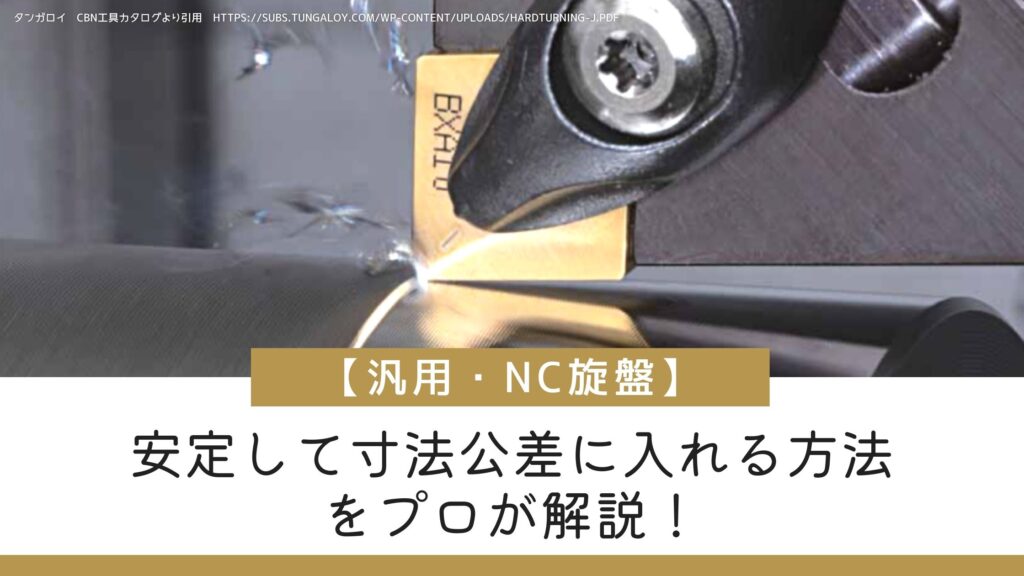
切削加工、特に旋盤加工は、そのほとんどがワークの寸法を「公差に入れる」ということが仕事です。
公差がない場合はそもそも旋盤で加工する必要がなく、切削という加工方法をとらなくても良い場合が多いくらいです。
本記事では現役旋盤工の私が、汎用・NC旋盤で寸法公差に正確に入れるコツをご紹介しました!
刃物の選び方
旋盤で公差に入れるためにまずポイントとなってくるのは、刃物(インサート・チップ)の選び方です。
私が使っている基本的な仕上げ用の刃物は2種類あります。
まずは一番良く使うものを紹介しますね。
コーテッドサーメットの精密仕上げ用のもの
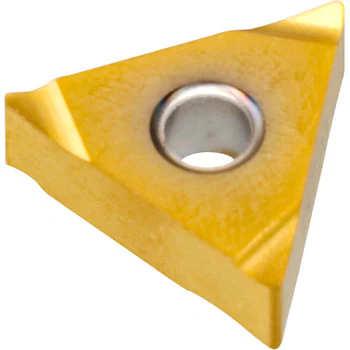
一番良く使う仕上げ用のチップがこちら。
被削材にもよりますが、比較的万能に使うことができるサーメット材種の鋭いブレーカーを持ったチップです。
私が使っているのは三菱マテリアルのTNGG160402-NX2525です。
追記:京セラのチップに変えました。型番はTNGG160402R-S PV720。上記のチップとほぼ同じ値段ながら、寿命が倍くらいに長い上、低切削速度でも摩耗しにくく、サーメットでありながら軽断続切削も可能です。圧倒的にこちらの方がおすすめです。
低切削速度域でもかなり表面を美しく光らせることができ、寸法も安定します。さらにノーズR0.2のものを選んでいることも相まって切削抵抗が低くびびりにくいこともポイントです。
ノーズRについてはこちらの記事を参考にしてください!
コーテッドサーメットのSブレーカーは各社取り揃えていますので、お好きな工具メーカーのものを使うと良いです。
比較した上で京セラ製のものを使っているわけではないので、同等以上の性能でもっとコスパが良いものがあるかもしれません。
被削材は鋼材・アルミニウムで使えます。
ステンレスはSUS303など加工しやすいものであれば問題ありませんが、SUS316やSUS304といった削りにくい材種ではかなり寿命が短くなってしまいます。
数ものを加工している最中にチップが傷んでしまっては公差を外してしまいますので、SUS304等削りにくいステンレスの場合は以下に紹介するチップをおすすめします。
他にもタンガロイ社の運営する切削コミュニティ「キリコミ」で、様々なおすすめのチップが投稿されていますので、ぜひご参考にされると良いと思います。
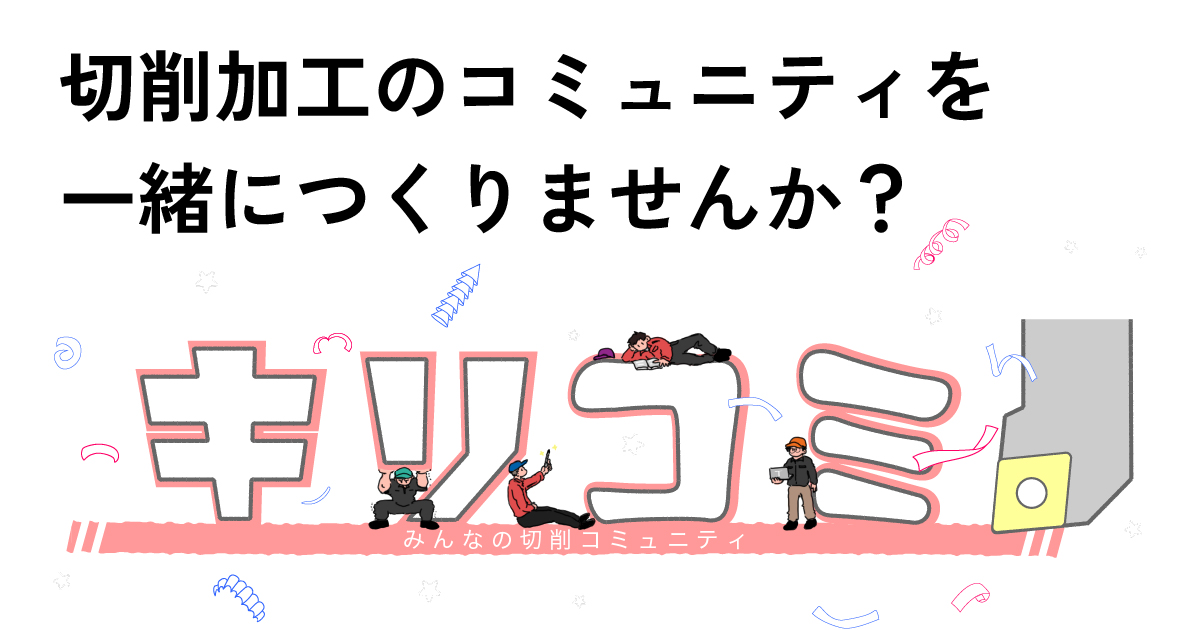
SUS304やSUS316等にはこのチップ
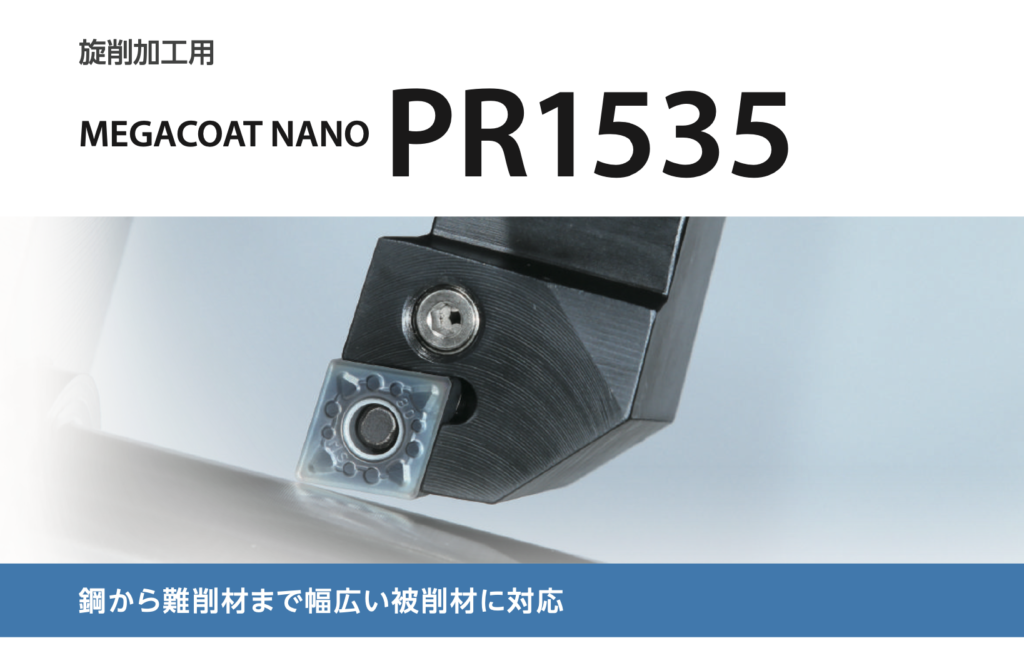

次に紹介するのはステンレス用に私が使っているチップです。
SUS304やSUS316を仕上げて公差に入れるのに特におすすめなのが京セラのこちらのチップです。
型番は TNGG160402MFP-SK PR1535
三角のものを使っています。ノーズR0.2ながらもSUS304などでもかなり長持ちしますので大変おすすめです。
仕上げ精度も十分です。
欠点としては鋼材では使えないこと。表面がザラザラになってしまうため、上で紹介したPV720を使わざるをえません。
アルミでは一応使えますしきれいに仕上がりますが、上で紹介したPV720のほうがさらにきれいに仕上がります。
外径の公差を仕上げる手順
チップの選定が終わったら、いよいよ仕上げ加工に入っていきます。
今回は材質S45Cのφ20外径のh7公差(φ20であれば-0.021~0mm)を仕上げることを想定して解説していきます。
荒加工では仕上げしろを0.2mm残す(NC旋盤の場合)
仕上げの前に荒加工を行っておきます。
荒加工での仕上げしろの量は、仕上げ加工に大きく影響する大切なポイントです。
私は通常、NC旋盤では荒加工での仕上げしろを直径値で0.2mm残しています。
加工ひずみや振れる可能性が想定される場合はは0.5mm、ときには1mm残す場合もあります。
汎用旋盤では、仕上げしろを0.5mm残しています。
仕上げしろはノーズRの半分(半径値)が基本です。つまり、ノーズR0.4でしたらはじめに0.4mmつけておく、ノーズR0.2でしたらはじめに0.2mmつけておくのが基本になります。
まずは仕上げしろの半分を削り、寸法を測定する
寸法を測定するために、荒加工で0.2mm残した仕上げしろのうち半分を削ります。今回であれば直径値で0.1mmだけ削るということですね。
機械操作としては、NC旋盤では仕上げの工具の摩耗補正Xを+0.1した上で仕上げのプログラムを動かします。
汎用旋盤であれば面当てしたところから、仕上げしろの半分だけ切り込んだ上でその点をゼロセットしておきます(例えば仕上げしろが直径値で0.5mmであれば0.25切り込みます)。
このとき、刃物はもちろん回転数や送り速度も最終仕上げと同じ条件で行ってください。条件を変えてしまうと最終仕上げの際に寸法がズレる可能性があります。
また、最も大事なポイントは仕上げしろの半分を狙って削ることです。
その理由は、測定のための前仕上げと最終仕上げで削る量が異なると、寸法がばらついてしまうからです。
例えば仕上げしろを0.5mm残しているのであれば0.25mm、0.8mm残しているのであれば0.4mm削ります。
マイクロメーターでの測定を正確に行い、仕上げ加工
削り終わったらマイクロメータを使って測定します。この測定がかなり重要な作業で、仕上げ精度はこれを正確に行えるかどうかにかかっているといっても過言ではありません。
今回は一例として、測定値がφ20.115だったとします。
公差はφ20(-0.021~0)ですので、φ20-0.016を狙います。(通常であれば公差の真ん中の-0.0105を狙うところですが、私の勤務先ではメッキが乗ることを考慮し、0.005mmほどマイナスめに仕上げています。)
測定の結果から、0.131を切り込み最終仕上げを行います。NC旋盤であれば摩耗補正を-0.131加算し、汎用旋盤であれば0.131ぶん切り込み仕上げます。
削り終わったら再度マイクロメーターで測定します。
問題なく削れていれば、公差に入っているはずです。
内径や端面の公差も基本的には同様
内径・端面も基本的に外径と同じやり方で仕上げることができます。内径の場合、測定器がマイクロメーターからシリンダーゲージに変わっただけです。
ちなみに内径加工で私の使っている刃物は、外径のものと同じサーメットNX2525の、勝手のついた精密仕上げ用ブレーカーでノーズR0.4のものです。
内径は削る量が外径より少ない事が多いため、ステンレスも含め全ての材質を同じチップで仕上げています。
削る環境によっては、材質に合わせて複数の仕上げチップを使い分けるのも良いと思います(^^
内径は栓ゲージを使って仕上げる方法も
内径は削る長さが短い場合、シリンダーゲージを使わず栓ゲージを使って仕上げる方法があります。
例えばφ20H7(0~+0.021)を仕上げる場合、ノギスで-0.03くらいまではじめに削っておき、公差範囲いっぱいである0.021ずつ切り込むことを栓ゲージが入るまで繰り返す方法です。
この方法であればシリンダーゲージの段取りをする必要がなく、仕上げの時間を短縮することができます。
ですが、この方法も良い点ばかりではありません。
後述しますが、0.02など切り込み量が極端に少ないと刃先の摩耗がかなり激しくなります。
そのため長さ30mm以内くらいの、摩耗が無視できる程度の長さの仕上げにしか使えないという点には注意しておく必要があります。
仕上げしろが少なすぎる状態で削るのは不良のもと!
仕上げしろが直径値で0.04mm以下くらいになると、刃物が材料に食いつかず、上滑りしてしまうため刃先の摩耗がかなり激しく進行します。
そのため40mmも削るとテーパーになってしまい、公差不良の原因になってしまいます。
なので、仕上げしろはある程度残した状態で一気に仕上げなければなりません。
念の為といって0.01mmほど大きめに仕上げて、追加で0.01mm削るというのは初心者はやってしまいがちですが、逆に仕上がり寸法が不安定になってしまいます。
また、切り込み量が小さすぎるのは摩耗の原因になるだけでなく、削りすぎの原因にもなります。
それまで切り込み量が0.1mmだったのに急に0.01mmになるわけですから、刃物やワークの逃げが全くなくなるため基本的には削りすぎます。
具体的には、大体狙ったところから0.01mmほど削りすぎてしまいます。
このような事態を防ぐため、切り込み量は0.07mm以上くらいは確保しておきましょう。
構成刃先に注意!
構成刃先とは、簡単に説明すると金属材料が刃先にくっついてしまうことです。
詳しくはこちらの記事を参照ください!
仕上げ切削で構成刃先が起こると表面がザラザラになってしまい、寸法も安定しません。
構成刃先の影響で削りすぎて不良になってしまうこともあります。
そのため切削温度を上げ、構成刃先が発生しない条件で削ることを心がけましょう。
切削温度を上げるためには回転数を上げる、切り込み量を増やすというのが王道の方法です。
荒加工ではワークが光るのも、切削温度が高く構成刃先が起こらないからですね。
チップを変えても表面がザラザラになるという場合は、この方法で構成刃先を回避できないか試してみましょう!
新品のチップは摩耗しやすい
新品のチップは刃先が鋭利すぎる状態になっているため、摩耗しやすいです。
油断すると削るにしたがって太くなっていくテーパーになってしまったり、削り残しがでて公差から外してしまう可能性があります。
チップを交換した場合は、数回加工して寸法が安定するまでこのことを頭において作業するようにしましょう。
機械のクセにも注意
機械のクセで、手順通り加工しても寸法がズレてしまうこともめずらしくありません。機械のクセを把握し、例えば仕上げ加工で0.01マイナスする傾向にあるならあらかじめ0.01摩耗補正をプラス側に入れておくなど、対策しておくのが得策です。
A5052など粘っこいアルミは0.02ほど残すことできれいになる
A5052や5056などのアルミはかなりむしれやすいです。
公差の入った面を仕上げるということは、寸法を出すだけでなく表面を美しくするということも含まれます。
A5052のようなむしれやすい材質を仕上げるためには、面倒ですが、仕上げしろを0.5→0.1→0.02→0と分けて仕上げるようにします(NC旋盤の場合)
最終的に0.02とかなり小さい取りしろで仕上げるのは、自身の切り粉の影響でむしれが発生してしまうことを防ぐためです。
0.02だけ削った切り粉であればむしれの原因になることはありませんし、これほど柔らかい素材であれば刃先の摩耗も気にすることなく加工できます。
条件をうまく調整すれば通常通りの仕上げ回数で仕上げることも可能ですので、数が多い場合は色々試してみてください。
チップと材質の組み合わせによっては鏡面加工も可能
こちらはHORN社のダイヤモンド工具で真鍮を鏡面加工した動画です。
チップと材質の組み合わせによっては、こういった加工も可能です。
最後に:表面の仕上げは最終工程。慎重に行おう
仕上げは最終工程です。少しでも削りすぎて公差を外してしまうとオシャカ(不良)になってしまい、荒加工からやりなおしになってしまうため本当に気を遣う作業ですよね。
切り込んだ数値通りにいかないことも多い仕上げ加工ですが、ポイントさえつかんでしまえば安定して加工できるようになります。
厳しい公差も、無事に仕上げられたときは達成感を感じることができるはずです。
ちなみに冒頭の画像にはタンガロイさんのCBN工具カタログのものを使わせていただきました!
↓こちらの記事でも触れていますが、強断続切削用のラインナップまであるこだわりのCBNインサートです。
コメント