例えばφ3
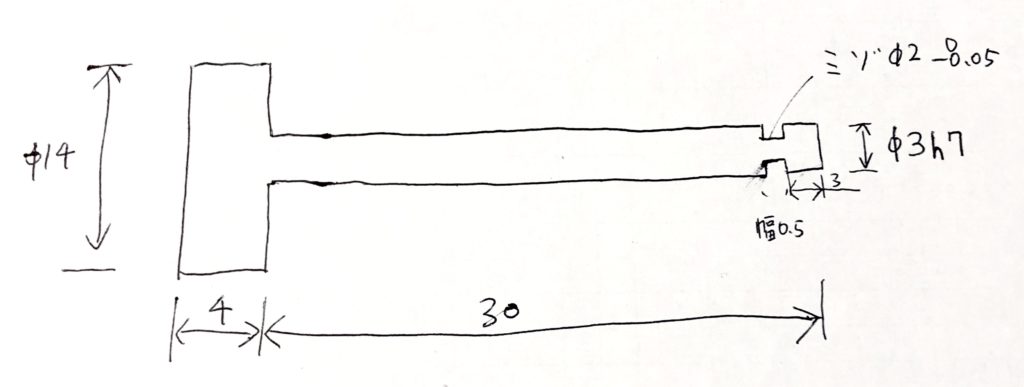
荒加工の切り込み量を少なくする
まず、φ3のような小径加工を行うにあたって警戒しなければならないことは、φ3の部分が折れてしまうことです。
1mmなんて切り込んでしまおうものなら、すぐに折れてしまうでしょう。
まずはφ6くらいまでは切り込み量1mmで行い、そこからはap0.25mmずつなど、薄く切り込むようにすれば折ることなく荒加工を行うことができます。
センタ穴は小さいセンタドリルを使うか、治具を作る
φ3ともなると、長くてもセンタ穴もいつもどおりにあけられませんよね。
うちで通常使っているセンタドリルは先端φ2のものなので、どう考えても無理です。
そんな場合は細いセンタドリルでセンタリングを行います!
うちではこんなときのために、先端φ0.7、φ1、φ1.5の細いセンタドリルを買ってあります。
一番細いセンタドリルであればなんとかφ3のワークにもセンタ穴を開けられると思います。
といっても細いセンタドリルなんて準備する時間がない!という場合もあると思います。
そういう場合はセンタ穴なしでセンタを押すことができる治具を作ります。
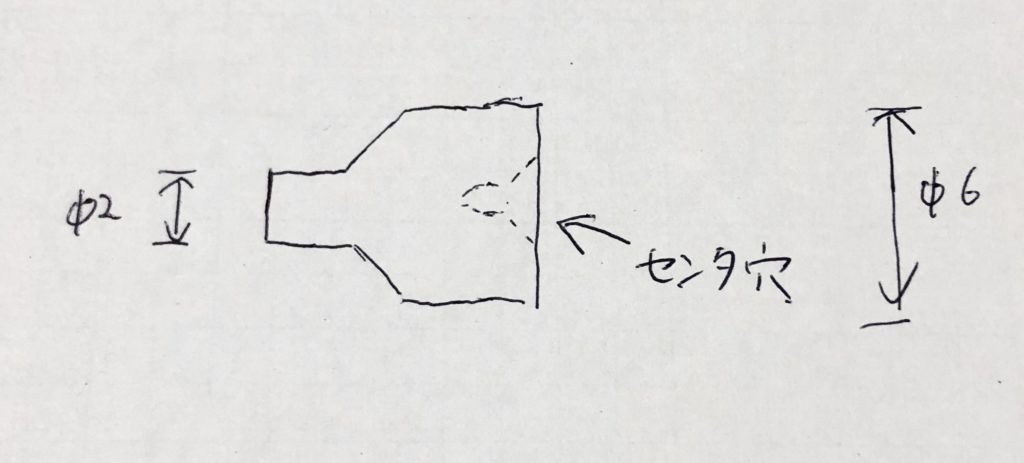
画像のような治具を作り、芯押しセンタの先にくっつけてやります。そして穴をあけずに芯を押してやれば大丈夫です。
芯押し加工をする際の2つの注意点
小径の場合は、芯押し加工をする際に注意しなければならないことがあります!
サイクル基準点Zは0.1に!
φ3のような細いワークの場合、バイトがセンタ先にぶつかるかぶつからないか本当にギリギリのところだと思います。
なので当然端面は先に仕上げておき、サイクル基準点はギリギリの0.1にします。
あとはバイトは干渉しにくい形状のものを選び、ノーズRの小さいチップを使い、可能な限り干渉しにくい段取りを組んでやります。
面取りはしない!
プログラムで面取りを行うと、例えばC0.2とってしまうと本来φ3までバイトを持っていけば良いはずがφ2.6かそれ以下までバイトを下げなければなりません。
それでは干渉してしまう可能性がさらに高まってしまいますね。
なので、このような場合面取りはプログラムで行わず、手で行います。
加工後にチャックを回し、ヤスリやペーパーで面取りだけ行ってやるのです。
切削条件はココを気をつけろ!
切り込みの話は特に重要なので先に話しましたね。その他にも気をつけておいたほうが良いことがあります。
回転数はリミットを上げよう
φ3ともなると、通常の切削速度で削るのはまず不可能です。ですが、もし表面が悪くなるようでしたら、できるだけ切削速度を上げるために回転数を高くしてやりましょう。
例えば普段リミットを2000回転に設定している場合でも、この加工を行うときだけ3500回転に設定するなどして、安全な範囲で可能な限り回してやります。
それでも足りないと思いますが、普段の切削速度に近い速度で削ることができると思います。
送りは低めに!
うちでは仕上げ加工は普段0.1mm/revで送っていますが、それだと削った目がだいぶ目立ちます。
細くなればなるほど旋盤の目が目立ちやすくなるため、小径加工の場合は0.05〜7mm/revくらいで低めに設定してやるときれいに仕上がります。
バイトの芯高に注意!
バイトの芯高が狂っていると、径が小さければ小さいほど寸法に影響が出やすくなります。
理屈を知りたければコメントください。説明しますので!
なので、以下のようなことが起こってしまいます。
今回はφ3のh7公差が入っていますね。
その場合、例えばまず+0.1mm の仕上げ代をとって仕上げ削りを行うとします。
削り終わったらマイクロで測定し、測定値が+0.13mmだったので摩耗補正で-0.005mmをねらって再度仕上げると・・・測定値が+0.01!? ズレてる!!
と、芯高がずれているとこういうことになってしまうのです。
なので、小径加工をする場合はより正確に芯高を合わせましょう!
公差が入っているミゾは測れないのでこうやって加工する!
今回φ2の極細のミゾを入れなければなりませんね。
この場合、測定ができないので機械精度で公差に入れるしか無いです。やりかたは・・・
まずミゾを入れる箇所の外径を、仕上げ代を残して仕上げ、正確に測定します。そして、溝入れバイトの工具補正を呼び出してから、0.001mmずつ仕上げ面に近づけ、当たったところで先程の測定値を使って溝入れバイト工具長を再設定してやります。
これで溝入れバイトが小径の場合のぴったりの工具長設定になったため、あとは公差の真ん中をねらってミゾをいれてやればOKです。
このときも、溝入れバイトの芯高がずれていると、工具長はちゃんと設定できていても、実際のミゾ径は大きめになってしまっている・・・ということになりかねません。芯高はきちんと設定するようにしましょう。
φ3のような小径を掴むときはベビーチャックを使う!
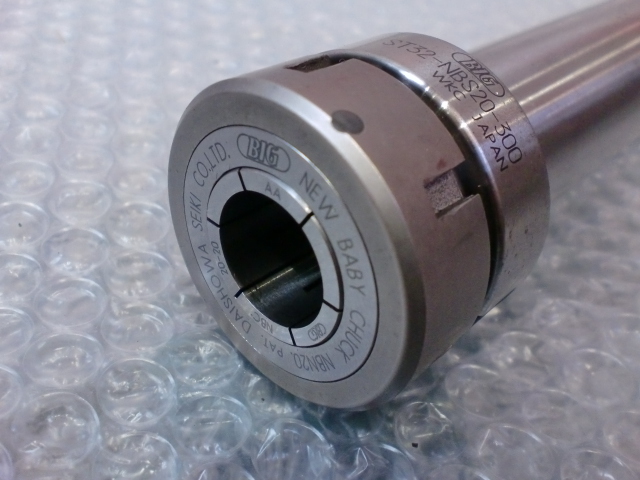
φ3にけずったワークを掴んで反対側を加工したい!っていうときありますよね。
そんなときはベビーチャックを使って掴みます。
ベビーチャックは、コレットを入れ替えることで、小径の様々な径の丸棒をチャッキングできる治具です。
本来マシニングセンタで突き出し長さを伸ばしたりする目的で使うものですが、旋盤で掴むこともできます。
今回の例だとベビーチャックにφ3のコレットを装着し、ワークを入れてやれば簡単にチャッキングすることができます。
しかしここで注意点があります!
それは強く締めすぎないこと。
ベビーチャックはエンドミルなど工具を掴むために設計されているので、ステンレスや鋼材などをつかむと潰れてしまう場合が結構あります。
せっかく公差に入れていてもオシャカになってしまうので、緩めに締めるように気をつけましょう。
当然ですが、ゆるく締めた分切込みを少なくして、ワークが回らないように注意しましょう。
数物の場合①:生爪をフライスで尖らせて削る
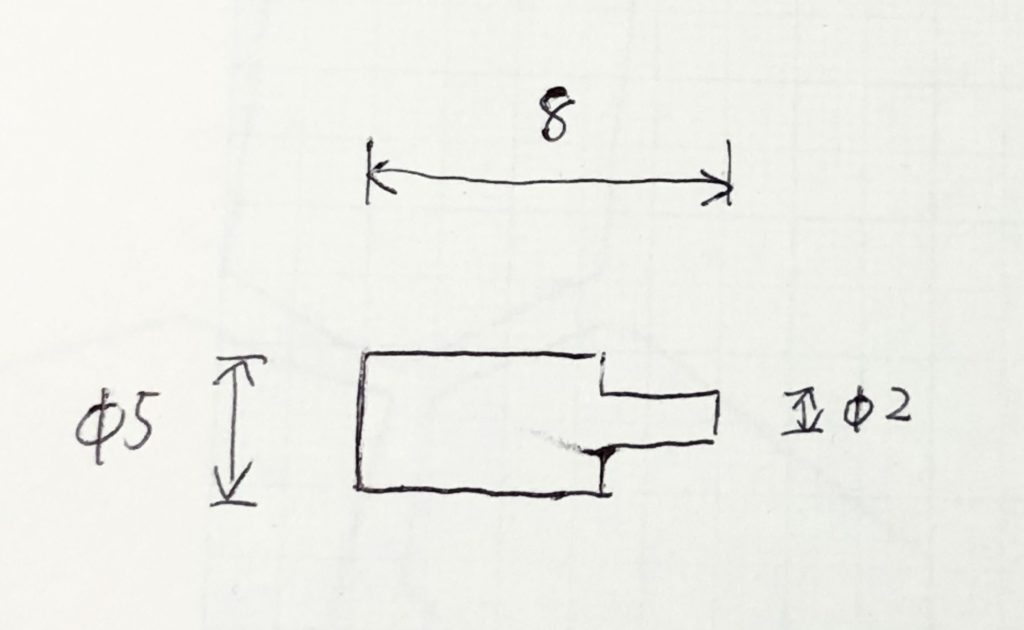
例えば上の図面、100個の制作が必要とします。
右面は長いまま加工し、切り落としてしまえばいいのですが、左面の端面を仕上げるにはどうすればよいでしょうか。
先程と同様にベビーチャックで・・・と言いたいところですが、数物ではベビーチャックの弱点がでてしまいます。
それは、数物を同じ深さでチャッキングできないこと。
比較的長い場合は底の”あて”を使うことができますが、画像のような形状だとベビーチャックの奥にあてることができません。
そこで用いる方法が生爪をフライス加工で尖らせて使う方法です。
生爪を加工するにはフライス盤かマシニングセンタが必要になります。
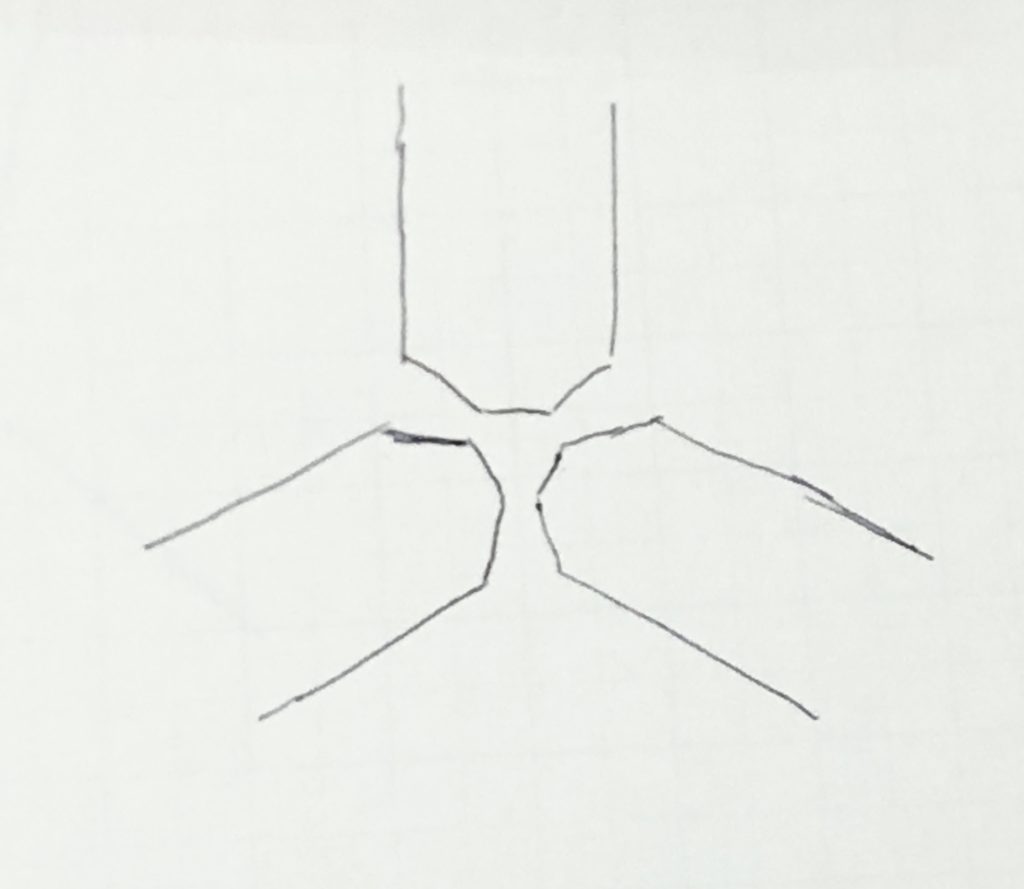
通常生爪は上画像のように先端が面取りされており、φ5のような小径のワークは掴むことができません。
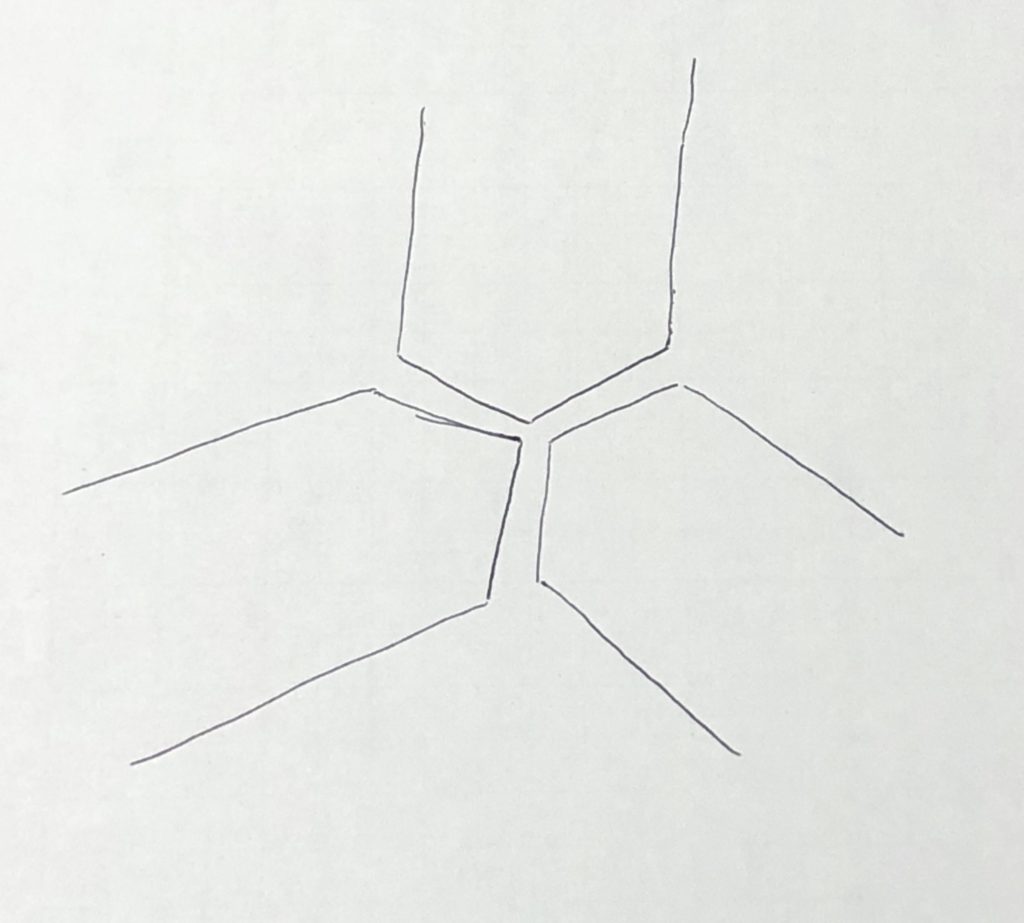
ですが、生爪をフライス加工で尖らせることで、φ5でも掴むことができるようになります。
上画像のように尖らせたら・・・
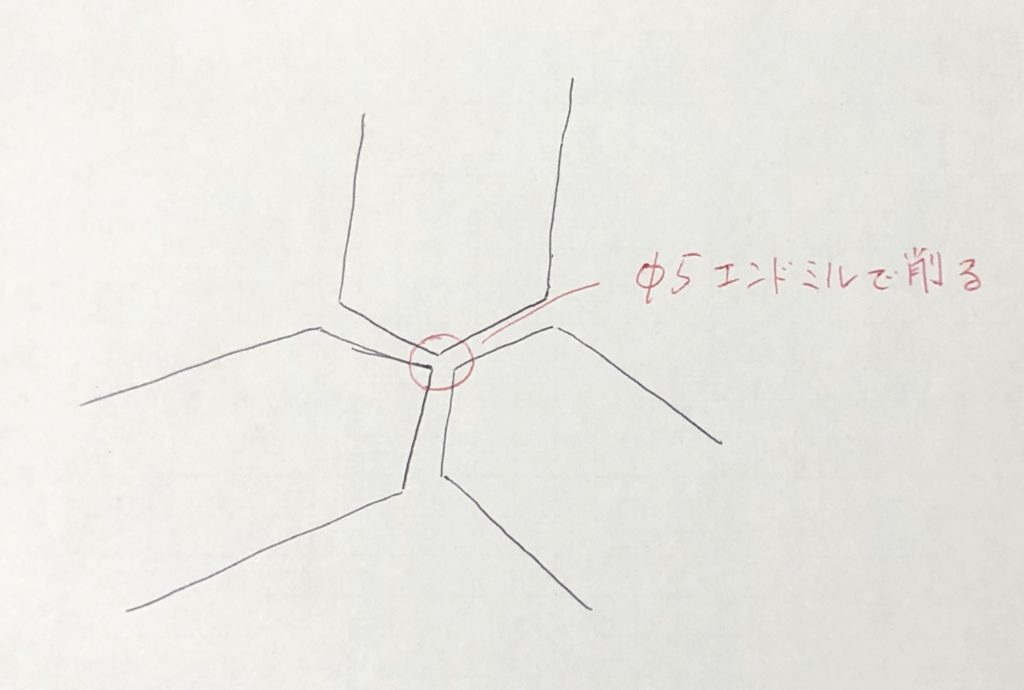
今度は旋盤に生爪を取りつけ、φ5のエンドミルで適当な深さまでつついてやります。
今回制作する部品であれば深さ4くらいがちょうどよいです。
あとは普通に掴んで加工するだけ。
NC旋盤で生爪を取り付ける際、通常通りに取り付けられれば何も問題ありませんが、もしジョーナットが干渉するようであれば生爪を固定するボルトを一本外した状態で加工しています。
ただし、危険をともなう作業になるので、条件は落として万が一生爪が外れても怪我のないように作業しましょう。
数物の場合②:切り割りを入れた治具を使う
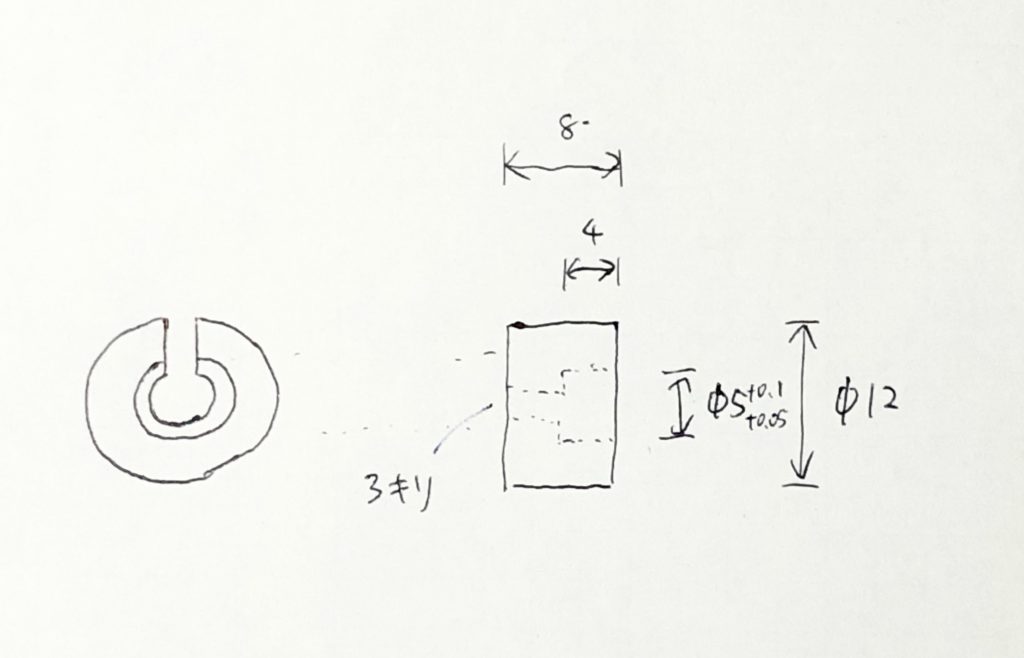
先程のφ5の数物の図面、もう一つやり方があります。
それは上図のような切り割りの治具を使う方法。
切り落とした後の部品をこの治具にセットし、治具ごとチャックに掴んで部品の端面を仕上げます。
作り方は簡単で、旋盤やNC旋盤で3キリとφ5エンドミルで加工し、割るだけです。
NC旋盤であればエンドミルを偏心させられるのでφ5をプラスめにすることも簡単です。公差はあくまで目安で、大きめになるぶんには+0.2くらいまでなら問題ないでしょう。
これならフライス加工も必要ありません。
割る方法は、勤務先ではコンタマシンを使いましたが、径が小さい分少々危険なため、治具をバイスでつかんで下画像のようなハンドソーを使うと安全に割ることができます。
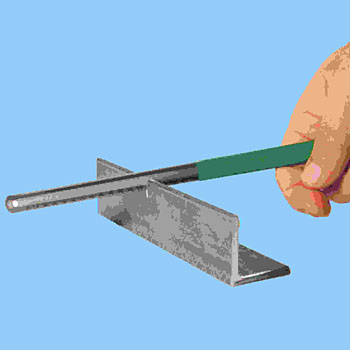
コメント
サブ側の爪をエンドミルでつつくだけでも、ワークの芯はでますか?
コメントありがとうございます!
サブ側の爪というのがわかりかねますが、爪を旋盤に装着した状態でチャックを回してエンドミルを使って旋削すれば、内径バイトで削るのと同様に芯は出ますよ。
参考になりましたら幸いです。