
表面粗さ(面粗度)の三角記号、現場の図面ではよく見ますよね。
実はこの書き方、1992年以前の書き方なんです。
ですが加工現場には残っている表記ですので、どのくらいの送り速度で送ればいいのか今回は参考までに計算して書き留めておきます。
今回記す数値はあくまで理論値ですので、実際の表面粗さとは異なる可能性があるためご注意ください!
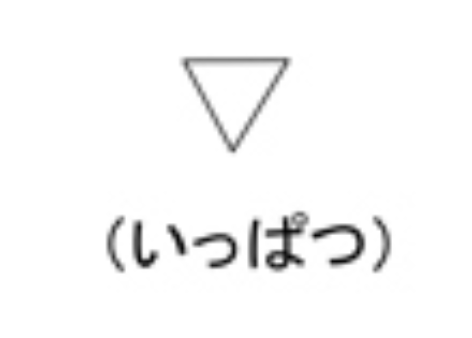
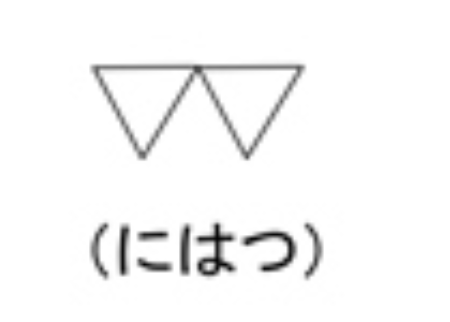
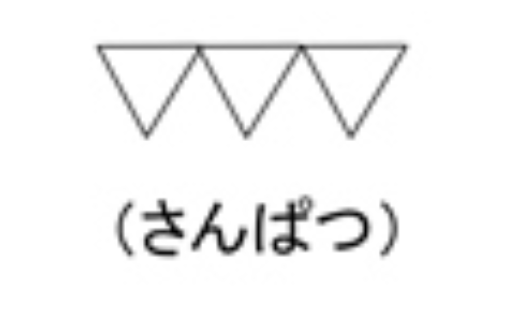
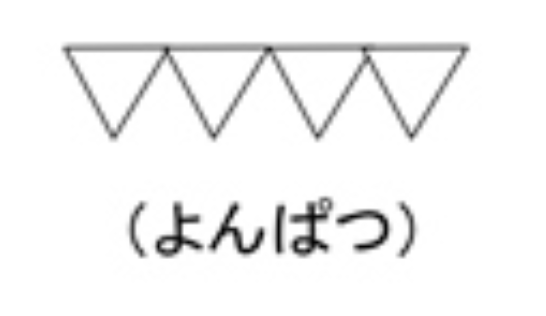
旋削加工の場合の送り速度
ノーズR0.2の場合
まずはノーズR0.2の場合の送り速度です。
1発:f=0.4mm/rev
2発:f=0.2mm/rev
3発:f=0.1mm/rev
ノーズRが大きくなっても理論仕上げ面粗さは良くなるだけなので、ノーズRが0.2より大きくなる分には上記の送り速度で大丈夫です。
四発は切削加工では理論値どおりに仕上げるのが難しいため、研磨で仕上げるのが無難です。
ノーズR0.4の場合
次にノーズR0.4の送り速度を書き留めておきます。
ノーズR0.4であればR0.2より理論上送り速度を上げることができます。
1発:f=0.56mm/rev
2発:f=0.28mm/rev
3発:f=0.14mm/rev
ただしくどいようですが、むしれなどが発生した場合は上記の送り速度でも理論値より大きく粗い表面粗さになってしまうので気をつけましょう。
フライス加工の場合の送り速度(φ10エンドミル理論値)
フライス加工は工具や加工方法が様々であるため、φ10のエンドミルによる側面削りの値とします。
1発:f=2mm/rev S1000のときF2000
2発:f=1mm/rev S1000のときF1000
3発:f=0.5mm/rev S1000のときF500
理論的にはかなり高い送り速度ということがわかります。しかし、以下の図を見てください
フライス削りの欄は、精密の部分でも3発になっています。旋削がそれ以上の表面粗さを加工できることを考えると、フライス削りは計算上の理論仕上げ面にはなりにくい加工といえます。
そのため、3発の加工面が必要な場合は、送りを0.1mm/rev以下にしておくのが無難といえます。
つまり、S1000であれば、F100ですね。
なお表面粗さの計算では、エンドミルの歯数は数えません。 エンドミルの刃の長さは完璧に同じとはいえないため、片方の刃でのみ表面を形成していると考えるからです。
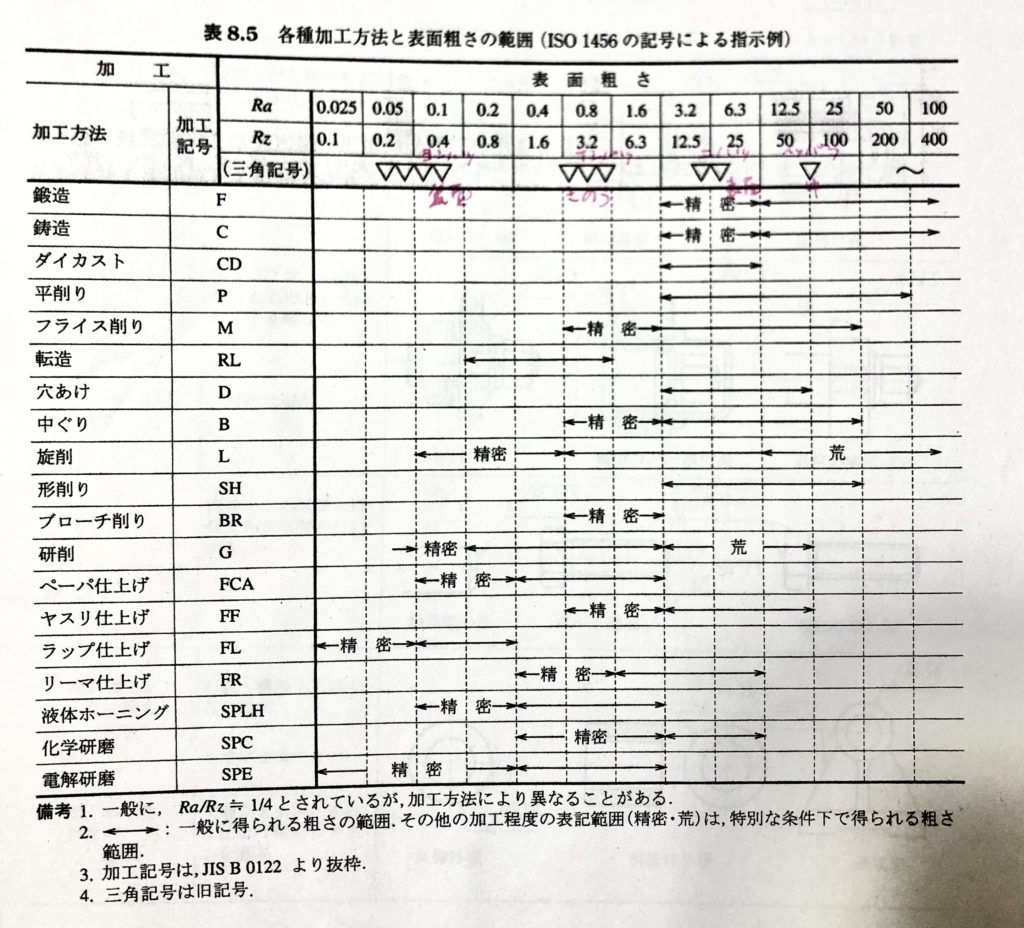
1〜3発って、どのくらいのRa,Rzなの?
大まかな値にはなりますが、1発2発3発に対応するRa,Rzは以下の通りです!
1発はRa12.5~25、Rz50〜100
2発はRa3.2~6.3、Rz12.5〜25
3発はRa0.4~1.6、Rz1.6〜6.3
図面によって、発数表記、Ra表記、Rz表記が分かれるので、大まかにでも把握しておくと便利です(^^
コメント