粘っこいアルミの加工を一応は行うことができます。
切削条件は切削速度高めで、切込みも大きめが良いです。
しかしこれでも切粉が分断されないことが多々あります。
太い切粉がつながって、チャックに巻き込まれてすごい音がしたり、ワークに傷がついたりと、放っておくとトラブルになってしまいます。
なので、どうしても切粉が切れない場合は、NC旋盤であれば停止と起動ボタンを交互に押して切粉を切りながら加工するようにしましょう。
汎用旋盤でも同じように切粉を切ってやれば良いです。
ですが単品ものだとこれで良いですが、数物だと毎回切粉を手動で切りながら加工するのも大変です。
そういった場合は、切削速度を思い切って下げてみましょう。
大体V140m/minくらいまで下げると、「ボリボリボリボリ!!」と音を立てながらむしれながら削っていく状態になります。
この状態になると、むしれて大変表面はきたなくなりますが、切粉は切れるようになります。
この状態になる切削速度は材料のロット等によってばらつきがあるので、自分で切削速度を下げてみて様子を見ながら切削速度を調整してみましょう。
この状態で削ると運が悪ければ0,5の仕上げしろでは足りない場合があるため、失敗できない場合は径で1mmくらい仕上げしろを確保しておくと間違いありません。
内径荒加工
切削速度V400m/min
切り込みap1.5~2mm
送りf0.2mm/rev
内径荒加工も基本的には外径と変わりません。
しかし、内径の方がより切粉が切れにくく、苦労させられます。
また、内径のほうが切粉が切れないときのワークへの影響が大きいです。切粉が穴に詰まってしまい、ワークをボロボロに痛めつけてしまいます。
なので切粉の処理は必ず行わないといけません。
チップが外径のものより小さい分ブレーカーも小さくなってしまうことが原因の一つだと思いますが、径が小さめの穴ぐりの場合はバイトを大きくするわけにはいきませんので、頑張って先程説明したように切粉を手動で切りながら削っていくことになります。。
数物などで、いちいち手動で切粉を切っていられない場合、外径のように仕上げしろを多めにとり、切削速度を落としてむしれさせながら削ってみましょう。
それでも切粉が切れない場合は手動で切るか、刃物をかえるしかありません(^^;
仕上げ加工
ここまでは仕上げに関しては難しい要素がなかったので仕上げ加工の説明は省略していましたが、この50系は別です。
普通に仕上げると、一部ワークにむしれの線が入ってしまうことがあります。
むしれの原因は、削っている感じでは切粉が刃物とワークの間に噛み込んでしまうことによるものだと思います。
なのでその対策として、仕上げは2回に分けて行うと良いです。
1回目は仕上げしろを径で0.06mm残して仕上げます。そして多少のむしれが入ってしまっても、2回目の最終仕上げできれいに仕上げるというかたちです。
A6063等、50系以外のアルミの削り方
A6063などの60系は50系と比べてかなり削りやすいです。
外径荒加工では切粉はサクサク切れてくれますし、内径でも50系ほど苦労することはまずありません。
切削条件は先程説明した50系の切削条件を使えば大丈夫です。
とはいえ内径加工では切粉が詰まってしまうとワークを傷つけてしまうことは50系と同様に気をつけなければいけないです。
私はよくピン角が必要な60系のアルミの内径加工をやる機会があるのですが、うまくプログラムを組まないと、内径に詰まった切粉によって仕上げ加工で角に多少のC面が取れてしまいます。
そういうときには、仕上げを2回に分けるプログラムを組んだり、最終仕上げ加工の前にM0で一度プログラムを停止させ、切粉を掃いてから仕上げるようにすることで解決できます。
仕上げ加工もたまにむしれるトラブルがありますが、大抵は1回の仕上げできれいに仕上がります。
真鍮の削り方
真鍮は削りやすいのですが、やっかいな性質を持っています。
それは細かい切粉が出ること。
NC旋盤でしたら機械の隙間に入り込んでしまい、機械を傷める原因になってしまいます。
なのでできれば汎用旋盤を使って削れると良いです。
それからNC旋盤・汎用旋盤のどちらで削る場合でも、クーラントは使わないようにしましょう。
細かい切粉がクーラントタンク中に入り込んでしまい、とれなくなってしまいます。
クーラントタンクの中だけでしたらまだクーラント入れ替えできれいにできますが、ポンプに入ってしまった場合はとることができませんので、気をつけたほうが良いです。
なので汎用旋盤やNC旋盤の下に新聞紙を敷き、切粉がその上に落ちるようにして加工していきましょう。
真鍮は削りやすい分熱くなりにくいので、仕上げ前に熱を取るのもそれほど時間はかからないはずです。
そして切削条件は、45Cと同じ条件でOKです。
それで表面も十分きれいに仕上がるはずです。
最後に注意しておかなければならないことがあります。
少量を削るだけの場合等でクーラントを使った場合、クーラントがついたまま製品を放置しておくと、クーラントのしずくの跡が仕上げ面に残ってしまうことです。サビのようなものなのでしょうか。これが拭くだけではとれないんです。
なのでクーラントを使った場合も、最後に製品をきれいに拭き取ってから保管するようにしておきましょう。
鋳物の削り方
鋳物に関しては、以前別の記事で詳しくまとめましたので、それを参考にしてください。
↓↓
大方を説明すると、仕上げやすいですが、切粉が粉状になって機械のすきまに入り込んでしまうため厄介な材料です。
真鍮でも説明したように新聞紙を使って加工を行うようにしましょう。
チタンの削り方
チタンは粘っこく切粉が切れにくいですが、傷がアルミほど付きやすい材料ではないため、そこまで苦労することなく削ることができると思います。
材料自体の価格が高いため、不良にしないよう気をつけて削るようにしましょう。
切削条件に関しては45Cと同じでOKです。
チップによっては仕上げ面が粗くなってしまう
チタンで問題になってくるのが仕上げ面の粗さです。
もしかすると使っているチップによっては仕上げ面がザラザラになってしまうかもしれません。
私がいつも使っている仕上げチップ、サーメットのノーズR0.2で、精密仕上げ用の勝手付きブレーカーのものでしたら外径はきれいに仕上がります。
チタン端面仕上げ加工のポイント
端面も同じチップできれいに仕上がりますが、通常の上から下への端面加工ではザラザラになってしまうことがあるため、センタ穴を0.03mm開けて切削速度ゼロ点を回避した上で、中心から上に向かって端面仕上げ加工を行っています。
比較的びびりやすい加工方法ではありますが、少し外形仕上げバイトを傾ければびびることはほとんどありません。試してみてください!
タップを立てるには最も厄介な材料
チタンほどタップが折れやすい材料はそうありません。
チタンは比較的柔らかい金属ですが、粘っこい分切粉がタップに喰い付いてしまい、一気に立てようとすると簡単に折れてしまいます。
チタンにスパイラルタップを使う場合は、必ず手で立てるようにしましょう。
私はいつも、機械で5mmくらいだけ立てて、あとは手でタッピングを行っています。
機械やボール盤などでタッピングを行う場合、新品の切れ味の良いタップを使い、ペースト状の切削性の良い油を使った上で行なえば問題ない場合が多いです。
焼入れ鋼の削り方
焼入れ鋼とひとくちに言っても様々な硬度のものがあります。
例えば柔らかめのマルエイチ材等の調質材は焼きが入っているとはいえ普通に削れますが、SK材などの工具鋼は刃物が負けるほどの硬度だったりします。
私の勤務先では焼入れ鋼を削ることはそれほど多くないため、焼入れ鋼用の刃物もありません。
なので、普通の工具で焼入れ鋼を削る方法を書いていきます。
マルエイチ材等の比較的柔らかい焼入れ鋼
削れる範囲の調質材は、上で説明したSUS304の切削条件で削ればOKです。
もちろんステンではありませんので、刃物は鋼用のものを使ってください。
硬い分切粉はよく切れますし、仕上げ面もむしれることがなく光りやすいので、むしろ削りやすいと感じるかもしれません。
硬い焼入れ鋼の場合、まずは削れる硬さかチェックする
ここからが本題です。
追加工品を加工しようと思ったらガチガチに焼きが入っていて、刃物を当てた瞬間火花とともに刃が欠けた・・・ そんな経験が私にもあります。
焼きが入っていそうな品物は慣れれば見た感じで大体分かると思いますが、硬度は分からない場合が多いです。
なので、まずは焼きがどのくらい入っているかをチェックするところから始めます。
φ30くらいのものとして、まずはS300m/minくらいで回し、ap0.1mmほどでサーメットの刃物をワークにゆっくり当ててみましょう。
削れれば、時間をかければまだなんとかなる硬さです。
もしそれでも無理なら、仕上げ用の超硬チップを使ってみます。
私が使っているのは京セラのコレ。 画像はクリックで拡大できます。
話は変わりますがこのチップ、SUS304や316に対してかなりの耐久性があり、仕上げ面の具合も申し分ないため、ステンレスを削るのに大変重宝しています。
私が使っているのは三角のネガチップで、ノーズR0.2の勝手がないものです。
焼入れ鋼に対してもサーメットよりは有効です。
これで同じように削ってみて、それでも無理なものは焼入れ鋼用のチップを用意するしか無いでしょう。
例えばSKD11の真空焼入れ品などはかなり硬く、焼入れ鋼用のチップが必須といえます。
仕上げ用の刃物で低回転低切込みでゆっくり削っていく
硬い材質の場合、低回転で削ることがポイントです。
仕上げ加工は回転数を落とせば可能かと思いますが、荒加工は正直難しいです。
どうしても荒加工が必要な場合は、仕上げ用の刃物で以下のようにやってみてください。
切削速度V30m/min
切り込みap0.25mm
送りf0.1mm/rev
本来削れないものを無理やり削っているかたちになるので、このくらい切削条件を落とさないと刃物がやられてしまいます。
焼入れ鋼を削る場合多くは追加工品かと思いますので、削る量はそこまで多くないはずです。
刃物は2,3コーナー消費することになるかもしれませんが、これでなんとか削れるはずです。
何にせよ数や削る量が多い場合は、焼入れ鋼用の刃物を用意したほうが手っ取り早いです(^^;
切削加工における、条件設定は大変重要
本記事では、金属加工における様々な材質に対する具体的な切削条件やコツを詳しく解説しました。それぞれの材質に適した加工方法を理解することで、効率的かつ高精度な仕上がりを実現することが可能です。
切削加工をスムーズに進めるためには、適切な切削速度、切り込み量、送り速度を設定することが不可欠です。また、工具の選定やクーラントの使用も重要な要素です。各材質ごとに最適な条件を見つけることで、加工効率を向上させ、工具の寿命を延ばすことができます。
今後も金属加工の技術をさらに向上させたい方は、他の記事や最新の加工技術情報をぜひチェックしてください。また、実際の作業で疑問が生じた際には、この記事を条件設定の参考にしていただければ幸いです。
お読みいただきありがとうございました!
コメント