
「高送りカッター」とは、その名の通り、従来の工具と比べて大変高い送り速度で加工することができるミーリングカッターです。
うまく活用できれば、普段の荒加工を大幅に効率的に行うことができるようになります。
本記事では高送りカッターの加工原理から、切削条件、加工のコツ、おすすめのメーカーまで、現役加工技術者である私が幅広く解説しました!
ご使用経験がない方はもちろん、使ったことがあるという方も、しっかりと仕組みや最適な条件を理解できているかというと不安な場合もあるかと思います。
同じように加工していても、本記事で原則を学んでいただければトラブルへの対処もしやすくなるかと思います。
なるべく読みやすく解説していますので、ぜひ日々の加工や学習にお役立てください。
高送りカッターのおすすめメーカーを知りたい方は、記事下部に記載していますのでこちらからスキップしてください。
高送りカッターでの加工を解説!
高送りカッターは、一般的な刃先交換式エンドミル(ミーリングカッター)と似た形状ですが、その名の通り、ときには通常のカッターの10倍以上の大変速い送り速度で加工することが可能です。
推奨切削条件通りに加工すれば基本的には問題ありませんが、条件を上げられる原理を理解して使うことで、条件の調整などの際にチップの寿命が極端に短くなったりといったトラブルを未然に防ぐことができます。
そこで、まずは高送りカッターの基本について解説します。
用途
高送りカッターは、荒加工を速く、それでいてなるべく機械に負荷をかけずに行うことを目的として使われます。
動画はHORN社のものですが、大変速く加工が進んでいるのが分かるかと思います。
荒加工が主になるため、高送りカッターで加工した後の加工面は、基本的にエンドミルで仕上げ加工を行い精度を出します。
底面の平面になる部分については、材質によっては、送りを落とすことでそのまま仕上げ面とすることも可能です。
原理
高送りカッタは、刃先交換式の肩削りカッタやフルバックと異なり、刃先の外周部がわずか高くなった形状をしています。
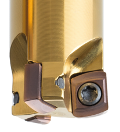
一見すると、加工面の端を仕上げることができないため不便な形状に見えますが、この刃先形状が高送りが実現できる理由になります。
この原理を解説するのに非常にわかりやすい図を見つけましたので、引用させていただきました。
刃先への切削抵抗を考えるにおいて、非常に重要な要素が“切りくず厚さ“です。切屑厚さは、当然薄いほど切削抵抗は小さくなります。高送りカッタは、切りくず厚さを最小化するために、 切り込み角を極限まで小さくする工夫がなされています。
図を見ていただければわかる通り、同じ切りくず厚さを削り出すとすると、チップの切り込み角が小さくなればなるほど刃あたり送りを上げることができることがわかります。
また、切り込み角を小さくすることで、切削抵抗のほとんどが径方向ではなく軸方向にかかるようになり、びびりにくく切削安定性が増します。
これらが、高送りカッターで送りを大きく上げられる仕組みです。
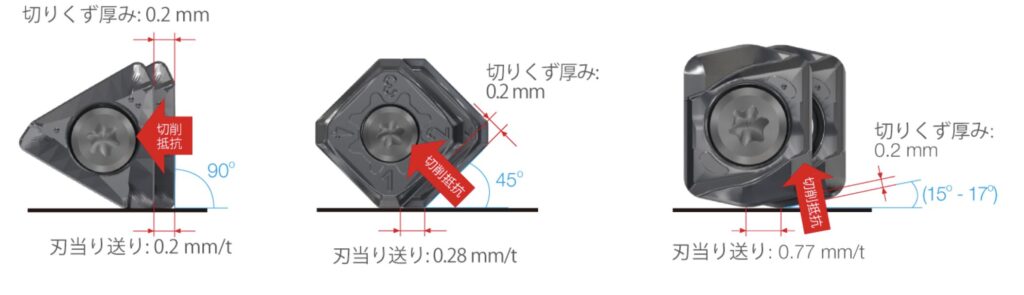
メリット
高送りカッタのメリットは以下のとおりです。
- 荒加工の速度が速い
- 工具への負荷が小さい
- びびりにくい
- 機械剛性が比較的必要ない
- 底面が比較的フラットに近いため、中仕上げ加工が必要ない
デメリット
- パス回数が多くなりがちなため、プログラムが長く複雑化しがちで、CAMが必要。
- ワークに軸方向の剛性が必要。
- 底面がフラットにならない
以上のメリット・デメリットを踏まえたうえで、エンドミルや肩削りカッタと比較しながら目的に合った工具を使いましょう。
高送りカッターの種類
高送りカッターは、様々な製品がラインアップされています。
主に選択する必要があるのは、「サイズ」「刃数」「チップ」です。
サイズ(径)
高送りカッタは、Φ12〜Φ125くらいの範囲で様々な径のものがラインアップされています。
どのサイズのカッタを選べば良い?
高送りカッタは、パス数を少なくして能率を高めるために、ワークの加工領域に応じて、機械剛性の許す範囲で可能な限り大きいカッタを選ぶのがベストです。
ですが、比較的高価な工具なので、自社に合った加工に絞って選択すると良いです。
私の勤務先では、Φ32とΦ63をよく使います。負荷と加工範囲のバランスが丁度良いためです。
普段使いであるΦ10のエンドミルを使った荒加工よりも明らかに速いため重宝します。
刃数
高送りカッターに限らず、 フライスカッターは刃数が多ければ多いほど送り速度を上げることができます。
またその一方で、刃数多いほど チップポケットが小さくなり傾向がはけにくくなります。また、構造上チップを大きくしにくいというデメリットもあります。
ほとんどのモデルではその径に最適な刃数があらかじめ設定されていますが、数を選択できるモデルで迷った場合は、切粉のはけやチップの大きさ(切込量)を重視したいのか、送り速度を重視したいのかを考えて選ぶと良いです。
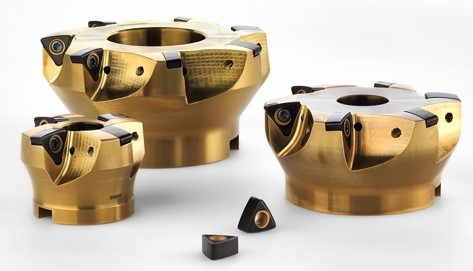
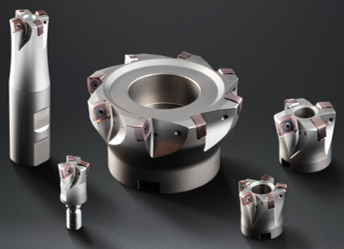

チップ
チップ(インサート)形状は、主に2コーナーの長方形に近い形と、4コーナーの正方形に近い形が使われることが多いです。また、メーカーによっては三角形のチップも使われます。
チップで大きく経済性を左右するのが、両面使えるかどうかという点です。HORN社のDAH82,84のように、正方形に近い形のインサートで8コーナー使えるものもあります。
どの形状も、限られたスペースの中で最大の有効刃長とコーナー数を両立させられるように、各メーカーで研究を重ねて設計されています。
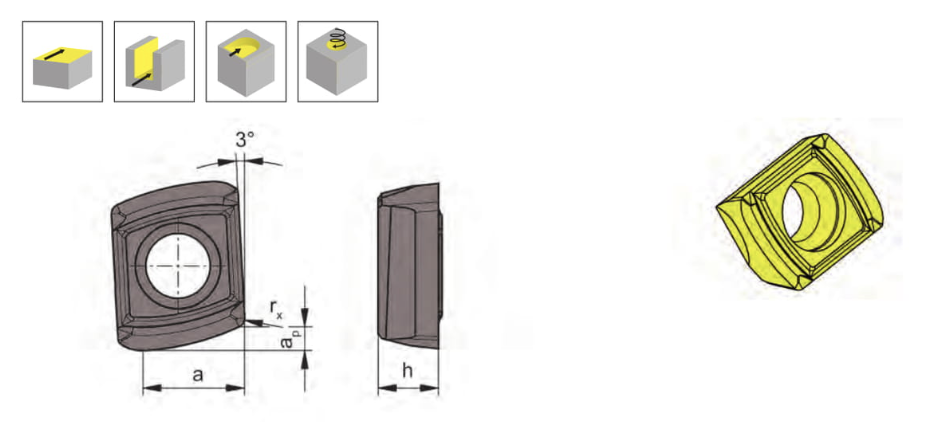
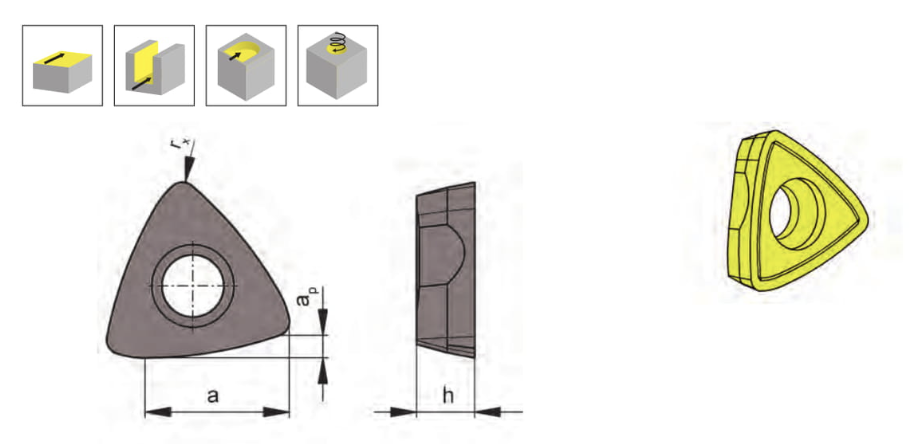
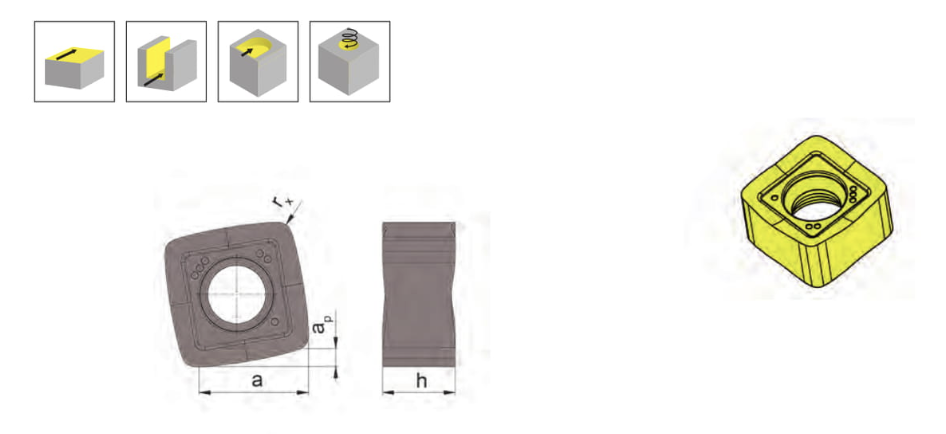
また、コーティングも様々なものから選ぶことができます。例えばHORN社では、2022年秋にSA6A、IG6Bという2種類のコーティングが新発売され、3種類から選択することができます。詳しくはカタログをご覧ください。
一つの工具で高送りと高切り込み、両方の加工に対応したい場合は、丸コマインサートのカッターを選ぶのも一つの手です。
低切込時は切り込み角が小さいため高送りに適し、2mm以上大きく切り込んだ場合は切り込み角が大きい相当になるため、送りを下げた重切削に適します。
両方に使える分、どちらで使うにしても専用の工具には性能が及ばず、最適な切削条件も切り込み量によって大きく変化するため、扱いが難しいチップ形状でもあります。
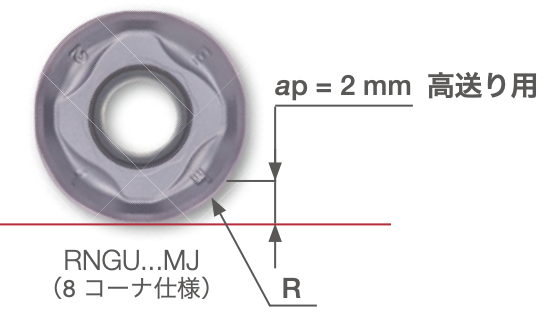
高送りカッターの切削条件
高送りカッターは、適切な切削条件を設定しないと十分な性能を発揮することができません。本項では一例として汎用性が高い「DAH84」(HORN社)のΦ63を例としてその切削条件をご紹介します。
インサートは2022年秋発売の、最も汎用性の高い「IG6B」を使用する想定です。鋼材を主とし、ステンレスやチタンなど、様々な材質に対応できます。
鋼材
まずは鋼材での切削条件をご紹介します。
推奨条件の中の限界ではなく、実際に安定して使えるレベルの切削条件を記載しています。
切込量ap=1.5mm
切削速度V=200mm/min
刃あたり送りfz=1.5mm/rev
5枚刃Φ63のため、テーブル送りF=7578mm/min
これがもし刃先にサーメットを使った肩削りカッターでしたらap=2mmで切り込み、F=250mm/min程度で送るのが通常の速度になります。
送り速度は、サーメットの肩削りカッターの実に30倍になります。
切り込み量が減ったのを加味したとしても、約23倍の加工能率で加工することが可能なことがわかります。
以下は実際にこの条件で加工を行っている動画です。
SUS304
同じ工具で切削速度Vを半分程度に落とせば、SUS304の高送り加工も可能です。本当にそんなことが可能なのか半信半疑の方もいらっしゃると思いますので、YouTube動画を掲載しておきます。
日本では手に入らない海外工具の動画ですが、工具の構造は同じです。以下の条件で加工しています。
切込量ap=1.27mm
切削速度V=67mm/min
刃あたり送りfz=1.7mm/rev
7枚刃Φ50のため、テーブル送りF=5080mm/min
※切削幅は28mm(工具径の56%)
切削幅56%で工具全体で削っておらず、7枚刃の工具とはいえ、テーブル送りF=5080mm/minでSUS304を安定的に加工できています。
仕上げの切削条件
底面のストレート部をそのまま仕上げ面としたい場合は、仕上げのパスのみ送り速度を落として加工しましょう。
SUS系や一部を除く鋼材などむしれにくい材質であれば、そのまま仕上げ面とすることができます。
高送りカッタを使った加工のコツ
高送りカッターは、高い効率で加工できる分通常のカッターとは少し違った注意点があります。
本項では、タンガロイ社の切削コミュニティ「キリコミ」運営様の解説の内容を参考にさせていただき、「工具寿命が短い」「難削材でチップがすぐ欠ける」といったトラブルを防ぐための加工のコツをご紹介します。
コーナーR部を超えない
高送りカッターの加工では、コーナー部にかからないところまでの切り込み量で抑えることが大変重要です。
もしコーナーに切り込みがかかってしまう部分が出てしまうと、下図のようにコーナー部の切り取り厚さが厚くなってしまいます。
先述のとおり、高送りカッターは切り取り厚さが可能な限り薄くなるように設計された工具で、その最大切込量はコーナーRに届かないところまでに設定されています。
そのためコーナーを超えて切り込んでしまうと、その部分は高送りでない通常のミーリングカッターと同等になってしまい、高送りで加工するとチッピングの原因になります。
工具の性能を発揮するために、必ずカタログ掲載の最大切込量未満で使用するようにしましょう。
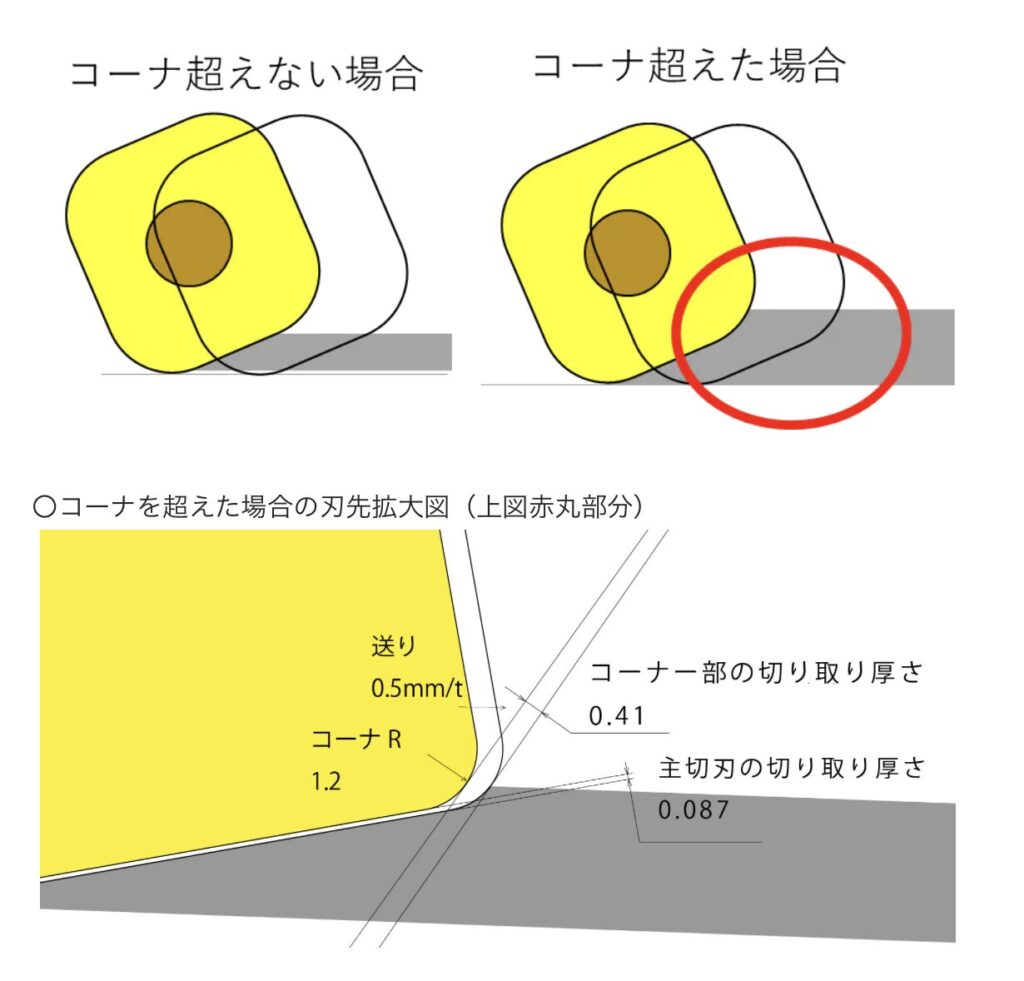
それでも大きく切り込みたい場合は、チップが大きい高送りカッターを選びましょう。
例えばHORN社の工具であれば、DAH82であれば最大切り込み量は1mmですが、DAH84であればチップが大きくなるため、同じ径でも最大切り込み量は1.5mmになります。
「食いつき厚く、抜け際薄く」を意識する
これはエンドミルを含む、フライスカッター全般に言えることですが、「食いつき厚く、抜け際薄く」を守って加工することが肝要です。
どういう意味かといいますと、ワークを削る際に、食いつき部で切り屑が分厚く、抜けぎわで切りくずが薄くなるようなカッターパスが理想ということです。
特に抜けぎわが重要で、抜けぎわで切りくずが厚いと分厚い金属片ををちぎり取るような挙動が発生してしまい、突発的な欠損が発生しやすくなります。特に超硬工具ではハイスと比べて靭性が小さく、この挙動で刃先が傷みやすいです。
具体的には、下図のように、「食いつき厚く、抜け際薄く」になる位置で加工を行います。
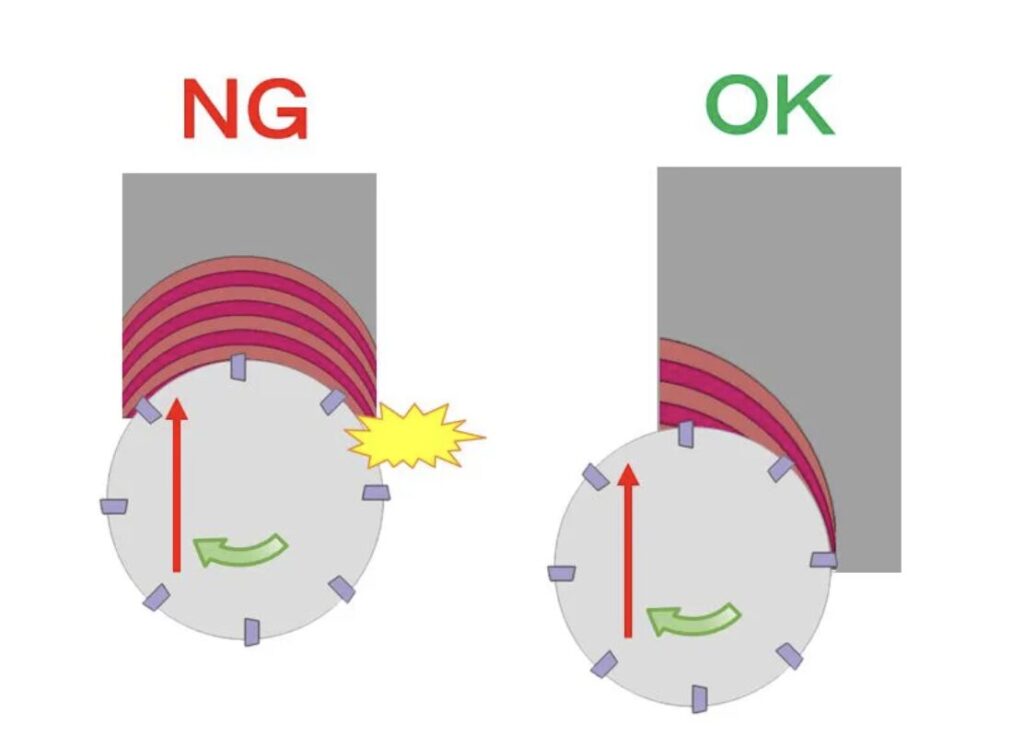
また、穴の上を加工する断続加工においても同様です。
下図NG例のように、 工具の真ん中に穴が来るようなカッターパスを設定してしまうと、切りくず厚さが最も厚い部分で穴にかかることになってしまうため、「抜け際薄く」が守られない状態になってしまいます。
そのため下図OK例のようなカッターパスに変更することで、抜け際の切りくずが薄くなり、工具寿命を伸ばすことができます。
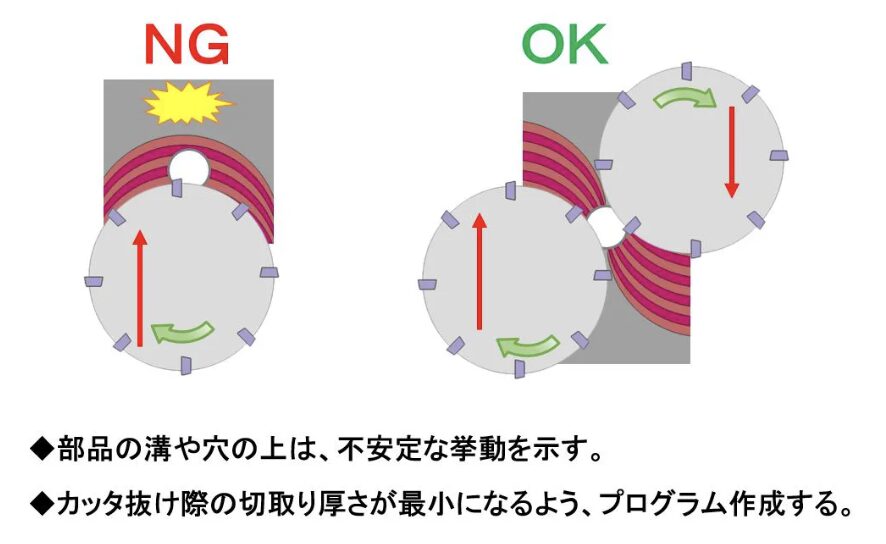
チップの傷み方に合わせた対策を取る
加工のご経験がある方は納得していただけると思いますが、フライスカッターでチップを交換する際は、大概は通常摩耗ではなく欠損によって交換になります。
欠損の仕方は様々ですが、その欠損の原因を把握してそれに合わせた対策を取ることで、工具寿命を伸ばすことができます。
本項では、主な4つの欠損のしかたと、それぞれに合わせた対策をご紹介します。
写真も合わせてご紹介していますので、ご自身のカッターの状態と見比べて、それに合わせた対策を取るためにご活用ください。
切削速度が高すぎる
まず、下の写真の”刃先強度不足”、”サーマルクラック”、”クレーター摩耗”による欠損は、 切削速度を下げることによって改善する場合があります。
刃先強度不足による欠損については、より剛性の高いブレーカーを選んだり、靭性の高いチップ素材を選ぶことで改善しやすいです。
サーマルクラックは、急激な温度変化が原因の損傷ですので、クーラント使って加工されているなら、乾式加工を試してみてください。
クレーター摩耗については送り速度を落とすことも効果的です。
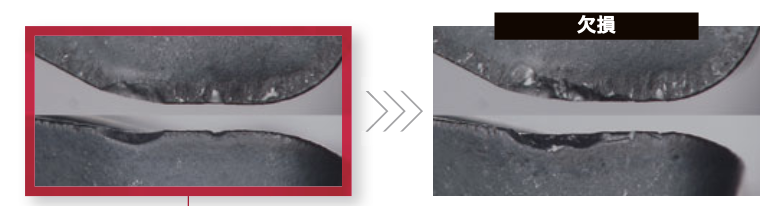
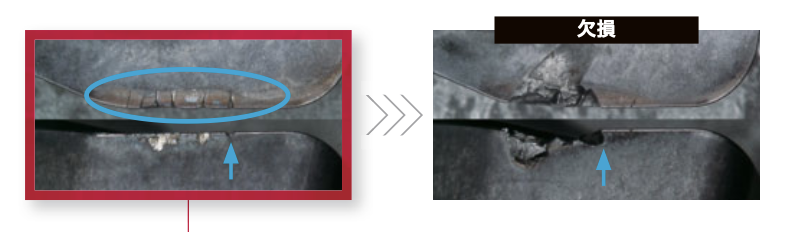
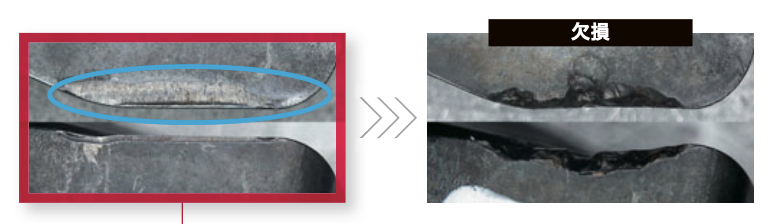
切削速度が低すぎる
逆に切削速度が低すぎることで起こる損傷が、溶着に起因する欠損です。
切削速度が低いことによって切削温度が十分に上がらないと溶着が起こりやすくなります。そしてその溶着した構成刃先が脱落する際に欠損が起こります。
この場合は切削速度を上げることによって改善することができます。
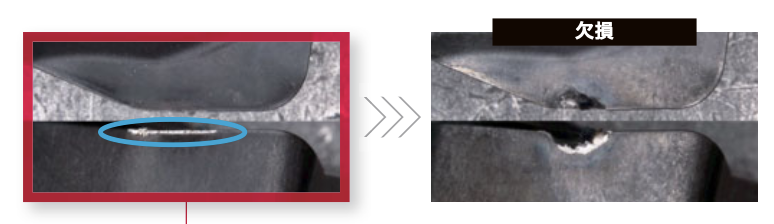
高送りカッターの比較とおすすめ工具
高送りカッターのおすすめメーカー
京セラ・タンガロイなど国内メーカー
高送りカッタを検討するにあたって、まず候補に上がるのが国内メーカーかと思います。
私も各社カタログを見てみましたが、特に小径のツールがラインアップされているタンガロイ・京セラがおすすめです。
一方で、カッタは一度買うと何年も長期的に使うものですので、少し値ははりますが、ドイツのメーカー「HORN」の高剛性なカッタを購入できればベストです。
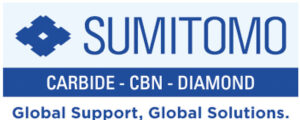
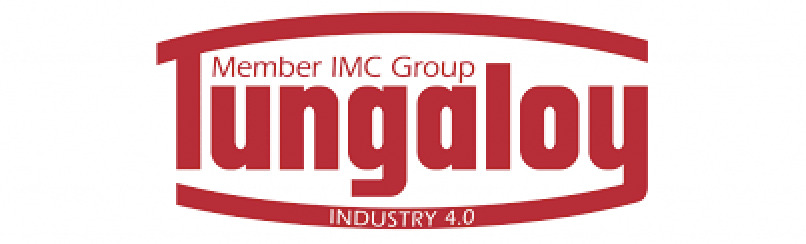
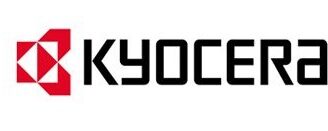

HORN
当サイトで推しているのがHORNの高送りカッタです。
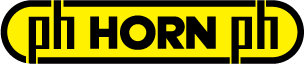
HORNはドイツの工具メーカーで、大企業であるにもかかわらず溝入れ工具に特化しているのが特徴です。
世界70ヶ国以上に展開する海外では大変有名なメーカーで、日本での知名度も急速に高まってきていますのでご存じの方も多いのではないでしょうか。
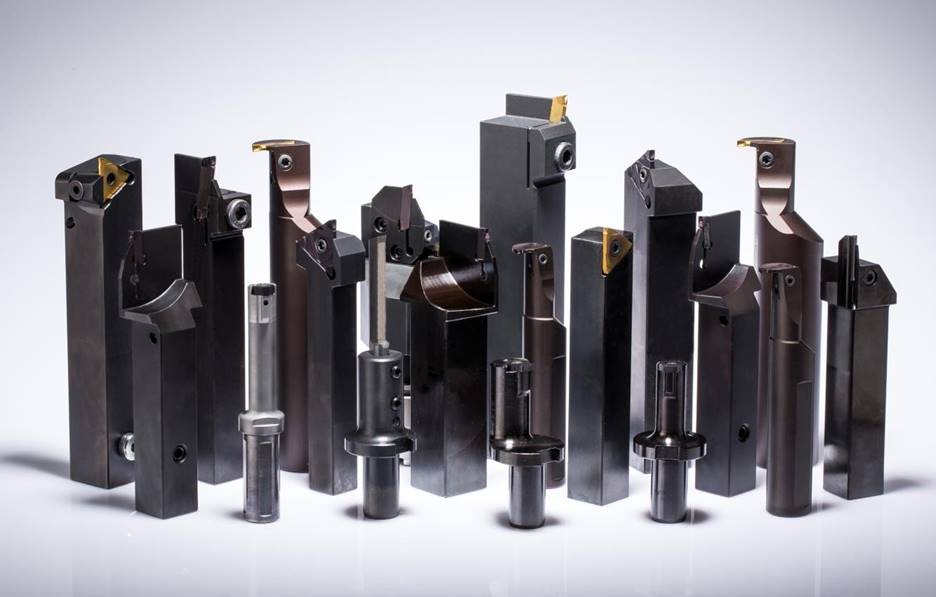
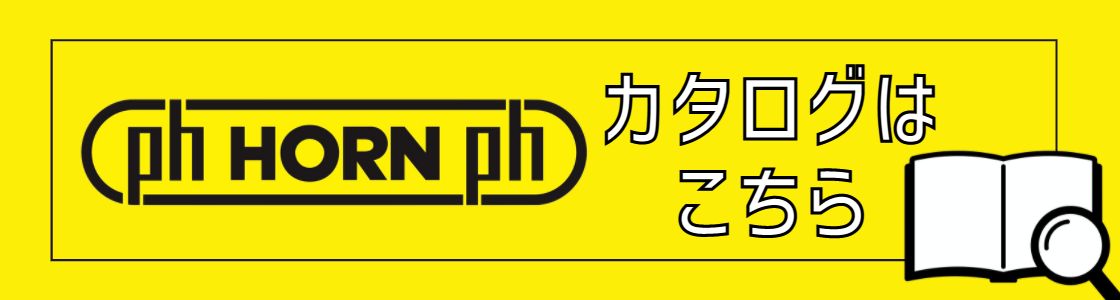
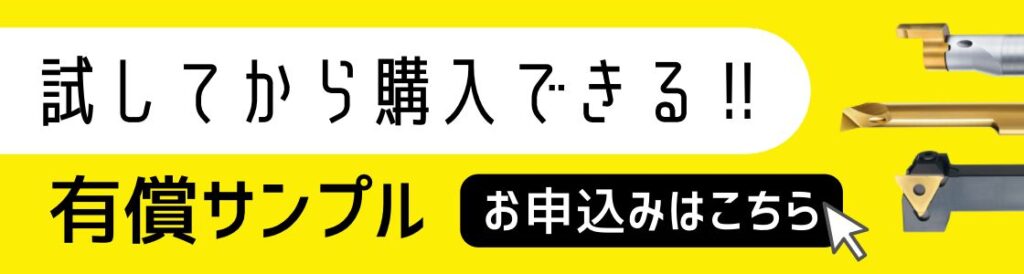
HORN社製カッタを推す理由
まず、工具本体全てに剛性にこだわったプリハードン鋼が使われており、びびりに強いです。
また、下図のようにインサート全体が直線に近い複合R形状で、切り込んだ部分全体で切削できる形状なので、同じ切込量でも他メーカー製のものよりも切込み角を小さくすることがき、より安定的に送り速度を上げることができます。
少し難しく書いてしまいましたが、要するにインサート形状が高送りに完全に特化しているということです。
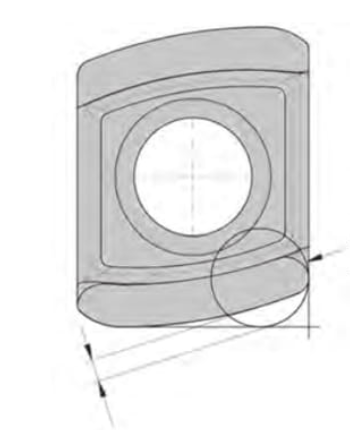
そして、DAH82,84でメインで使われているインサートが8コーナー仕様なのが大きなメリットです。 国内メーカーでは8コーナーは調べた範囲では見つからなかったため、ランニングコストを大きく下げることができます。
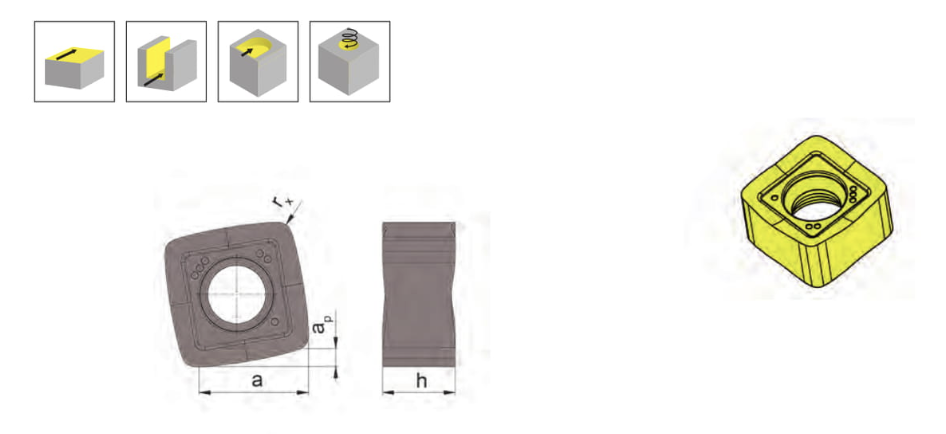
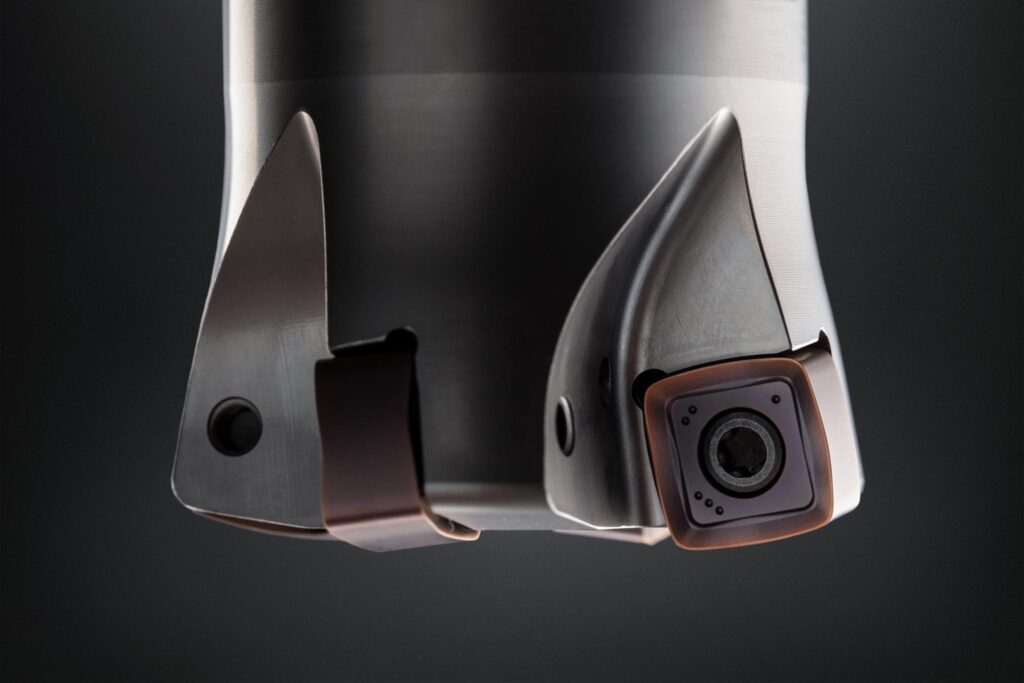
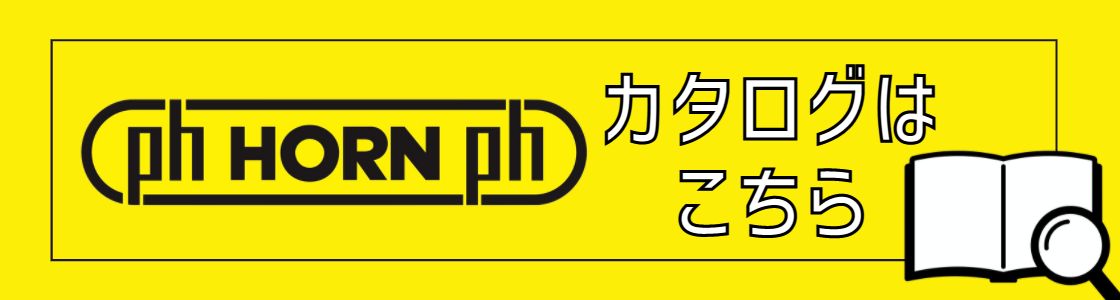
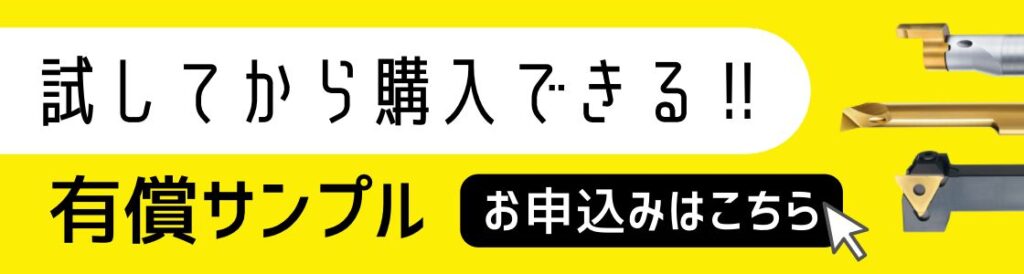
加工事例
HORN社カッターの加工事例をご紹介します。同条件で加工を行っていながら他社製品と比較して振動が少なく、面粗度も良くなっていることが分かります。
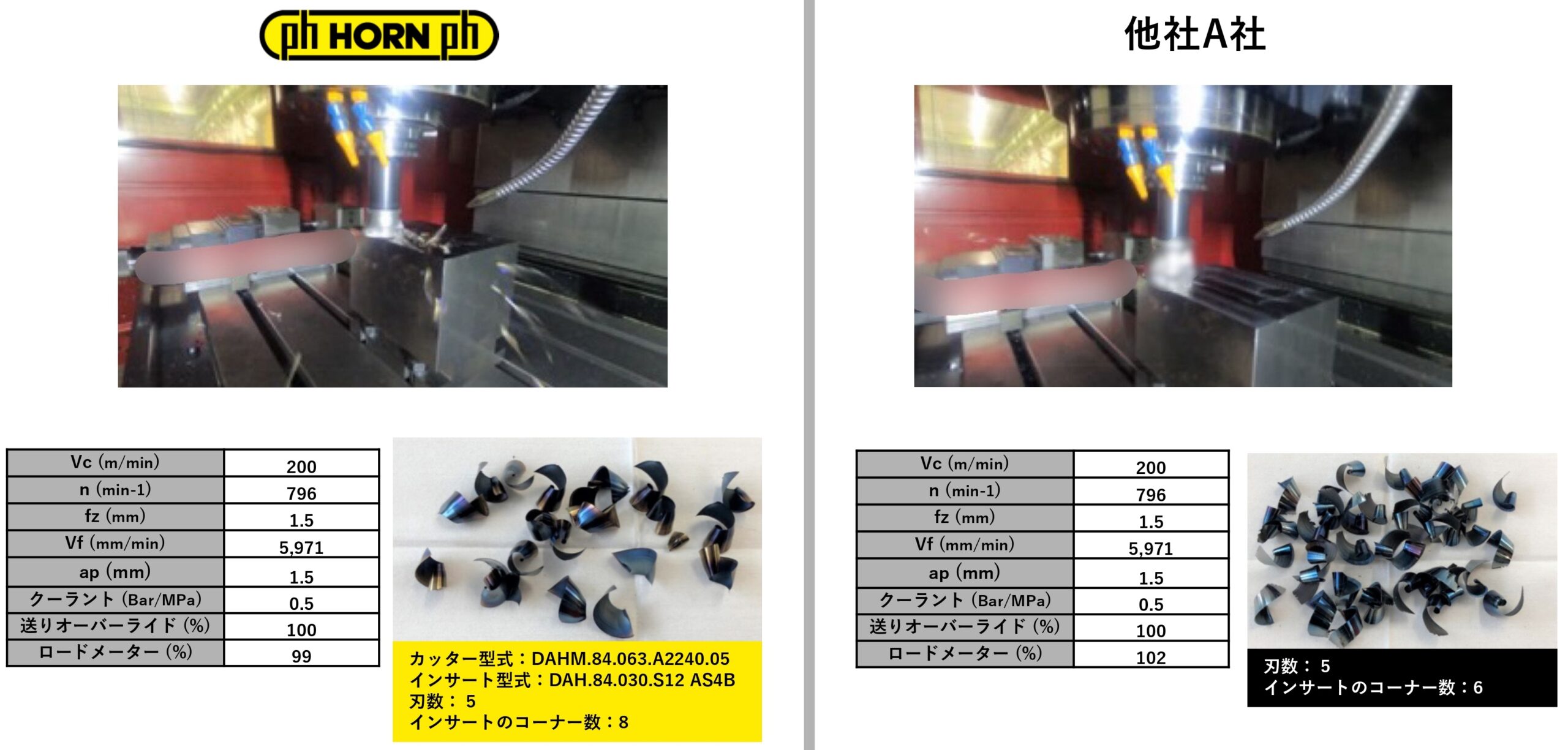
縦形マシニングセンター NIDEC OKK VM660Rにて試験。主軸:#50、被削材:C50、クーラント:エアー、出力:最大 26kw/22kw、ワーククランプ:ねじ止めクランプ、ロードメーター値:主軸の値を計測
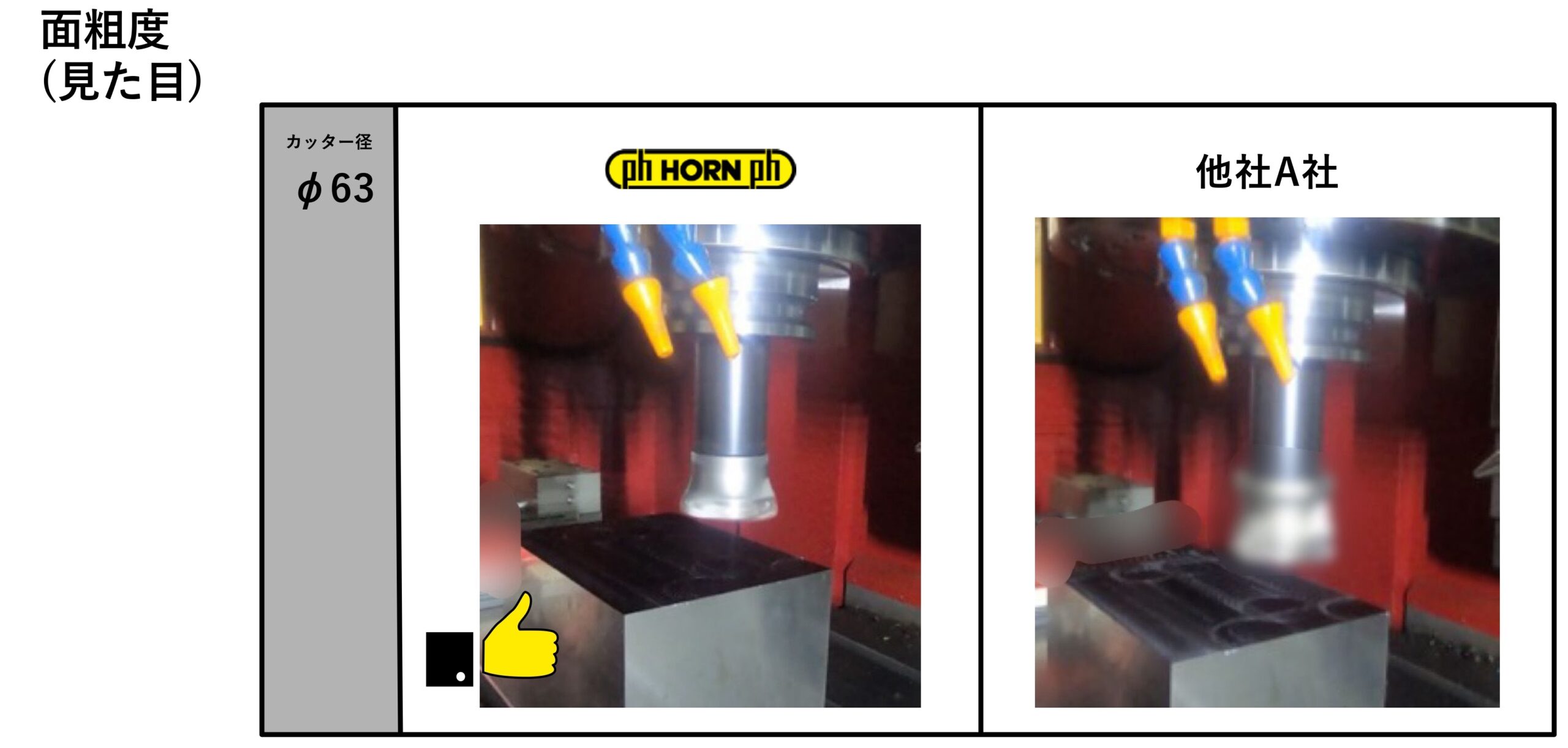
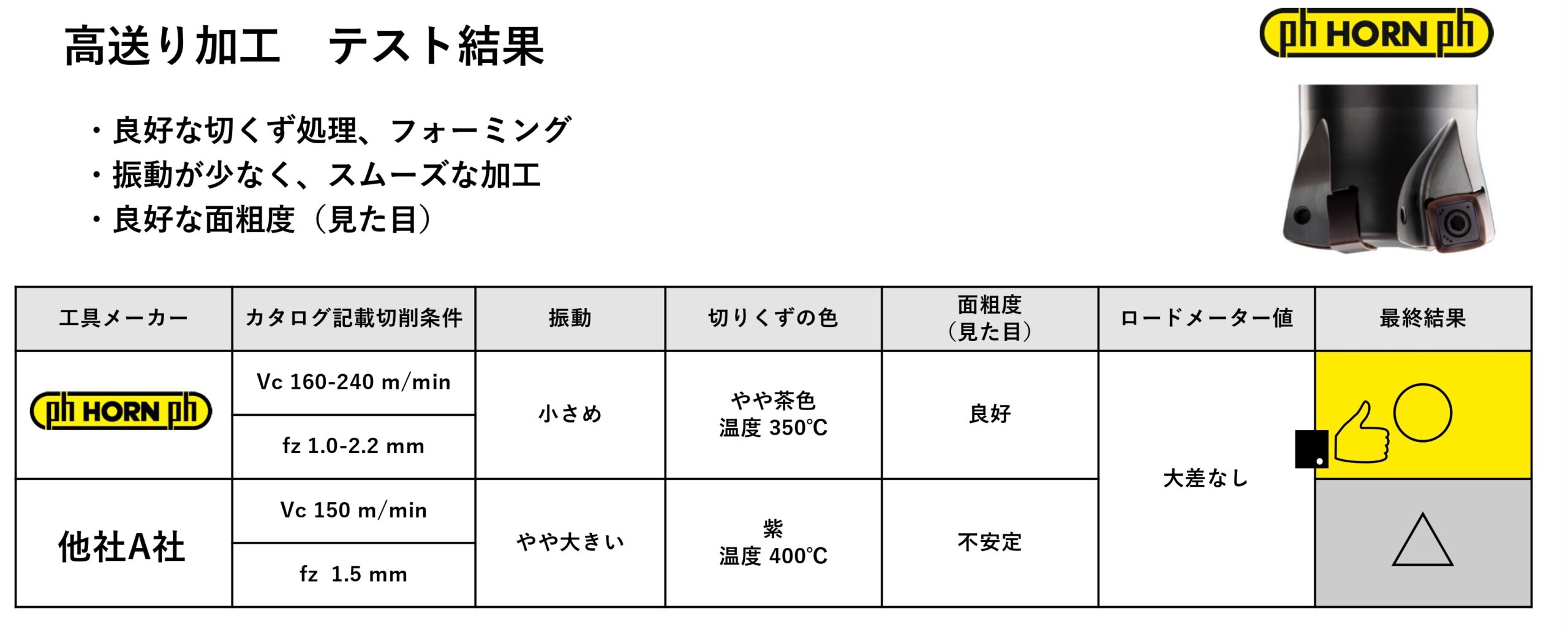
HORN社高送りカッターのラインアップ
HORNの高送りカッターは、インサート形状で主に3種類に分けられます。
そのどれもが、鋼材で刃あたり送りf=1.8mm/rev以上で送ることができます。
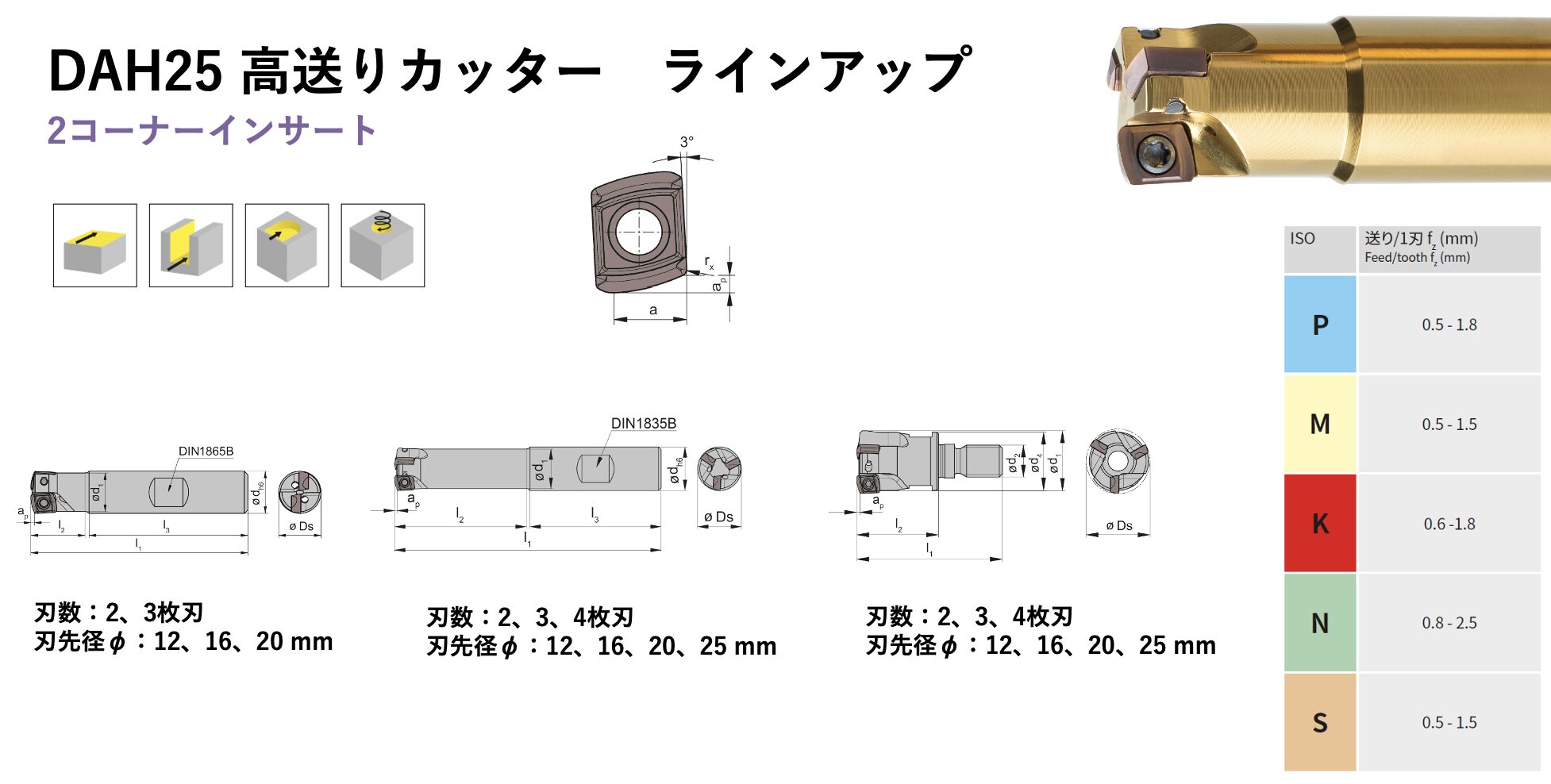
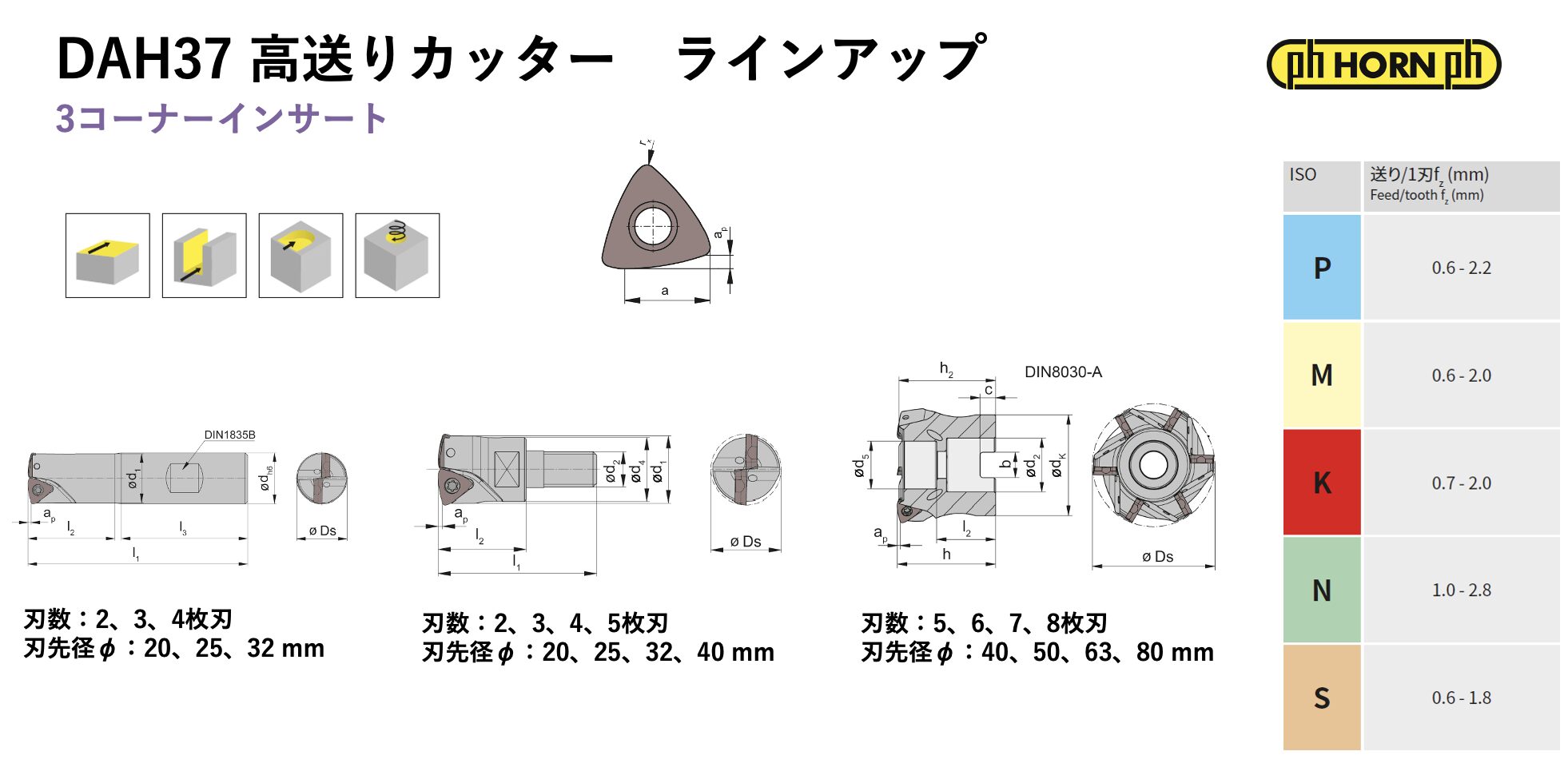
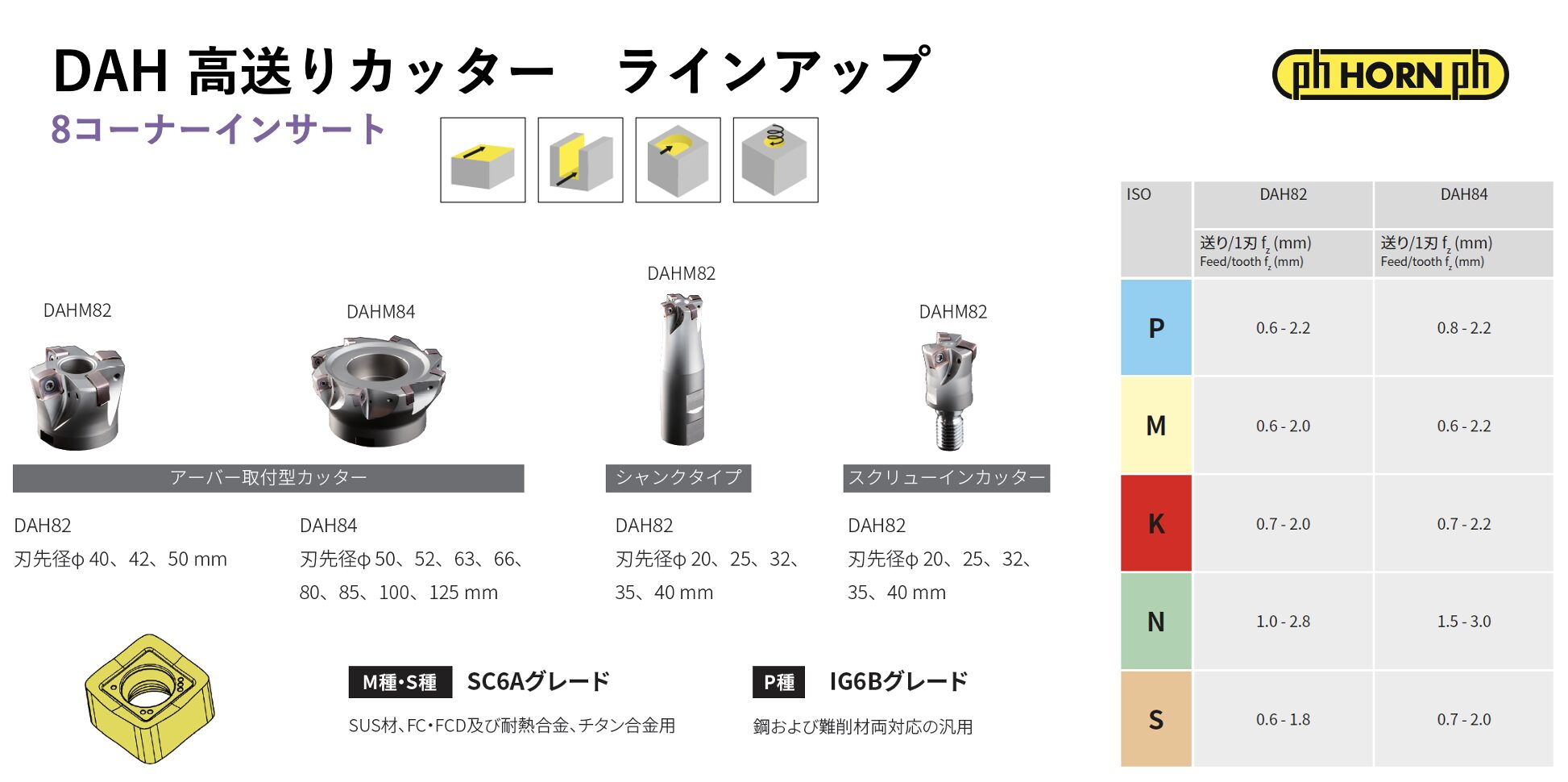
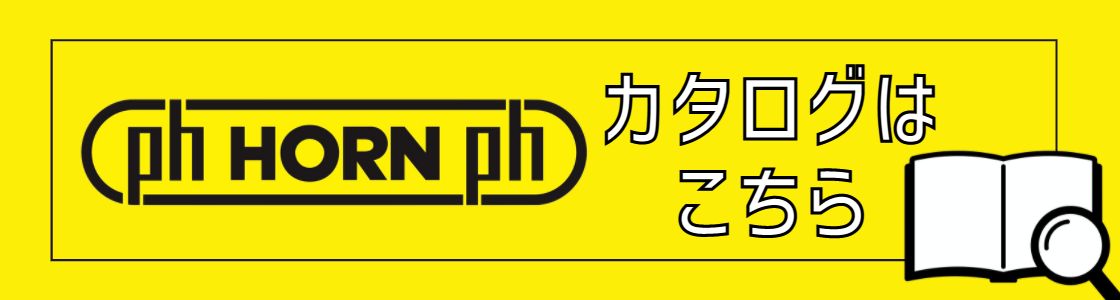
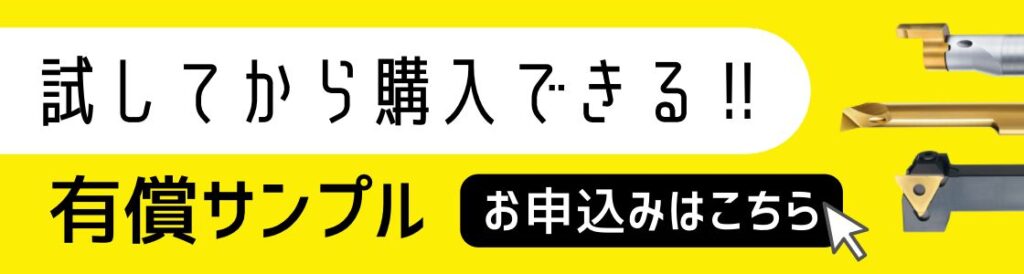
2024年最新版!溝入れフライス総合カタログ
溝入れフライスをはじめとした、各種フライスカッターが掲載された最新カタログの日本語版が新たに制作されました!
この機会にぜひご覧ください。
→HORN社公式 溝入れフライス・フライスカッターのカタログを見る
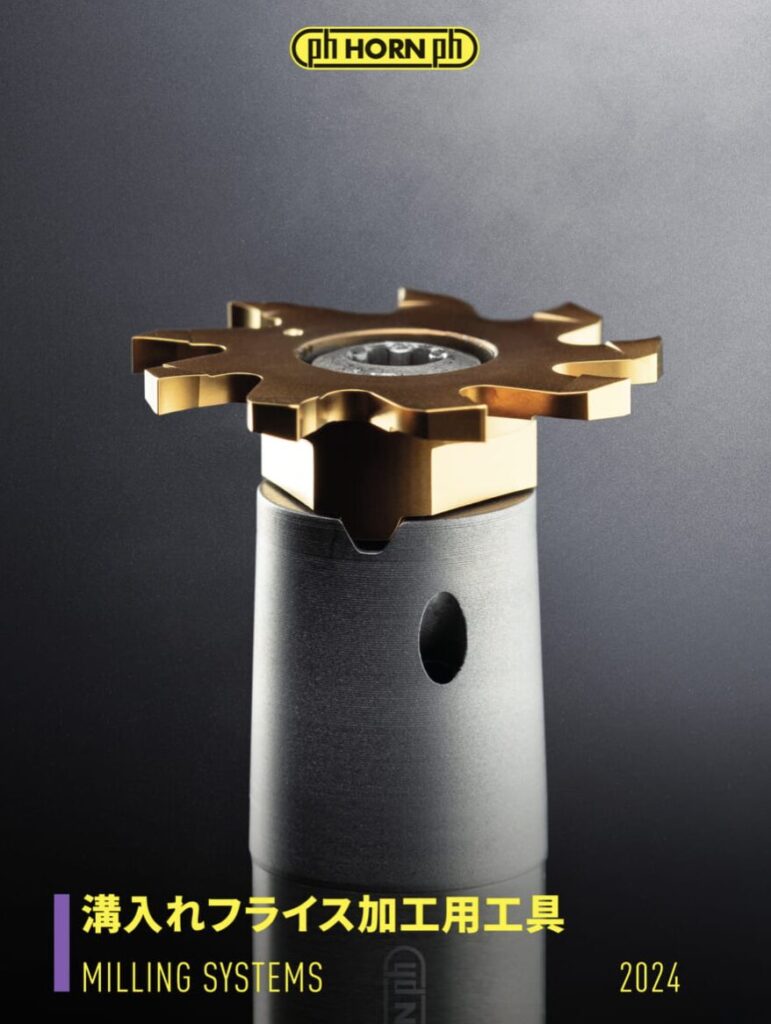
工具選定の電話相談も可能
海外メーカーというと、サポート面が不安な印象もありますが、HORNはその点も充実しています。
下記の電話窓口より、国内の工具メーカーと同様に電話で技術相談を受け付けています!
こちらの電話番号(IZUSHI 刈谷テクニカルセンター)で電話相談が可能です。
→HORN工具に関する技術相談窓口(IZUSHI 刈谷テクニカルセンター)TEL:0566-62-8075
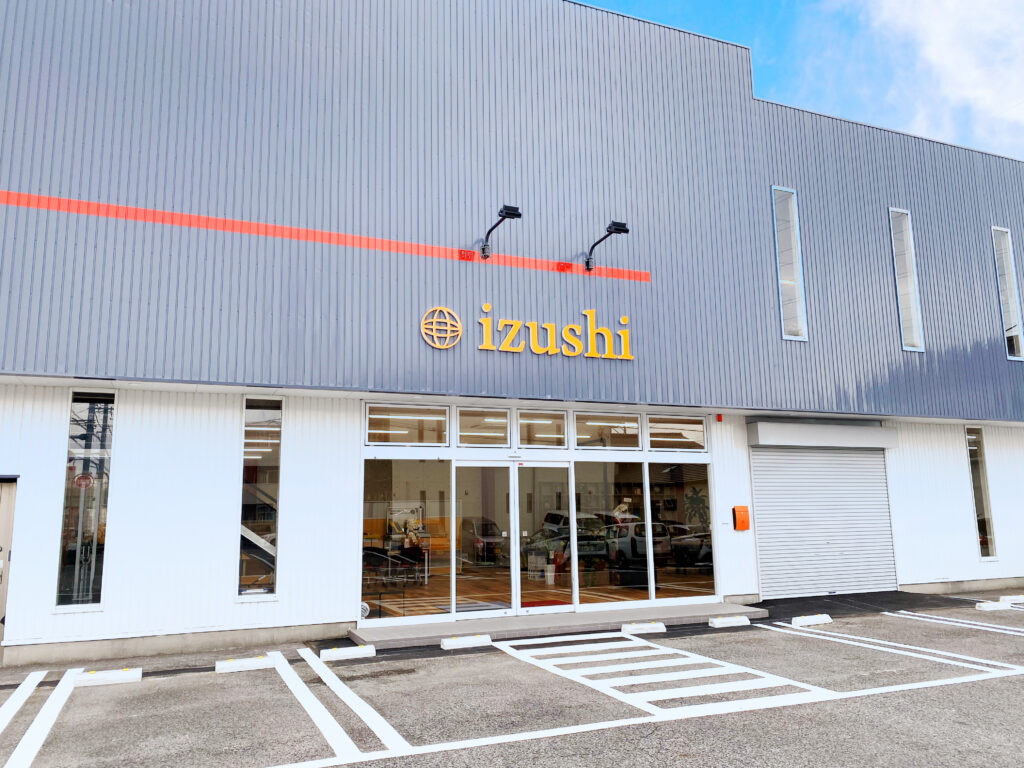
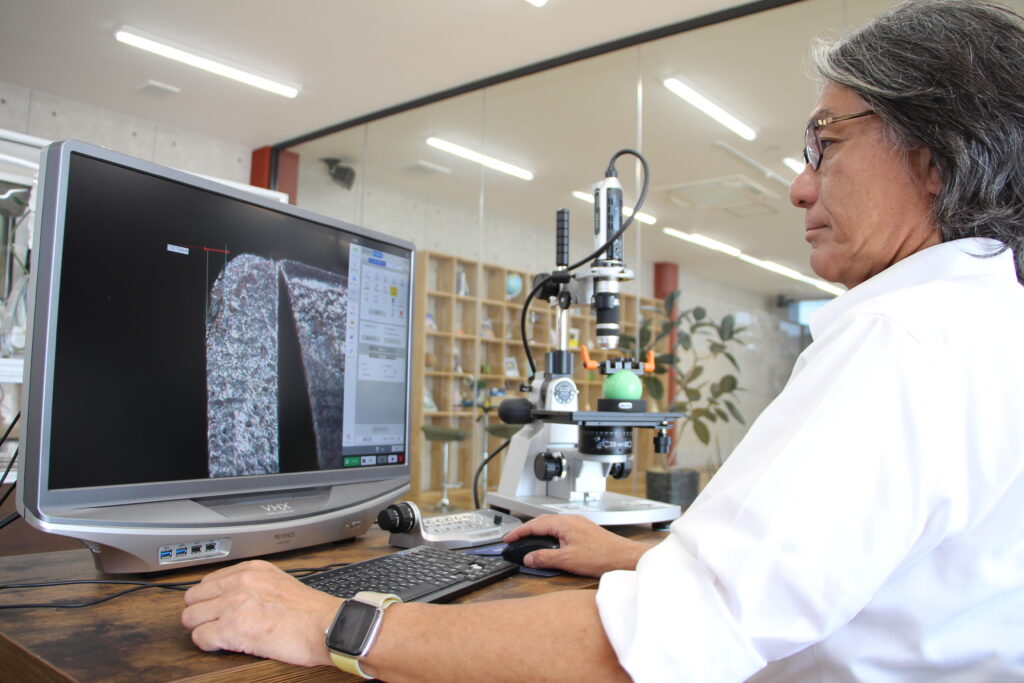
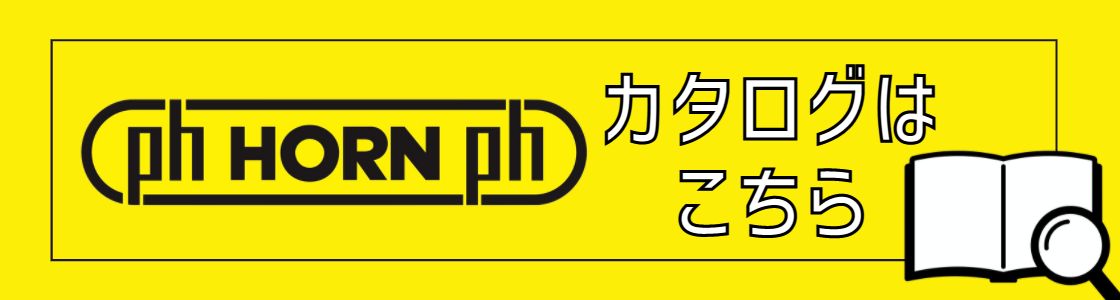
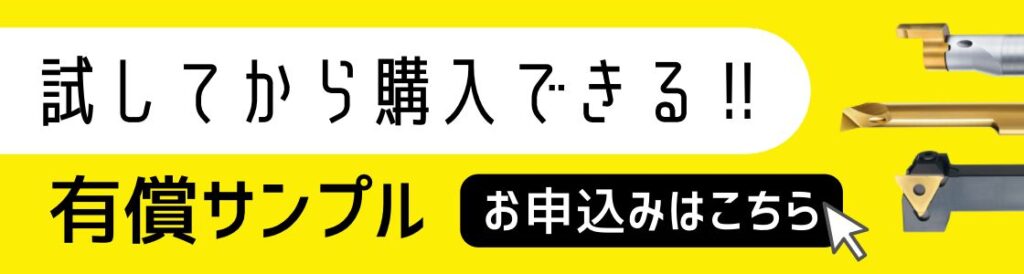